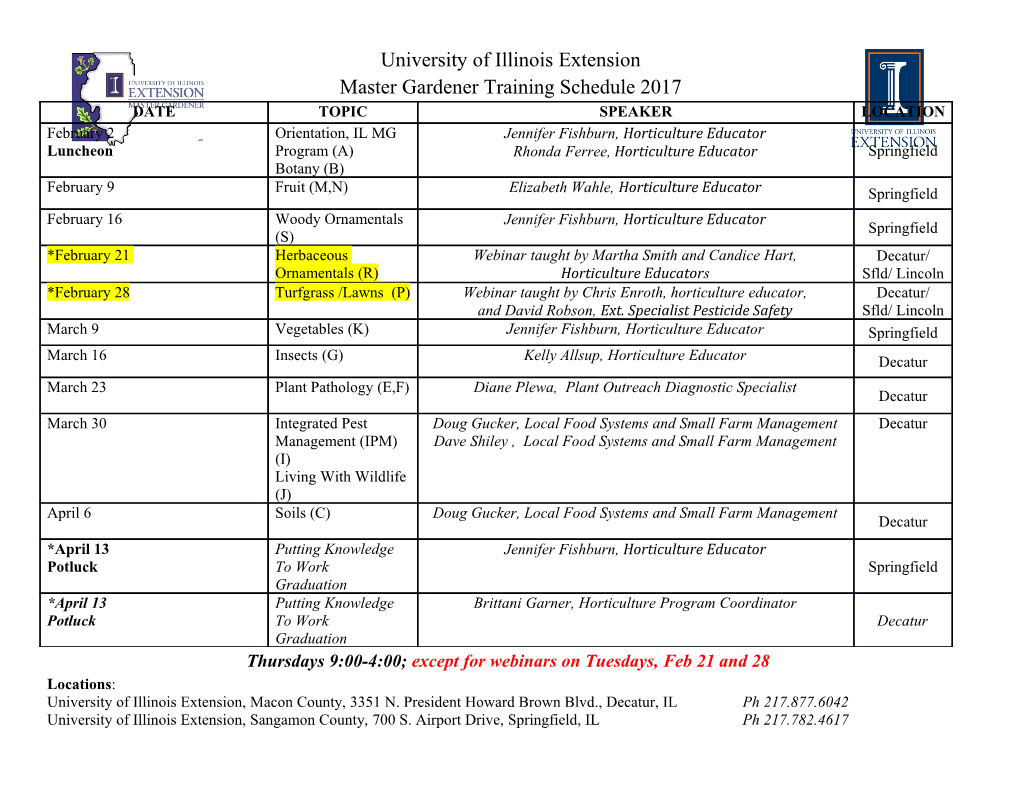
International Journal of Rotating Machinery, 10: 1–13, 2004 Copyright c Taylor & Francis Inc. ISSN: 1023-621X print DOI: 10.1080/10236210490258016 Pumping Speed Measurement and Analysis for the Turbo Booster Pump R. Y. Jou, S. C. Tzeng, and J. H. Liou Department of Mechanical Engineering, Chien Kuo Institute of Technology, Changhua, Taiwan, Republic of China also made with other turbo pumps. The compared results This study applies testing apparatus and a computational show that the turbo booster pump presented here has good approach to examine a newly designed spiral-grooved turbo foreline performance. booster pump (TBP), which has both volume type and mo- mentum transfer type vacuum pump functions, and is capa- Keywords CFD, DSMC, Flow meter method, Transition flow, Turbo ble of operating at optimum discharge under pressures from booster pump approximately 1000 Pa to a high vacuum. Transitional flow pumping speed is increased by a well-designed connecting element. Pumping performance is predicted and examined INTRODUCTION via two computational approaches, namely the computa- Review of the Turbo Pump Designs tional fluid dynamics (CFD) method and the direct simu- Plasma-based etch and chemical vapor deposition (CVD) de- lation Monte Carlo (DSMC) method. In CFD analysis, com- pend on the reaction of gas molecules and reactive ions on the parisons of measured and calculated inlet pressure in the wafer surface. The concentration, arrival rate and directionality slip and continuum flow demonstrate the accuracy of the of reactive gases and ions determine the etching rate, deposi- calculation. Meanwhile, in transition flow, the continuum tion rate, step coverage, process uniformity, and etching profile. model of CFD is unsuitable for calculating such rarefied Meanwhile, the parameters of concentration, arrival rate and di- gas. The pumping characteristics for a full 3D model on a rectionality are in turn determined by flow rates and chamber rotating frame in transition and molecular regimes thus are pressure, as well as by plasma energy and the distance between simulated using the DSMC method and then confirmed ex- the plasma and wafer. The above two processes differ from alter- perimentally. However, when the Knudsen number is in the natives in that they require high flow rates, and relatively shallow range 0.5 < Kn < 0.1, neither CFD computation nor DSMC vacuum levels. Specifically, pressures of around 10 mTorr are re- simulation is suitable for analyzing the pumping speed of quired, along with flow rates of up to 800 SCCM. Those require- the turbo booster pump. In this situation, the experimental ments become increasingly stringent with the move to 300 mm approach is the most appropriate and effective method for wafer and 0.25 to 0.18 µm designs. Consequently, pumps used analyzing pumping speed. Moreover, the developed pump for pumping CVD or etching equipment in the IC industry re- is tested using assessment systems constructed according to quire superior discharge characteristics in conditions ranging ISO and JVIS-005 standards, respectively. Comparisons are from atmospheric pressure to a high vacuum. Momentum transfer from the high-speed rotating blades to the gas molecules affects the action of a turbomolecular pump Received 19 June 2002; accepted 31 December 2002. (TMP). In molecular drag pump (MDP) designs, the pumped The National Science Council under the contract number of NSC90- 2212-P-270-001 provides supports for this work. All authors deeply fluid generally moves parallel to the moving wall, while in TMP appreciate the experimental support of Precision Instrument Develop- designs the movement is perpendicular. Maurice (1974) pro- ment Center, National Science Council in Taiwan. Support of Ms. Y.W. posed a significant improvement to the MDP design that en- Chang in DSMC simulation and Dr. H. P. Cheng in CFD calculation hanced pump compression ability by reducing the influence of is also highly appreciated. Both of them have done much excellent internal leakage. Moreover, Henning (1988) reviewed 30 years research in this field. Address correspondence to R. Y. Jou, Department of Mechani- of turbo type and turbodrag type pump design to trace the devel- cal Engineering, Chien Kuo Institute of Technology, Changhua 500, opment of turbo pumps. Furthermore, Duval et al. (1988) dis- Taiwan, Republic of China. E-mail: [email protected] cussed the development history of molecular pumps. Duval et al. 1 2 R. Y. JOU ET AL. noted that modern MDP possess some interesting characteris- (1913), Holweck (1923), Siegbahn (1943), and Becker (1961) tics, particularly a high compression ratio in the viscous flow are being proposed. These designs generally improve pumping range, enabling MDP to operate as a booster and to operate in performance in certain ways, including either pumping speed