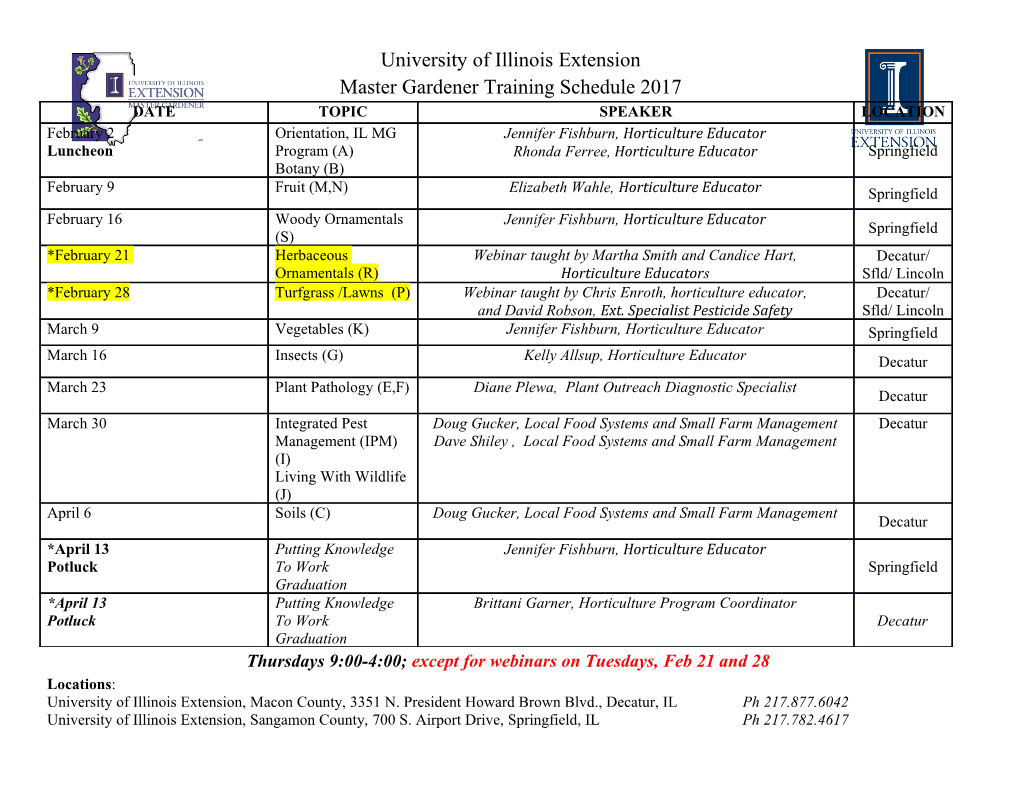
Materials Research. 2015; 18(Suppl. 1): 95-100 © 2015 DOI: http://dx.doi.org/10.1590/1516-1439.329014 Mechanical Behavior of Electrodeposited Bulk Nanocrystalline Fe-Ni Alloys Isao Matsuia,b*, Hiroki Moria, Tomo Kawakatsua, Yorinobu Takigawaa, Tokuteru Uesugia, Kenji Higashia aDepartment of Materials Science, Osaka Prefecture University,1-1, Gakuen-cho, Sakai, Osaka, 599-8531, Japan bStructural Materials Research Institute, National Institute of Advanced Industrial Science and Technology – AIST, 2266-98, Shimo-Shidami, Moriyama-ku, Nagoya, 463-8560, Japan Received: September 13, 2014; Revised: September 16, 2015 Bulk nanocrystalline Fe-Ni alloys with Ni content of 40-55 at.%, grain size of 12-15 nm, and hardness of 3.9-4.6 were prepared by an electrodeposition. The decrease in the hardness values as grain size decreased was discussed in terms of grain refinement effect, solid solution strengthening, and grain boundary relaxation strengthening. It was found that the change of Ni content could not significant solid solution strengthening, and there were no difference in the state of grain boundary for each sample. Micro X-ray diffraction analysis on the sample after tensile tests showed that the (200) texture was developed but full width at half maximum was not changed. This indicated the potency that the grain boundary activity would be induced by a tensile loading. The softening behavior of electrodeposited Fe–Ni alloys would be related to the transition of the dominant deformation mechanisms. Keywords: nanocrystalline metals, electrodeposition, Fe-Ni alloys, mechanical properties, micro X-ray diffraction 1. Introduction Nanocrystalline metals with grain sizes less than 100 nm termed grain-boundary-relaxation strengthening. Relaxation of exhibit very high mechanical strength compared with materials the grain boundary has an appreciable effect on the strength; having conventional grain size1. The strength of nanocrystalline an increase in hardness of up to ~20% was observed for metals strongly depends on the grain size, and extensive electrodeposited nanocrystalline Fe-Ni alloys9. Further studies have demonstrated the grain size (Hall-Petch) effect investigations, including those on grain-boundary-relaxation in the nanometer range. In addition, alloying elements affect strengthening, are important to gain a deeper understanding the strength of nanocrystalline materials2,3. The strengthening of the strength of nanocrystalline metals. behavior of a solid solution, due to not only intentional In our previous study10, bulk nanocrystalline Fe-Ni alloying elements but also light elements that are usually alloys with Ni content of 42-55 at.% were electrodeposited inadvertently incorporated within the materials during and the tensile properties measured. The results showed that production, has been discussed. For example, Matsui et al.4 the tensile strength decreased from 1.87 to 1.61 GPa with a tracked the effect of substitutional sulfur and interstitial decrease in the Ni content and grain size. The details of this carbon contents in electrodeposited nanocrystalline Ni and behavior were not revealed or discussed. Therefore, the aim found that solid-solution strengthening by carbon plays an of the present study is to develop a better understanding of the important role in increasing the mechanical strength of the mechanical properties for bulk nanocrystalline Fe-Ni alloys. electrodeposited Ni. Recently, it was demonstrated that the We electrodeposited bulk nanocrystalline Fe-Ni alloys with Ni state of the grain boundary, in addition to the grain size and content of 40-55 at.