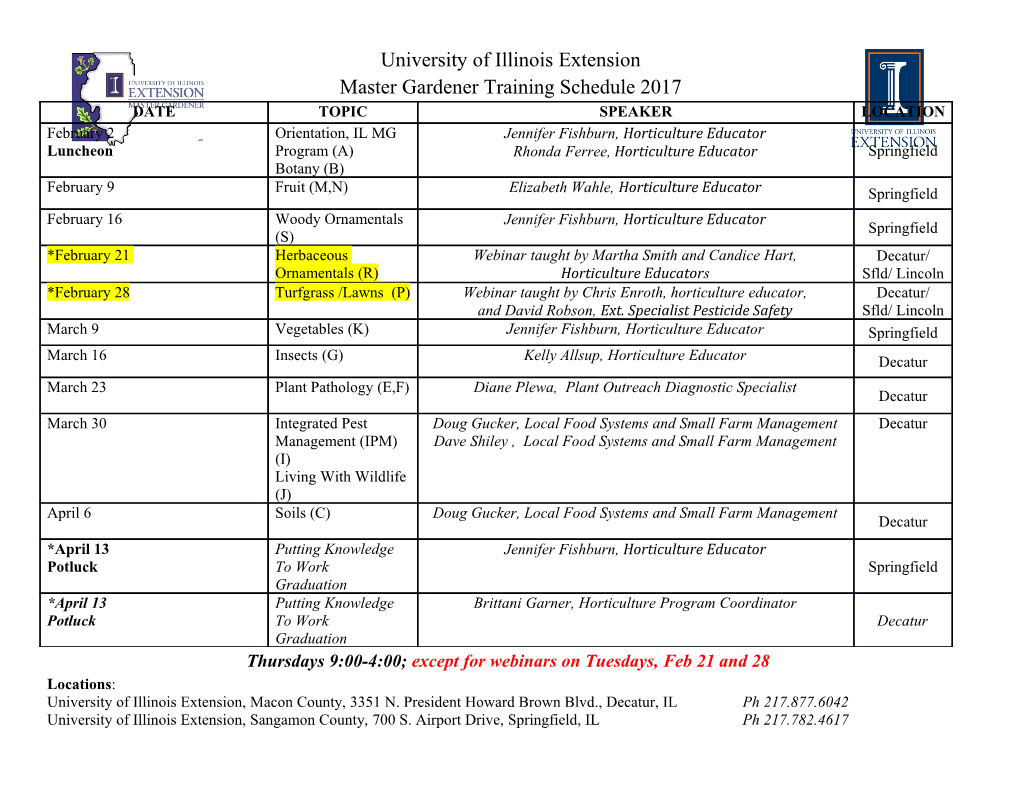
USOO7687568B2 (12) United States Patent (10) Patent No.: US 7.687,568 B2 Mueller et al. (45) Date of Patent: Mar. 30, 2010 (54) POLYESTER COLORANT CONCENTRATE 4,782,111 A 1 1/1988 Klein et al. 5,484.837 A 1/1996 Kung et al. (75) Inventors: Wolfgang Mueller, Premnitz/OT 5,604,279 A 2f1997 Bernhardt et al. Doeberitz (DE); Harald Eckhardt, EG R. 19O Whs tal Niederwerth (DE); Hans-Peter Koenig, -- w enzel et al. Montabaur (DE); Nathalie Fischbach, 7,066,993 B2 6/2006 Wuzik et al. ERAp.) Franz Thurnherr, FOREIGN PATENT DOCUMENTS a SC DE 1183,195 12, 1964 (73) Assignee: Clariant Masterbatches (Deutschland) DE 1594216 8, 1969 GmbH, Lahnstein (DE) DE 1965379 7, 1970 EP OOO8373 3, 1980 (*) Notice: Subject to any disclaimer, the term of this 3. patent is extended or adjusted under 35 GB 1044378 9, 1966 U.S.C. 154(b) by 0 days. GB 1249.720 10, 1971 WO WO91f13931 9, 1991 (21) Appl. No.: 11/663,521 OTHER PUBLICATIONS (22) PCT Filed: Sep. 17, 2005 PCT Search Report for PCT/EP2005/010054, mailed Dec. 21, 2005. (86). PCT No.: PCT/EP2005/010054 Kim D- et al., “Effects of Dispersing Agents on Dispersity and Mechanical Properties of Carbon Black/PET.” Polymer Engineering S371 (c)(1) and Science, Wiley, Hoboken, NJ. US vol. 39 No. 3, ppp. 500-507: . Mar. 1999. (2), (4) Date: Mar. 21, 2007 PCT English Translation of PCT International Preliminary Reporton (87) PCT Pub. No.: WO2006/032423 Patentability for PCT/EP 2005/010054, mailed Jul. 12, 2007. Primary Examiner Peter D Mulcahy PCT Pub. Date: Mar. 30, 2006 (74) Attorney, Agent, or Firm—Anthony A. Bisulca (65) Prior Publication Data (57) ABSTRACT US 2008/OO85959 A1 Apr. 10, 2008 Polyester colorant concentrates containing: 1) a polyester (30) Foreign Application Priority Data Supporting material; b) a colorant selected from the group of dyes and/or pigments; c) 0.1 to 2 parts by weight per part by Sep. 21, 2004 (DE) ....................... 10 2004 O45 639 weight of the colorant of copolyester comprising the reaction 51) Int. C product from (A) of at least one aliphatic primary dihydric (51) o 28.3/02 2006.O1 alcohol with 2 to 6 C atoms, and; (b) dicarboxylic acids ( .01) selected from the group consisting of phthalic acid, tereph (52) U.S. Cl. ........................... 524/513:524/88: 524/90; thalic acid, isophthalic acid and/or sebacic acid. The copoly 523/351 ester is characterized by having i) a melting range between (58) Field of Classification Search ................. 524/513, 120 and 160°C., ii) a melting viscosity SV ranging from 12 to 524/88, 90. 523/351 126 Pas, measured at 190° C. and 2.16 kg in accordance with See application file for complete search history. ISO 1133, and iii) a melting viscosity factor SF ranging from (56) References Cited -2.3 to -0.3 Pas/deg, determined at a temperature increase ranging from 160° C. to 240° C. with a shear rate of 109s. U.S. PATENT DOCUMENTS The inventive polyester colorant concentrates are particularly 3,436,301 A 4, 1969 McHale Suited for spin dyeing polyester fibers and filaments. 3,926,920 A 12/1975 Georgoudis et al. 4.279,802 A 7/1981 Laely et al. 10 Claims, No Drawings US 7,687,568 B2 1. 