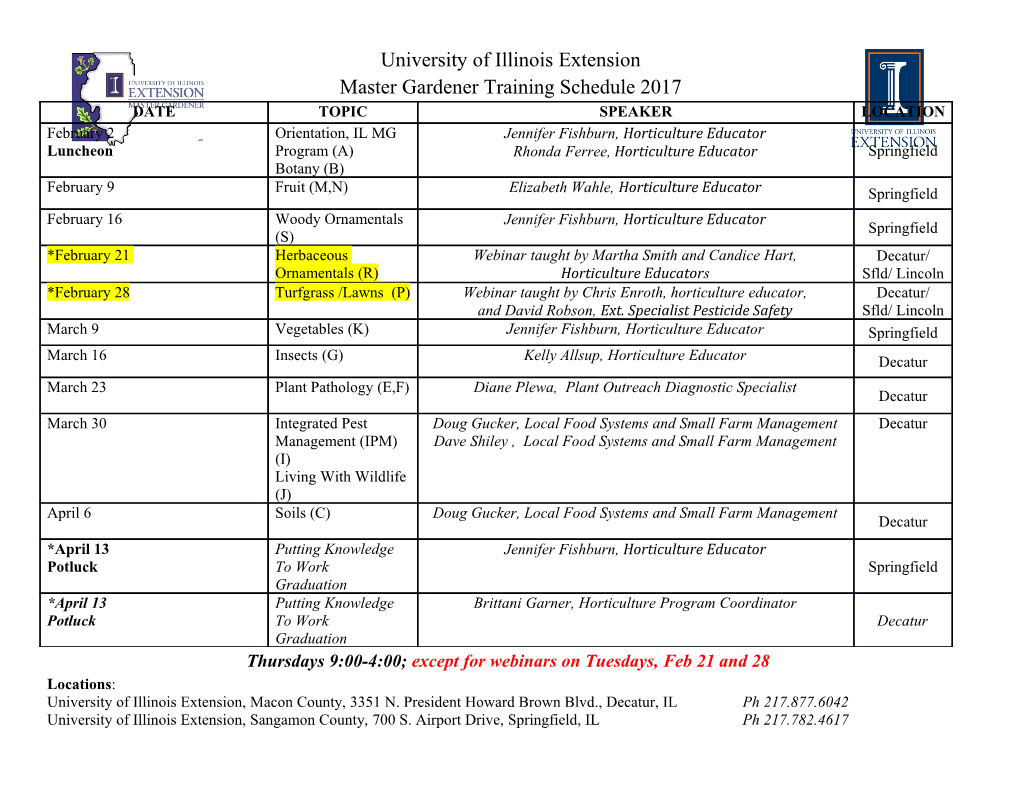
(19) TZZ_¥ _T (11) EP 1 853 427 B1 (12) EUROPEAN PATENT SPECIFICATION (45) Date of publication and mention (51) Int Cl.: of the grant of the patent: B41M 5/00 (2006.01) B41J 3/407 (2006.01) 09.04.2014 Bulletin 2014/15 B41J 11/00 (2006.01) (21) Application number: 05813087.3 (86) International application number: PCT/US2005/038461 (22) Date of filing: 26.10.2005 (87) International publication number: WO 2006/073538 (13.07.2006 Gazette 2006/28) (54) PRINTING PLASTIC CONTAINERS WITH DIGITAL IMAGES DRUCKKUNSTSTOFFBEHÄLTER MIT DIGITALEN BILDERN IMPRESSION DE CONTENANTS PLASTIQUES AVEC DES IMAGES NUMERIQUES (84) Designated Contracting States: (72) Inventor: UPTERGROVE, Ronald, L. AT BE BG CH CY CZ DE DK EE ES FI FR GB GR Northville, MI 48168 (US) HU IE IS IT LI LT LU LV MC NL PL PT RO SE SI SK TR (74) Representative: Weiss, Peter Designated Extension States: Dr. Weiss & Arat AL BA HR MK YU Zeppelinstrasse 4 78234 Engen (DE) (30) Priority: 30.12.2004 US 640605 P 02.09.2005 US 219411 (56) References cited: EP-A2- 0 209 896 WO-A1-99/08935 (43) Date of publication of application: US-A- 3 490 363 US-A- 6 135 654 14.11.2007 Bulletin 2007/46 US-A1- 2002 097 280 US-B1- 6 769 357 US-B2- 6 513 435 (60) Divisional application: 13169055.4 / 2 657 040 Remarks: Thefile contains technical information submitted after (73) Proprietor: Plastipak Packaging Inc. the application was filed and not included in this Plymouth, MI 48170 (US) specification Note: Within nine months of the publication of the mention of the grant of the European patent in the European Patent Bulletin, any person may give notice to the European Patent Office of opposition to that patent, in accordance with the Implementing Regulations. Notice of opposition shall not be deemed to have been filed until the opposition fee has been paid. (Art. 99(1) European Patent Convention). EP 1 853 427 B1 Printed by Jouve, 75001 PARIS (FR) 1 EP 1 853 427 B1 2 Description rality of independently movable print heads is provided at each printing location, wherein said print heads are BACKGROUND OF THE INVENTION separately movable perpendicular to the direction of con- tainer flow, and providing a sensor which determines the [0001] The present invention relates to a method of 5 location of the container surface to be printed and pro- printing digital images onto curved plastic containers. vides electronic feedback to an articulation device which [0002] Conventional techniques for printing onto movesthe printheads independentof each other tomain- curved plastic containers are subject to significant draw- tain a constant distance between the container surface backs. For example, it is difficult to obtain proper regis- to be printed and the print heads. First a first digital image tration between colors, and changing images, designs or 10 is printed on a first printing area on said curved surface wording is expensive and time consuming. of each container at said first printing location; and sec- [0003] Inkjet printing with multiple nozzles is useful for ond a second digital image is printed on a second printing flat surfaces. However, it is difficult to satisfactorily use area on said curved surface of each container at said multiple nozzles on curved surfaces. second printing location. The first digital image is a mul- [0004] It would be highly desirable to print a digitally 15 ticolour image printed at the first printing location in one generated image directly onto a plastic container, partic- pass, and the second digital image is a multicolour image ularly a curved plastic container, wherein the printing can printed at the second printing location in one pass be done at a reasonable speed and at a reasonable cost. [0008] The steps of digitally printing the digital image [0005] The WO99/08935 A1 discloses a method for directly onto the plastic container prints the digital images printing on plastic bottles during a process for producing 20 directly onto a preformed container, for example onto an a packaging system comprising a first step consisting in injection molded or blow molded container, such as pol- applying a first substance onto a selected surface area yethylene terephthalate (PET) or high density polyethyl- of the packaging system by use of first application means, ene (HDPE). The digital printing operation may print the the selected surface area and the hollow body being both digital image directly onto the plastic container as by jet- in motion relative to the first application means and the 25 tingink through an inkjet print headand onto the container selected surface area being solely in contact with the first surface. The ink may be a UV-reactive ink, in which case substance during the first step. The