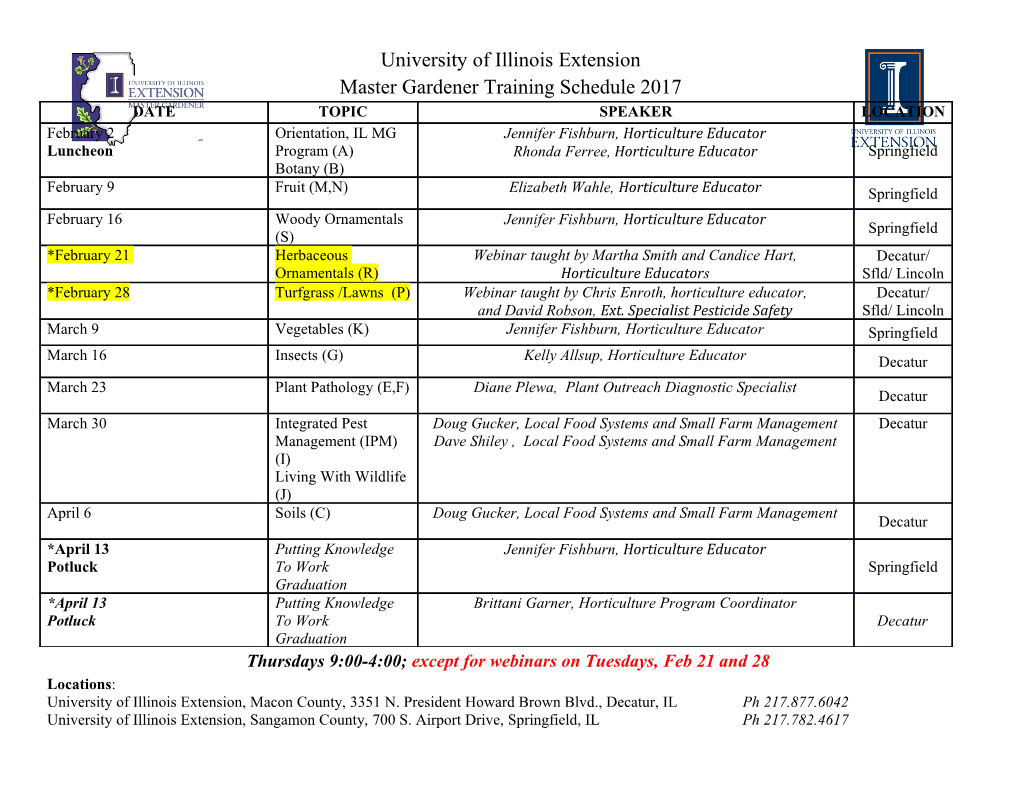
This article was downloaded by: [Faculty of Chemical Eng & Tech], [Krešimir Košutić] On: 30 April 2015, At: 03:13 Publisher: Taylor & Francis Informa Ltd Registered in England and Wales Registered Number: 1072954 Registered office: Mortimer House, 37-41 Mortimer Street, London W1T 3JH, UK Desalination and Water Treatment Publication details, including instructions for authors and subscription information: http://www.tandfonline.com/loi/tdwt20 Microfiltration of cutting-oil emulsions enhanced by electrocoagulation b a a b Janja Križan Milić , Emil Dražević , Krešimir Košutić & Marjana Simonič a Faculty of Chemical Engineering and Technology, Department of Physical Chemistry, University of Zagreb, Marulićev trg 19, HR-10000 Zagreb, Croatia, Tel. +385 1 459 7240 b Faculty of Chemistry and Chemical Engineering, Laboratory for Water Treatment, University of Maribor, Smetanova 17, SI-2000 Maribor, Slovenia Published online: 30 Apr 2015. Click for updates To cite this article: Janja Križan Milić, Emil Dražević, Krešimir Košutić & Marjana Simonič (2015): Microfiltration of cutting-oil emulsions enhanced by electrocoagulation, Desalination and Water Treatment, DOI: 10.1080/19443994.2015.1042067 To link to this article: http://dx.doi.org/10.1080/19443994.2015.1042067 PLEASE SCROLL DOWN FOR ARTICLE Taylor & Francis makes every effort to ensure the accuracy of all the information (the “Content”) contained in the publications on our platform. However, Taylor & Francis, our agents, and our licensors make no representations or warranties whatsoever as to the accuracy, completeness, or suitability for any purpose of the Content. Any opinions and views expressed in this publication are the opinions and views of the authors, and are not the views of or endorsed by Taylor & Francis. The accuracy of the Content should not be relied upon and should be independently verified with primary sources of information. Taylor and Francis shall not be liable for any losses, actions, claims, proceedings, demands, costs, expenses, damages, and other liabilities whatsoever or howsoever caused arising directly or indirectly in connection with, in relation to or arising out of the use of the Content. This article may be used for research, teaching, and private study purposes. Any substantial or systematic reproduction, redistribution, reselling, loan, sub-licensing, systematic supply, or distribution in any form to anyone is expressly forbidden. Terms & Conditions of access and use can be found at http:// www.tandfonline.com/page/terms-and-conditions Desalination and Water Treatment (2015) 1–10 www.deswater.com doi: 10.1080/19443994.2015.1042067 Microfiltration of cutting-oil emulsions enhanced by electrocoagulation Janja Krizˇan Milic´b, Emil Drazˇevic´a,*, Kresˇimir Kosˇutic´a, Marjana Simonicˇb aFaculty of Chemical Engineering and Technology, Department of Physical Chemistry, University of Zagreb, Marulic´ev trg 19, HR-10000 Zagreb, Croatia, Tel. +385 1 459 7240; emails: [email protected] (E. Drazˇevic´), [email protected] (K. Kosˇutic´) bFaculty of Chemistry and Chemical Engineering, Laboratory for Water Treatment, University of Maribor, Smetanova 17, SI-2000 Maribor, Slovenia, emails: [email protected] (J.K. Milic´), [email protected] (M. Simonicˇ) Received 17 November 2014; Accepted 10 April 2015 ABSTRACT Electrocoagulation (EC) was examined as a pre-treatment to the microfiltration (MF) of oily