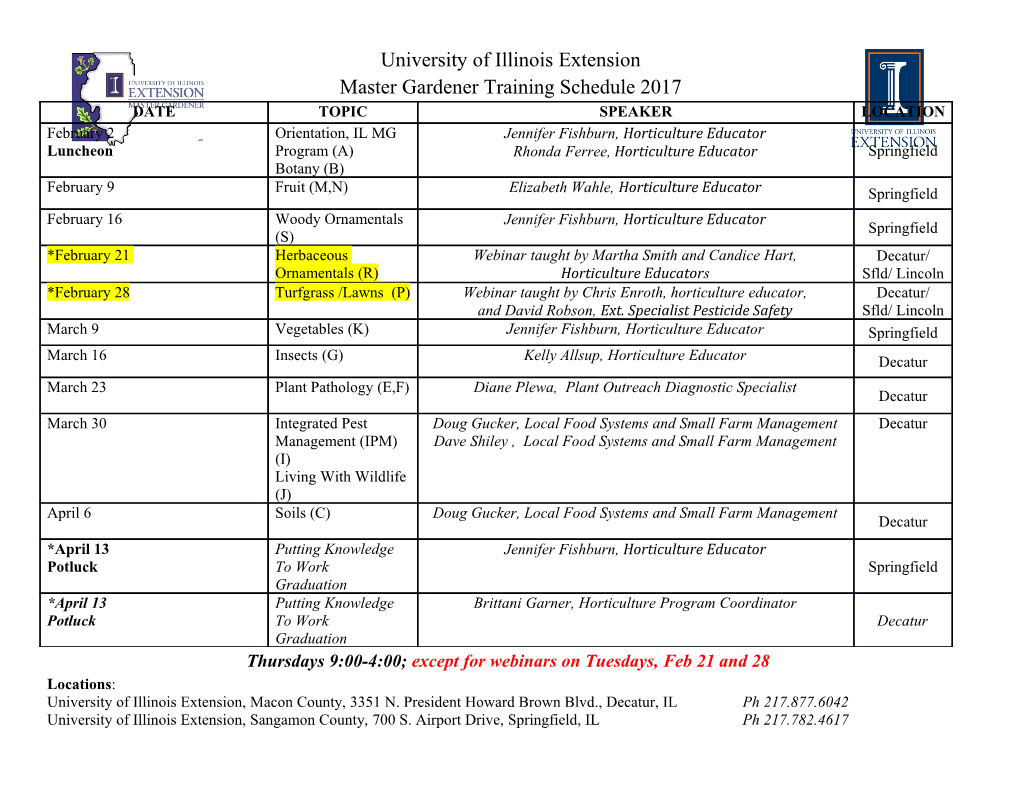
INSTRUCTION MANUAL FOR FORDS PACKAGING SYSTEMS 18 HEAD ROTARY INDUCTION SEALER SERIAL NUMBER 21510 1 95150217_01 Copyright Fords Packaging Systems Ltd 1998. All rights reserved. Fords Packaging Systems Ltd. Ronald Close Woburn Road Industrial Estate Kempston Bedford MK42 7SH Tel: +44 (0)1234 846600 Fax +44 (0)1234 853040 e-mail: [email protected] website: www.fords-packsys.co.uk Every effort has been made to ensure that the information given in this manual is correct at the time of printing. However, the product described in this manual is subject to continuous development and improvement. Fords Packaging Systems Ltd accepts no responsibility for any loss, damage or injury arising from the use of any information given in this manual. SPECIFICATION MACHINE TYPE Rotary Induction Sealer YEAR OF PRODUCTION 2012 MACHINE SERIAL NUMBER 21510 MAXIMUM SPEED 160 containers per minute ELECTRICAL SUPPLY 480V, 3ph, 60hz PNEUMATIC SUPPLY 7 bar 2 95150217_01 SECTION 1 SUPPLIER INFORMATION 3 95150217_01 SECTION 1 SUPPLIER INFORMATION 1.1 INTRODUCTION This manual relates specifically to Fords Packaging Systems Ltd. Rotary Induction Sealer. 1.2 ABOUT THIS MANUAL This manual contains information required for correct installation and commissioning of the Rotary Induction Sealer, together with operating and maintenance instructions. All procedures detailed in this manual should only be performed by suitably trained and qualified personnel. This manual should be read prior to attempting to install, operate or maintain the unit. Fords Packaging Systems Ltd. will not be liable for any injury or damage resulting from a failure to follow the procedures and instructions detailed in this manual. 1.3 ADDITIONAL DOCUMENTATION In addition to the basic manual, the documentation package supplied with all new machines includes the following: Overall layout drawing showing basic machine sizes and space requirements for installation. Parts lists, including assembly diagrams and recommended spares. Electrical circuits diagrams. Pneumatic circuits diagrams. Third party component information. These additional documents are all machine specific. They will be bound as appendices to this manual, or in additional binders as required. 4 95150217_01 SECTION 1 SUPPLIER INFORMATION 1.4 WARRANTY Fords Packaging Systems Ltd. warrants all equipment against defects in workmanship and materials for a period of 12 months from the date of shipment, or 2,000 hours of operation, whichever occurs earlier. The warranty is limited to free replacement and shipping of any faulty part, or sub-assembly which has failed due to poor quality or manufacturing errors. All claims must be supported by evidence that the failure has occurred within the warranty period. All warranty claims must specify the unit/type number and the serial number. These details are printed on the unit identification plate, as fixed to each unit. The warranty will be void if any modification is carried out on the unit without prior written approval from Fords Packaging Systems Ltd. For warranty purposes the following conditions must be satisfied: Only genuine Fords Packaging Systems Ltd. approved spare parts, lubricants and materials must be used. All scheduled maintenance operations detailed in this manual must be carried-out at the specified intervals by suitably trained and qualified personnel. The machine must not be operated outside the design parameters specified in this manual. Failure to satisfy any of these conditions will automatically void the warranty. 