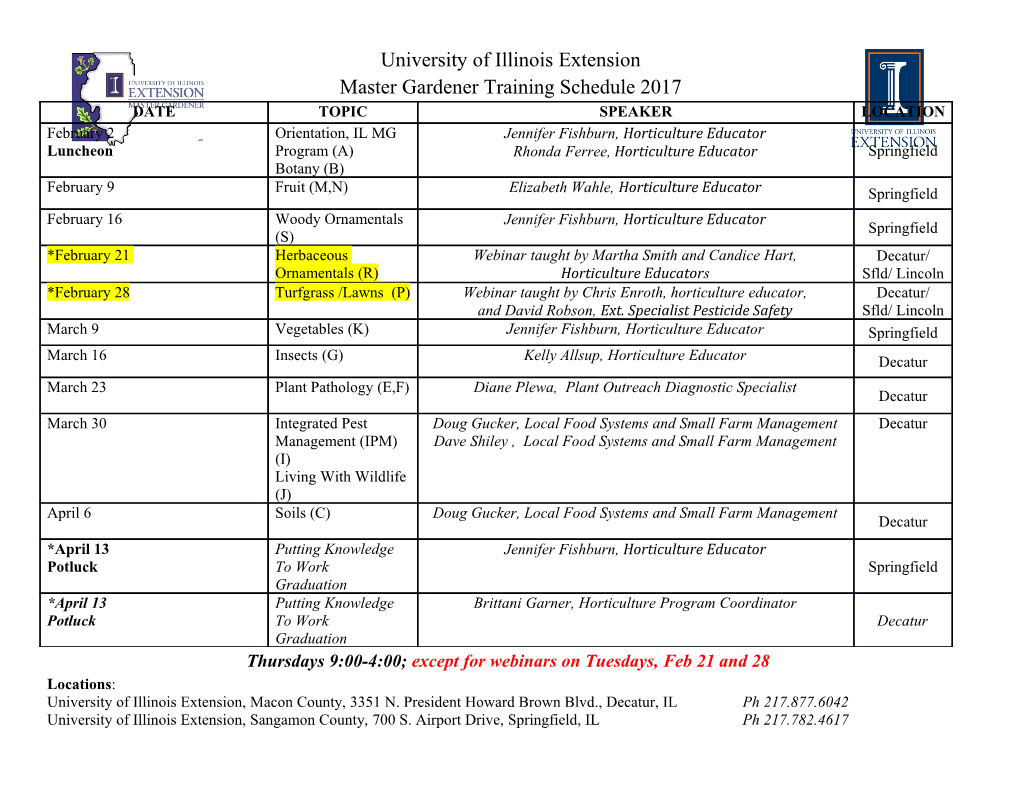
A Service of Leibniz-Informationszentrum econstor Wirtschaft Leibniz Information Centre Make Your Publications Visible. zbw for Economics Toma, Eiji Article Optimization of rotor shaft shrink fit method for motor using "Robust design" Journal of Industrial Engineering International Provided in Cooperation with: Islamic Azad University (IAU), Tehran Suggested Citation: Toma, Eiji (2018) : Optimization of rotor shaft shrink fit method for motor using "Robust design", Journal of Industrial Engineering International, ISSN 2251-712X, Springer, Heidelberg, Vol. 14, Iss. 4, pp. 705-717, http://dx.doi.org/10.1007/s40092-018-0255-9 This Version is available at: http://hdl.handle.net/10419/195635 Standard-Nutzungsbedingungen: Terms of use: Die Dokumente auf EconStor dürfen zu eigenen wissenschaftlichen Documents in EconStor may be saved and copied for your Zwecken und zum Privatgebrauch gespeichert und kopiert werden. personal and scholarly purposes. Sie dürfen die Dokumente nicht für öffentliche oder kommerzielle You are not to copy documents for public or commercial Zwecke vervielfältigen, öffentlich ausstellen, öffentlich zugänglich purposes, to exhibit the documents publicly, to make them machen, vertreiben oder anderweitig nutzen. publicly available on the internet, or to distribute or otherwise use the documents in public. Sofern die Verfasser die Dokumente unter Open-Content-Lizenzen (insbesondere CC-Lizenzen) zur Verfügung gestellt haben sollten, If the documents have been made available under an Open gelten abweichend von diesen Nutzungsbedingungen die in der dort Content Licence (especially Creative Commons Licences), you genannten Lizenz gewährten Nutzungsrechte. may exercise further usage rights as specified in the indicated licence. https://creativecommons.org/licenses/by/4.0/ www.econstor.eu Journal of Industrial Engineering International (2018) 14:705–717 https://doi.org/10.1007/s40092-018-0255-9 (0123456789().,-volV)(0123456789().,-volV) ORIGINAL RESEARCH Optimization of rotor shaft shrink fit method for motor using ‘‘Robust design’’ Eiji Toma1 Received: 5 August 2017 / Accepted: 10 January 2018 / Published online: 24 January 2018 Ó The Author(s) 2018. This article is an open access publication Abstract This research is collaborative investigation with the general-purpose motor manufacturer. To review construction method in production process, we applied the parameter design method of quality engineering and tried to approach the opti- mization of construction method. Conventionally, press-fitting method has been adopted in process of fitting rotor core and shaft which is main component of motor, but quality defects such as core shaft deflection occurred at the time of press fitting. In this research, as a result of optimization design of ‘‘shrink fitting method by high-frequency induction heating’’ devised as a new construction method, its construction method was feasible, and it was possible to extract the optimum processing condition. Keywords Robust design Á Quality engineering Á Shrink fitting Á High-frequency induction heating Introduction advance, to speed up the development of new products and strengthen the constitution of production technology In recent years, there are frequent cases of recall problems capabilities, it is desired to advance technology develop- due to quality problems of consumer electronics products ment with high versatility and high