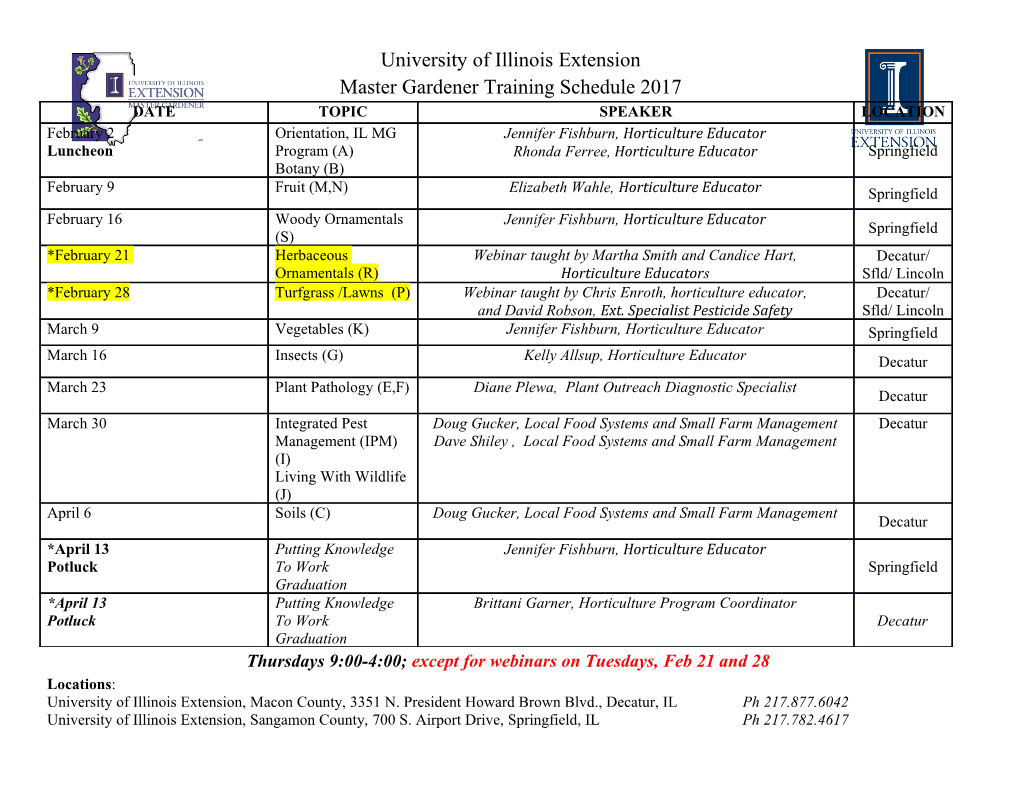
UNIVERSITY OF CALIFORNIA Los Angeles High Frequency Dynamics of Magnetoelastic Composites and their Application in Radio Frequency Sensors A dissertation submitted in partial satisfaction of the requirements for the degree Doctor of Philosophy in Mechanical Engineering by Paul Killian Nordeen 2016 © Copyright by Paul Killian Nordeen 2016 ABSTRACT OF THE DISSERTATION High Frequency Dynamics of Magnetoelastic Composites and their Application in Radio Frequency Sensing By Paul Killian Nordeen Doctor of Philosophy in Mechanical Engineering University of California, Los Angeles, 2016 Professor Gregory P. Carman, Chair Recently the consumer electronics market has experienced a major demand for autonomous, networked devices which can collect and process information independently from the operator. These “smart” devices are the constituents of a larger computing paradigm known as the internet of things which seeks to combine environmental sensing, communication and computing technologies into an intelligent, all-in-one platform. Driven by advances in the reduction in the size and power consumption of computing technology, this expansion of the smart device market has created a need for new sensors which can be integrated onto compact and robust chip level systems. The success of these devices leverages the scaling of existing sensor technologies to improve the footprint and efficiency of the overall electronics package while maintaining compatibility with current manufacturing processes. This size reduction of current sensor technology often presents immense engineering challenges which stem from the undesirable scaling of the physical phenomena upon which the sensor operates. The scaling of electrically ii controllable magnetic field devices is one such category which demands an alternative approach at small length scales to achieve practical efficiencies. In this work an approach is taken to design small scale electrically controlled magnetic field sensors which sharply deviates from the traditional Oersted field devices typical of macroscale systems. Strain mediated multiferroic composites, which couple the intrinsic magnetic and electric degrees of freedom inside the material through mechanical strains, are explored in the context of antennas and static magnetic field sensors. An analysis of the radiation efficiency of a multiferroic antenna is presented and steps are taken to realize a practical experimental device. Two types of magnetometers are studied which use multiferroic composites to improve the sensitivities and measurement accessibility of such devices. The results of this work clearly demonstrate the significant advantages offered by strain mediated multiferroic materials for use in chip-scale sensor technologies which have significant potential to advance the capabilities of integrated “smart” electronic systems. iii The dissertation of Paul Nordeen is approved. Pei-Yu Chiou Robert N. Candler Christopher S. Lynch Gregory P. Carman, Committee Chair University of California, Los Angeles 2016 iv For my family, Mom, Dad, Anna, Eir, Nick, Aubrey, Catherine, James and Jake. v Table of Contents 1. Chapter 1: Introduction…………………………………………………………………1 2. Chapter 2: Multiferroic Antennas………………………………………………………9 I. Introduction………………………………………………………………......