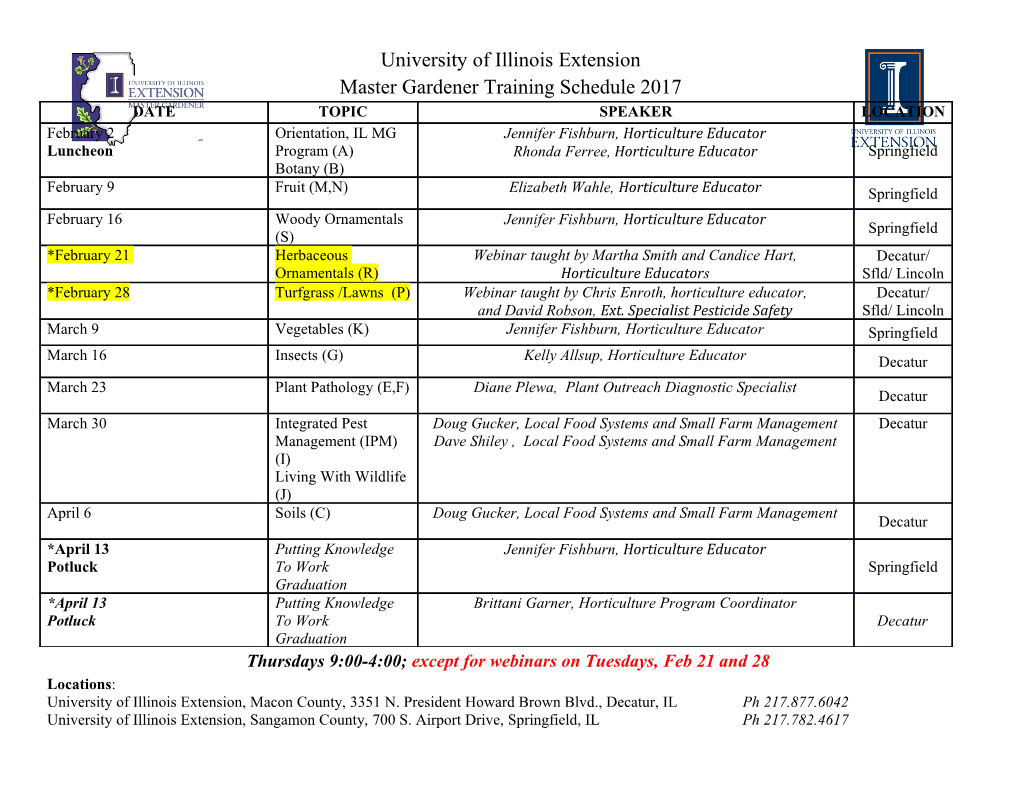
Superconductivity and Cryogenics Vol.12, No.4, (2010), pp.1~7 Progress of Pulse Tube Cryocooler Yoichi Matsubara1,* and Deuk-Yong Koh2 1Former Professor of Nihon University, 763 Kotto Chikura minamiboso Chiba 295-0022, Japan 2KIMM, 171 Jang-dong Yuseong-ku Daejeon 305-343, Korea Received 7 September 2010; accepted 15 October 2010 ``` Abstract-- The pulse tube cooler as an alternative of of future development of the cooling system for each Stirling, G-M or VM cooler to overcome the requirement application fields. from the various application fields is described. The necessity of the object oriented cooler development is explained to realize the cryocooler of more energy-efficient, more reliable, 2. CLASSIFICATION OF PTC more compact and less expensive than what is currently available commercially. 2.1. Critical components of PTC Most characteristic merit of the pulse tube cooler is that it 1. INTRODUCTION has no mechanical moving components at the cold part of the cooling device without the sacrifice of thermodynamic Cryogenic technology, including cryocoolers, is a efficiency. From the view point of thermodynamic aspect, crucial supporting technology for superconductor pulse tube cooler will be divided into five critical applications, without exception. In general, if the existing components. room temperature technology is replaced with the Fig. 1 shows the basic arrangement of each component; superconducting technology, the extra work required for pressure wave generator, regenerator, pulse tube, heat the cooling system becomes a sort of penalty. Therefore the exchanger and the work receiver section. The simplest development of efficient cryocooler becomes essential configuration of the pressure wave generator will be issue. The request from the application fields, however, is represented by a piston control volume with heat exchanger. not only the efficiency but also reliability, low cost, Similarly, the work receiver part will be represented by a compactness and applicability (easy to use). reservoir with an orifice as shown in the doted area The key technical aspects that must be taken into respectively. The regenerator, in typically, is made by a consideration are the different specifications required for stack of fine metallic mesh (normally ~300 mesh) within various applications. Generally, for power applications, the the thin tube to have good heat transfer with the gas, when most important application issues are reliability and the gas passing through in the void volume of the mesh. The redundancy problems; for electronics applications, pulse tube is a simple hollow tube with no heat transfer reliability, cost and, possibly, temperature stability are surface in it. Therefore the pulse tube is act as an adiabatic critical issues. Cryocoolers might be used in various tube. In this example of Fig. 1, the mechanical moving temperature regions in the future, depending on their component applications; at present, operation temperatures of 4.2 K, Work receiver 20 K and 77 K (based on the liquid temperature of Helium, Pressure wave generator Hydrogen and Nitrogen) are standard. Cryocoolers are categorized by the thermodynamic operating cycle, such as; Brayton, Joul-Thomson, Stirling and Gifford-McMahon (G-M) cycle. Former two are based on the circulating gas and the latter two are based on the Regenerator Pulse tube oscillating gas. Pulse tube cooler (PTC) as an alternative of Stirling cooler or G-M cooler, which also uses the oscillating gas, is noted as a cooling system to overcome the request from the wide application fields described Vacuum chamber above. Pulse tube coolers might be a promising solution for Heat exchanger some power and electronics applications. The cooling temperatures obtained from each cryogen described above Fig. 1. Fundamental arrangement of the pulse tube cooler are completely covered by pulse tube coolers. Fundamental divided into five critical components. White arrow thermodynamics of PTC is described to find the direction indicates the work flow direction to generate the cooling effect at the heat exchanger between the regenerator and the * Corresponding author: [email protected] pulse tube. 2 Progress of Pulse Tube Cryocooler component is only the piston located at the room thermo-acoustic or Vuillemier type because it is same as temperature. Input the external energy to the piston, then it the gas compression part of Vuillemier (VM) cycle. If the produces the work flow directed to the regenerator as displacer used in the VM cycle replaced to a gas column, shown by the white arrow on the figure. then it becomes thermo-acoustic engine. This work flows through the pulse tube and dissipated at One of the pressure wave generators is connected to the the orifice within the work receiver section. According to regenerator side and one of the work receivers is connected the pressure oscillation, the gas temperature at the heat to the