process also com- after printing the ink may be cured by exposure to UV prises a second step which consists in applying a second light. One may also, for example, treat the container sur- substance onto the selected surface area by use of the face to be printed prior to the printing operation, as by second application of means after completion of the first 30 flame treatment, corona treatment or plasma jet treat- step, the selected surface area and the hollow body being ment. both in motion relative to the second application means [0009] Further features of the present invention will be and the selected surface area being solely in contact with discussed hereinbelow. the second substance during the second step, the proc- ess taking place at a continuous line speed. 35 BRIEF DESCRIPTION OF THE DRAWINGS SUMMARY OF THE INVENTION [0010] The present invention will be more readily un- derstandable from a consideration of the following illus- [0006] The present invention provides for printing dig- trative drawings, wherein: ital images or indicia directly onto a plastic container, 40 particularly a curved, plastic container, and accomplish- Figure 1 is a top view of the container conveyer with ing this in a continuous operation at a reasonable speed containers; and at a reasonable cost. Full color digital graphic images Figure 2 is a side view of one embodiment of the or indicia may be directly printed onto containers at mul- container flow and treatment; tiple areas thereon. 45 Figure 3 is a side view of an alternate embodiment [0007] In accordance with the present invention a se- of the container flow and treatment; ries of plastic containers are firmly held and moved to Figure 4 is a side view of the container clamp as- and from a first digital printing location and a first digital sembly; and image is printed thereon at the first printing location on Figure 5 is an enlarged side view of an alternate em- a first printing area on the containers, with the containers 50 bodiment of the container flow and treatment. held at the top thereof and at a second position spaced from the top thereof, preferably at the base. Desirably, DETAILED DESCRIPTION OF PREFERRED EMBOD- the containers are moved from the first digital printing IMENTS location to a second digital printing location and a second digital image printed thereon on a second printing area 55 [0011] As can be seen from Figures 1 - 3, a conveyer on the containers spaced from the first printing area, with assembly 10 is provided to move the containers 11 the containers held at the top thereof and at a second through the treatment procedure in the direction of flow area spaced from the top, preferably at the base. A plu- 12. The containers 11 enter the conveyer assembly from 2 3 EP 1 853 427 B1 4 infeed conveyer 14 at container entry 16 and are secured face 38, desirably an area opposed to the first container in container clamp assembly 18. The clamp assembly surface, as 180° therefrom. secures the containers 11 at two spaced areas, as shown [0018] After rotation the containers 11 with container in Figures 1 and 4, by container base holder 20 and con- first surface 38 having printing thereon are moved tainer top holder 22. It is preferred to hold the container 5 through a second pre-treatment area A-2 where the sur- at the top and bottom, although one could employ a top face energy of the container on the container second holder plus a second holder spaced therefrom, as on the surface 44 is raised as at the first pre-treatment area A- sidewall. This prevents the containers from moving in 1. The containers will then pass the second printing site any direction except for the direction of container flow 46, area B2, wherein the second printing will be per- 12. The base holder 20 and top holder 22 are synchro- 10 formed on the second surface 44 of the containers. nized to maintain the same velocity and relationship to [0019] Similar to first printing site 30, printing at the each other at all times. Naturally, a commercial operation second printing site may be a direct drop on demand may have more than one conveyer assembly line. inkjet head as shown in Figure 3 or an indirect drop on [0012] As can be seen, particularly in Figures 2 and 3, demand inkjet pad 40 as shown in Figure 2. Also, at the the containers 11 are curved, as for example, round or 15 second printing site 46 U.V. ink will be applied directly to oval, and have a container radius or curved portion 24. the second surface 44 of the containers in one pass, as The container track 26 also contains a radius of the multicolor graphics of high quality, as desired.
Details
-
File Typepdf
-
Upload Time-
-
Content LanguagesEnglish
-
Upload UserAnonymous/Not logged-in
-
File Pages10 Page
-
File Size-