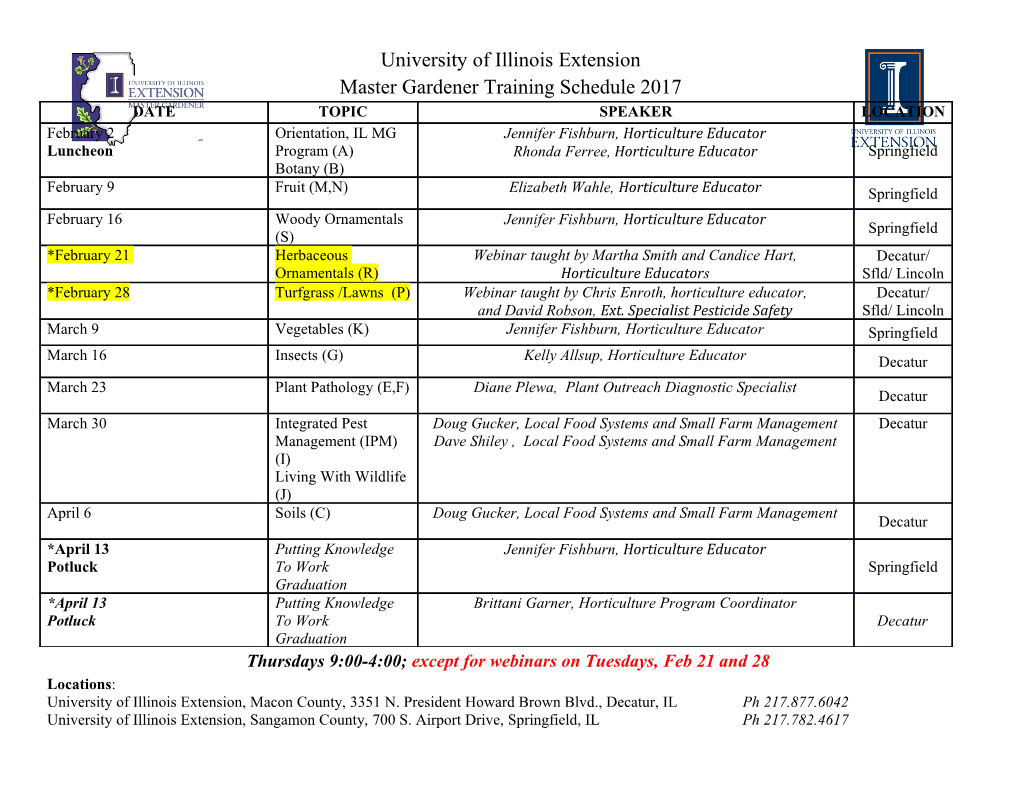
Carbon Solution in Liquid Iron and Iron Alloys Haiping Sun1, Katsumi Mori1, Veena Sahajwalla2 and Robert D. Pehlke3 1 Department of Materials Science and Engineering, Kyushu University, Fukuoka 812, Japan 2School of Materials Science and Engineering, The University of New South Wales, Sydney, NSW, Australia 3Department of Materials Science and Engineering, The University of Michigan, Ann Arbor, MI 48109 USA (Received October 23, 1997) ABSTRACT chemical reactions in a cupola /1-3/, it was clear that the iron-based charge material, during its descent The dissolution of carbon into liquid iron and iron through the cupola, undergoes several different carbon alloys was investigated using four independent transfer reactions. They are carbon dissolution (from experimental approaches, i.e., immersion of a graphite coke), and carbon loss (due to oxidation by gas and slag cylinder in a melt bath using an electric resistance phases). These phenomena dictate the carbon content furnace, immersion of a coke particle in a melt bath of the tapped metal stream, and hence, understanding using an induction furnace, a molten droplet on a these reactions is critical for the accurate prediction of graphite plate using an induction furnace and sliding a final carbon content and for describing the melting metal droplet down a graphite spiral in a resistance process in the cupola. The dissolution of carbon into furnace. The dissolution rate was analysed by assuming liquid iron alloys has been studied by many that this reaction is governed by the diffusion of carbon investigators /4-8/, and it is generally agreed that this from the carbon-metal interface to the bulk liquid metal reaction is governed by the diffusion of carbon from the through a boundary layer. The experimental results for carbon-metal interface to the bulk liquid metal through each case were well interpreted by both concentration a boundary layer. However, a considerable lack of and activity driven models. The variation in the carbon agreement exists on the carbon transport rate among dissolution rate with the experimental method was these studies. The primary objective of this study was explained by the Olsson relation or the penetration to determine consistent values of the carbon pickup rate theory. for various experimental conditions. An increase in carbon dissolution rate with temperature was observed. The carbon dissolution rate into liquid Fe-C alloy was not changed by addition of EXPERIMENTAL RESULTS 1.9 wt% silicon to the melt, while a decrease in the Carbon pickup rates were investigated using four dissolution rate of carbon was observed by adding 1 independent experimental approaches, i.e., an wt% sulfur to the melt. immersion method using an electric resistance furnace, an immersion method using an induction furnace, a plate method using an induction furnace and a spiral INTRODUCTION method using an electric resistance furnace. These experimental methods are described in more detail as In a recent series of researches on the modeling of follows. 257 Vol. 17, No. 4, 1998 Carbon Solution in Liquid Iron and Iron Alloys 1. Carbon pickup from immersed graphite particles then immersed into the liquid Fe-C alloy to start the in an electric resistance furnace ~ carbon dissolution process. Before being immersed, the graphite particle, in the shape of a cylinder, 20 mm in An electric resistance furnace, as shown in Figure 1, height and 13 mm in diameter, was heated to the was employed for heating and melting iron-caibon experimental temperature near the melt surface for alloys in an alumina crucible. Both ends of the reaction several minutes. After a certain reaction time, the tube were closed with water-cooled brass caps, sealed incandescent graphite sample immersed for a pre- with an O-ring, and flooded with purified argon gas to determined time period was withdrawn from the melt. prevent the oxidation of liquid iron by air. The Some metal samples (1-3 grams) for carbon analyses temperature was measured with a thermocouple placed were withdrawn before and after the graphite immer- just below the alumina crucible in the homogeneous sion using a quartz tube. The reaction areas were temperature zone (15 cm long) and was controlled to calculated from the average dimensions of the graphite within ±0.5°C. cylinder before and after its immersion. About 100 grams of iron-carbon alloy was first To prevent the reduction in the graphite sample melted in an alumina crucible under an argon size, which could affect the reaction area, the above atmosphere. After the experimental temperature was experimental procedure was repeated using a new attained, the graphite particle fixed to a quartz rod was graphite sample to create a carbon content versus time relationship. The carbon saturation levels for each run -> Gas outlet condition were determined by the carbon content of the metal bath into