pulse tube side to complete the pulse tube cooler. exchanger is lower when the gas flows from the pulse tube Three additional components shown by arrows below the to the regenerator than that of the reversed flow. This gives vacuum chamber are act as the phase shift mechanism. the cooling effect at the heat exchanger and the minimum The efficiency of the pulse tube cooler keeps improving cooling temperature is given when this cooling effect by changing the work receiver since the first pulse tube balanced with the heat load. cooler was reported by W. E. Gifford and R. C. Longsworth Traditional expression of the cooling effect is due to the in 1964 [1]. They choose the work receiver of simple heat gas expansion occurred near the expansion piston head. In exchanger. This type is now called as Basic pulse tube the case of the pulse tube, there is no solid expansion cooler. Second important improvement has been done by E. piston; however, the part of the gas column, which is I. Mikulin in 1984 [2]. Instead of the simple heat exchanger, oscillating within the pulse tube will act as a gas piston. an orifice and the reservoir is added to receive the work Therefore the heat exchanger temperature decreases and more actively. This type is called as Orifice pulse tube has some cooling capacity at the appropriate cooling cooler. temperature without any moving parts at the low A bypass valve between the regenerator warm end and temperature region inside of the vacuum chamber. This the pulse tube warm end, as shown in middle part of Fig. 2, unique structure leads the design flexibility of the cooling was added to the orifice pulse tube by S. Zhu in 1990 and is system and it expands the further application fields. called as Double inlet pulse tube [3]. Cooling performance Following section introduces the various pressure wave of this type improved further than Orifice type and is generators and the work receivers to understand the classified as 3rd generation corresponding to 2nd mechanism of keeping high efficiency of the pulse tube generation of Orifice type and 1st generation of Basic type. cooler. All other work receivers shown in Fig. 2 are proposed since 1988 to improve the performance of the pulse tube cooler 2.2. Historical background and are corresponding to 3rd generation [4-6]. The warm Three different types of pressure wave generator are displacer can be used instead of warm expander. If this given in Fig. 2. Type (a) is called as valve less compressor solid displacer is replaced to simple gas column then it or Stirling type because it is same as the gas compression becomes thermo-acoustic cooler. Two valves in the Active part used in Stirling cycle. Type (b) consists of circulating buffer type connected to each buffer must be well gas compressor with a heat exchanger (generally called as controlled with main valves of GM type pressure wave after cooler), and a set of switching valve to generate the generator. oscillating flow. This type is called as valved compressor or G-M type because it is same as the gas compression part used in Gifford-McMahon cycle. Type (c) is called as (a) thermo Vacuum chamber Heat exchanger (a) Stirling type After cooler (b) Switching Orifice & reservoir Valve, Ph Regenerator Pulse tube compressor Switching Valve, Pl Bypass valve Warm expander (b) G-M type Warm displacer regenerator (c) Active buffer Ph side displacer Pl side Pulse tube volume Inertance tube (c) Vuillemier type Four valve method Fig. 3. Equivalent PV diagrams within the pulse tube. Fig. 2. Schematic comparison of the pressure wave (a) Basic pulse tube, (b) Orifice pulse tube, (c) Double inlet generators (left side of dashed line) and the work receivers or any other 3rd generation pulse tube. Y-axis is the (right side of dashed line) for a common regenerator and pressure, X-axis is the pulse tube volume, left end is the low the pulse tube. Additional phase sifters are shown by temperature side and the right end is the room temperature arrows below the vacuum chamber. side. Yoichi Matsubara and Deuk-Yong Koh 3 generator. If these two buffers are eliminated and reservoir, so it makes compact but the problem of the connected to the main compressor high and low pressure circulating flow is still remains. Active buffer method and side respectively, then it becomes four-valve method. The the Inertance tube method have no such closed loop as a reason of the necessity of these developments will be source of instability, however, the former requires extra explained by PV diagram as shown in Fig. 3. buffer volume and the latter is not applicable to GM type or In the case of Basic pulse tube, warm end of the tube low frequency pulse tube cooler. Improvement by use of (right side) is closed by a heat exchanger. Therefore the Inertance tube is not significant for the small scale coolers.
Details
-
File Typepdf
-
Upload Time-
-
Content LanguagesEnglish
-
Upload UserAnonymous/Not logged-in
-
File Pages7 Page
-
File Size-