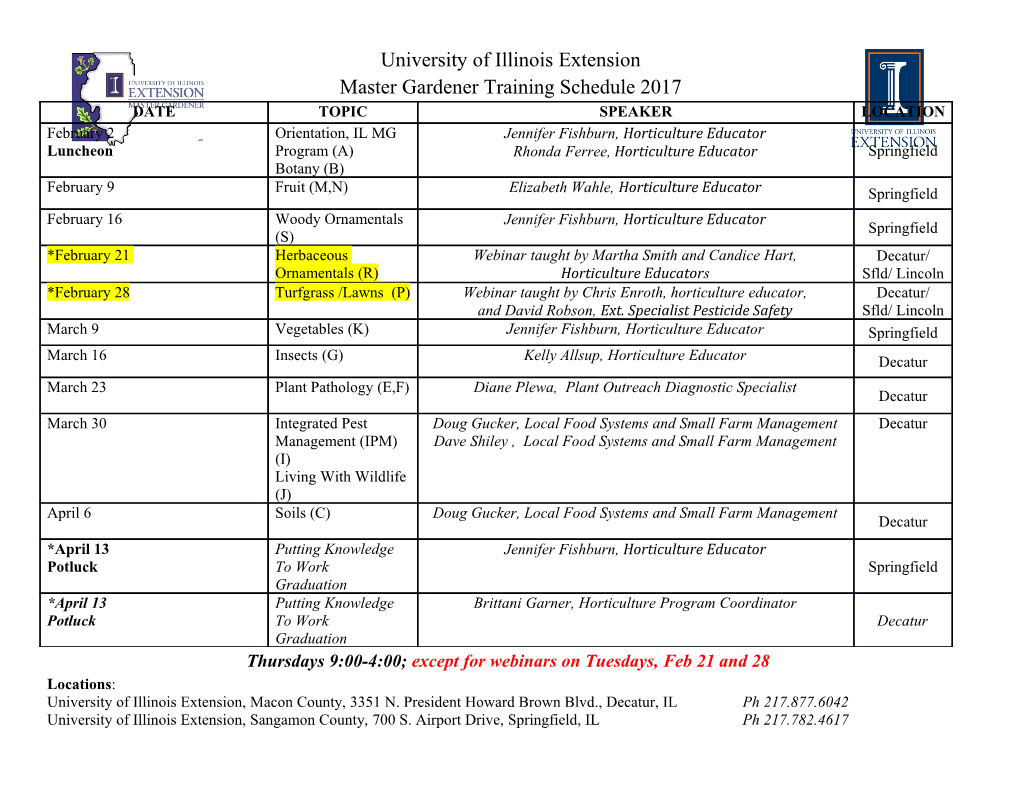
@uropaisches Patentamt J) •uropean Patent Office ® Publication number: 0 1 79 940 Office europeen des brevets B1 g) EUROPEAN PATENT SPECIFICATION ® Dateof publication of patent specification: 21.09.88 ® Int. CI. : C 23 r 1/04, bObB ia/4Ub, G 05 B 19/19 Jj) Application number: 84113095.8 ® Date of filing: 31.10.84 54) An automated chemical milling process. ® Date of publication of application: @ Proprietor: GRUMMAN AEROSPACE 07.05.86 Bulletin 86/19 CORPORATION . South Oyster Bay Road Bethpage,NY11714(US) (45) Publication of the grant of the patent: 21 .09.88 Bulletin 88/38 _ (72) Inventor: Org,_ Lawrence, H. 21 Robin Drive ® Designated Contracting States: Hauppauge New York (US) CH DE FR GB LI NL SE Inventor: Jaffee, Herbert R. 7 Country Drive Plainview New York (US) (§) References cited: Inventor: Mitzelman, Irwin EP-A-0 122941 49 Wildwood Drive US-A-3 803 960 Wantagh New York (US) US-A-3 881 379 US-A-4117 751 _ „ L ._, „ US-A-4120 583 ® Representative: Schmidt-Evers, Jurgen, Dipl.- US-A-4137118 Ing.etal US-A-4 340 166 Patentanwalte Dipl.-lng. H. Mitscherlich Dipl.- US-A-4 364 1 10 ln9- K- Gunschmann Dipl.-lng. Dr.rer.nat. W. US-A-4 370 720 Korber Dipl.-lng. J. Schmidt-Evers Dipl.-lng. W. US-A-4 371 923 Melzer Steinsdorf strasse 1 0 D-8000 Munchen 22 (DE) Within nine months from the publication of the mention OTtne gramoTine nuropedn paicm, a,,y .-=y Note- shall notice to the European Patent Office of opposition to the European patent granted. Motice of opposition give fee has been be filed in a written reasoned statement. It shall not be deemed to have been filed until the opposition convention). paid. (Art. 99(1 ) European patent ^_ Courier press, Leamington spa, cngiana. 1 0 179 940 2 Description contemplated. In the event multiple etching baths are desired, the cut mask line is recovered with a The field of the present invention relates to an sealant material. After all of the stencil marks improved automated method for chemically mill- have been cut, and the secondary cuts have been ing metal and metallic structures. Chemical mill- 5 coated, one portion of the mask material is ing is widely employed in the aircraft and aeros- removed. The metal plate is then milled and pace industries to remove excess metal from rinsed in a counterflow rinse water. The second metal parts wherein the removed metal is not mark are is removed, and the workpiece is essential to the strength of the component part. reimmersed in the etching bath. The workpiece is The chemical milling process normally employs a io rinsed again and the process is repeated for the series of masking and metal removal steps. The desired number of milling steps. At the conclu- metal is removed by an etching or milling bath sion of the milling step, the workpiece is "de- which may be either caustic or acid depending smutting". A typical "de-smutting" agent is dis- upon the metal or alloy being milled. Chemical closed in U.S. Patent 3,988,254. milling may be used to produce one piece struc- w There are two problems in the present prior art tures having a skin and load bearing ribs or method of chemical milling that are solved by the stiffeners that provide lightweight alternatives for present invention. traditional aircraft skin and stringer constructions. a) controlling the depth of the cut through the The prior art has used chemical milling to masking material. At present, the mask is hand- reduce the weight of metal parts intended for use 20 scribed by skilled workmen. If the cut is too deep, in aircraft or aeronautic applications for over the cut allows the etching bath to mill the metal twenty years. Chemical milling is widely used to and undercut the mask. If the cut is too shallow, increase the strength to weight ratio of com- and the mask material is not completely severed, ponents parts in the aircraft airframe. Chemical it will "blowout", blister or tear when that portion milling traditionally involves the steps of masking 25 of the mask is removed. This necessitates a time- and chemically milling a metallic workpiece and consuming repair step for the stencil mask. In may repeat the sequence several times to further addition, if the "blowout" is not detected, the alter the workpiece configuration. workpiece will be undercut by the etching sol- U.S. Patent 4,137,118 discloses a method of ution. chemically milling an efficient lightweight struc- 30 b) the time consumed in laying each stencil on ture by removing excess metal to form the ribs the workpiece, marking each line to be cut and and skin of an aircraft structure. The milling step cutting each line by hand is substantial. A typical is repeated to sequentially undercut and impart three-feet (0.9 m) by four-feet (1.2 