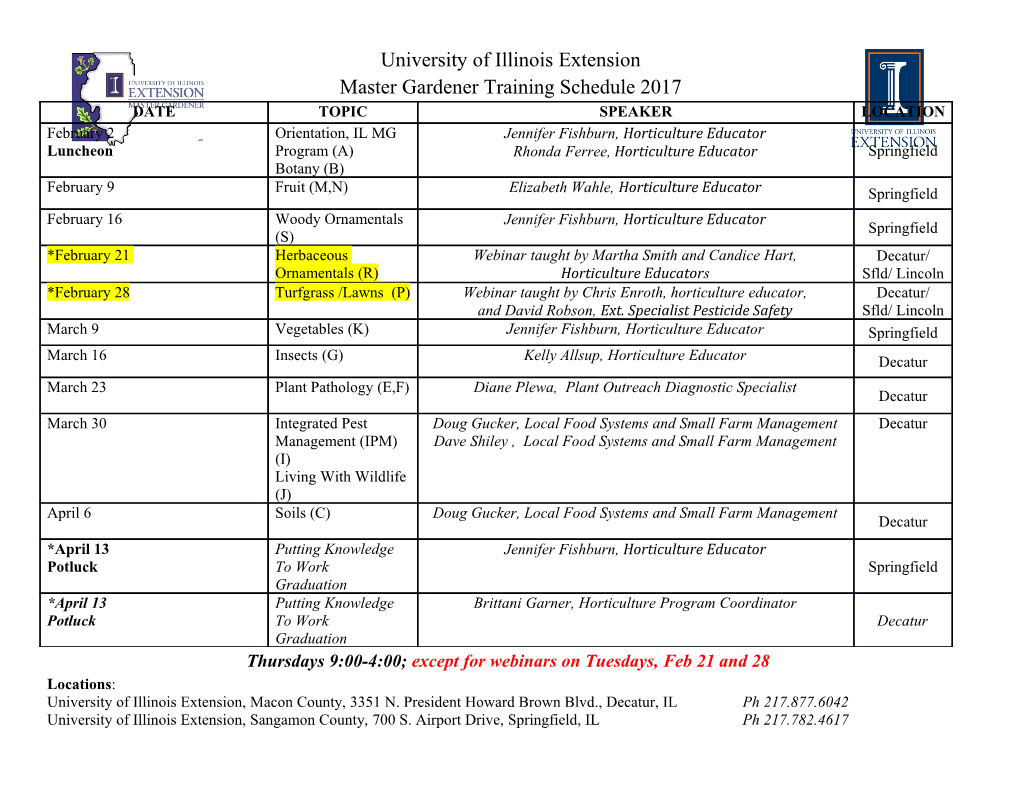
University of Cincinnati Date: 10/29/2010 I, Fumitaka Ichihashi , hereby submit this original work as part of the requirements for the degree of Master of Science in Aerospace Engineering. It is entitled: Investigation of Combustion Instability in a Single Annular Combustor Student's name: Fumitaka Ichihashi This work and its defense approved by: Committee chair: San-Mou Jeng, PhD Committee member: Shanwu Wang, PhD Committee member: Kelly Cohen, PhD Committee member: Asif Syed, PhD 1304 Last Printed:3/4/2011 Document Of Defense Form Investigation of Combustion Instability in a Single Annular Combustor A thesis submitted to the Graduate School of the University of Cincinnati in partial fulfillment of the requirements for the degree of Master of Science in the Department of Aerospace Engineering and Engineering Mechanics of the College of Engineering Nov 2010 by Fumitaka Ichihashi B.S., Aerospace Engineering, University of Cincinnati, USA Committee Chair: Dr. San-Mou Jeng Abstract The well known criterion for combustion instability is called the Rayleigh‘s criterion. It indicates that, for combustion instability to occur, the heat release rate (q‘) and pressure oscillation (p‘) must be in phase. This thesis describes measurement techniques and study methods for combustion instabilities that occurred in the prototype single annular sector Rich-Burn Quick-Mix Lean-Burn (RQL) combustor on the original (short) and new (long) experimental rig configuration with a focus on q‘ and p‘ measurements. A change in the configuration of the combustor rig was necessary in order to acquire more precise measurements of forward- and backward-moving acoustic pressure waves within the rig by mounting pressure transducers on preselected locations of the upstream duct, downstream duct and combustion area. Pressure transducers provided such local pressure behaviors as amplitude and frequency per location, also in addition to transfer functions that allow for the calculation of the acoustic impedance at any location within the combustor rig. A high-speed camera was capable of filming a chemiluminescene image, i.e., the rate of heat release through a quartz window that is mounted on the side of the combustor. Two imaging analysis techniques, Proper Orthogonal Decomposition and Fourier Transformation, were applied to the chemiluminescene image obtained by a high-speed video device. Two different test cases were investigated. Both a high and low fuel-to-air ratio were used for the investigation of the Rayleigh‘s criterion, which was confirmed by the corresponding q‘ and p‘ data sets. Finally, the resonance frequency that agrees with combustion instability was well predicted by utilizing the one-dimensional wave propagation theory and the known geometry of the combustor rig, temperature of fluid, and boundary conditions. ii iii Acknowledgements I would like to first state my deepest appreciation to my advisor, Dr. San-Mou Jeng, for providing me funding, guidance, and the opportunity to work on the combustion instability rig, and also on other projects and rigs at the University of Cincinnati Center Hill combustion research laboratory. I have learned extremely valuable engineering knowledge through these experiences. I would like to thank Dr. Kelly Cohen for guiding and supporting my thesis. His wisdom and passion have educated me in additional engineering fields of analysis and control systems; he has also coached me on my work ethic so that I could become a better engineer. My great appreciation for him will never be forgotten. Finally, I would like to express my great appreciation to Dr. Asif Syed for supporting my thesis and being a mentor to me for five years while at college. The experiences, knowledge, wisdom, and ethics that I have learned from him has become the core of my engineering work. My deepest appreciation also goes to Dr. Shanwu Wang of GE Aviation, for his time, effort, and advice as a committee member. Additionally, I would like to thank Mr. Curtis Fox for supporting and educating me on engineering measurements and programming throughout college life. Without him, I would not have enjoyed research and obtained the confidence I have now. My thanks also go to Dr. Samir Tambe and University of Cincinnati Aerospace Engineering undergraduate student, Joe Tscherne, for helping me set up and run the combustion instability experimental rig, and I am very thankful to University of Cincinnati Aerospace Engineering undergraduate student, Christine Englert, for enhancing my thesis writing. iv Table of Contents Abstract .......................................................................................................................................................... i Acknowledgements ...................................................................................................................................... iv Table of Contents .......................................................................................................................................... v List of Figures ............................................................................................................................................. vii Nomenclature .............................................................................................................................................. xii Chapter 1: Introduction, Literature Review, and Objectives: ....................................................................... 