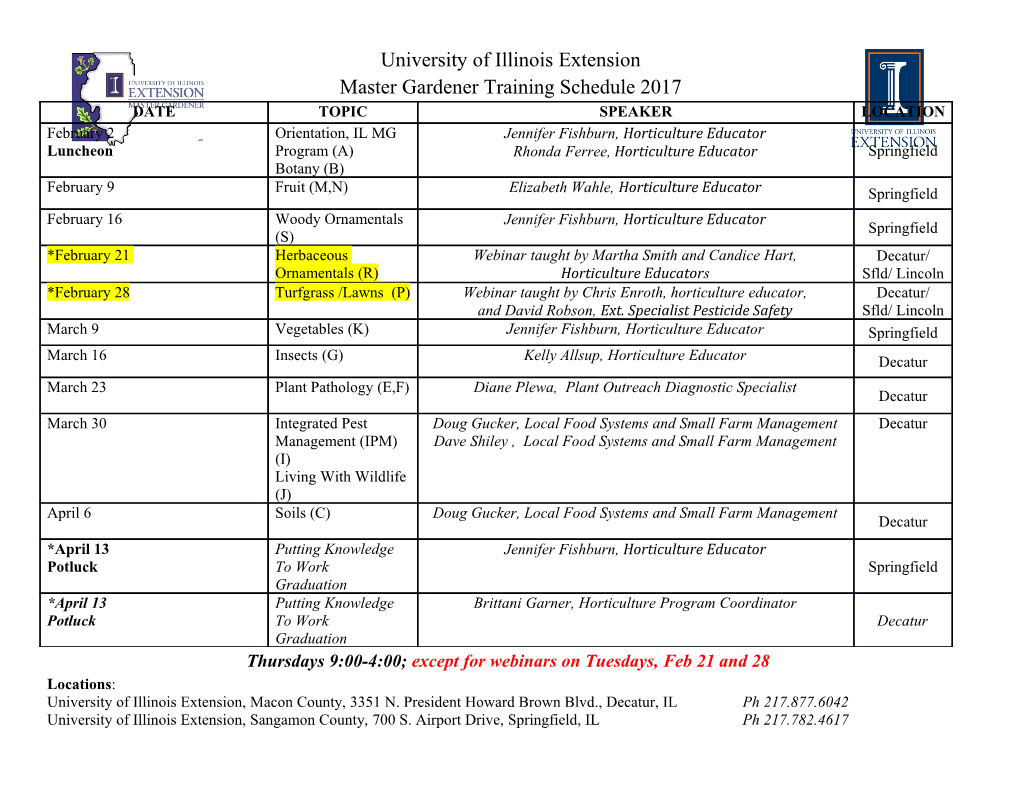
A THREE Axis CNC ROUTER DESIGN by Alexander D. Sprunt SUBMITTED TO THE DEPARTMENT OF MECHANICAL ENGINEERING IN PARTIAL FULFILLMENT OF THE REQUIREMENTS FOR THE DEGREE OF BACHELOR OF SCIENCE AT THE MASSACHUSETTS INSTITUTE OF TECHNOLOGY JANUARY 2000 __~~X (j'T-)(D @ 2000 Alexander D. Sprunt All rights reserved The author hereby grants to MIT permission to reproduce and to distribute publicly paper and electronic copies of this thesis document in whole or in part. S ignature of A uthor ........................................................ ................ ................................. Dep rtment of Mechanical Engineering January 14, 2000 Ce rtified by ............................ { .... ......... .................................................................. Alexander H. Slocum Margaret MacVicar Faculty Fellow Professor of Mechanical Engineering Thesis Supervisor Accepted by .......................................... ............................................................................ Ernest George Cravalho MASSACHUSETTS INSTITUTE Professor of Mechanical Engineering OF TECHNOLOGY Chairman, Undergraduate Thesis Committee JUN 2 8 2000 ARCHIVESACIE LIBRARIES1 A THREE Axis CNC ROUTER DESIGN by Alexander D. Sprunt Submitted to the Department of Mechanical Engineering on January 14, 2000 in Partial Fulfillment of the Requirements for the Degree of Bachelor of Science in Mechanical Engineering ABSTRACT A preliminary design of a low-cost, three-axis, computer numerically controlled (CNC) router was completed with the goal of bringing the advantages of numerically controlled machine tools to the woodshop. To reduce cost, a novel single rail design was employed. The number of custom parts was kept to a minimum and, where necessary, every effort was made to minimize manufacturing cost. The novel features of the design include vacuum clamping, the ability to cut joinery at miter angles from 0* to 90*, and force controlled cutting. Many of the components are used quite aggressively (particularly with regard to stiffness), but the accuracy goal of ±0.005" in X and Y and +0.010" in Z was met. Thesis Supervisor: Alexander H. Slocum Title: Margaret MacVicar Faculty Fellow Professor of Mechanical Engineering 3 List of Symbols ball screw lead angular velocity Mioad mass of the load being moved Jtrans inertia of the transmission Fload external load Not optimal transmission ratio x a length (context sensitive) r constant for ball screw selection - accounts for external load c constant for ball screw selection - accounts for trajectory shape Cbuckle buckling constant kwhi, shaft whip constant E Young's modulus P mass density I 2 nd Moment of inertia (for beam bending, etc.) AX Cross-sectional area te Cycle time (ball screw selection) a Acceleration time (ball screw selection) b Deceleration time (ball screw selection) s, Shaft whip safety factor Sb Shaft buckling safety factor d Ball screw diameter Wd Heat dissipation in motor armature coil Ra Motor coil resistance K, Motor torque constant T, Torque i F, Force i J Inertia i L Life constant for calculating linear guide life {1 05 or 5-1 04} C Load capacity (bearing and ball screw life) dalong Distance between two trucks along a linear guide daco,, Distance between two trucks perpendicular to a linear guide n Bearing life equation coefficient a Angular acceleration PO Outside pressure 4 P Inside pressure Pam Atmospheric pressure Q Volumetric flow rate Cd Coefficient of discharge 91 Reynold's Number t Thickness v Velocity P Viscosity T Temperature R Ideal gas constant Ai Area i q7 Efficiency #8 An angle for ball screws 0 An angle G Shear modulus 3, Displacement i 3 Friction force Fn Normal force P, Static coefficient of friction Nholes Number of holes in the optical table All units are in Systeme Internationale unless otherwise noted. 