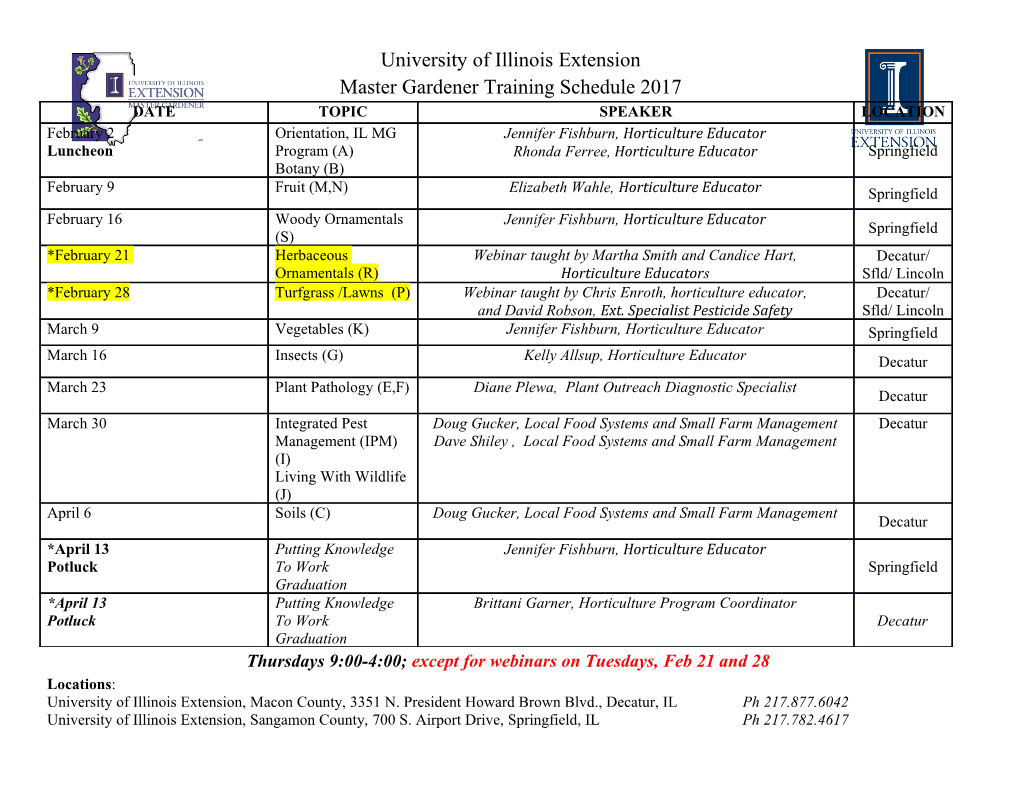
Robotics & Automation Lecture 23 Closed Kinematic Chain and Parallel Mechanisms John T. Wen November 10, 2008 JTW-RA23 RPI ECSE/CSCI 4480 Robotics I Examples of closed kinematic chains ² Constrained robot, e.g., robot in contact with environment (polishing, assembly, etc.). ² Multiple interacting robots, e.g., multi-finger grasp, multiple cooperative robots. ² Parallel mechanism, e.g., 4-bar linkage, slider-crank, Stewart-Gough Platform, Delta robot. qq 2 qq 1 qq 3 November 10, 2008Copyrighted by John T. Wen Page 1 JTW-RA23 RPI ECSE/CSCI 4480 Robotics I Kinematics Forward kinematics and inverse kinematics are the same as before: given joint positions, find the task frame, and vice versa – subject to the closed chain constraints. Usually: Serial mechanism has complicated geometry, inverse kinematics is more dif- ficult than the forward kinematics. Parallel mechanisms usually are based on imposing kinematic constraints to simple serial mechanisms. Therefore, inverse kinematics is usu- ally easy. The forward kinematics needs to take into account of constraints, and is more difficult to solve. November 10, 2008Copyrighted by John T. Wen Page 2 JTW-RA23 RPI ECSE/CSCI 4480 Robotics I Constrained mechanisms Consider a serial kinematic chain with n joints (q 2 Rn). Suppose the chain is constrained: f(q) = 0; f : Rn ! Rk: Then the mechanism has n ¡ k (unconstrained) DOF. Example: ² 3-DOF Planar arm with tip constrained to move along a line (2 dof) ² 4-bar linkage (1 dof) November 10, 2008Copyrighted by John T. Wen Page 3 JTW-RA23 RPI ECSE/CSCI 4480 Robotics I Greubler’s Formula Consider a planar mechanism. Let N = # of links, g = # of joints, fi = # of DOF of ith joint. DOF: 3N g Constraints: 3g ¡ ∑i=1 fi. g Net # of DOF: 3(N ¡ g) + ∑i=1 fi for spatial mechanisms (bodies are free to translate and rotate in Cartesian space), we have g Net # of DOF: 6(N ¡ g) + ∑ fi: i=1 Example: planar platform with three legs. November 10, 2008Copyrighted by John T. Wen Page 4 JTW-RA23 RPI ECSE/CSCI 4480 Robotics I Kinematics: 4-bar linkage Example rotation: R = exp(zˆq1)exp(zˆq3) = exp(zˆq2)exp(zˆq4) (1 constraint) position: p14 = exp(zˆq1)(p13 + exp(zˆq3)p34) = p12 + exp(zˆq2)p24 (2 constraints) Inverse kinematics: given R (equiv. qE = q1 + q3 = q2 + q4), find (q1;q2;q3;q4). Forward kinematics: Suppose q1 is the active joint. Given q1, find qE . Typically, inverse kinematics is easy (since each leg is simple), but forward kinematics hard (solving the constraint equations). November 10, 2008Copyrighted by John T. Wen Page 5 JTW-RA23 RPI ECSE/CSCI 4480 Robotics I Slider Crank qq2 qq1 qq3 Structure equation (kinematics + constraints): (q1+q2+q3)zˆ R03 = R01R12R23 = e p0T = R01 p12 + R01R12 p23 + R01R12R23 p3T R03 = I T y p0T = 0: November 10, 2008Copyrighted by John T. Wen Page 6.
Details
-
File Typepdf
-
Upload Time-
-
Content LanguagesEnglish
-
Upload UserAnonymous/Not logged-in
-
File Pages7 Page
-
File Size-