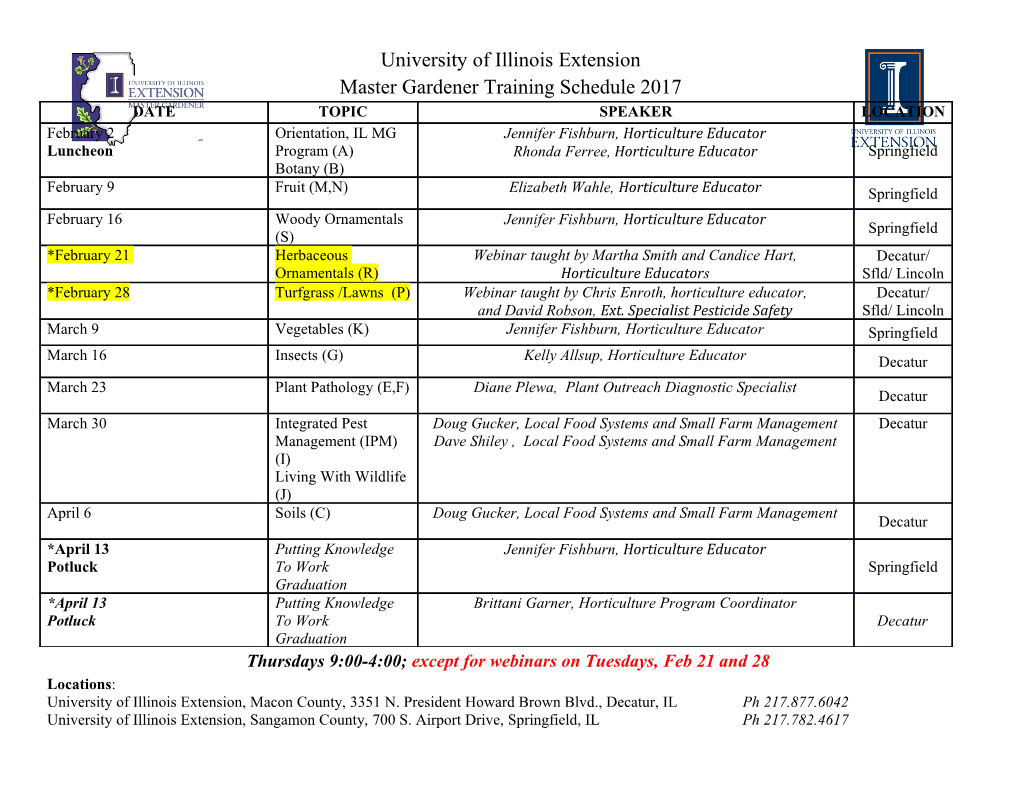
Innovative Braking and Controls Worldwide Electrohydraulic Components designed for use in electrohydraulic braking and/or electronic throttle control applications Electronic Pedals, Digital Valve Controllers, and Electrohydraulic Valves MICO, Inc. Form No. 84-950-028 Revised 2010-01-07 1 Electrohydraulics About this Catalog Catalog Index Pages 3 through 6 provide functional diagrams of a variety of electrohydraulic brake systems. These Electrohydraulics functional diagrams are not detailed representations of What are Electrohydraulic actual systems, but are meant to provide an overview Brake Systems . 2 of various brake system confi gurations that might be About this Catalog. 2 considered using electrohydraulic technology. What does MICO have to offer . 2 Pages 7 through 11 provide information on MICO Electrohydraulic Brake Systems components that can be used in the design of an Electrohydraulic Brake System . 3 electrohydraulic brake system. Please consult MICO Electronically Enhanced engineering about your application. Components that Full Power Brake System . 3 might be better suited to your application may not be Full Power Brake System with ABS . 4 presented in this catalog. Full Power Brake System with Traction Control . 4 What does MICO have to offer? Electrohydraulic Brake System with ABS The products shown in this catalog are designed for and Traction Control . 5 use in electrohydraulic braking and/or electronic throttle Electrohydraulic Brake System control applications. MICO offers a complete electro- with Inching Control . 5 hydraulic package, which includes a variety of electronic Hydraulic Brake System with pedal confi gurations and sensing options, digital valve ABS and Traction Control . 6 drivers, and a variety of electrohydraulic brake valves Electrohydraulic Brake System (EBV). for Trailers . 6 Typical applications for these new products would be T-Series Valve Driver . 7 drive-by-wire, electrohydraulic braking, machines with Electronic Pedals with multiple operator stations, remote control operation, or Brake Valve Interface . 8 - 9 propel and inching pedals for hydrostatic drive systems. In throttle applications, the pedal can be confi gured to EBV Series Electrohydraulic interface directly to the engine's electronic control unit. Brake Valve . 10 - 11 MICO® electronic pedals provide force feedback, proportional to pedal rotation, with rotary sensors to provide one or more analog outputs that are proportional to pedal rotation. Both treadle and suspended pedal models are available. What are Electrohydraulic Brake Systems? The MICO® Digital Valve Driver is designed to accept dual inputs from an electronic pedal and convert the Electrohydraulic brake systems are the combination of signal into current needed to drive the MICO® Electro- electronics and hydraulics to create a more versatile hydraulic Brake Valves. brake system. The electronics provide control fl exibility, while the hydraulics supply the power. MICO® Electrohydraulic Brake Valves are full power brake valves used for modulating output pressures, up Electrohydraulic braking offers many advantages over to 207 bar (3000 PSI), in proportion to the input current. traditional hydraulic