the 10−2 to 10−1 mbar at full pumping speed. Sawada et al. (1990, or compression ratio. Because of uncertainty regarding natu- 1992, 1993) proposed an analytical method for investigating the ral and treatment difficulties of the transitional flow problem, it pumping performance of spiral grooved visco-vacuum pumps is difficult or even impossible to improve pumping speed and with arbitrary groove cross-sections. Moreover, Sawada et al. compression ratio simultaneously, especially at higher exhaust also experimentally assessed this theoretical model. pressure. Jou et al. (2000) presented a turbo booster pump (TBP) Cleanliness is an important consideration in vacuum turbo with smooth and good performance in the transition regime. As pump design. The most common method of ensuring cleanli- shown in Figure 1, this design has a compact structure com- ness involves increasing the tolerable discharge pressure to allow pared with other available designs and differs significantly from the use of oil-free backing pumps. The compound turbo pump, available methodologies in terms of design principles. which complements the conventional TMP design by incorpo- rating a turbo-drag section on the same rotation shaft, permits discharge pressures of 1000 to 2000 Pa. Meanwhile, Levi (1992) Analysis and Simulation for Turbo Pump Designs developed another type of pump, called a hybrid pump, which Regarding the numerical analysis of turbo vacuum pumps, combines different impellers on the same axis without increasing Lee and Lee (1996) investigated the compression characteris- the number of stages. Furthermore, Hablanian (1994) reviewed tics for a simplified drag pump model. Moreover, Schneider the development history of turbine-type, high vacuum pumps et al. (1998) built an empirical and 2D numerical calculation for and noted that the optimization process for designing a general- a single stage turbomolecular pump. Additionally, Nanbu et al. purpose turbopump for high-vacuum use is incomplete. Finally, (1991) applied DSMC to design spiral grooves on a turbomolec- Heldner and Kabelitz (1990) compared the design and perfor- ular pump rotor. Heo and Hwang (2000) also used DSMC to mance characteristics of the most widely used rolling element calculate the blade row of a TMP in the molecular and transition bearing system to more advanced bearing systems and noted that flow regions. Heo and Hwang concluded that the maximum com- fully magnetic bearing designs are growing in popularity, and pression ratio and pumping speed depend strongly on the Knud- becoming a design standard for IC industry application. Table 1 sen number in the transition region, and also depend weakly briefly lists some basic characteristics of the TMP, MDP, and on the Knudsen number in the free molecular flow region. In compound molecular pump (CMP). those studies, when dealing with the simulation of turbomolec- The main advantage of compound turbo pumps is that they ular pumps, it is usual to fix the analysis model on the rotating can exhaust at relatively high pressures, so high that simple, dry rotor and make some assumptions and simplifications. Owing to diaphragm pumps can be used for backing. Turbo pumps also are the geometrical characteristics of the turbo booster pump rotor, often used as an upstream booster or “supercharger” for a Roots as depicted in Figure 2, Chang et al. (2001) proposed a full 3D blower, which has poor throughput in low milliTorr pressure DSMC model on a rotating frame that included the design pa- ranges, but pumping speed still tends to decline. Currently, vari- rameters of clearance between the rotor and the stator and blade ous pumps combining the traditional design principles of Gaede thickness. Additional treatments related to Coriolis acceleration TABLE 1 Characteristic List of TMP, MDP, and CMP TMP MDP CMP (TMP + MDP) Rotor configuration Pumping speed High Relatively small High Foreline pressure Very low (<1 Pa) High (1000 to 2000 Pa) High (1000 to 2000 Pa) Transitional flow performance Poor Good Good Structure Complex Compact Complex; with TMP element Compact; without TMP element Manufacture Difficult Easy Difficult; with TMP element Easy; without TMP element PUMPING SPEED MEASUREMENT AND ANALYSIS 3 pumps. However, to provide preliminary testing results for re- search, this study adopts the original standard specifications for turbomolecular pump testing. To test the entire operating range of the turbo pumps, a sys- tem that combines the measurement functions of the flow meter and orifice methods should be developed. This approach would facilitate the calculation of pumping speeds under a constant inlet pressure condition based on the stable chamber pressure, mass flow into the chamber, conductance of the
Details
-
File Typepdf
-
Upload Time-
-
Content LanguagesEnglish
-
Upload UserAnonymous/Not logged-in
-
File Pages14 Page
-
File Size-