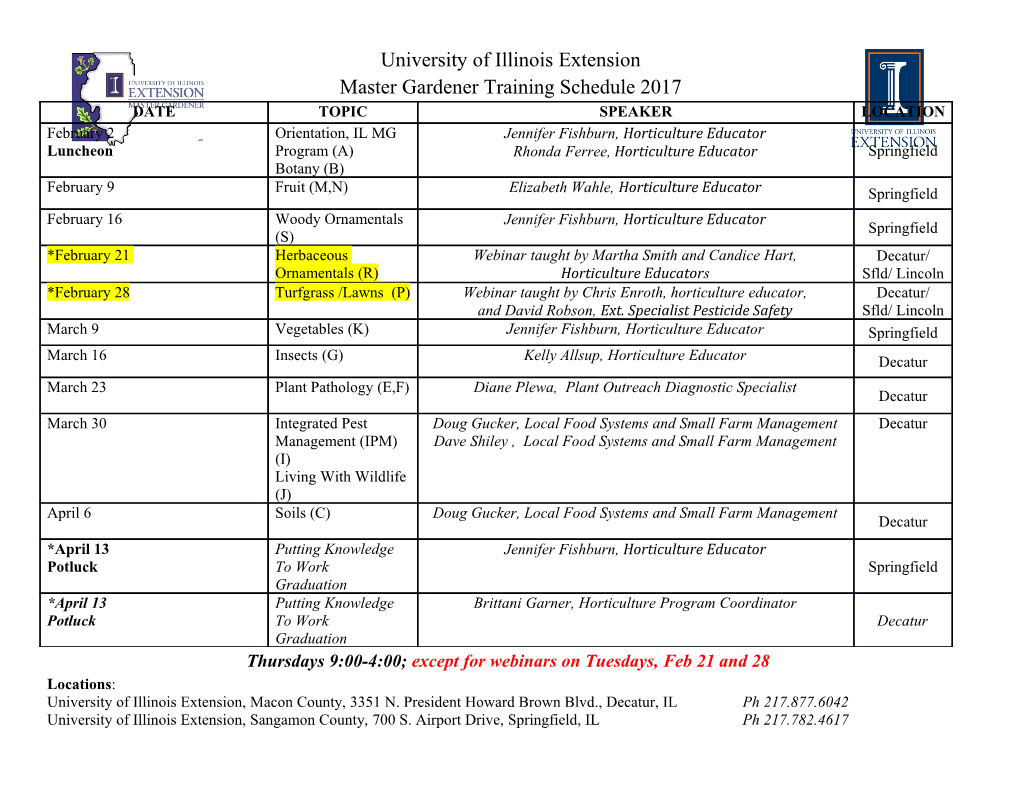
SUPER SIMPLE LEAN SIX SIGMA GLOSSARY The web is overflowing with Lean Six Sigma resources. Our glossary provides clear, straight-forward language, organized for quick access so you can easily find and understand terms that you’re searching for. For a better understanding of these terms and an advanced understanding of Lean Six Sigma, please check out our Green Belt and Black Belt Training & Certification courses. View online Lean Six Sigma Glossary including visuals & infographics at: https://goleansixsigma.com/glossary/ P300-10 COPYRIGHT 2019 GOLEANSIXSIGMA.COM. ALL RIGHTS RESERVED. 1 5S: 5S is a workplace organization technique composed for five primary phases: Sort, Set In Order, Shine, Standardize, and Sustain. 5 Whys: 5 Whys is a simple but effective method of analyzing and solving problems by asking “why” five times, or as many times as needed in order to move past symptoms and determine root cause. This approach is used in tandem with Cause- and-Effect or Fishbone diagrams. 8 Wastes (aka Muda): The 8 Wastes refer to a list of issues that get in the way of process flow and cause stagnation. The list consists of Defects, Overproduction, Waiting, Non-Utilized Talent, Transportation, Inventory, Motion, and Extra-Processing. The idea of process improvement is to identify and remove all forms of waste from a process in order to increase efficiency, reduce cost and provide customer value. A3: On a literal level, A3 refers to a ledger size (11x17) piece of paper. But in the Lean Six Sigma world, it is a tool to help see the thinking behind the problem-solving. Don’t mistake A3s as a document to be completed after the problem is solved. It’s important to use the A3 while working through the problem. The practice of using A3s forces project teams to focus their efforts. At the same time, A3s make it easier for a leader or coach to review a problem solver’s work. A3s become valuable coaching tools since leaders can see and provide feedback on the problem solver’s thought process. Action Plan: An Action Plan is a simple way of tracking the "who, what and when" of tasks and decisions involved in supporting any project, implementation or initiative. The Action Plan enables a group to document who has been assigned to do each task and when each task is expected to be completed. Affinity Chart (aka Affinity Diagram): An Affinity Chart (or Affinity Diagram) organizes a large amount of data according to their natural relationships. Useful for bringing order out of chaos, Affinity Charts make complex processes & procedures easier to grasp by breaking them down into their constituent parts and reorganizing them into groups based on similarity. In practice, this involves writing ideas onto notecards or sticky notes, and then grouping these ideas into similar columns. This is generally a silent activity completed by 1 or 2 members of a group. Agile: Agile is a pragmatic, experience-driven way of organizing and managing projects. Agile places a great value on individuals and interactions, working products and services, customer collaboration, and being responsive to change. Ally’s Network Worksheet: The Ally’s Network Worksheet provides a structured approach to building a helpful support network for any improvement effort. To learn more about Ally’s Network Worksheet, please register for our Lean Six Sigma Black Belt Training & Certification course. Alternative Hypothesis: The Alternative Hypothesis, known as HA, is a form of hypothesis that assumes there is a statistically significant difference between two or more data samples. In any hypothesis test, if there is a less than 5% probability that the difference is due to chance, then the Null Hypothesis is rejected and the Alternative Hypothesis can be pursued. To learn more about Alternative Hypothesis, please register for our Lean Six Sigma Black Belt Training & Certification course. Alternative Path: Used in process mapping, the Alternative Path method shows multiple ways of achieving the same result. Ideal for the mapping of very large and detailed processes, alternative paths are a process analysis tool. This is often done by assigning percentages to each path (e.g, time/incidents) for comparison purposes. Analyze Phase: The Analyze Phase is the third phase of the DMAIC process, and focuses on identifying the root cause (or causes) of a process problem. The Analyze Phase requires data and knowledge gleaned from the previous Define and Measure phases of DMAIC. This phase focuses on analysis of the data and the process. In terms of the data focus, statistical analysis is a cornerstone of Analyze, ensuring that potential root causes are not only validated but significant enough to merit attention. Methods and tools used include Process Maps, Charts and Graphs, Hypothesis Testing, and Value-Added Analysis. Anderson-Darling Test for Normality (aka Normality Test): The Anderson-Darling Test for Normality is a statistical test that determines whether or not a data set is normally distributed. A normal distribution is often referred to as a “Bell Curve”. Whether a distribution is normal or not determines which tests or functions can be used with a particular data set. To learn more about the Anderson-Darling Test for Normality, please register for our Lean Six Sigma Black Belt Training & Certification course. P300-10 COPYRIGHT 2019 GOLEANSIXSIGMA.COM. ALL RIGHTS RESERVED. 