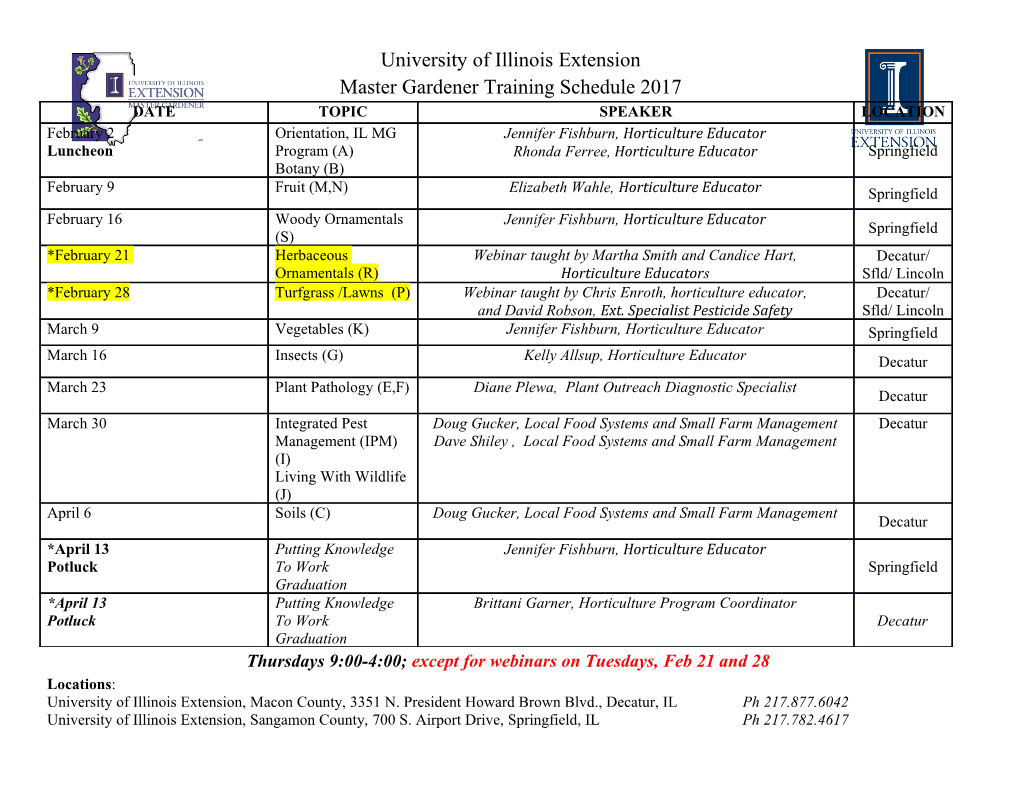
metals Article Influences of Different Die Bearing Geometries on the Wire-Drawing Process Gustavo Aristides Santana Martinez 1,*, Eduardo Ferro dos Santos 1 , Leonardo Kyo Kabayama 2 , Erick Siqueira Guidi 3 and Fernando de Azevedo Silva 3 1 Engineering School of Lorena, University of São Paulo-USP, Lorena 12602-810, Brazil; [email protected] 2 Institute of Mechanical Engineering, Federal University of Itajubá-UNIFEI, Itajubá 37500-903, Brazil; [email protected] 3 Guaratinguetá School of Engineering, Campus de Guaratinguetá,São Paulo State University-UNESP, 12516-410 Guaratinguetá, Brazil; [email protected] (E.S.G.); [email protected] (F.d.A.S.) * Correspondence: [email protected]; Tel.: +55-12-3159-5337 Received: 2 September 2019; Accepted: 8 October 2019; Published: 10 October 2019 Abstract: Metalworking is an essential process for the manufacture of machinery and equipment components. The design of the die geometry is an essential aspect of metalworking, and directly affects the resultant product’s quality and cost. As a matter of fact, a comprehensive understanding of the die bearing geometry plays a vital role in the die design process. For the specific case of wire drawing, however, few efforts have been dedicated to the study of the geometry of the bearing zone. In this regard, the present paper involves an attempt to investigate the effects of different geometries of the die bearing. For different forms of reduction as well as bearing zones, measurements are carried out for the wire-drawing process. Subsequently, by extracting the friction coefficients from the electrolytic tough pitch copper wire in cold-drawn essays, the numerical simulations are also implemented. We present the results on both the superficial and center radial tensions obtained by finite element methods. It is observed that the reduction of the friction coefficient leads to an increase in radial stress, while for a given friction coefficient, the substitution of the C-type die by the R-type one results in a decrease in the superficial radial stress of up to 93.27%, but an increase at the center of the material. Moreover, the die angle is found to play a less significant role in the resultant center radial stress, but it significantly affects the superficial radial stress. Lastly, R-type dies result in smaller superficial radial stress, with a change of up to 34.48%, but a slightly larger center radial stress up to 6.55% for different die angles. The implications of the present findings are discussed. Keywords: wire drawing; finite element method; drawing die; die geometry; radial stress; friction 1. Introduction The influence of die drawing in the metalworking processes has attracted much attention. A vital feature of the process is that the resulting stress is applied indirectly by an external source, as in the cases of extrusion [1,2] and wire drawing [3]. Previous studies on wire drawing have reported the improvement of the drawing quality by selecting the appropriate die geometry (Figure1). The influence of the reduction zone as well as the bearing zone is known to significantly affect the drawing force, spatial profile of the radial stress, residual stress behavior, and properties of the resultant wire [4–12]. Metals 2019, 9, 1089; doi:10.3390/met9101089 www.mdpi.com/journal/metals Metals 2019, 9, x FOR PEER REVIEW 2 of 10 Metalsit has2019 been, 9, demonstrated 1089 in [18,19] that the radial stress due to specific die bearing contour geometry2 of 10 has a significant impact on the degree of residual stress. FigureFigure 1. Schematic 1. Schematic illustration illustration of the of internal the internal longitudinal longitudinal section section structure structure of the of wire the wire die. die. VariationsA reduction in zone radial determines stress aff ectthe theprimary mechanical deformation properties, during and the plastic subsequently, metal forming the quality process of, theindicated drawn by product, the ∆ parameter which might defined lead in toEq disqualification.uations (1–2). To be Such more defects specific, include it gives shape the relation distortion,ship crackbetween propagation, the geometrical inferior measures surface and finish the semi quality, die angle and β, reduced which consequently dimensional affects accuracy the drawing [13–17]. Forforce instance, and friction it has [20 been–22]. demonstrated in [18,19] that the radial stress due to specific die bearing contour geometry has a significant impact on the degree of residual stress. β 2 A reduction zone determines the primaryΔ = deformation[1 + √1 − r during] the plastic metal forming process,(1) r a indicated by the D parameter defined in Equationsa (1) and (2). To be more specific, it gives the Af relationship between the geometrical measuresra = 1 and− the, semi die angle β, which consequently affects(2) Ai the drawing force and friction [20–22]. where ra is the reduction in area and β is the semi-angle