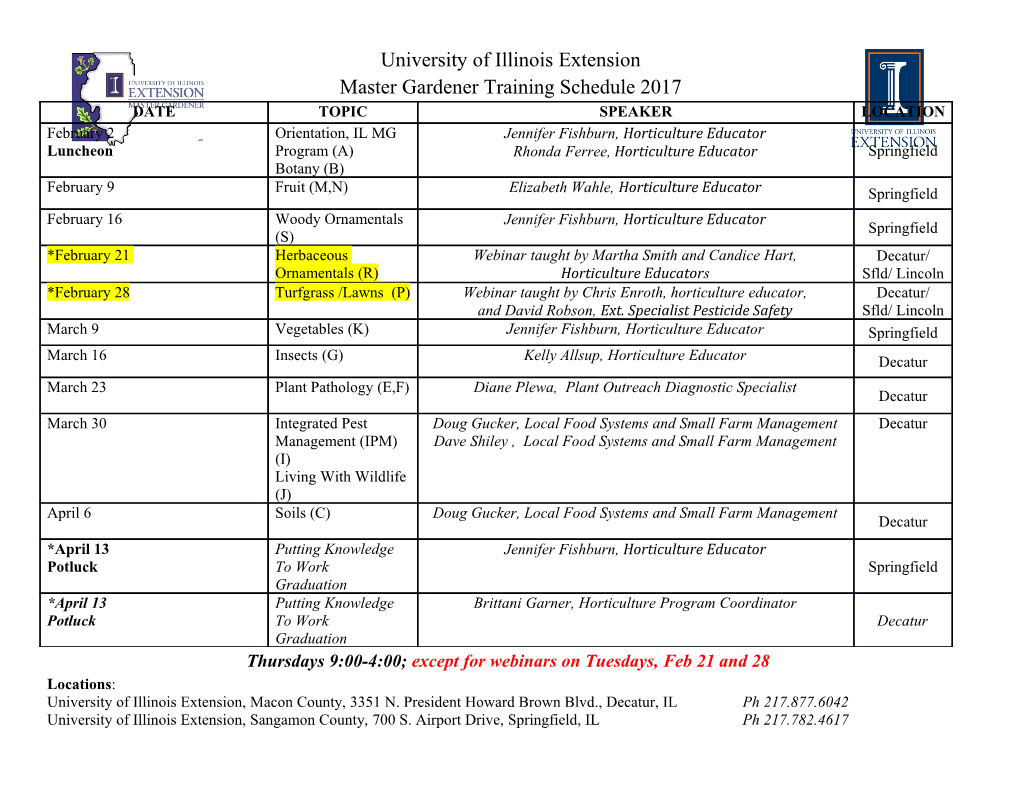
sensors Letter MAELASviewer: An Online Tool to Visualize Magnetostriction Pablo Nieves * , Sergiu Arapan , Andrzej Piotr K ˛adzielawa and Dominik Legut IT4Innovations, VŠB—Technical University of Ostrava, 17. listopadu 2172/15, 70800 Ostrava-Poruba, Czech Republic; [email protected] (S.A.); [email protected] (A.P.K.); [email protected] (D.L.) * Correspondence: [email protected] Received: 27 September 2020; Accepted: 9 November 2020; Published: 11 November 2020 Abstract: The design of new materials for technological applications is increasingly being assisted by online computational tools that facilitate the study of their properties. In this work, based on modern web application frameworks, the online app MAELASviewer has been developed to visualize and analyze magnetostriction via a user-friendly interactive graphical interface. The features and technical details of this new tool are described in detail. Among other applications, it could potentially be used for the design of magnetostrictive materials for sensors and actuators. Keywords: magnetostriction; magnetoelastic effects; graphical user interface; web application; visualization 1. Introduction Magnetostriction is a physical phenomenon in which the process of magnetization induces a change in the shape or dimension of a magnetic material. These materials have the advantage that their magnetostrictive properties do not degrade over time as is the case for some poled piezoelectric materials, in addition to their good performance in terms of strains, forces, energy densities, and coupling coefficients [1]. As a result, magnetostrictive materials are widely used in many technological applications like sensors (torque sensors, motion and position sensors, force and stress sensors) and actuators (sonar transducers, linear motors, rotational motors, and hybrid magnetostrictive/piezoelectric devices) where a high magnetostriction is required [2–4]. Conversely, in other applications such as electric transformers, motor shielding, and magnetic recording, it is important to reduce the magnetostriction of the magnetic materials [5] as much as possible. Currently, magnetostrictive materials have some drawbacks such as the size and weight required in some applications, high manufacturing cost, and high non-linear and hysteretic effects. These limitations might be overcome by optimizing the design of the materials and their applications. Thanks to modeling techniques, significant improvements have been made in relation to these problems [1]. The study and design of different properties of materials are being increasingly assisted by online visualization tools. For instance, ELATE (an open-source online application for analysis and visualization) is an online user-friendly interface that has been implemented to analyze second-order elastic stiffness tensors and visualize anisotropic mechanical properties [6]. It makes use of a Python module to generate an HTML web page with embedded Javascript for interactive dynamical plots. A similar approach could also be particularly useful in the case of magnetostrictive materials since magnetostriction can be highly anisotropic. Recently, we have developed the MAELAS code [7,8] to calculate magnetostrictive coefficients by automated first-principles calculations. As a complementary online tool of MAELAS, in this work we present the app MAELASviewer to visualize and analyze magnetostriction. The online application is available at https://maelasviewer.herokuapp.com/, Sensors 2020, 20, 6436; doi:10.3390/s20226436 www.mdpi.com/journal/sensors Sensors 2020, 20, 6436 2 of 14 while the open-source Python module is available at GitHub repository https://github.com/ pnieves2019/MAELASviewer. 