2 Andon: Andon is an alert system that can be visual or audible, facilitating quick response to any problems in the process or system. This system includes a way for employees to stop the process, physically or electronically, so that the issue can be addressed before production continues. ANOVA: ANOVA (Analysis of Variance) is a form of hypothesis testing that determines if there is a significant difference in the means or averages of two populations of data. To learn more about ANOVA, please register for our Lean Six Sigma Black Belt Training & Certification course. Approvals: An approval indicates a process step that requires time and attention from someone in an organization to sign or provide an “okay” before the process can continue. This adds to the waste of “Waiting,” generally does not add value and frequently becomes a “rubber stamp” type activity when the approver does not have the time to pay close attention. The fewer approvals required, the faster a process can flow. Assumption Busting: Assumption Busting is a brainstorming and questioning technique that does two things: it identifies and challenges conventional assumptions and eliminates them if they are obstacles to optimal solutions. Attribute Data (aka Discrete Data): Attribute data refers to categories or counts that can only be described in whole numbers; i.e. you can’t have half a defect or half a customer. This type of data is the opposite of continuous or variable data (temperature, weight, distance, etc.). Typical Attribute Data refers to the number of defects, number passed vs. number failed as well as the counts of different categories; i.e. number blue, number red, number yellow, etc. Attribute data can be represented in percentages and ratios such as 2.1 guests per hotel room or a 75% occupancy rate, but the source unit, the guest, can still not be truly divided. Autonomation (aka Jidoka): Autonomation describes a brand of automation where a machine stops itself if there is an abnormal situation. This technique was invented by Sakichi Toyoda back in the 1896 so that his power loom invention would stop and and allow workers to intervene and fix the issues. The 4 steps in Jidoka are: 1. Detect the abnormality 2. Stop the machine 3. Fix what is wrong 4. Find and solve the root cause To learn more about Autonomation, please register for our Lean Six Sigma Black Belt Training & Certification course. Average (aka Mean): The Average is one of the measures of "central tendency" in a data set. Calculating an average involves determining sum of a list of numbers and then dividing the sum by the number of numbers in the list. Averages don't take process variation into consideration. Balanced Scorecard: A Balanced Scorecard is a one-page graphical display of key metrics using charts, graphs and informational color coding. The Scorecard is a type of organizational Dashboard where traditional financial metrics are balanced with measures of employee engagement, operational capability as well as customer satisfaction. The words “Dashboard” and “Scorecard” are often used interchangeably but Dashboards are more commonly associated with graphical displays of measures for a specific process or one quadrant of a Balanced Scorecard. To learn more about Balanced Scorecards, please register for our Lean Six Sigma Black Belt Training & Certification course. Bartlett’s Test: Bartlett’s test is a hypothesis test that determines whether a statistically significant difference exists between the variances of two or more independent sets of normally distributed continuous data. It is useful for determining if a particular strata or group could provide insight into the root cause of process issues. To learn more about Bartlett's Test, please register for our Lean Six Sigma Black Belt Training & Certification course. Baseline Measure: A Baseline Measure results from data collected to establish the initial capability of a process to meet customer expectations. By collecting a baseline prior to making any changes to the process it is possible to determine if solutions implemented later on have the desired impact. P300-10 COPYRIGHT 2019 GOLEANSIXSIGMA.COM. ALL RIGHTS RESERVED. 3 Batching: Batching is the practice of making large lots of a particular item to gain economic efficiencies. Although the assumption is that it increases efficiency, batching increases total cycle time and increases the waste of waiting both internally and for the customer. Batching is considered the opposite of the concept of "Single-Piece-Flow" where the goal is to use the smallest batch possible with the optimal size being one unit.
Details
-
File Typepdf
-
Upload Time-
-
Content LanguagesEnglish
-
Upload UserAnonymous/Not logged-in
-
File Pages30 Page
-
File Size-