emulsions within the metalworking industry. The aim of this pre-treatment was to improve the MF performance in terms of flux decline and removal of oil by applying the minimum time of EC pre-treatment. Aluminium electrodes were used in EC, and flat sheet- regenerated cellulose membrane in MF. The experiments were carried out using cutting-oil emulsions at different concentrations (0.1, 0.5 and 1.0% (v/v)) and conductivity of about − 700 μScm 1. Drop size and zeta potential distributions were carried out to evaluate the impacts of EC time on zeta potential and average particle size. We found that in all emul- sions, 10 min of EC made the average size of oil particles bigger than the average size of the pores in MF and substantially reduced pore clogging and irreversible fouling. Reduced flux decline was related to the continuous formation of Al(OH)3 in EC that interconnected the colloidal oil particles into porous and irregularly shaped flocs which formed highly porous cake layer on the membrane surface. Keywords: Microfiltration; Electrocoagulation (EC); Cutting-oil emulsion; Cake layer; Flux decline; Zeta potential 1. Introduction low-energy consumption and a compact design com- pared to robust space-consuming traditional processes Cutting-oil emulsions are used as lubricants and [2–4]. The efficiency of MF/UF, however, may vary coolants specifically designed for metalworking pro- when considering fouling (e.g. pore-clogging) [5–9], cesses. Used cutting-oils may cause high levels of con- Downloaded by [Faculty of Chemical Eng & Tech], [Krešimir Košuti] at 03:13 30 April 2015 flux decline and consequently change in rejection [6]. tamination and rancid odours due to the presence of High water flux in MF/UF, along with high separation emulsifiers, corrosion inhibitors, extreme pressure of oil and considerably low mass transfer of very big agents, biocides or antifoam compounds. Their treat- and slow diffusing oil molecules, causes 10-fold higher ment and final disposal should be handled carefully [1]. concentration of oil at the membrane surface [10,11]. Micro- and ultra-filtration (MF/UF) have arisen Enhanced concentration of oil near the membrane sur- over time as an effective technology in the treatment of face may facilitate oil adsorption, and oil droplets may oily wastewaters as it offers high removal of oil, enter the membrane pores, i.e. clog them. In this way, irreversible fouling occurs [8,9,12]. Periodical hydraulic *Corresponding author. cleaning, such as backwashing, back-pulsing and 1944-3994/1944-3986 Ó 2015 Balaban Desalination Publications. All rights reserved. 2 J.K. Milic´ et al. / Desalination and Water Treatment pulsing by filtration, can reduce irreversible fouling i.e. reduce the concentration of heavy metals and the concentration polarisation or cake layer formation, chemical oxygen demand of the feed [25]. while irreversible fouling caused by oil adsorption and The main drawback of MF of cutting-oils is the flux pore plugging cannot be completely avoided without reduction which is usually caused by the cake layer further chemical cleaning [4]. Chemical cleaning of a resistance. One of the ways to decrease the cake layer membrane to reduce or eliminate irreversible fouling resistance is to increase the water permeability of the should be limited to a minimum frequency because cake layer. Water permeability of the cake layer repeated chemical cleaning increase the cost of the MF increases when