5 95150217_01 SECTION 2 SAFETY 6 95150217_01 SECTION 2 SAFETY 2.1 STANDARDS FOR SAFETY CE-marked machines, along with those supplied with a Certificate of Incorporation, have been designed and manufactured to comply with the essential health and safety requirements of the European Union Directives as stated on the relevant documentation supplied with the manual. Machines that do not require be CE-marking are built to a similar level of safety unless alternative regulations or equipment levels are specified. 2.2 RESPONSIBILITY FOR SAFETY Every care has been taken in the design and manufacture of the equipment to ensure that it meets all the safety requirements mentioned in Section 2.1. However, any individual operating or working on any machinery is primarily responsible for: Personal safety, safety of other personnel, and the machinery. Correct utilisation of the machinery in accordance with the procedures in this manual. The contents of this manual include suggested best working practices and procedures. These are issued for guidance only, they do not take precedence over the above stated individual responsibilities or any local safety regulations that may exist. 2.3 MISUSE OF EQUIPMENT The Rotary Induction Sealer is intended to be used for sealing caps on to plastic containers. It is not suitable for purposes other than those specified in this manual. Any use of the equipment other than for its intended use, or operation of the equipment contrary to the relevant procedures, could cause injury to the operator, or damage to the equipment. The unit must never be operated outside the design parameters specified in this manual. 2.4 MANUAL SAFETY CONVENTION The following conventions are used in this manual to alert the reader to areas of potential hazard and to provide additional information regarding particular subjects. A WARNING is given in this document to identify a hazard which could lead to personal injury. Usually an instruction will be given, together with a brief explanation and the possible result of ignoring the instruction. A CAUTION identifies a hazard which could lead to damage to the machine, damage to other equipment and/or environmental pollution. Usually an instruction will be given, together with a brief explanation and the possible result of ignoring the instruction. A NOTE is used to highlight additional information which may be helpful to you but where there are no special safety implications. 7 95150217_01 SECTION 2 SAFETY 2.5 MACHINE END-OF-LIFE 2.5.1 Procedure for disposal/scrapping When this product has reached the end if its useful life, a number of possible options are available: Contact the original manufacturer to determine if there is a possibility of buy-back. Sell on as a complete unit through a professional scrap metal trader. Dismantle and dispose of individual parts for scrap. Whichever route is chosen, in order to maintain a safe environment, methods for moving the machine must be those described in the original Operation Manual. For the purposes of disposal, the machine construction can be considered as follows: Metals used are mainly Stainless Steel and may be recycled through conventional channels. Plastic materials are non-hazardous, and are principally Nylatron GSM (Gearwheels) and Clear Acrylic (Guard Doors). No hazardous chemicals were used in the construction, although appropriate measures should be taken with regard to lubricants contained within the machine. Electrical & electronic devices should be recycled / disposed of against prevailing Policy & Law at time of disposal. Note: Certain PCB’s may contain Lithium-Ion batteries. Order of dismantling is not important, although components should not be removed in an order that causes the machine to be unstable. 