m) workpiece an "I" or "1" section to the ribs and to reduce the requires six to eight hours of hand labor to thickness of the skin. 35 handmark and cut each of the areas to be U.S. Patent 3,745,079 discloses a method of chemically milled. The automated process of the chemically milling a titanium alloy stock for use present invention can do the same marking and as a structural member in an aircraft. cutting in 11 minutes. In addition it can perform U.S. Patent 2,888,335 discloses a process of cuts that cannot be done by hand. chemically milling a workpiece that sets forth a 40 If the chemical milling is done on a three- method of sequentially milling the workpiece with dimensional workpiece, all of the foregoing multiple cuts in the mask material to produce a problems are accentuated. In addition, it is plurality of milled levels in the workpiece. in necessary to preform the metal part around a between each etching bath, a portion of the mask master mold in a molding or die-stamping step to is removed so that the final configuration has a 45 provide the desired three-dimensional configura- milled pattern of varying depths throughout the tion. Each of the stencils must be provided with workpiece. the appropriate compensation for three-dimen- U.S. Patent 3,380,863 discloses masking sional positioning. In the present prior art prac- g material for use in chemical milling having a tice, after the metal plates have been preformed styrene/butadiene block copolymer composition. so to an approximate three-dimensional configura- This material is widely used in chemical milling tion, they are pinned to a master moid, and the processes for masking the part to be protected individual stencils are also pinned to provide during the etching bath. intimate contact between the stencil and the At the present time, the prior art methods workpiece. Further, the three-dimensional nature comprise the steps of marking the aluminum or 55 of the workpiece makes it even more difficult to titanium stock with a reference mark or tooling accurately handcut the stencil to the desired hole for conveying the stock through the etching depth. solution. The metal part is then covered or coated The present invention involves the new use of with the butadiene/styrene copolymer masking two existing devices which have heretofore been material. A template is laid over the masking 60 used for other tasks. material and the masked material is handcut In the drafting and cartography fields, large along the template line. The masking material is computer operated drafting machines have been then marked with a marking pen along the cut or used to mark blueprints and scribe plastic stencils scribe line. These steps are repeated with that are intended for use in photoredproduction separate masks when separate milling levels are 65 processes. These machines are quite large. 2 ) 179 940 laving a drafting area that may be 8 feet (2.4 m) new template geometry on a l.k i via an existing vide by 34 feet (10.4 m) long. A motorized carriage computer program that is currently sold under the raverses the drafting bed in both the x and y "CADAM" tradename. This program will define dimensions and carries on its carriage a plurality of the x and y coordinate values of the newly created stored narking pens. One such device is the Kongsberg 5 mask before they are digitized and on I800S Series Flatbed Drafting Table. This drafting magnetic tape. able may be fitted with a variety of drafting tools The present invention relates to an automated ncluding a tangentially controlled scribing tool, chemical milling process for metals, said process rhis tool uses a single knife or chisel and is comprising coating the metal to be chemically normally used for cutting and stripping material ro milled with a resist coating, digitizing the area(s) to jsed in the photoreproduction of integrated cir- be chemically milled, to define at least x and y :uits. The knives are used to scribe coated films. coordinate values for the perimeter of the area(s) U.S. Patent 3,555,950 discloses a device for to be chemically milled, automatically scribing the automatically cutting a photomask for use in metal and coating with a scribing tool, said sroducing integrated circuits. In this device, the w scribing tool cutting through said coating along aluminum foil is cut, and the plastic laminate the perimeter defined by the x and y coordinate naterial is retained to define an optically trans- values, removing the resist coating from the jarent negative for producing an integrated circuit area(s) to be chemically milled and immersing said aoard.
Details
-
File Typepdf
-
Upload Time-
-
Content LanguagesEnglish
-
Upload UserAnonymous/Not logged-in
-
File Pages17 Page
-
File Size-