braking systems. These advantages When used in properly designed systems, these valves can be exploited to provide improved system perfor- can provide hydraulic power for normal and emergency mance and greater comfort for the operator. Valves can power-off braking for electrohydraulic brake systems, be moved away from the cab and closer to the brakes, anti-lock braking systems, and traction control systems. reducing plumbing costs. Remote operations are easily handled without having to duplicate the valving. Vehicle In addition to these components, MICO can provide full controls can be improved by implementing a variety power brake systems with ABS, traction control, or both, of control schemes such as electrohydraulic brake for vehicles that require up to eight channels of control. systems, anti-lock brake systems (ABS), and traction control systems (TCS). These systems are a result of hydraulics and electronics combining to create brake systems that provide value added features for the machine operator. 2 MICO, Inc. Form No. 84-950-028 Revised 2010-01-07 Electrohydraulic Brake Systems Electrohydraulic Brake System (See Figure 1) These systems provide fl exible control while complying with requirements of primary and secondary braking standards. Dual pedal angle sensors send signals to redundant input valve drivers that control the brake valves. Features of this type of system include: ● Ability for designers to remove the brake valve and MICO ELECTROHYDRAULIC the hydraulic hoses from the operator station BRAKE VALVE ● Provides primary and secondary braking to meet ACCUMULATOR 2 industry standards +V BRAKE MICO WARNING ELECTRONIC MICO VALVE DRIVER PEDAL WITH REDUNDANT ● Pedal force feedback is proportional to pedal angle INPUT MICO PRESSURE SWITCH MICO DUAL ● Programmable pressure vs. pedal angle functions ACCUMULATOR CHARGING VALVE ● Easy to add additional remote operator stations MICO VALVE DRIVER WITH REDUNDANT ● Automated braking can be programmed to occur INPUT based on inputs from other sensors or controllers ACCUMULATOR 1 ● Operator warning and vehicle stop light control ● Fault diagnostics for easy troubleshooting MICO ELECTROHYDRAULIC BRAKE VALVE FIGURE 1 Electronically Enhanced Full Power Brake System (See Figure 2) The addition of electrohydraulics to enhance a hydro- mechanical full power system allows designers to add MICO control fl exibility to the brake system while maintaining B ELECTROHYDRAULIC BRAKE VALVE the hydromechanical tradition and redundancy of the single modulating brake valve. The pedal angle sen- PT ACCUMULATOR 2 sor, electronic control unit (ECU), and electrohydraulic modulating brake valve are used to provide program- BRAKE-BY-WIRE CONTROLLER ACCUMULATOR 1 mable pressure vs. pedal angle function to the brake system. Features of this type of system include: ● Provides primary and secondary braking to meet MICO DUAL industry standards ACCUMULATOR A P (OPTIONAL) CHARGING VALVE MICO REMOTE INPUT PEDAL T ● Programmable pressure vs. pedal angle functions MICO SINGLE MODULATING ● Easy to add additional remote operator stations BRAKE VALVE ● Automated braking can be programmed to occur based on inputs from other sensors or controllers PT MICO ● Many of the benefi ts of electrohydraulic