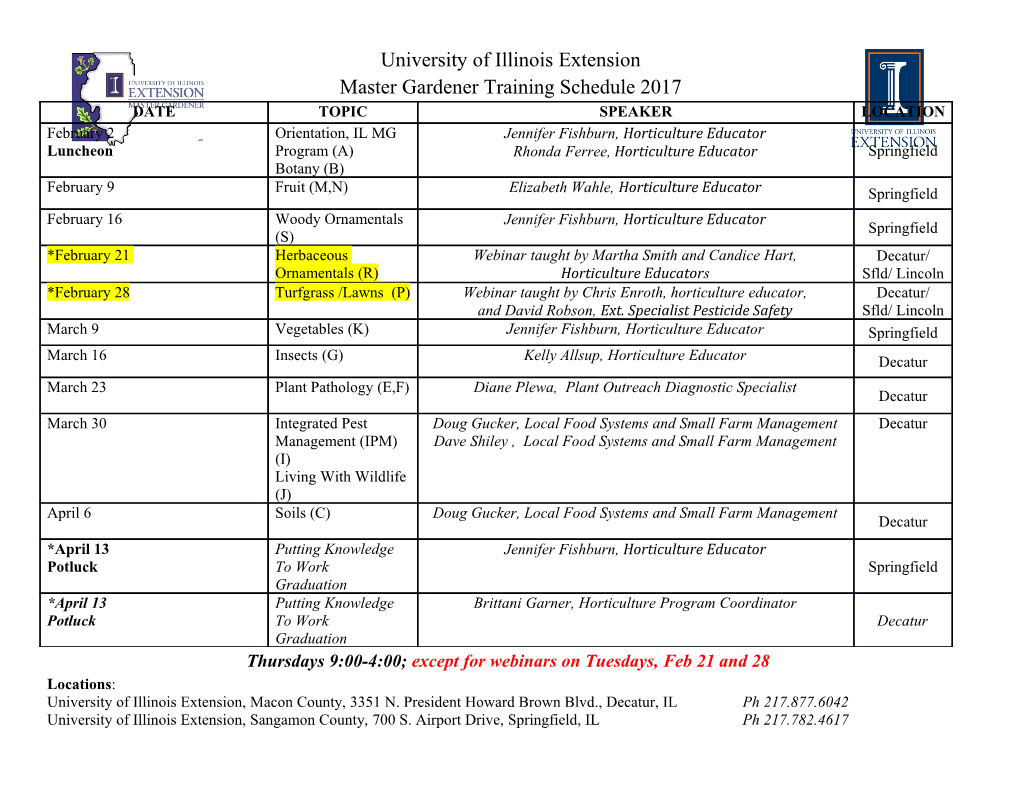
Aluminum-Water Energy System for Autonomous Undersea Vehicles Nicholas B. Pulsone, Douglas P. Hart, Andrew M. Siegel, Joseph R. Edwards, and Kristen E. Railey Aluminum-fueled energy systems that leverage In recent years, autonomous systems the energy-dense aluminum-water reaction to » have been developed for applications span- ning air, ground, and both sea surface and produce both hydrogen and electrical power subsurface domains. The technical chal- are maturing rapidly. These systems are safe, lenges faced by these systems vary considerably from one reliable, quiet, and completely air independent. domain to the next. This article describes a collaborative Furthermore, they employ scalable designs and research effort between the Department of Mechanical Engineering at MIT and Lincoln Laboratory to address require few moving parts. These advantages are the problems inherent in powering autonomous undersea leading to the imminent use of aluminum-fueled vehicles (AUV). systems in undersea applications. When operating below the sea surface, an AUV must navigate without access to the Global Positioning System (GPS) and with relatively short-range, limited- bandwidth communication links. These constraints make it difficult for operators to interact with the AUV, thereby placing a high demand on the autonomous behavior of the vehicle. Also, an AUV’s lack of access to air while it is submerged significantly limits energy storage options. Currently, most commercial AUV sys- tems use lithium-ion battery technology, which provides three days of endurance to a mid-sized AUV travel- ing at 3 knots. The goal of our research is to increase endurance by a factor of 10, expanding mission time for the same mid-sized AUV from 3 to 30 days. A tenfold increase in endurance could expand the uses of AUVs into new mission areas. Background and Motivation Recent advances in technology have enabled the development of highly capable AUVs for a wide range of applications, such as mapping the seafloor, characterizing VOLUME 22, NUMBER 2, 2017 n LINCOLN LABORATORY JOURNAL 79 ALUMINUM-WATER ENERGY SYSTEM FOR AUTONOMOUS UNDERSEA VEHICLES FIGURE 1. The illustration shows the current one-way operating range (small circle) and the one-way goal range (large Hawaii circle) for mid-sized AUVs launched from Hawaii. Current AUV one-way range = 166 miles Goal: Increase AUV one-way range by 10x = 1660 miles subsurface ocean currents, and monitoring marine mid-sized AUVs deployed from Hawaii. The smaller circle biology. Autonomous unmanned vehicles used for military represents the one-way operating range given a platform activities are equipped with sensors to detect sea mines speed of 2 knots for three days, or approximately 166 and characterize the undersea environment prior to the miles. If the platform endurance is increased by a factor start of operations. Future military missions may also of 10, then the one-way operating range increases to 1660 employ AUVs to collect data for intelligence, surveillance, miles, which is denoted by the larger circle. and reconnaissance (ISR). In the civil and commercial In addition to extending AUV endurance, a higher sectors, AUVs are used for disaster recovery and for oil energy density allows higher-speed operations that enable and