the cake layer is formed of irregularly process. shaped flocs. The novelty of this study is in investiga- In practice, MF is always paired with a pre-treat- tion of electrocoagulation as a pre-treatment to the MF ment process [13,14], usually coagulation [15], which of the cutting-oil emulsions. More detailed, the impacts increases the size of the colloidal particles and pre- of EC time on zeta potential and average particle size of vents the irreversible fouling/flux decline [4]. The cutting-oil emulsions on the efficiency of microfiltration benefits of conventional coagulation coupled with were evaluated. Model cutting-oil emulsions and mem- membrane processes have been reported by many brane were characterised using experimentally obtained authors. For instance, several authors have reported drop size distribution and zeta potential (ζ) of a model that coagulation enabled the formation of a porous emulsion and scanning electron microscope (SEM). cake layer of flocs and reduced membrane fouling [5]. The porosity of a cake layer depends on the flocs’ characteristics, such as irregularity and size, and the 2. Materials and methods flocs’ stabilities within a rectangular channel with a 2.1. Cutting-oil emulsion feed spacer that are affected by cross-flow-induced shear stress [5]. Conventional mineral coagulants such The model cutting-oil emulsion was prepared by as Fe3+ may in some cases decrease fouling resistance mixing commercial cutting-oil (Die-Lubric 7050) and of the membrane [16,17]. In addition, Al3+ and Fe3+ deionised water. Commercial cutting-oil concentrate form less stable flocs that can be easily broken at the is, as its major part, made of polysiloxane. Its physical membrane’s surface [5]. The polyelectrolytes used as properties are; white colour, pH 9.5, density of − coagulants form shear stress-resistant flocs; however, 0.994 g mL 1 and dynamic viscosity of 0.0018 Pa s. The polyelectrolytes could potentially adsorb on the poly- volume percentages of model cutting-oil emulsions in meric membrane surface and induce severe fouling water were 0.1, 0.5 and 1% (v/v). The pH values of [5]. Al3+ was found to be a fair coagulant [15], the model cutting-oil emulsions were between 6 and especially if the same amount was in two steps [13]. 7.5, depending on concentration. The conductivity of μ During the second step, Al(OH)3(s) precipitate was the emulsions was around 700 S/cm. formed which enabled the formation of irregular flocs which later on formed porous cake layer on the mem- 2.2. Membrane characterisation: swelling, SEM and zeta brane surface. potential measurements Electrocoagulation would appear as fairly good pre-treatment to filtration of cutting-oils [18–20], as A flat sheet polymeric (regenerated cellulose (RC) compared to the conventional dosing of Al3+, under —UC030) membrane was kindly supplied by MICRO- the influence of an electric current, electrocoagulation DYN-NADIR GmbH (Wiesbaden, Germany). UC030 produces metallic ions (Al3+) in situ, by the electro- was selected due to its high water flux and good foul- chemical dissolution of electrode (anode). Dissolution ing resistance to organics [4]. Downloaded by [Faculty of Chemical Eng & Tech], [Krešimir Košuti] at 03:13 30 April 2015 of aluminium is always paired with the instant forma- Membrane swelling, i.e.
Details
-
File Typepdf
-
Upload Time-
-
Content LanguagesEnglish
-
Upload UserAnonymous/Not logged-in
-
File Pages11 Page
-
File Size-