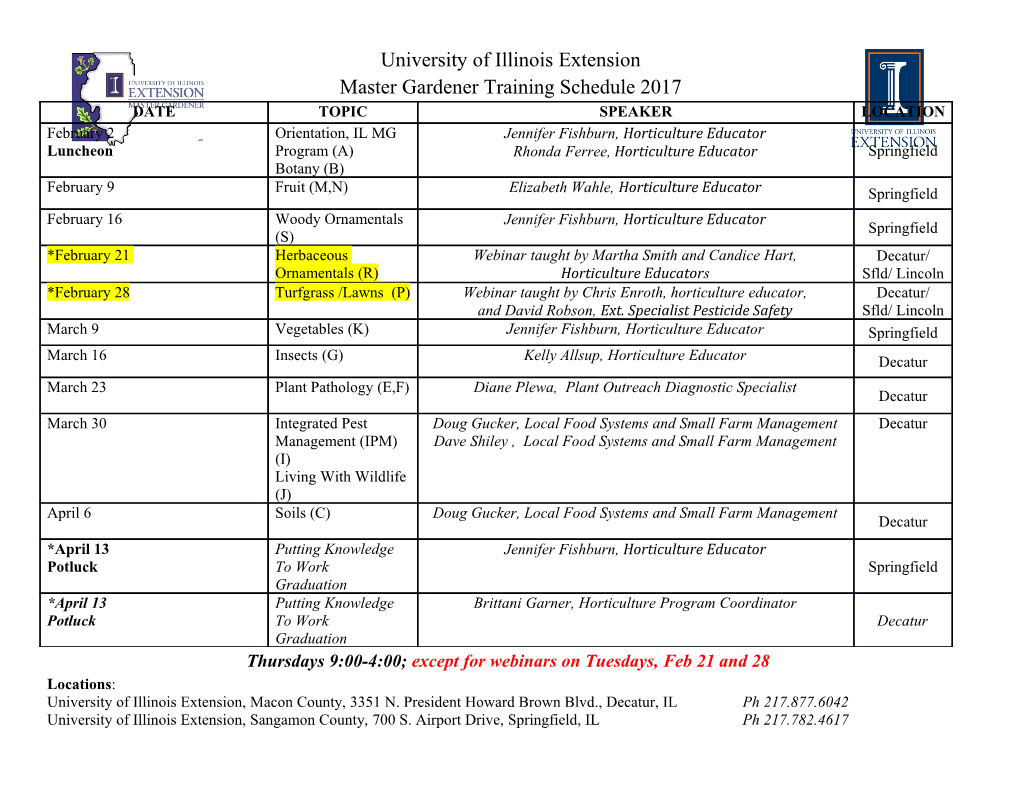
WORKING MATERIAL ABSTRACTS AND MEETING MATERIAL 3rd IAEA Technical Meeting on Divertor Concepts IAEA Headquarters, Vienna, Austria, 4–7 November 2019 indico/event/192 DISCLAIMER This is not an official IAEA publication. The views expressed herein do not necessarily reflect thoseof the IAEA or its Member States. This document should not be quoted or cited as an official publication. The use of particular designations of countries or territories does not imply any judgement by the IAEA, as to the legal status of such countries or territories, of their authorities and institutions or of the delimitation of their boundaries. The mention of names of specific companies or products (whether or not indicated as registered) does not imply any intention to infringe proprietary rights, nor should it be construed as an endorsement or recommendation on the part of the IAEA. 1 Preface Nuclear fusion is recognised as a long-term energy source. The International Atomic Energy Agency (IAEA) fosters the exchange of scientific and technical results in nuclear fusion research and devel- opment through its series of Technical Meetings and workshops. The Third Technical Meeting on Divertor Concepts (DC 2019) aimed to provide a forum for dis- cussing and analyzing the latest findings and open issues related to the divertor of a fusion device in the context of DEMO. The event focused on an integral approach, i.e. connecting plasma physics and engineering aspects, and aimed at an intensive exchange of ideas on the different aspects that the divertor design and fusion machine operation involve, from ITER divertor developments to innovative technologies for DEMO divertor. The DC 2019 was organized by the IAEA. Previous meetings in this series were held in Vienna, Austria (2015) and Suzhou, China (2017). A very first IAEA Technical Committee Meeting on Divertor Concepts was held in Aix-en-Provence, France (2001). The main topics of the meeting were: divertor and confinement; radiative power exhaust; scape-off layer and divertor physics; steady state operation and transient heat loads; plasma facing components materials and heat exhaust for steady state operation; and divertors for demo and reactors. This document has been assembled from the information submitted by the contributing authors via the IAEA-Indico conference management platform. Layout, editing, and typesetting was done by Pierre-Marie Brieda (France). The IAEA officer responsible for this document was M. Barbarino of the Division of Physical and Chemical Sciences. 2 International Programme Advisory Committee Mr Anthony LEONARD (Chair) United States of America Mr Nobuyuki ASAKURA Japan Mr Suk-Ho HONG Republic of Korea Mr Masahiro KOBAYASHI Japan Mr Brian LABOMBARD United States of America Mr Bruce LIPSCHULTZ United Kingdom Mr William MORRIS United Kingdom Ms Rudolf NEU Germany Mr Richard PITTS ITER Organization Mr Liang WANG China Mr Marco WISCHMEIER Germany Mr Guoyao ZHENG China Meeting Secretariat IAEA Scientific Secretary: IAEA Administration: Mr Matteo BARBARINO Ms Marion LINTER Division of Physical and Chemical Sciences Division of Physical and Chemical Sciences Department of Nuclear Sciences and Applications Department of Nuclear Sciences and Applications International Atomic Energy Agency International Atomic Energy Agency Vienna International Centre Vienna International Centre PO Box 100 PO Box 100 1400 VIENNA 1400 VIENNA AUSTRIA AUSTRIA Session Chairs PFC design: L. Wang Divertor Control: B. Lipschultz 3D fields: O. Schmitz Divertors in Stellerators: M. Kobayashi Alternative PFC Materials: R. Neu Core-edge coupling: A. Leonard DEMO design: M. Wischmeier Next Steps: N. Asakura 3 18 - Plasma Facing Component Design Divertors for DEMO and Reactors - 4 Nov 2019, 09:30 Development and testing results of water-cooled divertor target concepts for EU DEMO reactor Eliseo Visca ENEA Department of Fusion and Technology for Nuclear Safety and Security, Italy Power handling is one of the most critical scientific and technological challenges for a nuclear fusion power plant. Divertor is a key in-vessel component of a fusion reactor being in charge of power exhaust and removal of impurity particles. For the European demonstration reactor (EU-DEMO), divertor targets local peak heat flux is expected to reach more than 20 MW/m2 during slow transient events. Sufficient heat removal capacity of divertor targets against normal and transient operational scenarios is the major requirement. Material degradation due to neutron irradiation has to be also considered (cumulative dose for the structural material: up to 14 dpa for lifetime). To find a feasible technological solution, an integrated R&D program for the European DEMO reactor was launched since 2014 in the framework of the EUROfusion Consortium Work package “Divertor” (WPDIV). The