2. Overview of Magnetostriction 2.1. Theoretical Description The main magnetostriction effects are the Joule effect (length change along the same direction as the magnetic field), Villari effect (magnetization change due to a mechanical stress applied), Wiedemann effect (twisting of a magnetostrictive cylinder when helical magnetic field is applied to the material), and Matteucci effect (induced helical magnetization by a torsion). In this section, we provide a brief introduction to the equations that describe the field-induced magnetostriction (Joule effect and Wiedemann effect), which are implemented in the app MAELASviewer. A more detailed discussion about this topic can be found in [7,9–13]. 2.1.1. Relative Length Change Due to the Joule Effect Frequently, the physical quantity of interest related to the Joule effect is the change of a material’s length along a measuring direction. It is given by the relative length change (l − l0)/l0 = Dl/l0, where l0 is the initial length of a demagnetized material along a measuring direction b (jbj = 1), and l is the final length along the same direction b when the system is magnetized along the direction a (jaj = 1), see Figure1. For instance, the relative length change for a cubic single crystal system (point groups 432, 43¯ m, m3¯m) can be written as [9] a Dl a 3 2 2 2 2 2 2 1 = l + l001 ax bx + ayby + az bz − l0 2 3 b (1) + 3l111(axaybx by + ayazbybz + axazbx bz), a where coefficient l describes the volume magnetostriction (isotropic), while l001 and l111 are the anisotropic magnetostrictive coefficients that give the fractional length change along the [001] and [111] directions when a demagnetized material is magnetized in these directions, respectively. In the case of hexagonal crystal systems (point groups 6mm, 622, 6¯2m, 6/mmm), the relative length change reads [9,10,14] a Dl a1,0 2 2 a2,0 2 a1,2 2 1 2 2 = l (bx + by) + l bz + l az − (bx + by) l0 3 b 1 1 (2) + la2,2 a2 − b2 + lg,2 (a2 − a2)(b2 − b2 ) + 2a a b b z 3 z 2 x y x y x y x y e,2 + 2l (axazbx bz + ayazbybz). These magnetostrictive coefficients are related to the normal strain modes for a cylinder [9,10]. In addition to cubic and hexagonal systems, MAELASviewer also supports other single crystals like trigonal systems (point groups 32, 3m, 3¯m), tetragonal systems (point groups 4mm, 422, 4¯2m, 4/mmm), and orthorhombic systems (point groups 222, 2mm, mmm). The equation of the relative length change for these systems can be found in [7]. The implemented equations include the magnetostrictive coefficients up to the second-order of the direction cosine polynomial. Sensors 2020, 20, 6436 3 of 14 Figure 1. Sketch of the (a) Joule effect and (b) Wiedemann effect. Typically, single-crystal magnetostrictive alloys help to understand and characterize the material behavior in the design stage of the material. However, magnetostrictive polycrystalline alloys are