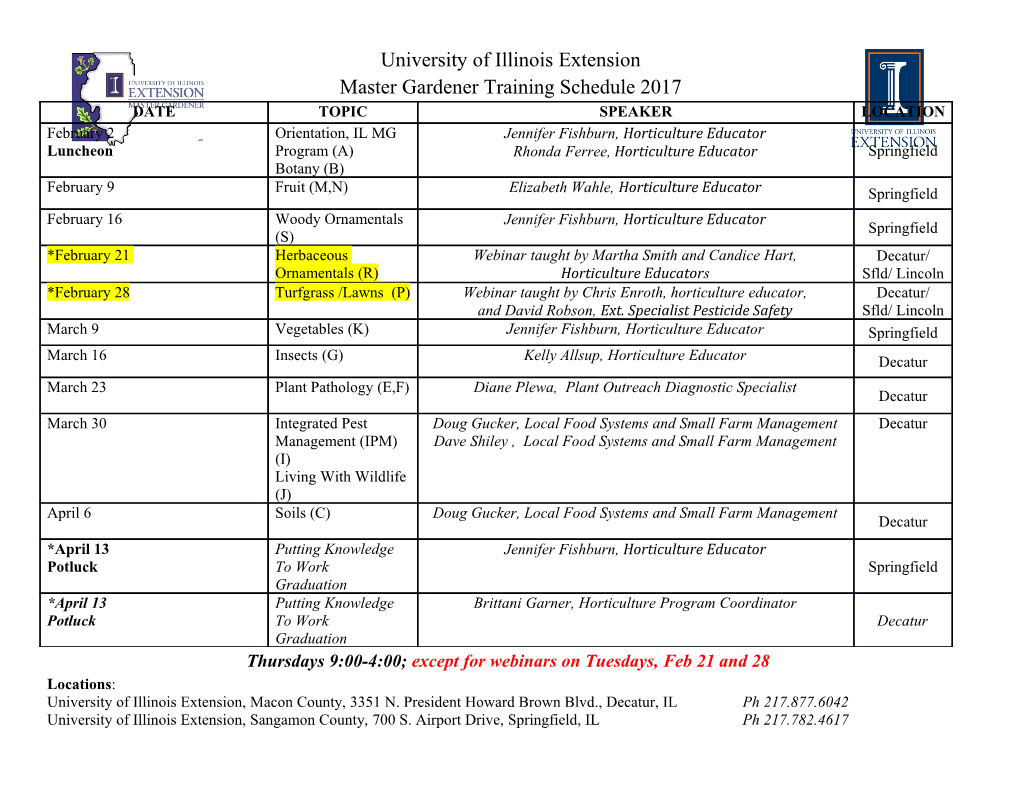
Overview of the NASA Systems Approach to Crashworthiness Program Lisa E. Jones NASA Langley Research Center l.e.j ones @ larc.nasa.gov Hampton, VA Abstract The NASA Aviation Safety Program was developed in response to the federal government's goal to reduce the fatal accident rate for aviation by 80% within 10 years. ACcident Mitigation is a primary element of the Aviation Safety Program. The overall Accident Mitigation goal is to provide technology to the air transport industry to enable a decrease in the rate of fatalities and injury from crash loads and from in-flight and post- crash explosion and/or fire. Accident Mitigation is divided into two main elements - Fire Prevention and Systems Approach to Crashworthiness. The Systems Approach to Crashworthiness goal is to develop and promote technology that will increase the human survival rate or reduce the fatality rate in survivable accidents. The technical background and planning, selected technical activities, and summary of future efforts will be presented in this paper. Introduction February 1997 a national goal to reduce the fatal accident rate for aviation by 80 According to the Gore Commission final percent within 10 years. report, the worldwide demand for air travel is expected to double or triple by In response to the presidential 2017 with the requirement for $1 trillion announcement, NASA initiated the in new aircraft deliveries [1]. Without Aviation Safety Investment Strategy decreasing the accident rate, such a Team (ASIST), which sponsored four traffic volume would lead to 50 or more industry- and government-wide major accidents a year. Given the very workshops to define research needs. visible, damaging, and tragic effects of The planning effort lasted from February even a single major accident, this to April 1997, and involved over 100 number of accidents would clearly have industry, government, and academic an unacceptable impact upon the organizations. A subset of the research public's confidence in the aviation investment areas from ASIST, denoted system and impede the anticipated Human Survivability, formed the basis growth of the commercial air-travel for the technical activities within market. President Clinton announced in NASA's Aviation Safety Program (AvSP) Accident Mitigation (AM) Presented at the American Helicopter Society element. Human survivability included 58 th Annual Forum, Montreal Canada, June 11- the areas of mitigating the impact and 13, 2002. This paper is a work of the U.S. fire effects of an accident and in-flight Government and is therefore in the public domain. fire prevention. The official start of the AvSP was FY 2000. Prior to the start of the AvSP, Crashworthiness and fire focus on specific functions to meetthe prevention were included in the program objectives. The first sub- Airframe Airworthiness Assurance elementis crash load predictions using (AAA) program. AAA provided the finite element modeling. The second opportunity to upgrade computational sub-element, occupant protection, capabilities, increase instrumentation includesdevelopingdesignapproaches, inventories, purchase mechanical standards,and materials for protecting equipment, fund survey reports on occupants from crash loads. Crash transport,rotorcraft andgeneralaviation resistant fuels systems (CRFS) is the accidents and a fuel system report third sub-element. CRFS includes [2,3,4,5],hold workshopswith industry design approaches, standards, and andtheFederalAviation Administration materialsfor protection againstrupture (FAA), and conduct analyses and of fuel system tanks, lines, and other testing. Basedon thesesurveyreports, components. industry and FAA input, and in-house efforts,theplansfor theAvSPAM were The Systems Approach to developed. Crashworthiness plans include partneringwith customersto accomplish AvSP emphasizes not only the end goals. The partnersinclude the accident rate reduction, but also a Federal Aviation Administration, U.S. decreasein injuries and fatalities when Army, analyticalcodevendors,seatand accidentsoccur. The AvSP goal is to restraint manufacturers, airframe develop and demonstratetechnologies manufacturers and fuel system thatcontributeto a reductionin aviation manufacturers. accidentandfatality ratesby a factorof 5 by year 2007andby a factor of 10 by A more detailed description of year2022. the technical approachand work being conducted in each sub-element is To reach the goal of reducing presentedin thefollowing sections. injury and fatality rates in accidents, understandingthe crashenvironmentis Crash Load Predictions required. For occupantsto survive a crashof an aircraft, a numberof things In the last ten years, significant must happen. The majority of the advances have occurred in computing impact energymustbe absorbedby the capabilities, data acquisition