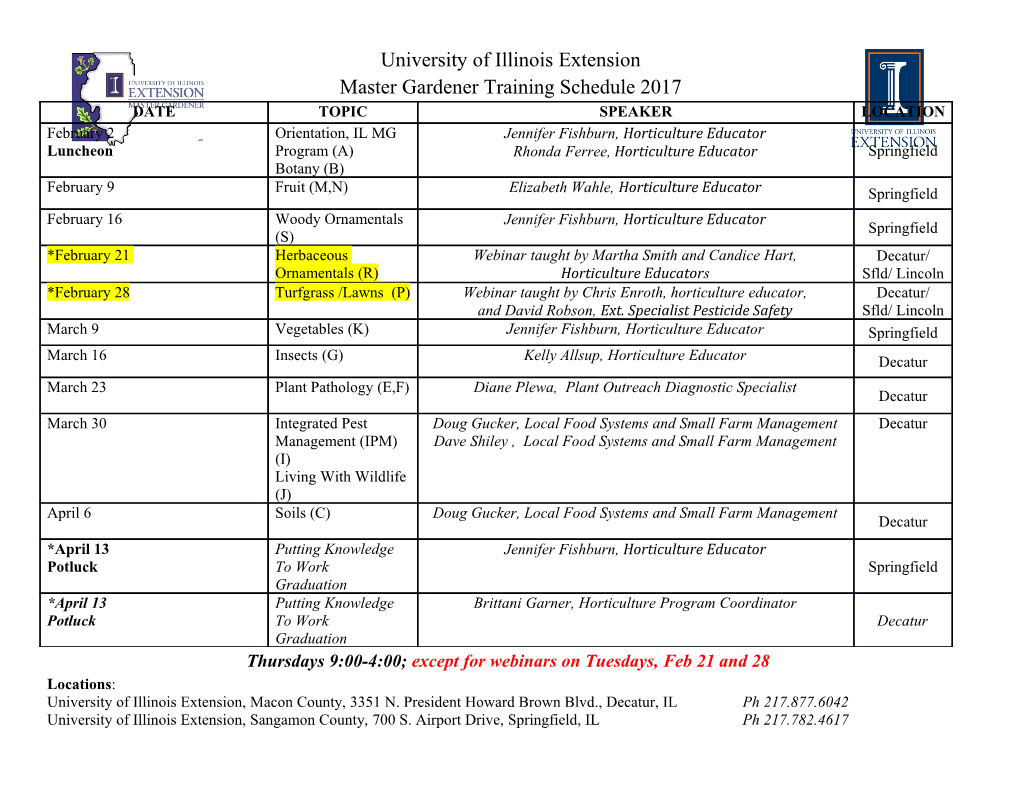
Journal of Basic and Applied Engineering Research Print ISSN: 2350-0077; Online ISSN: 2350-0255; Volume 2, Number 6; April-June, 2015 pp. 452-454 © Krishi Sanskriti Publications http://www.krishisanskriti.org/jbaer.html Design of Catalytic Converter for Stationary Diesel Engine Ajinkya B. Patil1 and Rajaram M. Shinde2 1PG Student, RIT Sakharale, Sangli (M.S.) 2RIT Sakhrale, Sangli (M.S.) E-mail: [email protected], [email protected] Abstract—Air pollution from on road as well as off road vehicles is 2. CATALYTIC CONVERTER DESIGN major problem. The harmful pollutants like CO, HC, , PM are emitted from on road and off road vehicles which causes hazardous In this section, some parameters are discussed to be effect on human health as well as environment. So, it is necessary to minimize these air pollution. For this purpose, different technologies considering for design of catalytic converter. After this, are used like enhancement in engine design, pretreatment on fuel, methodology of design and material selection for catalytic exhaust treatment, etc. So, it is challenging to researchers to control converter has been presented. emissions from stationary diesel engines. The present work comprises 2.1. Shape of Catalytic Converter of design of catalytic converter for stationary diesel engine. In this work, catalytic converter is designed from engine specifications. The shape of catalytic converter should be selected as round There are different parameters to be considered for designing the honeycomb structure because it is easy for manufacturing. By catalytic converter system. Also, materials for catalytic converter are discussed. Finally it is possible that designed catalytic converter can choosing this shape, surface area of substrate increases. Also, reduce emissions significantly. with these shape, minimum time required for assembly and it is easy for maintenance. With the use of round honeycomb 1. INTRODUCTION structure, mass of substrate get reduced and flow area increases. With use of round shape backpressure reduces about Air pollution and global warming from on road as well as off 10 to 15%. Also thermal conductivity goes on increases by road vehicles are major issues nowadays. The utilization of choosing this shape. There are other shapes like oval, vehicles has increased due to population growth, increased rectangular used. But in this shape, pressure drop is more as urbanization, and industrialization. The exhaust emissions compared to round shape. Also wall thickness is more in case from internal combustion engine takes part more than 60 to of the rectangular shape. Therefore surface area is reduced. 70%. Harmful pollutant like CO, HC, , PM are emitted For this reason shape of catalytic converter should be selected from internal combustion engines. These emissions causes as round honeycomb structure [1]. hazardous effect on the human health and environment. Also, these pollutants are responsible for greenhouse effect, acid 2.2. Space velocity rain, etc. Hence, emission regulations are becoming very Space velocity is the ratio of exhaust gas flow rate to the serious every year. There are different devices developed for volume of converter [1]. Space velocity means residential time aftertreatment of exhaust emissions. The most effective of exhaust gases in converter or reactor. In general space aftertreatment