gas exploration. In all these applications, the system’s an AUV to perform ship tracking and interception. Other performance, thus the success of the mission, is limited by components of an undersea network, including sono- the total energy stored in the AUV power source. buoys and bottom-mounted sensors, will also benefit from Many fuel sources have been considered to power increased endurance. AUVs. Combustible organic fuels, such as gasoline or jet propellant, are energy dense but have not been used in Energy System Options AUVs because typical missions require extended peri- Over the years, researchers looking to maximize AUV ods of time below the surface without access to oxygen. endurance, given the constraint of a fixed hull volume at Instead, electrochemical power sources such as lithium- neutral buoyancy, have explored various fuel options for ion batteries power most industry-built AUVs. In mid- powering underwater systems. In undersea applications, sized AUVs, lithium-ion technology can power an AUV the available volume within the hull of a vehicle imposes at 2 to 3 knots for three days [1]. However, because many a volume constraint on the vehicle’s energy system, and missions demand timelines longer than three days, AUVs the need to maintain neutral buoyancy imposes a con- used in such missions require a power source with a high straint on the system’s mass. Hence, for undersea sys- enough energy density to achieve the needed endurance. tems, both volumetric and gravimetric energy densities Currently, this energy density is not available. are important. These constraints apply to the complete The map in Figure 1 illustrates the benefit of energy system, which includes the fuel, the oxidizer (if increased AUV endurance. Operating radii are shown for any), all the plumbing, electronics, and any unfilled hull 80 LINCOLN LABORATORY JOURNAL n VOLUME 22, NUMBER 2, 2017 NICHOLAS B. PULSONE, DOUGLAS P. HART, ANDREW M. SIEGEL, JOSEPH R. EDWARDS, AND KRISTEN E. RAILEY volume. Thus, the specific gravity of the fuel itself can the changing demands during the mission. Finally, an vary, so long as the final energy system maintains a spe- additional advantage for the energy source is to produce cific gravity of 1. Fuel options that exhibit high volumetric minimal impact on the environment. energy density and are considered safe to handle include Table 1 compares the most relevant characteristics aluminum, anthracite, and silicon. Figure 2 illustrates for a number of different energy options. As indicated, the energy density for a number of fuel options. The an energy source based on an aluminum-water reac- energy density per unit mass is on the x -axis, and energy tion has an extremely high energy density and uses density per unit volume is on the y-axis. water as an oxidizer, making it a particularly attrac- An energy source for an AUV must operate without tive fuel for AUVs. access to air or oxygen, be reliable, and be easy to refuel Currently, the most common energy sources used even under nonideal conditions. For military applica- in undersea systems are lithium-ion batteries. Batter- tions, the energy source also must be marine-safe for ies, which can be custom fabricated from individual transportation and exhibit a low acoustic signature for cells, fit well into AUV