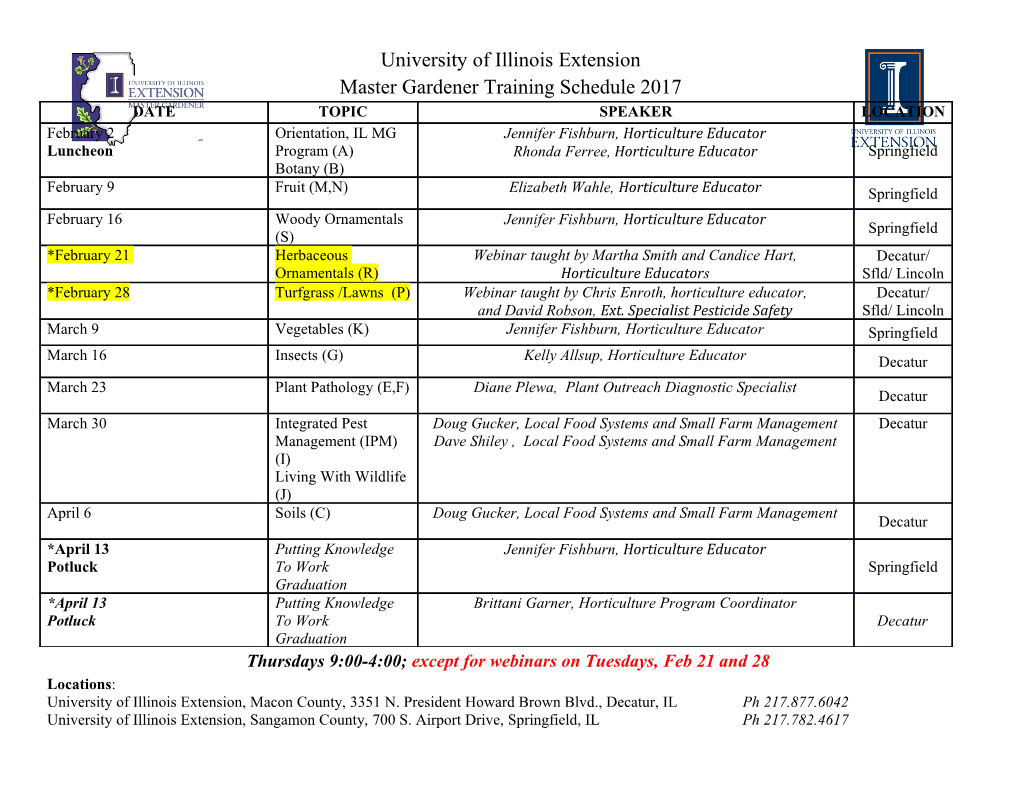
Construction Science 10.2478/cons-2013-0008 2013 /14____________________________________________________________________________________________________________ Microstructural Investigations of Ultra-High Performance Concrete Obtained by Pressure Application within the First 24 Hours of Hardening Janis Justs1, Diana Bajare2, Aleksandrs Korjakins3, Gundars Mezinskis4, Janis Locs5, Girts Bumanis6, 1-6 Riga Technical University Abstract. In this study, the effect of pressure application (0–50 There are examples of commercially available UHPC that is MPa) to fresh concrete right after casting and during the first 24 used in the construction industry today. One such example is hours of hardening has been examined. Supplementary Ductal®. The Ductal® technology was developed by the cementitious materials in a form of silica fume, nanosilica and combined efforts of three companies: Lafarge – the ground quartz sand were used. The aim of pressure application construction materials manufacturer, Bouygues – the was to reduce porosity, thus improving concrete mechanical properties. Considerable reduction in porosity and a subsequent contractor in civil and structural engineering and Rhodia – the increase in compressive strength reaching the level of Ultra-High chemical materials manufacturer [11]. Performance Concrete (UHPC) were achieved. Mechanical and The aim of this study is to investigate the influence of physical properties were tested and gas sorption porosimetry, pressure applied during the sample hardening process. mercury intrusion porosimetry (MIP), X-ray diffraction (XRD), Concrete mix composition with the designed compressive as well as scanning electron microscopy (SEM) were used for strength of approximately 100 MPa at 28 days was selected as material characterization. a basic mix. Pressure has been applied right after casting in order to improve concrete properties. Mechanical strength of Keywords: Ultra-High Performance Concrete (UHPC), prepared samples was compared. By pressing concrete in the pressure application, porosity, compressive strength fresh state, most of entrapped air can be eliminated and pore diameters reduced. Distance between particles determines I. INTRODUCTION most of the concrete properties. Elimination of voids and Ultra-high performance concrete (UHPC) is a modern reduction of pore diameters would result in enhancement of building material with superior properties. such as high concrete performance [12; 13]. As the macroscopic properties compressive strength, high modulus of elasticity, low of UHPC are related to its microstructure, porosity, pore-size permeability and excellent durability. All these properties can distributions as well as morphology of hydration products be achieved taking into account some basic principles and were analysed by using SEM and Hg porosimetry. UHPC processing methods that can be listed as follows: (i) strength border of 150 MPa was reached by applying the minimizing defect occurrence in a concrete matrix and pressure of 50 MPa. obtaining maximum density by optimizing particle size distribution; (ii) minimizing water/cement ratio by the use of II. MATERIALS AND METHODS water reducing admixtures; (iii) using pozzolanic materials, A. Materials such as silica fume, to fill voids between larger particles, to improve rheological properties and to enhance secondary The materials used in this study were commercially calcium silicate