5 Introduction This thesis describes the preliminary design of a low-cost router table that brings the benefits of computer numerical control (CNC) tools to the woodshop. The router introduces entirely new capabilities such as full three-dimensional shaping to the shop in addition to obviating the need for several conventional woodworking implements such as joinery jigs and conventional table routers. Tiresome and repetitive tasks can also be automated for superior output and increased throughput. Cost reduction was accomplished using a novel, single rail, design that minimizes part count and eases assembly. There are relatively few custom parts, and those required were designed with attention to manufacturability. During the course of the project, numerous safety, performance, and ease of use advantages were developed for a force controlled cutting system that could easily be implemented using the hardware that was the principal focus of this thesis. Naturally, there is a balance between cost and performance. With that in mind, a reasonable set of specifications was chosen and the design effort was focused on maximizing the potential of the available hardware. 6 Specifications and Features Footprint 3' x 4'6" + computer Work Volume 2'6" x 5' x 10" Router 3 hp, 8-22 krpm, '/2" collet Accuracy ±0.005" for the Y and X Axes, ±0.010 for the Z-Axis Feed Rate 20 fpm Vacuum Clamping Vacuum Chip Removal Joinery Capable Force Controlled Cutting Table 1 The specifications and features were developed in consultation with Ken Stone, Director of the MIT Hobby Shop. The last two features were added midway through the project and will be described in detail later. See the Appendix for competitive benchmarking data. 7 Now Configuration An optical table was selected as the machine's base with the intention of mounting the table nearly vertically to meet the footprint specification. The optical table provides an inexpensive, lightweight, precision surface that is essentially pre-configured for vacuum clamping (see Vacuum Clamping section). Three initial configurations were considered, one open (Configuration A, Figure 1) and two closed (Configurations B and C, Figures 3 and 2). A structure is closed if its components form a loop, and open if they do not. For example, a "U"shape is an open structure, while an "0"shape is closed. Of the closed configurations, the one with the longer axis fully supported (B) was clearly superior. Open structures are inherently more compliant than closed structures, but are also simpler and less expensive, so once a preliminary spreadsheet analysis of the structure's stiffness established that it could be stiff enough, an open structure was pursued. Figure 1: Configuration A (Open) Figure 2: Configuration Fon Figure 3: Configuration B (Closed) 8 -1 A-Axis --... Fixed Supports to elevate the Y-Axis -~ Figure 4: More