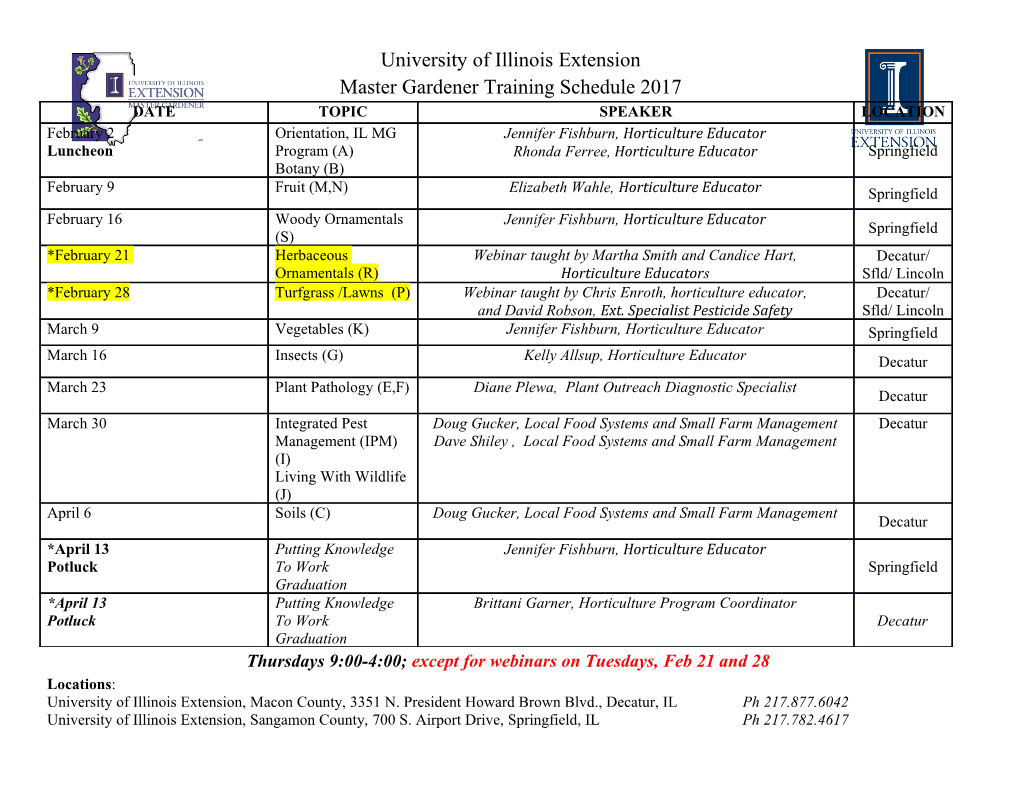
Hindawi Publishing Corporation Mathematical Problems in Engineering Volume 2013, Article ID 379068, 5 pages http://dx.doi.org/10.1155/2013/379068 Research Article Drop Impact Analysis of Cushioning System with an Elastic Critical Component of Cantilever Beam Type De Gao,1 Fu-de Lu,2 and Si-jia Chen1 1 Ningbo Institute of Technology, Zhejiang University, Ningbo 315100, China 2 School of Aeronautics and Astronautics, Zhejiang University, Hangzhou 310027, China Correspondence should be addressed to Fu-de Lu; [email protected] Received 25 March 2013; Revised 16 April 2013; Accepted 17 April 2013 Academic Editor: Jun Wang Copyright © 2013 De Gao et al. This is an open access article distributed under the Creative Commons Attribution License, which permits unrestricted use, distribution, and reproduction in any medium, provided the original work is properly cited. In some electronic products and sculpture crafts, there are possibly vulnerable elements that can be idealized as cantilever beam type, failure of which will certainly lead the whole product to lose function. Based on the critical component of cantilever beam type, a nonlinear coupling dynamics model between the critical component and the item was established. The computing procedure of the model was designed using finite difference scheme. A numerical example shows that the acceleration changes notably withthe length of the critical component, and the cantilevered end of the critical component is liable to be damaged, because the dynamic stress there is the largest. In this case, the maximum acceleration just cannot serve as the damaged criterion of the packaged goods, only with the maximum stress value. In order to avoid making a mistake, it is necessary to consider the critical component as an elastic element. The maximum stress of the cantilever beam surpasses the proportional limit of elastic components or is notan effective structural strength to determine whether the product loses its functions. 1. Introduction vulnerable element of some products for which this simplified method is not suitable. Aiming at crafts, Xi and Peng [12]ana- The fragility of the products must be determined by a fragility lyzed the response of the products with a vulnerable element assessmentprocedurebeforecushioningisprovided.The that was idealized as a simple supported beam, and thought maximum acceleration versus static stress is mostly used in that the simple mass-spring system was not suited for evaluat- cushionpackaging,becausethevalueoftheaccelerationisthe ing the structural strength. The cantilever beam, simply sup- criterion to assess whether the items are destroyed [1]ornot. ported beam, and bar element are also available in the micro- Newton first introduced fragility damage boundary curves andportableelectronicproducts[13–15]. Subir [16]certifi- by linking the input environment and the characteristics cated the criterion of the maximum stress that is responsible of critical component of packaged item [2], assuming the for structural strength, and the analytical modeling demon- product as a spring-mass system. Newton’s model is only strated the application of the measured acceleration as a suitable for brittle materials such as glass and hard plastics. criterion of the dynamic strength can be misleading if applied Furthermore, inspection of many products after failure on to elements