hydrate formation; (iv) incorporation of steel available raw materials, cementitious materials and fibers to prevent brittle failure and polypropylene fibers, to admixtures. Chemical composition of CEM I 42.5 N Portland increase UHPC fire resistance [1-6]. cement was tested according to the standard LVS EN 196- In 1994 Richard and Cheyrezy [5] produced reactive 2:2005, and results are given in Table 1. powder concrete (RPC) with the compressive strength of 800 The initial cement setting time was 182 min and the final MPa. RPC is a type of UHPC that is characterized by very fine setting – 224 min (according to LVS EN 196-3:2005), the particles, and no coarse aggregate is present. Production normal consistency was 28.2% (according to LVS EN 196- technology included pressure application and heat treatment. 3:2005). 2 First demonstrations of UHPC outside laboratory were in Blaine fineness of cement was 3787cm /g (according to footbridges. These structures appeared at the end of 1990s. LVS EN 196-6:2010). Na equivalent was 1.68. Compressive Some of the most well-known examples are in Sherbrook strength after 1 day was 15.4 MPa, after 2 days – 32.9 MPa, (1997), Seoul (2002) and Kassel (2007) [7-9]. The first two after 7 days – 48.8 MPa and after 28 days – 60.5 MPa. road bridges using UHPC with the compressive strength of more than 170 MPa were built in France in 2001 (Bourg-lès- Valence bypass) [10]. 50 Unauthenticated Download Date | 12/11/16 7:36 PM Construction Science ____________________________________________________________________________________________________________2013 /14 TABLE I CHEMICAL COMPOSITION OF CEMENT AND POZZOLANIC ADDITIVES, [WEIGHT %] Silica fume* Nanosilica** Cement SiO2 98.4 99.99 18.85 Al2O3 0.20 4.37 Fe2O3 0.01 3.09 CaO 0.20 61.98 MgO 0.10 3.64 SO3 0.10 3.18 Na2O 0.15 0.22 K2O 0.20 1.25 TiO2 0.32 Fig. 1. Particle size distribution of the selected concrete mix. Cl 0.08 P2O5 0.06 C. Mixing Procedure Mn2O3 0.08 The mixing procedure of materials was the following: all Other 0.60 2.88 dry materials were mixed by a high speed electric paddle Total 100.00 100 100.00 mixer until a homogenous mixture was obtained (for 1 min). *From Elkem Microsilica 971material datasheet Then water and superplasticizer were added in two steps. ** From Elkem NanoSilica 999 material datasheet During the first step 70% of water was added and the batch was mixed for 1.5 minutes. During the second step the rest of According to material datasheet, 100% of nanosilica the water together with the full amount of superplasticizer was particles had sizes below 400 nm and 99.8% of silica fume added. Mix with the cone slump of class S2 (according to LVS particles were smaller than 45 µm. 90% of silica fume EN 12350-2) was obtained at the end of mixing. Total mixing particles had dimensions ranging from 20 nm to 0.5 µm, but time was approximately 6 minutes. size of nanosilica particles was in the interval between 20 and 100 nm. Polycarboxylate ether based superplasticizer (PCE) D. Experimental Setup was used. The W/C ratio was 0.25. Basic concrete mix was designed in order to provide 28-day compressive strength in The experimental setup for pressure applied cylindrical the range of 100 MPa. Mix composition is given in Table 2. specimen with a diameter of 50 mm and height of 100 mm is shown in Fig. 2. TABLE II CONCRETE MIX COMPOSITION Material Quantity, kg/m3 Cement CEM I 42,5 N 800 Sand 0.3-2.5 mm 510 Sand 0-1.0 mm 480 Ground quartz sand 