2 POLYESTER COLORANT CONCENTRATE is primarily dependent on the dispersing behavior in the car rier system, the particle size, the wettability by the carrier The invention relates to new polyester colorant concen system, and, to a Substantial degree, on the rheological (flow) trates obtainable by introducing a copolyester from the class behavior of the masterbatch system under the production and of polyester hotmelt adhesives having a defined melt viscos processing conditions. ity behavior for controlling the melt viscosity of the colorant/ In the case of carbon black/polyester products, therefore, polyester product for improved incorporation into a spinning the practical limit on the concentration of carbon black in the polymer. master is approximately 30%, owing to the Surface area/ There are numerous processes known for preparing poly volume ratio of the carbon black particles, the low wettability, ester colorant concentrates with a variety of carrier materials 10 and the associated high melt viscosity or structural viscosity and both with and without dispersing assistant. (dynamic viscosity) of the masters. For instance, EP-A-0 008373 describes the production of The production of masterbatches with pigments and/or a pigment preparation for the mass coloring of linear polyes dyes on the basis of polyester carrier systems is often accom ters, whereby from 20 to 80 parts of pigment and 80 to 20 panied, as a result of shearing in the course of extrusion or parts of a polyester that melts between 60 and 160° C. a 15 kneading, even after prior intensive (hot or warm) mixing, preconcentrate is prepared, by means of solvent salt knead slow mixing or addition of individual components, by ing, that is melted with a spinnable linear polyester and pro unwanted degradation of the polyester carrier. These poly cessed to pellets. mer-chain fragmentations lead to a reduction in the specific WO 91/13931 describes a process for producing highly Viscosity (intrinsic viscosity) of the carrier system and, con concentrated pigment concentrates (masters) with the highest sequently, also to a significant reduction in the specific vis achievable color strength, where a mixture of (A) one or more cosity (intrinsic viscosity) of the colored spinning polymer, pigments and/or fillers, (B) one or more anionic, nonanionic, with the consequences of reduced spinnability and a lower cationic, and electrically neutral wetting agents and/or (C) quality. One remedy, particularly with regard to the reduction one or more polymer carriers, and, where appropriate, further in specific viscosity, can be achieved in some cases through additives is charged to a suitable mixer, in which this mixture 25 the use of polyester carrier materials having higher specific is subjected to high shearing forces for a defined period of viscosities. However, the targeted adaptation of the melt vis time, until the composition melts as a result of the frictional cosity of the master to the melt viscosity of the polyester heat generated. spinning polymer is not possible with the known procedures. EP-A-0 1 14386 describes a process for producing polyes An aim of the invention is therefore to provide a method of ter colorant products where the colorant carrier is composed 30 adapting the melt viscosity (dynamic viscosity) and the spe of a linear