of different dimensions, weight, and materials. the shock motion revealed plastic deformation [3, 4]like Gao and Lu [17] studied the responses of the electronic prod- soft plastics, aluminum, and soft steels failed in a ductile ucts with bar type critical component, which is simplified as mode. Burgess developed a rigid-plastic model to account uniform and elastic parts. Abovementioned publications on for progressive failure and then obtained the elastic-plastic crafts and portable electronic products have shown that it is damage boundary theory. Many papers [5–11]developed the maximum stress, not the maximum acceleration, which damage boundary curves based on previous research results. is responsible for the dynamic strength of a structure. The studies cited above are all for mass-spring system; This paper presents the dynamics model of expanded some researchers have studied the impact response of elastic polyethylene foam cushioning system for products with 2 Mathematical Problems in Engineering 2 2(, ) 1 2 (1) (a) Coordinate system of the critical component + + Figure1:Packagingsystemwithcantileverbeamtypecritical component. (b) Force diagram of infinitesimal cantilever beam type vulnerable element, which is suitable section for some portable electronic products or crafts with cantilever Figure 2: Coordinate system of the critical component and force beam critical components, under drop impact loadings dur- diagram of infinitesimal section. ing transportation to introduce its application in cushioning packaging design. where is the density of the beam and 0 is the section area 2. Coupling Packaging Dynamic Model of the beam. Based on the moment balance of the differential element, The cantilever beam type structure mostly exists in electronic the following equation can be obtained: products, such as an electrical lead or intersect, and some crafts, such as the tail of sculpture animals, which is usually ( + ) − − (+ )=0. damaged functionally or physically due to the large-scale (3) deformation of the critical component. Figure 1 shows a packaging system with the tangential type cushion pad, in Equation (3) can be further simplified as follows4 ( ): which is the mass of the main part; 1 is the displacement ( ) of the packaging item and 1 is the restoring force; is the dropping height of the packaging system. = . (4) A local coordinate system of the critical component was built, with origin o at the cantilever end, taking the axial direction of the beam as direction and the deflection as the Then insert (4)into(2) and get the following expression: 2,asshowninFigure 2(a). Take the differential element 2 2 to analyze the movement of the critical component, as shown 2 =0 . (5) in Figure 2(b),where and are elastic modulus and section 2 2 moments of inertia, respectively; and are, respectively, shear force and bending moment of the section. The relationship between the bending moment and the By Newton’s second law, (1)isobtainedbasedon deflection 2 is expressed as Figure 2(b) as follows: 2 2 2 =− . (6) 2 2 =−+(+ ) . (1) 0 2 Combining (5)and(6), the movement equation of the critical Simplify the above as component is given as 2 2 4 2 = , 2 2 0 2 (2) + =0. (7) 4 0 2 Mathematical Problems in Engineering 3 The vibration equation of the main part is given by as follows: 3 (+Δ) − (−Δ) ̈ +(, ̇ )+ 2 =0, ̇ () = 1 1 ; 1 1 1 3 (8) 1 2Δ =0 (12a) (+Δ) + (−Δ) −2 () ̈ () = 1 1 1 ; 1 Δ2 