more convenient than single crystals for macroscale applications due to the lower production cost and a faster production rate. A widely used approximation to describe magnetostriction for polycrystals is to assume that the stress distribution is uniform through the material. For polycrystalline cubic systems (point groups 432, 43¯ m, m3¯m) the relative change in length may be put into the form [9,15,16] a Dl 3 2 1 3 2 1 = lS (a · b) − = lS cos x − , (3) l0 2 3 2 3 b where x is the angle between magnetization and measuring directions, and 2 3 l = l + l . (4) S 5 001 5 111 This equation describes an isotropic magnetostriction because the relative change in length depends on the magnetization direction in the same way for any measuring direction. Note that polycrystalline cubic systems might not exhibit an isotropic magnetostriction when l001 and l111 do not have the same sign and order of magnitude, the elastic tensor is not close to being isotropic, and there is a crystallographic texture [12]. On the other hand, the relative change in length for intrinsically isotropic materials like amorphous alloys without growth anisotropy can be well described in the form of Equation (3)[12]. We have also implemented Equation (3) in MAELASviewer. 2.1.2. Deformation Due to the Joule Effect The total deformation induced by the Joule effect can be described in terms of the displacement vector u(r) = r0 − r that gives the displacement of a point at the initial position r in the demagnetized material to its final position r0 in the magnetized state. For small deformations, the displacement vector can be calculated by solving [17] ! me 1 ¶ui ¶uj eij = + , i, j = x, y, z (5) 2 ¶rj ¶ri me where eij is the equilibrium magnetostrictive strain tensor given by the minimization of both the elastic and magnetoelastic energies [9,10]. The equilibrium magnetostrictive strain tensor is linked to the relative length change via [9,10] a Dl me = ∑ eij bi bj. (6) l0 b i,j=x,y,z Sensors 2020, 20, 6436 4 of 14 For instance, the equilibrium magnetostrictive strain tensor for a cubic single crystal (point groups 432, 43¯ m, m3¯m) reads [9,10] 0 1 0 1 0 1 1 0 0 a2 − 1 0 0 0 a a a a 3 x 3 3 x y x z me = a B C + B 2 − 1 C + B C e l @0 1 0A l001 @ 0 ay 3 0 A l111 @ayax 0 ayazA . (7) 2 2 1 2 0 0 1 0 0 az − 3 azax azay 0 This strain tensor contains three magnetostriction symmetries or normal strain modes for a cube. Namely, a volume change is given by la that does not depend on magnetization direction, while normal and shear deformations are related to l001 and l111, respectively [9,10]. In practice, Equation (5) can be solved numerically by finite element modeling (FEM) techniques. To illustrate this method we have used the FEM software COMSOL Multiphysics [18] to calculate the deformation of face-centered cubic −6 −6 (FCC) Ni (l001 = −46 × 10 and l111 = −24 × 10 [13]) induced by the Joule effect (without volume magnetostriction la = 0) for three simple geometries: cube, cylinder, and sphere with characteristic length 1µm. The results of the simulation are presented in Figure2. We see that the magnitude of the −11 maximum displacement vector is of the order 10 m for these material sizes.
Details
-
File Typepdf
-
Upload Time-
-
Content LanguagesEnglish
-
Upload UserAnonymous/Not logged-in
-
File Pages14 Page
-
File Size-