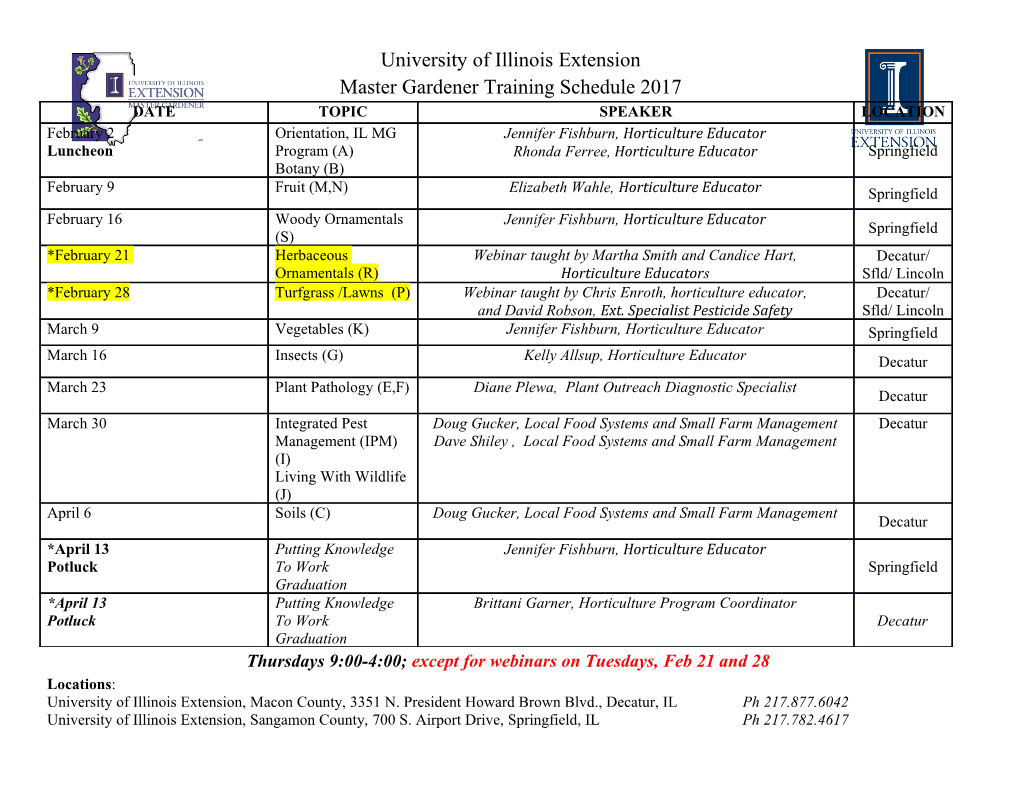
Microbial Heat Recovery Cell (MHRC) System Concept Bioelectrochemical Integration of Waste Heat Recovery, Waste-to-Energy Conversion, and Waste-to-Chemical Conversion with Industrial Gas and Chemical Manufacturing Processes A schematic of the microbial heat recovery cell (MHRC) system. Graphic courtesy of Nam, Advancing a Novel Microbial Reverse Cusick, Kim & Logan (2012) Environment Science and Technology. Electrodialysis Electrolytic System. Many current manufacturing processes electric potential required to produce and a significantly smaller footprint. produce both low-grade waste heat hydrogen. This same technology can With successful deployment, MHRC and wastewater effluents that contain be applied to a microbial fuel cell for technology could generate over 2% organic materials. A microbial reverse electric power production. Integration of total industrial electricity demand, electrodialysis electrolytic cell, designed of reverse electrodialysis with microbial or, alternatively, could be employed to to integrate waste heat recovery (i.e., a electrolysis can increase overall system produce high-value hydrogen. microbial heat recovery cell, or MHRC), performance relative to independent can operate as a fuel cell and convert operation of the individual systems. Applications in Our effluent streams into electric power, or Nation’s Industry it can operate as a microbial electrolysis Benefits for Our Industry unit and produce hydrogen. MHRC is compatible with current and and Our Nation future manufacturing infrastructure. It The driving force in a reverse MHRCs could increase industrial requires only low-grade waste heat and electrodialysis system is the energy energy efficiency, reduce emissions of can be retrofitted into existing operations. that is captured using the concentration greenhouse gases and environmental Therefore, it is quite possible to integrate difference between streams with high- pollutants, and reduce solid and liquid this technology into many manufacturing and low-salinity, such as seawater and wastes. As a result, this technology applications. MHRC is most applicable to fresh water. In a novel improvement, could reduce manufacturing costs across manufacturing facilities in the chemical, industrial waste heat will regenerate all applicable industries. In addition, food, pharmaceutical, and refinery the salt streams using a volatile salt in a MHRC technology is expected to be markets, which typically have effluent closed loop system. operable with lower-grade waste heat with high chemical oxygen demand that would otherwise be unsalvageable (COD) and low-grade waste heat sources. In a further system improvement, by conventional waste heat recovery The pulp and paper industry and other integrating a microbial electrolytic processes. Compared to existing industries are also potential MHRC users. cell with waste-heat-driven reverse wastewater treatment processes, the electrodialysis eliminates the need for MHRC technology is expected to have an external power source to provide the much higher efficiency, higher yield, ADVANCED MANUFACTURING OFFICE ADVANCED MANUFACTURING OFFICE Project Description During the course of the system Commercialization evaluation, a