% and grain size of 12-15 nm, and discuss solid-solution strengthening, also affects the strength of the softening behavior in terms of the grain refinement effect, nanocrystalline metals. Nanocrystalline metals in an as-prepared solid-solution strengthening, and grain-boundary-relaxation state often contain nonequilibrium grain boundaries with strengthening. This discussion points to the potential that the excess dislocation, regions of misfit, or excess free volume5-7. softening behavior is related to the transition of dominant Jang & Atzmon6 conducted high-resolution transmission deformation mechanisms from dislocation activity to grain electron microscopy (TEM) and found that grain boundaries boundary activity. Micro X-ray diffraction (µXRD) analysis evolve gradually from an initial discontinuous structure into of the samples after tensile tests was conducted to verify the structures that are more in equilibrium during low-temperature possibility. annealing, which involves no measurable change in grain size or texture. Rupert et al.8 found that low-temperature 2. Experimental Procedure treatments of electrodeposited nanocrystalline Ni–W alloys Fe-Ni alloys were prepared employing the electrodeposition can increase the hardness without any grain growth, which is technique described in our previous study10. The bath *e-mail: [email protected] composition in the present study is given in Table 1. Bulk 96 Matsui et al. Materials Research Table 1. Bath composition for Fe-Ni alloys. Chemicals Amount (g/L) Purpose Iron sulfate 70.0-135.0 Fe source Nickel sulfamate 140.0-215.0 Ni source Nickel chloride 20.0 Passivation inhibitor Boric acid 40.0 Complexing agent Saccharin sodium 5.0 Stress reliever Sodium lauryl sulfate 0.3 Pit prevention agent samples with thickness of ~0.7 mm were electrodeposited onto Cu substrates of commercial purity using two counter electrodes of titanium baskets with nickel iron plates (99.8%) and nickel plates (99.98%), varying the Ni content in the range of 40-55 at.% by adjusting the Ni/Fe ratio in the deposition bath. We assigned samples with labels that correspond to different Ni contents and electrodeposition conditions. All electrodeposition processes were performed Figure 1. Effect of the Ni/Fe ratio of the deposition bath on the Ni for ~192 h with a current density of 10 mA/cm2, bath content of electrodeposited Fe-Ni alloys. temperature of 50.0 ± 0.5 °C, and pH of 2.2 ± 0.1. The bath temperature was strictly maintained by a heater using a structure. This result is inconsistent with results presented proportional-integral-derivative controller. The pH of the by McCrea et al.11, which showed a mixed body-centered solutions was maintained by the addition of drops of either cubic (bcc)/fcc structure in electrodeposited Fe–Ni alloys 1.0 mol/L sulfamic acid or 5.0 mol/L sodium hydroxide. for Ni content ranging by approximately ±10 wt.% around The Ni content of the electrodeposits was determined by 40 wt.