……9 II. Analysis………………………………………………………………….…….…19 III. Design……………………………………………………………………………48 IV. Materials…………………………………………………………………....……66 V. Device Fabrication………………………………………………………….....…84 VI. Experimental Setup……………………………………………………...…...…106 VII. Results………………………………………………………………………..…150 VIII. Conclusion………………………………………………………………..….…158 3. Chapter 3: Multiferroic Magnetometers…………………………………………….161 1. Multiferroic Surface Acoustic Wave Magnetometers………………………166 I. Introduction……………………………………………….…..…...……166 II. 2D Finite Elements Simulation………………….………………...……171 III. Device Fabrication….………………………………………………..…177 IV. Characterization………………………………………………...………181 V. Experimental Setup……………………………………………...…......185 VI. Results…….………………………………………...…………….….…186 VII. Conclusion..…………………………………………………....…….…191 2. Wireless Detection of a Force Frequency Magnetometer…………………..193 I. Introduction………………………………………………………..……193 II. QCM Magnetometers and Wireless Detection….………………...……197 vi III. Device Fabrication….……………………………………………..……201 IV. Experimental Setup………………………………………………..…....205 V. Results…….……………………………………………………….……207 VI. Conclusion..…………………………………………………….………215 4. Chapter 4: Conclusion………………………………………………………………...217 5. References…………………………………………………………...…………………220 vii List of Figures Figure 1.1 - An iron nail wrapped with a current carrying wire aligns surrounding ferromagnetic iron filings to equipotential magnetic field line. ………………………………………………….2 Figure 1.2 - A single turn of copper wire of annular diameter D and wire diameter D/10 which carries a current on I. ……………………………………………………………………………..2 Figure 1.3 – A typical magnetostriction curved showing the characteristic transition points (left). An elliptical particle model demonstrating the intrinsic coupling between strain and magnetization. ……………………………………………………………………………………5 Figure 1.4 – A diagram of a piezoelectric PZT unit cell under no applied electric field (left) and applied electric field (right) illustrating the resulting lattice distortion. ………………………….6 Figure 2.1 – a. An image of a horizontally polarized dipole antenna. b. A schematic view of the currents and fields on a short dipole antenna during operation. ………………………………...10 Figure 2.2 – A schematic diagram of the operation of a multiferroic antenna. ………………...12 Figure 2.3 – The three types of PZT/Terfenol-D plate resonators tested for coupling (top). The coupling coefficients of the three plates as a function of applied magnetic field (bottom). ……14 Figure 2.4 – The x-band power absorption of a FeGaB/PZN-PT heterostructure under various electric field values applied to the PZN-PT layer. ………………………………………………16 Figure 2.5 – A schematic representation of the FMR absorption experiment using SAWs (top). a. An angular color map plot showing absorption of acoustic energy in the nickel film. b. Transmission measured at the output IDT for various upper harmonic modes as a function of applied bias field. ………………………………………………………………………………..18 Figure 2.6 – The radiation efficiencies for an electrically small wire loop antenna (yellow) and a strain driven block of three representative magnetoelastic materials as a function