device for reducing exhaust emissions are velocity means amount of entering volumetric flow rate of catalytic converters. reactants divided by the reactor volume. If space velocity goes The design of catalytic converter includes methodology, on increasing then converter volume decreases. i.e. material required for components of catalytic converter. In performance of catalytic converter goes on decreasing. So, practice design of catalytic converter is important task than space velocity is assumed in proportion with converter science. The catalytic converter is best solution for emission volume. Space velocity varies from about 20000 to 25000 per reduction of internal combustion engines to fulfill with hour depending upon the duty cycle of engine [1]. emission regulations. The catalytic converter is device which 2.3. Volume of Catalytic Converter converts toxic pollutants into non toxic pollutants. The position of catalytic converter is also important in case of This parameter is also important in designing of catalytic design consideration. So, catalytic converter is installed converter. The volume of catalytic converter is 0.5 to 1 times between engine exhaust manifold and muffler. that of the engine swept volume [1]. Also, volume of catalytic Design of Catalytic Converter for Stationary Diesel Engine 453 converter depends upon engine swept volume and is inversely = 0.00044178 3 proportional to the space velocity. If, volume of catalytic = 441.78 cc converter is lower than half of the engine swept volume then, = 0.44178 L space velocity increases tremendously. Because of this, Step 3: Outer Dimensions of Catalytic Converter reaction between catalyst and exhaust gases does not take Catalytic converter is a cylindrical shell. Therefore, place and emission goes on increasing. Hence, it is kept in the dimensions of catalytic converter are determined from volume range of engine swept volume. above calculated. Volume of Catalytic Converter = × 2 × L 3. METHODOLOGY 4 Assume, D = ¾ L In this section, design steps of catalytic converter have been This proportion of diameter and length used in some gas presented. The catalytic converter system means diesel engine vehicles models such as Mitsubishi 3000 GT, Jaguar oxidation catalyst and selective catalytic reduction technology cars, Acura cars, etc. But this proportion is not fixed. It is used in diesel engine for conversion of HC, CO, , PM. taken as per engine swept volume requirement. The main components of catalytic converter are – Now, 0.00044178 = × (3L/4)2 × L 4 1. Substrate 0.00044178 = × 9/16 × 3 4 2. Washcoat L = 100 mm 3. Catalyst [2] Then, D = ¾ ×100 = 75 mm D = 75 mm This Catalytic Converter system is designed for following engine. Step 4: Substrate Dimensions Tab le 1: Engine Specifications The standard dimensions of substrate are selected from volume of catalytic converter above calculated. The Make and Model Kirloskar, dimensions are selected as 1200/2 cell density from following No. of Cylinders One table 2. Orientation Vertical Cycle 4 Stroke Tab le 2: Substrate Dimensions [1] Ignition System Compression Ignition Parameter Cell Bore X Stroke 87.5 mm X 110 mm Density Displacement Volume 661 cc 400/6.5 600/4 900/2.5 1200/2 Compression Ration 17.5 : 1 Substrate 0.86 0.67 0.67 0.31 Arrangement of valves Overhead volume, l 2 Combustion Chamber Open Chamber (Direct Injection) GSA, m / l 2.74 3.48 4.37 