200 Silica fume 100 Nanosilica 20 Superplasticizer 20 Water 200 B. Particle Size Distribution Grading of materials is essential to produce UHPC. Particle size distribution of sand was obtained by sieving. Ground quartz sand particle size distribution was measured by particle size and Zeta potential analyzers “90 Plus MAS, ZetaPALS Fig. 2. Experimental setup for pressure application to the specimens. Brookhaven Industries”. To optimize packing of available materials down to nano- Customized cylindrical mold with an inner diameter of 50 scale, software from Elkem materials based on modified mm and adjustable height was designed and produced for the Andreassen particle packing model [3] was used (curve current study. The mold consisted of 3 high precision details: a central cylinder and two pistons closing the cylinder from both parameters q=0.25, Dmax = 2.5 mm and Dmin = 0.0001 mm were selected). ends. In order to remove the entrapped air and reduce pore Particle size distribution curve of the selected mix is given sizes, pressure of 10, 20, 30, 40 and 50 MPa was applied by a in Fig. 1. manual hydraulic press right after concrete casting and retained constant for 24 hours. Due to relatively low W/C ratio (0.25), little to no excess water was observed. Pressure 51 Unauthenticated Download Date | 12/11/16 7:36 PM Construction Science 2013 /14____________________________________________________________________________________________________________ readings were taken from the manometer installed on top of samples hardened under different pressure levels are shown in the press. Fig. 4. After the first 24 hours pressure was removed and the specimens were remolded and cured in the water at the temperature of 20˚C until the age of 28 days. E. Testing Methods of Concrete Mechanical, physical and microstructural investigations were carried out for specimens at the age of 28 days and 6 months. Mechanical properties were determined according to LVS EN 12390-3:2009 “Testing hardened concrete – Part 3: Compressive strength of test specimens”. Density was detremined according to LVS EN 12390- 7:2009 “Testing hardened concrete – Part 7: Density of Fig. 4. Density of the 28-day-old specimens depending on hardening pressure hardened concrete”. Porosity was detremined according to applied. ASTM C642-06 Standard Test Method for Density, Absorption, and Voids in Hardened Concrete. Two different regions can be clearly distinguished: samples Pore volume and pore sizes were determined by hardened without pressure and samples initially hardened Porosimeter NOVA 1200Е (0.35–200 nm) “Quantachrome under the pressure of 10–50 MPa. Figure 4 shows that the Instruments” and Hg Porosimeter Pore Master 33 (0.0064–950 most significant increase in density is observed, when pressure µm) “Quantachrome Instruments”. The samples were is increased from 0 to 10 MPa indicating removal of most of observed by the field emission scanning electron microscope the entrapped air from the specimens. In the next interval, Mira\LMU “Tescan”, and the elemental composition of the when pressure ranges from 10 to 50 MPa, density increases observed phases was assessed by the energy dispersive X-ray almost linearly, but the average increase rate is 7.6% of that spectrometrer (EDX) Inca 350 “Oxford instruments” installed observed in the first interval.
Details
-
File Typepdf
-
Upload Time-
-
Content LanguagesEnglish
-
Upload UserAnonymous/Not logged-in
-
File Pages8 Page
-
File Size-