hulls. They can also supply covert missions. In some applications, power demand power on demand, work during submerged operations, varies widely during a mission. For example, the vehicle and are reliable and silent. Despite the technological may need to first loiter at a low speed and then acceler- advances in lithium-ion batteries, they have limited ate to a higher speed for a short period of time. In such energy density and must be recharged. In addition, a situation, the energy subsystem must be sufficiently because large lithium-ion batteries can become hot flexible to output the appropriate power levels to meet enough to ignite nearby materials or even erupt into 90 Aluminum Reacts with water 80 Aluminum Nanoparticles react with water Lithium Silicon Lithium-ion battery Reacts with oxygen at high temperature 70 Anthracite 60 50 Magnesium Polystyrene Lithium borohydride 40 Iron Polyethylene Zinc Diesel Polyester Gasoline 30 Butanol Gasohol E85 Lithium Energy density per unit volume (MJ/L) Energy density per unit volume Glucose 20 Ethanol Liquid natural gas Sodium Methanol Liquid hydrogen 10 Natural gas (250 bar) Liquid ammonia Zinc-air battery Natural gas Lithium-ion battery Hydrogen gas 0 0 20 40 60 80 100 120 140 160 Energy density per unit mass (MJ/kg) FIGURE 2. Energy densities of select fuels are compared. These data are for relative comparison only; the volume and mass penalties of oxygen and water are not included. Data for lithium-ion and zinc batteries (which are complete energy storage systems and not fuels) are also included for relative comparison. VOLUME 22, NUMBER 2, 2017 n LINCOLN LABORATORY JOURNAL 81 ALUMINUM-WATER ENERGY SYSTEM FOR AUTONOMOUS UNDERSEA VEHICLES Table 1. Comparison of Energy Options for Underwater Vehicles Energy options Energy Submerged Reliable Easy Safe Low noise Power on Eco- dense operation refuel demand friendly Battery ü ü ü ü ü ü Wave energy N/A N/A ü ü ü Solar N/A ü ü ü Docking N/A ü ü ü ü ü Tether to shore N/A ü ü ü ü Combustion ü ü ü ü Ga/Al-H2O* ü ü ü ü ü ü ü ü Monopropellants ü ü ü ü Nuclear ü ü ü N/A ü ü ü *gallium/aluminum-water flame themselves when damaged, they present a major for the water-gas reaction to proceed efficiently. Also, safety concern on board marine vessels. the carbon monoxide waste is difficult to separate from Fuel cells and hybrid energy systems have the the hydrogen; it “poisons” the fuel cell catalyst; and it potential to increase power density in underwater is difficult to store and dispose of safely. systems while also lowering construction and main- Silicon, with a volumetric density of approxi- tenance costs. Fuel cells that convert chemical energy mately 76 MJ/L, is another potential high-density fuel. directly into electrical energy are particularly advan- Researchers at the University of Buffalo have demon- tageous for AUVs on covert missions because the cells strated that nano-sized particles of silicon react with utilize few moving parts and, consequently, have a low water to release hydrogen gas [2]. The hydrogen can acoustic signature. The main drawback of commercial then be used to power a fuel cell. The process to gener- air-breathing fuel cells is packaging.
Details
-
File Typepdf
-
Upload Time-
-
Content LanguagesEnglish
-
Upload UserAnonymous/Not logged-in
-
File Pages12 Page
-
File Size-