which a graphite rod was immersed for Water-cooled brass cap up to 2 horns until a variation of carbon content with time could not be observed. Alumina tube Quartz rod 2. Carbon pickup from immersed coke particles in an induction furnace SiC heating element As shown in Figure 2, an induction furnace was Alumina Pyrometer crucible Prism Metal Graphite Gas Outlet Quartz rod Refractory brick Coil Protection crucible Alumina supporter Graphite foil Alumina crucible Coke Thermocouple lump Metal protection tube Quartz support JL Water-cooled Quartz tube I brass cap Gas inlet Thermocouple Argon gas inlet Fig. 1: Schematic diagram of immersion of graphite cylinder in liquid iron using electric resistance Fig. 2: Schematic diagram of immersion of coke lump furnace. in liquid iron using induction furnace. 258 Haipung Sun et al. High Temperature Materials and Processes used for heating and melting iron-caibon alloys in an The steel sample was placed on a graphite plate, alumina crucible under an argon atmosphere. The which was set in the melting unit. As expected, some bottom of the reaction tube, made of quartz, was closed, carbon pickup occurred during melting. To account for while the upper portion was closed by a quartz cap this, immediately after the completion of melting, the sealed with vacuum grease. The temperature was power was turned off and a metal sample was quenched measured with an optical pyrometer viewing the surface to prevent any further carbon pickup. This sample was of the metal and was adjusted to 1873 ±20 K. The taken as the reference initial sample for the carbon carbon particles used in the measurement were made of pickup investigation. The experimental procedure was coke in the shape of a foreshortened cube, 10 mm in as follows. The steel sample, after the completion of height, 15 mm in length and 15 mm in width. melting, was allowed to pick up carbon for fixed The experimental procedure was essentially lengths of time. The droplets were immediately identical to those used with the electric resistance quenched by shutting off the power and analyzed for furnace. their carbon contents. The reference initial sample was analyzed, and was found to have a carbon content of 2.79 wt%C and the Si content remained the same as the 3. Carbon pickup from graphite plate in induction original, i.e. 0.58 wt% Si. furnace An experimental investigation of carbon pickup 4. Carbon pickup from graphite spiral in an from a graphite plate was conducted at 1773 Κ under electric resistance furnace an argon atmosphere, in an induction melting unit, using plain carbon steel of composition 0.31 wt%C, as A carbon pickup investigation was conducted by shown in Figure 3. running molten steel droplets down a graphite spiral, located in a resistance furnace at a temperature of 1773 Pyrometer Κ under an argon atmosphere as shown in Figure 4. Prism The spiral was machined from a graphite rod with the dimensions given below: -Inlet Length = 28.4 cm Quartz Diameter = 2.05 tube Total spiral length = 46 cm Groove height = 2.8 cm Droplet -^-Induction Groove depth = 1.9 cm Ο „ coil Ο Distance between bottom ο of a groove and top of a ο Graphite consecutive one = 3.2 cm ο base Pitch = 2.8 + 3.2 = 6.0 cm ο Ο Slope of groove = 37° To estimate the residence of a liquid droplet in the Quartz spiral, simulation experiments were conducted at room support temperature using various size steel balls, and water and mercury droplets. Based on these experiments, the Outlet average residence time (for ~0.5 gm) was found to be ~1 sec, which is equivalent to a velocity of about 46 Fig. 3: Schematic diagram of melting of a metal cm/sec. The iron particle was melted at the top of the droplet on graphite plate in an induction spiral and then allowed to roll down the spiral. The furnace. time period until the particle was allowed to roll down 259 Vol. 17, No. 4, 1998 Carbon Solution in Liquid Iron and Iron Alloys GRAPHITE the spiral after melting was about one second. The car- SPIRAL bon pickup during metal droplet travel in the graphite spiral was determined by the carbon analysis in metal noitofqir samples before and after their travel down the graphite spiral. The measured results are given in Table 2. The experimental conditions and results for these METAL four methods are summarized in Table 1 and Table 2. DROPLET The reaction areas for carbon pickup from the graphite plate and the graphite spiral were determined GRAPHITE by the shape of the iron droplet on a graphite base. Iron SLEEVE droplet shape was observed using an electric resistance furnace as shown in Figure 1 equipped with an X-ray source. An iron sample of about 0.5 gram shaped as a cylinder was placed on a graphite base in the furnace under an argon atmosphere, and then the temperature of the sample was raised.
Details
-
File Typepdf
-
Upload Time-
-
Content LanguagesEnglish
-
Upload UserAnonymous/Not logged-in
-
File Pages14 Page
-
File Size-