polyester having a softening point of above 60° C. cific viscosity (intrinsic viscosity) of colorant-comprising and polybutylene terephthalate having a specific viscosity of polyester masters to the melt rheology of undoped, customary 0.5 to 1.5, measured at a polymer concentration of 1 g/100 ml spinning polymers for the production of polyester fiber and in dichloroacetic acid at 25° C., and the colorant product polyester filament. between 210°C. and 150° C., preferably between 200° C. and 35 In accordance with the invention the object is achieved by 160° C., has a recrystallization exotherm of 8 to 55 joules/g, adding a below-defined copolyester from the class of polyes and the colorant carrier comprises a copolyester of tereph ter hotmelt adhesives to the usual components used in a thalic acid/isophthalic acid and ethylene glycol. polyester colorant concentrate (master). Such as carbon black The use of copolyesters based on alkanediols and organic and/or pigments and/or dyes, here referred to as colorants, dicarboxylic acids as hotmelt adhesives is known through 40 and polyester carrier, and also, if desired, dispersing numerous publications. assistant(s), before or during the melting of the individual For instance, U.S. Pat. No. 3,926.920 discloses the prepa components or of the mixture by extrusion or kneading. ration of a heat-stable hotmelt adhesive with a low viscosity The invention provides a polyester colorant concentrate and a melting point of not more than 150°C., which is formed comprising by reaction from a mixture of at least one aliphatic glycol 45 (a) a polyester carrier material, having 2 to 6 carbonatoms and from a mixture of two or more (b) a colorant from the group of dyes and/or pigments, dicarboxylic acids or their functional dicarboxylic acid (c) 0.1 to 2 parts, preferably 0.5 to 1.5 parts, by weight perpart derivatives in defined concentration ratios. by weight of colorant of a copolyester comprising the DE-A 1594 216 describes the preparation of copolyester reaction product of compositions as hotmelt adhesive for use as footwear adhe 50 (A) at least one aliphatic primary dihydric alcohol having 2 sives, having a melting point of 70 to 160° C. and a relative to 6 carbon atoms and viscosity of 1.3 to 1.6, tested in a solution of 0.3 g of the (B) dicarboxylic acids from the group phthalic acid, copolyester in 50 ml of a solvent mixture of 41.2% 2.4.6- terephthalic acid, isophthalic acid and/or sebacic acid; trichlorophenol and 58.8% phenol at 25°C., the copolyester said copolyester having being formed by esterification of a mixture of dicarboxylic 55 (i) a melting range between 120 and 160° C., preferably acids and an aliphatic diol. The dicarboxylic acids are a mix between 130 and 150° C.; ture of terephthalic acid, isophthalic acid, and an aliphatic (ii) a melt viscosity MV of 12 to 126 Pas, measured at dicarboxylic acid having 6 to 36 carbon atoms, and the major 190° C. and 2.16 kg in accordance with ISO 1133; and molar fraction of the aliphatic diol is a butanediol, at at least (iii) a melt viscosity factor MF of -2.3 to -0.3 Pas/deg, 80 mol%.
Details
-
File Typepdf
-
Upload Time-
-
Content LanguagesEnglish
-
Upload UserAnonymous/Not logged-in
-
File Pages5 Page
-
File Size-