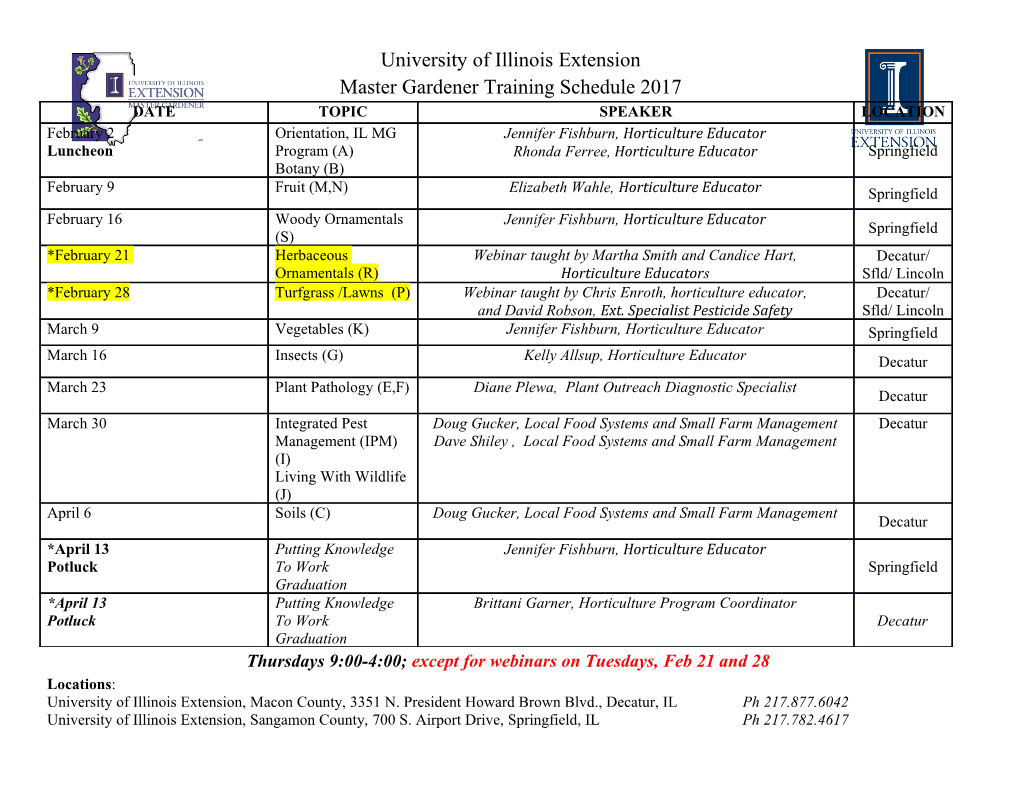
EPSON RC+ Ver.4.2 SPEL+ Language Reference Rev.3 EM086S1715F EPSON RC+ Ver.4.2 SPEL + Language Reference Rev.3 EPSON RC+ Ver.4.2 + SPEL Language Reference Rev.3 Copyright © 2007-2008 SEIKO EPSON CORPORATION. All rights reserved. SPEL+ Language Reference (Ver.4.2) Rev.3 i FOREWORD Thank you for purchasing our robot products. This manual contains the information necessary for the correct use of the EPSON RC+ software. Please carefully read this manual and other related manuals when using this software. Keep this manual in a handy location for easy access at all times. WARRANTY The robot and its optional parts are shipped to our customers only after being subjected to the strictest quality controls, tests and inspections to certify its compliance with our high performance standards. Product malfunctions resulting from normal handling or operation will be repaired free of charge during the normal warranty period. (Please ask your Regional Sales Office for warranty period information.) However, customers will be charged for repairs in the following cases (even if they occur during the warranty period): 1. Damage or malfunction caused by improper use which is not described in the manual, or careless use. 2. Malfunctions caused by customers’ unauthorized disassembly. 3. Damage due to improper adjustments or unauthorized repair attempts. 4. Damage caused by natural disasters such as earthquake, flood, etc. Warnings, Cautions, Usage: 1. If the robot or associated equipment is used outside of the usage conditions and product specifications described in the manuals, this warranty is void. 2. If you do not follow the WARNINGS and CAUTIONS in this manual, we cannot be responsible for any malfunction or accident, even if the result is injury or death. 3. We cannot foresee all possible dangers and consequences. Therefore, this manual cannot warn the user of all possible hazards. ii SPEL+ Language Reference (Ver.4.2) Rev.3 TRADEMARKS Microsoft, Windows, Windows logo, Visual Basic, and Visual C++ are either registered trademarks or trademarks of Microsoft Corporation in the United States and/or other countries. Other brand and product names are trademarks or registered trademarks of the respective holders. TRADEMARK NOTATION IN THIS MANUAL Microsoft® Windows® 2000 Operating system Microsoft® Windows® XPOperating system Throughout this manual, Windows 2000, and Windows XP refer to above respective operating systems. In some cases, Windows refers generically to Windows 2000, and Windows XP. NOTICE No part of this manual may be copied or reproduced without authorization. The content of this manual is subject to change without notice. We ask that you please notify us if you should find any errors in this manual or if you have any comments regarding its content. INQUIRIES Contact the following service center for robot repairs, inspections or adjustments. If service center information is not indicated below, please contact the supplier office for your region. Please prepare the following items before you contact us. • Your controller model and its serial number • Your manipulator model and its serial number • Software and its version in your robot system • A description of the problem SPEL+ Language Reference (Ver.4.2) Rev.3 iii SERVICE CENTER iv SPEL+ Language Reference (Ver.4.2) Rev.3 MANUFACTURER & SUPPLIER Japan & Others SEIKO EPSON CORPORATION Suwa Minami Plant Factory Automation Systems Dept. 1010 Fujimi, Fujimi-machi, Suwa-gun, Nagano, 399-0295 JAPAN TEL : +81-(0)266-61-1802 FAX : +81-(0)266-61-1846 SUPPLIERS North & South America EPSON AMERICA, INC. Factory Automation/Robotics 18300 Central Avenue Carson, CA 90746 USA TEL : +1-562-290-5900 FAX : +1-562-290-5999 E-MAIL : [email protected] Europe EPSON DEUTSCHLAND GmbH Factory Automation Division Otto-Hahn-Str.4 D-40670 Meerbusch Germany TEL : +49-(0)-2159-538-1391 FAX : +49-(0)-2159-538-3170 E-MAIL : [email protected] SPEL+ Language Reference (Ver.4.2) Rev.3 v SAFETY PRECAUTIONS Installation of robots and robotic equipment should only be performed by qualified personnel in accordance with national and local codes. Please carefully read this manual and other related manuals when using this software. Keep this manual in a handy location for easy access at all times. This symbol indicates that a danger of possible serious injury or death exists if the associated instructions are not WARNING followed properly. This symbol indicates that a danger of possible harm to people or physical damage to equipment and facilities exists if the associated instructions are not followed CAUTION properly. vi SPEL+ Language Reference (Ver.4.2) Rev.3 Table of Contents Summary of SPEL+ Commands 1 System Management Commands ................................................................................1 Robot Control Commands ............................................................................................1 Input / Output Commands.............................................................................................3 Coordinate Change Commands ...................................................................................4 Program Control Commands ........................................................................................4 Program Execution Commands....................................................................................5 Pseudo Statements.......................................................................................................5 File Management Commands.......................................................................................6 Numeric Value Commands...........................................................................................6 String Commands .........................................................................................................7 Logical operators ..........................................................................................................8 Variable commands ......................................................................................................8 Commands used with VB Guide...................................................................................8 Ethernet I/O commands ................................................................................................9 Fieldbus I/O commands................................................................................................9 Force sensing commands...........................................................................................10 Security commands ....................................................................................................10 Conveyor Tracking Commands ..................................................................................10 Operator Pendant Commands....................................................................................11 SPEL+ Language Reference 13 SPEL+ Error Messages 567 SPEL+ Language Reference (Ver.4.2) Rev.3 vii viii SPEL+ Language Reference (Ver.4.2) Rev.3 Summary of SPEL+ Commands The following is a summary of SPEL+ commands. System Management Commands Reset Reset the controller. Stat Returns controller status bits. Ver Displays controller setup. Date Sets the system date. Time Sets system time. Date$ Returns the system date. Time$ Returns system time as string. Hour Displays / returns controller operation time. Time Sets system time. Errhist Displays error history. ShutDown Shuts down RC+ and Windows. Robot Control Commands Calib Calibrates motors. CalPls Sets / returns calibration values. Hofs Sets / returns offset pulses between encoder origin and home sensor. Mcal Calibrates incremental encoder robots. MCordr Sets / returns joint order of Mcal. Mcorg Automatically calculates calibration parameters for Mcal. MCofs Sets / returns MCal parameters. HTest Displays / returns pulse count from home sensor to encoder Z phase. SPEL+ Language Reference (Ver.4.2) Rev.3 1 Summary of SPEL+ Commands Power Sets / returns servo power mode. Motor Sets / returns motor status. SFree Removes servo power from the specified servo axis. SLock Restores servo power to the specified servo axis. Jump Jump to a point using point to point motion. Jump3 Jump to a point using 3D gate motion. Jump3Cp Jump to a point using 3D motion in continuous path. Arch Sets / returns arch parameters for Jump motion. LimZ Sets the upper Z limit for the Jump command. Sense JS Returns status of Sense operation. JT Returns the status of the most recent Jump command for the current robot. Go Move the robot to a point using point to point motion. Pass Executes simultaneous four joint Point to Point motion, passing near but not through the specified points. Pulse Move the robot to a position defined in pulses. BGo Executes Point to Point relative motion, in the selected local coordinate system. BMove Executes linear interpolation relative motion, in the selected local coordinate system. TGo Executes Point to Point relative motion, in the current tool coordinate system. TMove Executes linear interpolation relative motion, in the selected tool coordinate system. Till Specifies motion stop when input occurs. !…! Process statements during motion. Speed Sets / returns speed for point to point motion commands. Accel Sets / returns acceleration and deceleration for point to point motion. Weight Specifies or displays the inertia of the robot arm. Arc Moves the arm using circular interpolation. Arc3 Moves the arm in 3D using circular interpolation. Move Move the robot using linear interpolation. CV
Details
-
File Typepdf
-
Upload Time-
-
Content LanguagesEnglish
-
Upload UserAnonymous/Not logged-in
-
File Pages600 Page
-
File Size-