where (1, 1̇ ) is the constitution relation of expanded polyethylene between the outer package and the product. (,) (, )+ Δ − (, )− Δ 2 = 2 2 ; Most of the cushioning materials for electronic products is 2Δ EPE, and its relation [18]canbefittedbythetangential 2 (,) (, )+ Δ + (, )− Δ −2 (,) function: 2 = 2 2 2 ; 2 Δ2 (12b) 1̇ 1 ()=[1 +2 tan (3 )] , (9) ℎ ℎ 2 (+Δ,) + (−Δ,) −2 (,) 2 = 2 2 2 ; 2 Δ2 where and ℎ are, respectively, area and thickness of the 3 2 cushion pad; 1, 2 and 3 are the parameters determined by =((+2Δ,) +2 (−Δ,) 3 2 2 the experimental data. With initial conditions and boundary conditions being 3 −22 (+Δ,) −2 (−2Δ,))/2Δ ; considered, the coupling dynamic equation between the critical component and the main party is given as follows: 4 2 =(6(,) −4[(+Δ,) + (−Δ,)] 4 2 2 2 3 4 1̇ 1 2 +[ (+2Δ,) + (−2Δ,)]) /Δ . ̈ +[ + ( )] + =0, 2 2 1 1 ℎ 2 tan 3 ℎ 3 =0 (12c) (10) 4 2 2 2 So the movements 1 and 2(, ) can be obtained by +0 =0. 4 2 combing (10)and(11), shown as = (,) − () . The initial conditions and boundary conditions are 2 1 (13) The maximum stress is determined as 0 = , 0 =0; 1 ( ) 2 ( ) = , (14) (,) ̇ (0) = 2 = √2; 1 =0 where istheradiusofthesectionofthecriticalcompo- (,) (11) nent; is the bending moment and calculated by = (0, ) =; 2 =0; 2 2 2 1 −( 2/ ) =0 . 2 (,) 3 (,) 2 = 2 =0. 3.1. Numerical Example. In the present study, an example was 2 3 = cited to illustrate the use of the dynamic model of the cushion packaging system with critical component of cantilever beam type.Thereisanelectronicdevicewiththemass=3kg, The analytic solutions of (10)arenotavailableduetothe andtheparametersofthecriticalcomponentareasfollows: 3 nonlinear behavior of cushion material used in this paper; density = 0.5 g/cm ,elasticmodulus = 100 MPa, therefore, only numerical solutions were obtained by different proportional limit = 3.3 MPa, length = 0.03 m, and schemes. 2 cross-sectional area 0 =5mm . The parameters of the It is assumed that the mass of the critical component cushion material of expanded polyethylene between the outer ismuchsmallerthantheitemsinportableproducts,so packaging box and the product are 1 = 280 Pa⋅s, 2 = the coupling between critical component and item can be 0.0894 = 1.91 = 0.01 2 neglected. MPa, 3 ,area m ,andthickness ℎ = 0.035 m. The packaging system drops from the height = 0.2 m. It should be checked whether the cushion size 3. Algorithm Design of the Model satisfies the demand of engineering. Substituting (12a), (12b), and (12c)into(10)and(11), A different method was used to solve the coupling model the deformation, acceleration, and stress distribution are shown in (10). The different schemes are introduced obtained, as shown in Figures 3–5. 4 Mathematical Problems in Engineering 60 0.02 50 0.015 40 30 (m) 0.01 20 2 10 0.005 0 0.03 0 0.025 0.03 0.02 0.02 0.015 0.02 0.025 (m) 0.01 0.01 0.02 0.005 0.015 0 0 (s) (m) 0.01 0.01 0.005 (s) 0 0 (a) The absolute acceleration of critical component (a) The absolute displacement of the critical component 40 ×10−3 6 30 5 20 4 3 10 (m) 2 0 1 0.03 0.025 0 0.02 0.03 0.015 (m) 0.01 0.01 0.005 (s) 0.02 0 0 0.025 (m) 0.02 (b) The relative acceleration of critical component 0.01 0.015 0.01 0.005 Figure 4: The absolute acceleration and relative acceleration of 0 0 (s) critical component.
Details
-
File Typepdf
-
Upload Time-
-
Content LanguagesEnglish
-
Upload UserAnonymous/Not logged-in
-
File Pages6 Page
-
File Size-