reproducibility. and automobiles in the market and betrayal of consumer For that purpose, it is important for engineers to acquire confidence. The way of manufacturing is also the problem the idea of quality engineering and how to proceed and solving type in most cases, and the recurrence prevention- fulfill the role and responsibility of engineers. Therefore, type development occupies mainstream in actuality. ‘‘Robust design’’ is utilized in technology development and Especially the recall problem of automobiles, such as the product design that account for most of design responsi- complicated structure of the products themselves, the fact bility (Koshimizu and Suzuki 2007; Hasebe 2009). that consumers’ eyes became more severe and that it was impossible to break down all the problems in the design process in shortening the development period, it shows the Research purpose limit of conventional quality control in the market envi- ronment. The reason why the recall cannot be prevented in This research is a collaborative with a motor manufacturer, terms of quality control is because the factors of the recall and we tried approach to optimization of construction problem are put in the design and development stage method by applying Quality engineering for the purpose of (Taguchi 1992). reviewing construction method in production process. Therefore, it can be said that it is difficult to reduce this Figure 1 shows the rotor core and the shaft which are the problem unless innovating the way of design and thinking main components of the motor used in this study (Yano into ‘‘prevention’’ concept. To prevent problems in 2004). In the process of joining the rotor core and the shaft, the press-fitting method has been adopted conventionally, but & Eiji Toma [email protected] as shown in Fig. 2, the quality defect of ‘‘rotor runout’’ of the rotor shaft occurring at the time of press fitting has 1 National Institute of Technology, Tsuruoka College, occurred. Simulation analysis reveals that the factor is Tsuruoka, Japan 123 706 Journal of Industrial Engineering International (2018) 14:705–717 Fig. 1 Rotor core and shaft 2 2 d2 À d1 p ¼ 2 Á E Á D; 2d1d1 where E is the Young’s modulus ðÞ¼ 201½GPa and D is the interference. • Area of junction (A) A ¼ pd1L; where L is the insertion length. • Transmission torque (T) T ¼ lpAd1=2; where l is the coefficient of friction (= 0.15). Materials Fig. 2 Inferior quality model • Rotor core: aluminum alloy and electromagnetic steel. caused by an unbalanced load at the time of press fitting the • Shaft: carbon steel for machine construction. shaft (Mori 2005; Taguchi 1992). Figure 3 shows the calculation model of the strength of the required interference at the time of press fitting. Specification Formula • Required rotation transmission torque: T = 70 [N m]. • Drawing load: F = 5000 [N]. • Internal pressure between cylinder and shaft after • Core inner diameter: d1 = [ 12 [mm]. joining (p) • Core outer diameter: d2 = [ 47.6 [mm]. Fig. 3 Press-fitting model L (Insertion length) Rotor core Shaft Press fitting 123 Journal of Industrial Engineering International (2018) 14:705–717 707 • Insertion length: L = 40 [mm]. Experimental method Calculation result Tables 1 and 2 show various factors and level tables. ‘‘Control factor’’ assigns press-fitting conditions to each level, and ‘‘Noise factor’’ is accuracy of core inner diam- • Area of junction: A ¼ pd L ¼ 1:51 Â 103½mm2 . 