% Ni. Meanwhile, Hong & Fultz12 compared the energy-dispersive X-ray spectrometry analysis using a scanning phase boundaries of the bcc and fcc phases of Fe-Ni alloys electron microscope (Hitachi S-4800). TEM specimens with obtained from nonequilibrium processing, such as thermal a diameter of 3 mm were prepared employing a twin-jet evaporation, sputtering, and ball milling. This comparison polishing technique and nitric acid–methanol solution (20% indicated that the phase boundaries depend on the fabrication processes and conditions. In fact, the single-phase fcc by volume of HNO3) at −30 °C and 15 V. The TEM specimens were examined using a JEOL JEM-2100F system operated at structure in electrodeposited Fe–Ni alloys cannot be obtained 200 kV. X-ray diffraction (XRD, Rigaku Ultimate IV) analysis when electrodeposition is conducted at current density of 2 and µXRD analysis (Rigaku SmartLab) were performed 30 mA/cm or without sodium saccharin. using Cu Kα radiation to confirm structures and to estimate The grain sizes of the samples were estimated from the grain sizes. To evaluate the hardness of the electrodeposits, width of the (111) diffraction peak using Scherrer’s equation micro-Vickers hardness tests were conducted on bulk samples and the results are presented in Figure 2. The calculated grain using a load of 500 g for 10 s. Each reported data point sizes ranged from 12 to 15 nm. These grain sizes decreased represents the average value for at least 12 indentations. with a decrease in the Ni content of electrodeposited alloys. From the bulk samples, dog-bone specimens with a gauge Figure 3 shows a bright-field TEM image for electrodeposited length of 12 mm, width of 4 mm, and thickness of 0.7 mm bulk nanocrystalline Fe-55 at.% Ni alloy. The alloy exhibits were machined by electrical discharge machining for tensile microstructures with a grain size of ~15 nm, which is comparable tests. It is noted that the copper substrate was removed by to the size calculated from the XRD peak width. No defined mechanical polishing. Tensile tests were performed at a precipitate was observed in the TEM microstructure. strain of 1 × 10−3 s−1 and at room temperature. The plastic The mechanical behavior of the electrodeposited bulk elongation of the specimen after fracture was measured by nanocrystalline Fe-Ni alloys was investigated by performing the change in the gauge length. micro-Vickers hardness tests. Figure 4 shows the results of hardness tests plotted against the inverse square root of the 3. Results and Discussion grain size. Homogeneous hardness was observed for all samples. The standard deviation of the hardness values was In total, six bulk samples were electrodeposited by 0.07 GPa. The hardness values decreased from 4.6 to 3.9 GPa varying the Ni/Fe ratio in the deposition bath (1.07, 1.31, as the grain sizes decreased from 15 to 12 nm and/or Ni 1.54, 1.66, 1.78, and 2.98). This expanded upon our previous content decreased from 55 to 40 at.%. results for Fe-Ni alloys that were limited to a Ni/Fe ratio The results of hardness tests showed that the strength of 1.54-2.98 in the deposition bath10. All electrodeposition reduced with a decrease in grain size or Ni content. There had good current efficiency of approximately 77%.Figure 1 are three factors that conceivably affect the mechanical shows the effect of the Ni/Fe ratio in the deposition bath strength of electrodeposited nanocrystalline metals: (i) the on the Ni content of electrodeposited Fe–Ni alloys.
Details
-
File Typepdf
-
Upload Time-
-
Content LanguagesEnglish
-
Upload UserAnonymous/Not logged-in
-
File Pages6 Page
-
File Size-