8 95150217_01 SECTION 2 SAFETY 2.6 SAFETY LABELS The following labels are fixed at strategic points around the unit so as to provide instruction, or to warn of potential hazards which may exist. All personnel should be familiar with the labels, the potential hazard to which they refer and the advice given in this manual, BEFORE using the machine. Mandatory instruction: Refer to the manual. White symbol on a blue circular background. This label is used whenever any of the other warning labels are fixed. It is used to instruct personnel to refer to this manual for information regarding the warning labels used and the potential hazard to which they refer. WARNING: FAILURE TO UNDERSTAND THE MEANING OF WARNING LABELS AND THE POTENTIAL HAZARD TO WHICH THEY REFER, ALONG WITH FAILURE TO FOLLOW THE ADVICE GIVEN, MAY LEAD TO SERIOUS INJURY. Warning: High Pressure Air Black symbol on a yellow background No maintenance work (involving removal of access panels) should be carried-out without first isolating the mains air supply to the unit. A "DO NOT OPERATE" sign should be placed over the mains isolator to prevent it inadvertently being switched on. Work on pneumatic equipment must only be carried-out by suitably trained and qualified personnel. Warning: Moving Machinery Black symbol on a yellow background No maintenance work (involving removal of access panels) should be carried-out without first switching off the machine, isolating all power supplies and isolating the mains air supply to the unit. The unit main electrical isolator switch should be operated to the off (0) position. A "DO NOT OPERATE" sign should be placed over the operator control panel to prevent the machine inadvertently being switched on. The pneumatic isolator switch must be moved to the closed position and a "DO NOT OPERATE" sign should be placed over the isolator to prevent it inadvertently being switched on. 9 95150217_01 SECTION 2 SAFETY 2.6 SAFETY LABELS (Cont...) Warning: Lethal Voltage. Black symbol on a yellow background. Used to warn of an electrical hazard that is considered potentially dangerous. It is attached to all guard panels and fixed covers behind which electrical hazards may be present. Work on electrical equipment should only be carried out by suitably trained and qualified personnel. WARNING NO WORK SHOULD BE CARRIED OUT ON ELECTRICAL EQUIPMENT WITHOUT FIRST SWITCHING OFF AND ISOLATING ALL POWER AND CONTROL SUPPLIES. CONSULT THE KRONES MANUAL FOR THE SITING POSITION OF THE MAINS ISOLATOR. THE ISOLATOR SHOULD THEN BE FIXED IN THE OFF POSITION BY USE OF A SUITABLE LOCKING DEVICE, I.E. PADLOCK, AND LABELLED WITH A `DANGER - DO NOT OPERATE' SIGN SO AS TO PREVENT ACCIDENTAL RE-CONNECTION OF POWER BEFORE ALL WORK IS COMPLETED. Warning: Non Ionising Radiation Black symbol on a yellow background.
Details
-
File Typepdf
-
Upload Time-
-
Content LanguagesEnglish
-
Upload UserAnonymous/Not logged-in
-
File Pages47 Page
-
File Size-