1 eter. Based on these level tables, experiments were con- Internal pressure between cylinder and shaft after ducted based on ‘‘L18 orthogonal array’’ which is a joining: p ¼ 51:5½N=mm2 . statistical tool for constructing an experiment plan. • Interference: D ¼ 64:5½lm . • Required heating temperature: DT. Experimental result • D ¼ d1 Á a Á DT ! DT ¼ D=ðÞ¼a Á d1 444½C Figure 6 shows the SN ratio calculated from experimental ÀÁresults as a factorial effect diagram. • a: Coefficient of linear expansion ¼ 12:1 Â 10À6½=C : A diagram showing the effect of combinations of factors As a result of the previous research, it was possible to on characteristic values is called a factorial effect diagram optimize the press-fitting method by setting the ideal (response graph). The vertical axis of the graph represents function (Fig. 4) by applying the quality engineering, and the SN ratio, and the horizontal axis represents the level of extract the processing condition to reduce the occurrence of the factor. core runout of the rotor shaft (Yano 2002; Koshimizu and Suzuki 2007). Reliability of experiment A summary of research on the optimization of the press- fitting method applying the quality engineering in the Table 3 shows the evaluation results on reliability of the previous research is described below. experiment in the response graph. Based on the benchmark condition and the estimation result of the SN ratio of the Experimental system condition considered to be optimum, it was judged that the experimental result is reliable. This means that the selected The outline of the experimental apparatus in the previous optimum condition is an appropriate level out of several research is shown in Fig. 5. Set the shaft and the core in the combinations. upper and lower jigs, and semi-automatic press fitting with However, it turned out that it is necessary to change the hydraulic pneumatic actuator. The press-fitting process processing conditions of the press-fitting method if the conditions (each parameter) were set, and the measurement target rotor shaft diameter changes according to the stan- results of the press-fit load and deflection, which are dard. Although it was able to suppress core runout, in fact, characteristic values, were analyzed and evaluated. due to the lack of process capability, 100% non-defective rate could not be achieved, and the current situation is that it has not led to abolishment of all inspections in process. It can be concluded that this is a factor that did not lead to an improvement in robustness, because the characteristic evaluation method in quality engineering in the previous research is a result based on ‘‘static characteristics’’. There are two types of quality characteristic evaluation in quality engineering, ‘‘static characteristic’’ and ‘‘dy- namic characteristic’’. Static characteristic refers to a characteristic that examines the output without changing the input. The target value is a constant quality character- istic, and ‘‘the nominal-is-best properties’’ is the main characteristic evaluation. However, even in the parameter design for the desired characteristic, the target result may not be obtained in some cases. One of the reasons is that the factor allocated to the orthogonal table may not be well separated into the factor for maximizing the SN ratio and the factor for adjusting the average value.
Details
-
File Typepdf
-
Upload Time-
-
Content LanguagesEnglish
-
Upload UserAnonymous/Not logged-in
-
File Pages14 Page
-
File Size-