braking, ELECTROHYDRAULIC with the back-up of hydromechanical braking B BRAKE VALVE ● Operator warning and vehicle stop light options ● Brake pressure controls are in parallel - brake receives highest pressure of hydromechanical or electrohydraulic valve FIGURE 2 MICO, Inc. Form No. 84-950-028 Revised 2010-01-07 3 Electrohydraulic Brake Systems Full Power Brake System with ABS (See Figure 3) SPEED SENSOR 1 SPEED SENSOR 2 Vehicle safety can be improved with the use of an anti-lock brake system giving operators control even in poor traction conditions. A typical hydromechanical full power brake system is shown consisting of a pump, accumulator charging valve, dual accumulators, and B B tandem modulating brake valve. ABS valves are ACCUMULATOR 2 normally open, which allow the tandem modulating PT TP ABS VALVE 1 ABS VALVE 2 brake valve to control braking pressure proportional to ACCUMULATOR 1 operator input force at the brake pedal. Speed sensors P A send electronic pulses, at a frequency proportional to T wheel speed, to the ABS electronic control unit (ECU). MICO ABS ELECTRONIC TANDEM CONTROL UNIT MODULATING MICO DUAL The ABS electronic control unit algorithm determines BRAKE ACCUMULATOR how much current is sent to each of the ABS valves. VALVE CHARGING VALVE P When the ABS valve receives current, pressure from A T the tandem modulating brake valve is blocked to the brake and pressure at the brake relieved. This allows the wheel to continue turning rather than slipping ABS VALVE 3 ABS VALVE 4 PT TP excessively. See MICO® Hydraulic Brake System with ABS Brochure (form number 80-950-243.) B B SPEED SENSOR 3 SPEED SENSOR 4 FIGURE 3 Full Power Brake System with Traction Control (See Figure 4) SPEED SENSOR 1 SPEED SENSOR 2 A full power brake system with traction control can help maintain traction in poor traction conditions. A typical hydromechanical full power brake system is shown consisting of a pump, accumulator charging valve, B B MICO MICO dual accumulators, and tandem modulating brake valve. ELECTROHYDRAULIC ELECTROHYDRAULIC BRAKE VALVE BRAKE VALVE Electrohydraulic brake valves are normally open, which ACCUMULATOR 2 allow the tandem modulating valve to control braking pressure proportional to operator input force at the ACCUMULATOR 1 brake pedal. Speed sensors send electronic pulses, A A at a frequency proportional to wheel speed, to the P P traction control system electronic control unit. The TCS electronic control unit algorithm determines how MICO DUAL A P ACCUMULATOR much current is sent to each of the electrohydraulic CHARGING VALVE brake valves. When the electrohydraulic brake valve T TCS ELECTRONIC receives current, pressure from the accumulators is MICO CONTROL UNIT TANDEM MODULATING BRAKE used to modulate pressure to the brakes. This stops VALVE the wheel from turning excessively and improves the A P vehicle's traction. The check valve reduces the pressure T drop through the electrohydraulic brake valve when the tandem modulating brake valve is applied to fi ll the brake cylinders. This series circuit is also an option to the parallel circuit, Figure 2,
Details
-
File Typepdf
-
Upload Time-
-
Content LanguagesEnglish
-
Upload UserAnonymous/Not logged-in
-
File Pages12 Page
-
File Size-