4.98 Rated Power 5.2 kW (7 HP) @1500 rpm OFA, % 75.7 81.4 85.6 83.4 2 Cooling Medium Water cooled Rf, litres/cm 3074 3990 5412 7589 Substrate 339 202 156 83 3.1. Design steps are as follows [5]. mass, g Step 1: Volume Flow Rate of Exhaust Gases The cell density 1200/2 is selected because it gives better volume flow rate = swept volume × Number of intake emission reduction as compared to other cell densities. stroke/hr Emissions reduction are shown in following table 3. Tab le 3: Emission Reduction [1] = × 2 × L × × 60 4 2 1500 = × 0.08752 × 0.110 × × 60 Cell Geometry Relative HC Relative 4 2 = 29.765 3/hr Emissions Emissions = 0.008268 3/sec 400/6.5 100 100 400/4.5 88 94 600/4.3 65-74 74-93 Step 2: Catalytic Converter Volume 900/2.5 52-66 59-75 Assume, space velocity = 67375 1 1200/2 41-57 57 − Space velocity = then, 4. MATERIAL OF CATALYTIC CONVERTER ℎ Converter volume = In this section, material of three components of catalytic 29.765 converter has been discussed. = 67375 Journal of Basic and Applied Engineering Research Print ISSN: 2350-0077; Online ISSN: 2350-0255; Volume 2, Number 6; April-June, 2015 454 Ajinkya B. Patil and Rajaram M. Shinde 4.1. Substrate substrate. Alloy coating is done on the washcoat. It consists of 2 3 [2]. Also, titanium dioxide will be used for washcoat as It is the component of catalytic converter which supports the alternative material [3]. catalysts. The function of substrate is to bring the active catalyst into maximum contact with the exhaust gases. 5. CONCLUSION Requirements of Substrate: [1,2] The effects of parameters for design consideration have • Substrate must be covered with the washcoat studied. Also, materials for catalytic converter have suggested. • Low thermal inertia and efficient heat transfer The catalytic converter for stationary diesel engine was • More surface area per unit volume successfully designed. So, designed catalytic converter can • Ability to withstand high operating temperature reduce emission significantly. • Long durability • High resistance to thermal shocks 6. ACKNOWLEDGEMENT There are different types of substrates used in catalytic I take this opportunity to thank all those who have contributed converter like pellet, ceramic, metallic, etc. In this in successful completion of this research work. I would like to investigation, metallic substrate is used having following express my sincere thanks to Prof. R. M. Shinde and Prof. L. dimensions. M. Jugulkar (Automobile Engg. Dept., RIT) who encouraged me to carry this work their valuable suggestions, critical Tab le 4: Substrate Dimension [1] examination of work during the progress, I acknowledge Cell Density 1200/2 with thanks to faculty, teaching and non-teaching staff of Substrate volume, l 0.31 the department, Central library and Colleagues. GSA, m2/ l 4.98 REFERENCES OFA, % 83.4 R cm2 f, litres/ 7589 [1] B.P.Pundir, “Engine Emissions”, Pollutant formation and Substrate mass, g 83 Advances in Control Technology, Narosa publications (2011). [2] Fred Schäfer and Richard van Basshuysen, “Reduced Emssions Advantages over ceramic substrate: [1,2] and Fuel Consumption in Automobile Engines”, SAE • Higher mechanical strength international (1995). • High thermal conductivity for faster warm-up [3] M.A.Kalam et.
Details
-
File Typepdf
-
Upload Time-
-
Content LanguagesEnglish
-
Upload UserAnonymous/Not logged-in
-
File Pages3 Page
-
File Size-