complete view of configuration A Reflection on the strengths of configuration A created configurations D and E (See Figures 5 and 6). Configurations D and E placed the linear guide for the long axis directly on the optical table that serves as the machine's base. This change eliminated the need to transfer a reference surface more than a foot up from the optical table. Placing the long axis directly on the optical table also removed any problems from the axis twisting along the unsupported span. 9 Optical Table Figure 5: Configuration D 10 Figure 6: Configuration E The names of the axes will now be defined (See Figure 5 and 6). The Y-Axis is the longest axis (over 60") and its linear guide is mounted directly to the optical table. The X-Axis (30") extends across the plane of the optical table orthogonally to the Y-Axis. The Z-Axis (over 10") is orthogonal to the plane of the optical table. The rotation axes are named A, B, and C in order based on which linear axis their rotation axis is parallel to. For example, an A-Axis will revolve around a rotational axis that is parallel with the X-Axis, while a B-Axis will revolve around an axis parallel to the Y-Axis, and so on. 11 The essential difference between Configurations D and E is that Configuration D places the Z-Axis at the end of the X-Axis instead of placing the X-Axis on the Z-Axis as in Configuration E. Configuration D thus enables the router to go into and cut deep cavities. By cantilevering so much mass, however, Configuration D will have a lower first natural frequency. It is important that the first natural frequency be above 30 Hz., or the machine will tend to ring. Ringing can damage the work piece and make the machine uncontrollable. Further consultation with the Director of the MIT Hobby Shop revealed that Configuration D had few advantages over configuration E because woodworking rarely requires cutting into deep cavities. Such activity is largely confined to mold and pattern making specialties, which represent only a tiny fraction of all woodworking activity. Consultation also revealed the great utility of having a joinery cutting capability. Joinery is cut on the edges of boards (See Figure 7), however, and neither configuration had the ability to work edges longer than the Z-Axis. Figure 7: Router cutting joinery Two methods were developed for relieving this edge length limitation. One was to create a manual B-Axis that could cut joinery on boards mounted to a second optical table that was perpendicular to the primary machine base (See Figure 6). The other option was to create a manual A-Axis. The router motor would be rotated 90* and driven to an extension to the end of the Y-Axis (See Figure 4). With either of these options, joinery could be cut in the edges of pieces as long as the Y-Axis. Using an A-Axis had the obvious advantages of involving fewer parts, requiring less assembly work, and being able to cut joinery into longer edges. There were two possible locations for the rotational joint of the A-Axis. The joint could be integrated with the casting for connecting the X-Axis with the Z-Axis (the entire X-Axis linear module would rotate along with the router head) or the joint could be built into the mount for the router.
Details
-
File Typepdf
-
Upload Time-
-
Content LanguagesEnglish
-
Upload UserAnonymous/Not logged-in
-
File Pages39 Page
-
File Size-