systems, airframe structure and seat. The and finite element simulation. These restraintsmust function well during the technical advances provide the ability to primary and secondary impacts (eg. effectively evaluate detailed finite minimize headstrikes). The seatmust element models. For the aircraft remainattachedto the floor. An egress industry, use of finite element codes in path must remain available and there designing crashworthy structures has not must be enoughtime for the occupants proven cost effective. In addition, no to egressbefore fire and smokebecome procedures or regulatory guidelines have incapacitating. Therefore,the Systems been established for use of codes in the Approach to Crashworthinessplan is crashworthiness certification process. divided into three sub-elements that Certification for crashworthiness relies solelyon seattests[6,7,8]. A full-scale crashtestcouldbeanoptionto certify an aircraft design that utilizes the systems approach.However,thisapproachis not accepted as an economically viable method due the manufacturing cost. Also, there is a disconnectbetweenthe designer's needsand the certification process. The designerneedsloads and displacementsto sizestructureor design Figure 1. Composite helicopter full- energy absorbing structure. The scale crash test and analytical model. certification process needs the input floor acceleration pulse and occupant responseinformation. No method to quantify the accuracyof the models is currently available. To addressthese issues,the crashload prediction efforts include best practices in analytical model development, guidelines and standards for test and analysis correlation,enhancementof theanalysis codesfor useasdesign,andcertification tools. Best Practices The best practices in analytical model development work is based on modeling of complete aircraft as presented in Figure 1.[9], fuselage sections shown in Figure 2. [10], outside customer projects [11], and small-scale lab experiments [12]. The structures are composed of composite, metallic, or hybrid materials. Data are being compiled for a report on the effective methods for developing detailed finite element crash models. The information will be updated as necessary. These documented data are intended to help the user develop the best model in a reasonable time by avoiding approaches that do not work. Examples of best Figure 2. Energy absorbing fuselage test practices to be included in the document article and analytical model. range from how to prevent geometric discontinuities, to the importance of Historically, when full-scale accurate material properties [13]. aircraft or sections of aircraft were Ultimately, these practices should be tested, instruments were mounted to give usedto develop a full aircraft model information on the performance of a used for designing and certifying concept. As the test and analysis crashworthyaircraft. One approachfor correlation requirements and this would requiretestingbut thetesting expectations change, the instrumentation couldbelimited to a fuselagesectionsor of the test article must evolve to provide critical components of the aircraft the data needed. For example, there are structure. Experimentaldatafrom these usually many accelerometers located on component tests would be compared the floor structure and on large masses. analytical results. If the correlation However, these data give little validatesthecomponentanalysisandthe information on the load path through the full aircraftmodelis developedwith the structure below the floor. The ability to samepractices,confidenceis increased correlate the predicted and test loads in for the validity of the full aircraft main structures in the wing box area simulation. would be advantageous to the designer. This information could be used to Test Analysis Correlation (TAC) identify structural members that need to be modified. However, obtaining this Guidelines and standards for test information from a test is not analysis correlation are needed to straightforward. Strain gages, though quantify the accuracy of the model excellent for use in quasi-static testing, simulations. Along with the offer little useful information in a full- computational capabilities, significant scale crash test. Part of the TAC effort advances have occurred in data is focused on development of acquisition systems. Digital data instrumentation for use in the crash acquisition systems are capable of environment. Other TAC efforts involve recording multiple channels and millions using the crash simulation results as a of data points at rates exceeding 10khz. guide for instrumentation layout, Analytical models with tens of efficient data reduction processes and thousands of elements are common
Details
-
File Typepdf
-
Upload Time-
-
Content LanguagesEnglish
-
Upload UserAnonymous/Not logged-in
-
File Pages9 Page
-
File Size-