1 1.1 Introduction: ........................................................................................................................................ 1 1.2 Literature Review: .............................................................................................................................. 8 1.3 Objectives: ........................................................................................................................................ 14 Chapter 2: Experimental Setup ................................................................................................................... 15 2.1 Prototype Single Annular Combustor Sector .................................................................................... 15 2.2 Research Facility ............................................................................................................................... 15 2.2.1 Pneumatic System ...................................................................................................................... 16 2.2.2 Fuel System and Ignition ........................................................................................................... 16 2.3 Experimental Section ........................................................................................................................ 17 2.4 Instrumentation System .................................................................................................................... 18 Chapter 3: Chemiluminescene – POD and Video FFT (Combustion) ........................................................ 33 3.1 Theoretical Notes .............................................................................................................................. 34 3.2 FFT Analysis:.................................................................................................................................... 36 3.3 POD Analysis: .................................................................................................................................. 40 Chapter 4: Acoustic Wave (FFT and Impedance)....................................................................................... 64 4.1 TEST Results and Discussion – Original Rig (Short) Configuration: FFT ...................................... 64 4.2 Conclusion of Test Results from the Original Short Rig Configuration: .......................................... 70 4.3 Suggested Changes in the Original (Short) Rig Configuration: ........................................................ 71 4.4 Results and Discussion – New Rig (Long) Configuration: FFT ....................................................... 71 4.5 Pressure Dynamics Measurement ..................................................................................................... 76 4.5.1 Acoustic Transmission and Impedance: Step Area Change and Gradual Area Change ............ 76 4.5.2 Upstream Swirler Impedance Measurement (Non-Reacting Case): .......................................... 82 4.5.2.1 Validation of Upstream Transducers: ................................................................................. 82 4.5.2.2 Impedance Measurement: Upstream Duct .......................................................................... 85 4.5.2.3 Impedance Measurement: Step Change at Flange: ............................................................. 87 4.5.2.4 Impedance Measurement: Diffuser and Swirler ................................................................. 89 4.5.3 Downstream Swirler Impedance Measurement (Non-Reacting Case): ..................................... 91 4.5.3.1 Validation of Downstream Transducers: ............................................................................ 91 4.5.3.2 Impedance Measurement: Downstream Duct ..................................................................... 93 v 4.5.3.3 Impedance Measurement: Combustor................................................................................. 95 4.5.4 Swirler Impedance ....................................................................................................................
Details
-
File Typepdf
-
Upload Time-
-
Content LanguagesEnglish
-
Upload UserAnonymous/Not logged-in
-
File Pages188 Page
-
File Size-