of characteristic length operating at 200 MHz. Length is the loop diameter in the case of the wire loop and represents the side length of the magnetoelastic block. …………………………………………30 Figure 2.7 – A plot of normalized imaginary radiated power from a wire loop antenna as a function of distance from the source (in wavelengths). …………………………………………31 Figure 2.8 – Radiation efficiency as a function of distance from a radiating magnetoelastic cube having 50µm side lengths for three types of magnetoelastic materials. ………………………...32 Figure 2.9 – A comparison of the power transmitted into three magnetoelastic films to a depth of 1μm at a frequency of 200 MHz. Output power is normalized to the power applied in the source medium. …………………………………………………………………………………………39 Figure 2.10 – A finite element simulation of a 200 MHz plane wave impinging on a 10x10x0.5μm nickel rectangular prism. Color hue corresponds to magnetic field norm magnitude measured in A/m. Black lines are equipotential magnetic field lines. …………………………..40 viii Figure 2.11 – Transmission coefficients for a 1μm thick nickel square illuminated by a TE10 wave as a function of square side length. As the side length approaches 20μm the nickel becomes a continuous film. ………………………………………………………………………………..42 Figure 2.12 – The transduction efficiency computed from the total mechanical power shown as a function of depth for three representative magnetoelastic films. Actuation frequency is 200MHz. ……………………………………………………………………………………………………44 Figure 2.13 – A least squares fit of the Langevin function (red) to experimentally measured MOKE data of a 500 nm thick nickel film on lithium niobate (black). ……………………….45 Figure 2.14 – Relative permeability (black) and piezomagnetic coupling coefficient (red) as a function of applied magnetic field for a 500 nm thin film of nickel. ………………………….46 Figure 2.15 – Transduction efficiency (black) for a 500 nm magnetoelastic nickel film excited using a 200 MHz electromagnetic plane wave. Also shown are the effects of constant permeability (red) and constant piezomagnetic coupling coefficient (green) on the output power. ……………………………………………………………………………………………………47 Figure 2.16 - A diagram of the components used to construct a simple two port SAW bandpass filter. ……………………………………………………………………………………………..50 Figure 2.17 – An illustration of the simulation setup used for testing the electrical and mechanical characteristics of a SAW bandpass filter consisting of two IDTs. …………………52 Figure 2.18 – An IDT electrode being actuated on a lithium niobate substrate at 230MHz. Color corresponds to surface displacement in m. Black lines are equipotential electric field lines. …..53 Figure 2.19 – a. The simulated S12 response of a SAW bandpass filter on 1280YX cut lithium niobate for different numbers of finger pairs in the IDT electrodes. b. The S12 response of the bandpass filter as the width of the finger electrodes is changed. ………………………………..56 Figure 2.20 – a. The simulated real impedance of a SAW bandpass filter operating at 300 MHz for IDT finger lengths of 13 and 9000 µm. b. The corresponding imaginary impedance for the
Details
-
File Typepdf
-
Upload Time-
-
Content LanguagesEnglish
-
Upload UserAnonymous/Not logged-in
-
File Pages246 Page
-
File Size-