series of stochastic model This project was to develop an MHRC In view of the unfavorable financial runs were made of the system to system prototype using wastewater outlook for the technology as currently evaluate the likely financial returns on effluent samples from candidate facilities configured, there are no plans to pursue the system as currently designed. The to produce either electric power or commercialization. Air Products will principal outcome of these studies was hydrogen. continue to track the costs of system that the likelihood that a system could be components, with special attention on designed that would achieve a positive Barriers the ion exchange membrane used in the return on investment is very small • Practical challenges associated MHRC stack. Air Products may resume (less than 10%). The main factor in the with using substrates obtained work on the technology should the costs unfavorable financial outlook was the from chemical and other industrial become low enough to justify further cost of the ion exchange membranes used manufacturing processes. work. in the MHRC stack. It was determined that the cost of this component would • Scale-up of the system to industrial Project Partners levels. have to be reduced by a factor of more than ten for the system to have a positive Air Products and Chemicals, Inc. Pathways return. As membrane development was Allentown, PA An initial laboratory study determined not a part of this project, Air Products Principal Investigator: Jim MacDougall suitable characteristics of effluent and the DOE management team agreed to Email: [email protected] substrate candidates and waste heat terminate the project. The Pennsylvania State University sources. Sample substrates from different Milestones University Park, PA source locations were screened in the laboratory. Methods to remove organics This project began in 2012 and ended in and COD and generate electricity were 2015. Completed milestones included: For additional information, tested. Process modeling was conducted please contact: • Achievement of an acceptable power concurrently to assess economic or H yield based on total COD from at Bob Gemmer feasibility. Site selection was to be made 2 least one candidate substrate. Technology Manager based on requirements for prototype U.S. Department of Energy testing and optimal process configuration. • Determination of a viable substrate Advanced Manufacturing Office source for integrated system laboratory Phone: (202) 586-5885 Once the site had been selected, the studies and prototype testing. E-mail: [email protected] optimum level of subsystem integration between all MHRC components was to • Completion of financial analysis Project final report available atwww.osti. be determined based on the laboratory and a detailed process model of the gov/scitech: OSTI Identifier 1242987 results. Implementation plans were to be commercial-scale, integrated MHRC developed for prototype construction, system with acceptable criteria. installation, startup, and operation. For more information, visit: manufacturing.energy.gov DOE/EE-0870 • Updated September 2017.
Details
-
File Typepdf
-
Upload Time-
-
Content LanguagesEnglish
-
Upload UserAnonymous/Not logged-in
-
File Pages2 Page
-
File Size-