preconceptual phase was concluded in 2018 where six different water-cooled target concepts were developed and evaluated. For all concepts a common R&D approach was adopted, namely, design study, failure simulation, design rules, materials definition, mock-up manufacturing, non-destructive inspection, high-heat-flux tests and microscopic examination of damage. Textured pure tungsten was used as reference armor material. Each concept was characterized by 1) tungsten wire-reinforced copper composite heat sink, 2) thin and thick graded interlayer, 3) thermal barrier interlayer, 4) flat-tile armor with W-Cu composite heat sink block, and 5) conventional ITER like monoblock, respectively. Extensive high-heat-flux tests were performed under DEMO-relevant oper- ational condition (heat flux: 20MW/m², coolant: 130°C, 4MPa) up to 500 load cycles after screening test up to 25MW/m². Furthermore, overload tests were carried out to explore the maximum loading limit (heat flux: >25MW/m², coolant: 20°C, 4MPa). The final results of R&D program are presented focusing on the overall technology achievement inthis preconceptual phase highlighting materials technology, mock-up fabrication and high-heat-flux qualifica- tion accompanied by non-destructive inspection and microscopic damage examination. The comparison of results of each design concepts candidate is presented. Correlation of non-destructive test and eventual thermal performance degradation is reported with evidences coming from metallographic investigations. Page 4 23 - Plasma Facing Component Design Divertors for DEMO and Reactors - 4 Nov 2019, 10:00 New developments in the design of a helium-cooled divertor for the Europen DEMO Bradut-Eugen Ghidersa Karlsruhe Institute of Technology, Germany The recent development of novel refractory materials for fusion applications with better ductile properties has led, in the recent years, to rethink the helium cooled divertor design under development at KIT. In particular, the availability of pipes and plates made of tungsten laminates showing very good mechanical properties over an extended temperature range has triggered a new search for concepts in which such materials can be used. As a first attempt, a divertor concept having a similar geometry with the water- cooled divertor developed for ITER was investigated both numerically and experimentally. The concept uses W slabs as armor brazed on a 15mm in diameter W-Cu laminate tube. The heat deposited on the surface of the armor is removed using a jet-impingement cooling scheme. Thus, the jets are created using a coolant distribution manifold in the form of a 6mm in diameter cartridge installed inside the W-laminate pipe. Under this configuration, the tested mock-up was able to withstand 8MW/m² fora total duration of 83h (100 cycles, each 5 min long) and 10MW/m² for more than 2h (25 cycles, each 5 min long). Taking advantage of the lessons learned with the first mock-up, a second mock-up has been developed using an improved cooling scheme, both in terms of pressure losses and in terms of jet flow distribution. The paper will give an overview on the experimental results obtained so far and discuss the further steps foreseen in the development of the present concept, including the integration into a divertor target. Page 5 75 - Plasma Facing Component Design PFC Materials and Heat Exhaust for SSO - 4 Nov 2019, 10:40 Additive manufacturing of tungsten by means of laser powder bed fusion for plasma-facing component applications Alexander Von Müller Max Planck Institute for Plasma Physics, Germany Tungsten (W) is currently considered the preferred plasma-facing material (PFM) for future magnetic confinement thermonuclear fusion reactors. This is mainly due to the fact that W exhibits a high threshold energy for sputtering by hydrogen isotopes as well as a low retention of tritium within the material. From an engineering point of view, however, W is a difficult metal to work with, as it is intrinsically hardand brittle which makes the processing and machining of W laborious and expensive. This is also the reason why rather simple geometries, for example flat tiles or monoblocks, are typically used for W armour parts in plasma-facing components (PFCs). Against these limitations, additive manufacturing (AM) technologies could represent a versatile and up- to-date approach for the realisation of W parts for PFC applications. The characteristic feature of AM processes is that three-dimensional objects are created by sequential layerwise deposition of material under computer control which means that such a technology is well-suited for producing objects with complex geometry. In this context, the present contribution will summarise results of research
Details
-
File Typepdf
-
Upload Time-
-
Content LanguagesEnglish
-
Upload UserAnonymous/Not logged-in
-
File Pages86 Page
-
File Size-