of the die in radians. In [7], Kraft et al. reported the process ofβ hdrawingp a commerciali2 electrolytic tough pitch copper D = 1 + 1 ra (1) (Cu-ETP) wire in an annealed condition at lowra speed with− a drawing block. The authors showed that different die angles result in significant differences in the parameter ∆, strain rate, and total Af deformation strain (due to redundant strain).ra Atkins= 1 [22,] observed that the deformations in the cases (2) − Ai ∆ 1 can be better explained by the redundant work factor (Φ). The factor Φ is defined by the ratio of β wherethe total ra isdeformation the reduction work in areato that and due isto thedimension semi-angle change. of the In die other in radians.words, it carries the information on theIn [additional7], Kraft et plastic al. reported deformation the process besides of drawingthose owing a commercial to the cross electrolytic-sectional tougharea reduction. pitch copper The (Cu-ETP)corresponding wire invalue an annealedfor Cu-ETP condition is found at to low be speed with a drawing block. The authors showed that different die angles result in significant differences in the parameter D, strain rate, and total deformation strain (due to redundant strain).Φ Atkins ≈ 1 + 0.27∆ [22]. observed that the deformations in the cases(3) D 1 can be better explained by the redundant work factor (F). The factor F is defined by the ≥ Other studies by Nakagiri [8], Coser [17], and Godfrey [23] focused on the effects of the wire/die ratiocontact of thelength total to deformationdiameter ratio work (L/Di to). thatHere due the tolength dimension of L is defined change. as In the other sum words, of the frustum it carries slant the informationlength at 2β ondie theangle additional and the length plastic of deformation the bearing besideszone Hc those indicated owing in Figure to the cross-sectional1. It was shown area that reduction.both the L/Di The ratio corresponding and residual value stress for were Cu-ETP small. is found to be Nonetheless, for the specific case of wire drawing die, to the best of our knowledge, few efforts F 1 + 0.27D. (3) have been dedicated to the geometry of the ≈bearing zone. Therefore, the main object of the present Otherpaper studies is to evaluat by Nakagirie the [8effects], Coser of [ 17die], andcontours. Godfrey To [23 be] focusedspecific, on we the study effects different of the wire forms/die contact of die lengthgeometry to diameter and its ratioimpact (L /Di).on reducing Here the the length radial of L stress is defined during as theand sum after of the frustumwire-drawing slant length process. at 2Therefore,β die angle the and present the length study of thewill bearing potentially zone improve Hc indicated the organizational in Figure1. It was process shown in that terms both of the the Lreduction/Di ratio andof shape residual distortion, stress were crack small. propagation, surface finish quality, and dimensional accuracy of the partsNonetheless,. for the specific case of wire drawing die, to the best of our knowledge, few efforts have been dedicated to the geometry of the bearing zone. Therefore, the main object of the present paper 2. Materials and Methods is to evaluate the effects of die contours. To be specific, we study different forms of die geometry and its impactA onbetter reducing understanding the radial stressof the duringeffects andof the after die the geometry wire-drawing in the process.process of Therefore, plastic deformation the present studyprovid willes valuable potentially information improve the and organizational potential for process further in termsdevelopment of the reduction in practice. of shape In the distortion, present crackstudy, propagation, we focus on surface the influences finish quality, of the andreduction dimensional and bearing accuracy zones of the of parts.the wire drawing die. The work is divided into three stages. In the first part of the study, tensile testing in commercial Cu-ETP 2.(99.94% Materials Cu) andwith Methods Ø 0.5 mm and a length of 200 mm in the annealed condition was performed using a tensileA better test understanding machine. The ofobject the e ffwasects ofto theobtain die geometrythe mechanical in the processproperties ofplastic of specimens. deformation The provides valuable information and potential for further development in practice. In the present study, Metals 2019, 9, 1089 3 of 10 we focus on the influences of the reduction and bearing zones of the wire drawing die. The work is Metals 2019, 9, x FOR PEER REVIEW 3 of 10 divided into three stages. In the first part of the study, tensile testing in commercial Cu-ETP (99.94% Cu)experimental with Ø 0.5 data mm collected and a length from ofthe 200 wire mm-drawing in the annealed process at condition different was speeds performed were used using to calculate a tensile testthe friction machine.
Details
-
File Typepdf
-
Upload Time-
-
Content LanguagesEnglish
-
Upload UserAnonymous/Not logged-in
-
File Pages10 Page
-
File Size-