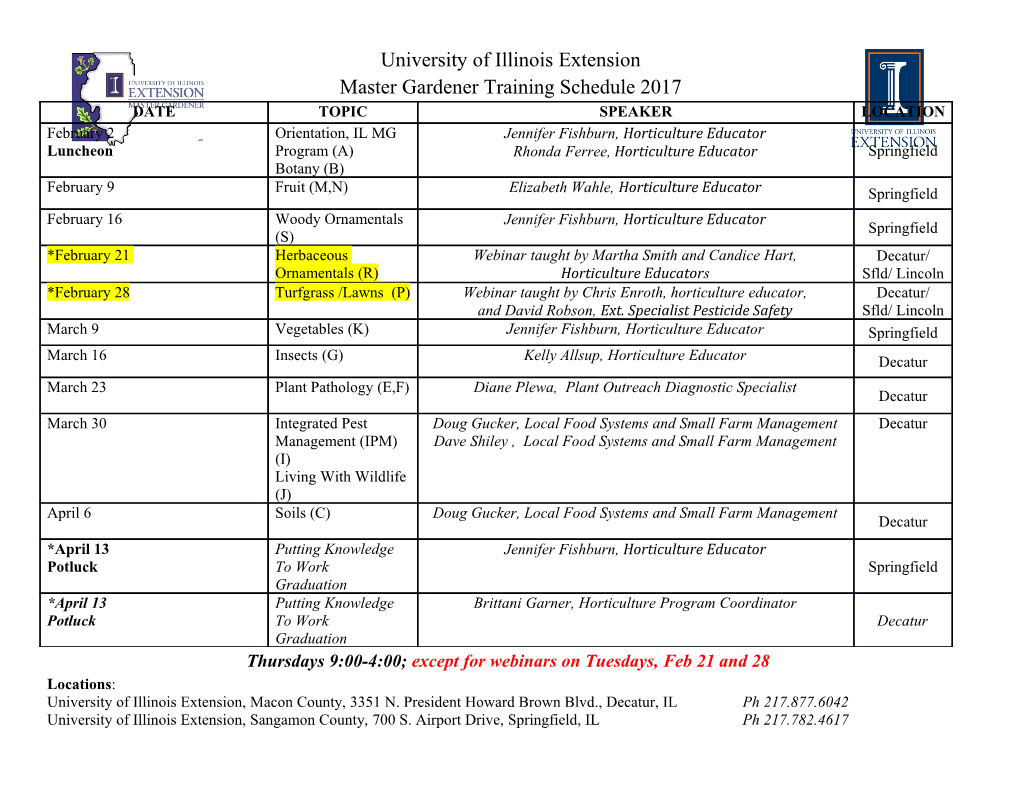
THIS DOCUMENT IS PROTECTED BY U.S. AND INTERNATIONAL COPYRIGHT. It may not be reproduced, stored in a retrieval system, distributed or transmitted, in whole or in part, in any form or by any means. Downloaded from SAE International by Peter Ernst, Saturday, September 15, 2012 04:51:57 PM Optimizing the Cylinder Running Surface / Piston 2012-32-0092 System of Internal Combustion Engines Towards 20129092 Published Lower Emissions 10/23/2012 Peter Ernst Sulzer Metco AG (Switzerland) Bernd Distler Sulzer Metco (US) Inc. Copyright © 2012 SAE International doi:10.4271/2012-32-0092 engine and together with the adjustment of the ring package ABSTRACT and the piston a reduction of 35% in LOC was achieved. This Rising fuel prices and more stringent vehicle emissions engine will go into production in September 2012 with requirements are increasing the pressure on engine limited numbers coated in the Sulzer Metco Wohlen facility manufacturers to utilize technologies to increase efficiency in Switzerland, until an engineered coating system is ready on and reduce emissions. As a result, interest in cylinder surface site to start large series production. More details on the coatings has risen considerably in the past few years. Among engine performance and design changes made to the cast these are SUMEBore® coatings from Sulzer Metco. These aluminium block in order to take full advantage of the coating coatings are applied by a powder-based air plasma spray on the cylinder running surfaces is presented in the paper (APS) process. The APS process is very flexible, and can from Zorn et al. [1]. process materials which wire-based methods cannot, particularly metal matrix composites and pure ceramics. INTRODUCTION Applications range from small 2-stroke engines, motorcycles, Over the past years, the demands in the field of internal and lightweight passenger car engines, up to high-speed combustion engines have increased continuously. The diesel truck engines and medium-speed diesel engines. reasons are manifold. Often, we see the reduction of CO2 emissions on top of the list. Reducing weight, minimizing The compositions of the coatings can be tailored to the friction, reducing consumption of fuel and oil, optimizing the specific challenges in an engine, e.g. excessive abrasive wear, combustion process, and ensuring the long term stability of scuffing, corrosion caused by adulterated fuel, improved heat the initial engine performance are all part of achieving this transfer from the combustion chamber into the water jacket, overall goal. In addition to these demands, engine developers etc. A number of engines have been tested successfully. Most are facing additional challenges with adulterated fuels in of them exhibited significant reductions in lube oil emerging markets, hybridization of cars and in-engine consumption (LOC), reduced fuel consumption, very low reduction of emissions with exhaust gas recirculation (EGR), wear rates and corrosion resistance on the liner surfaces. This although the latter is so far mainly an issue in commercial coating solution has been commercialized in various markets. vehicles and large diesel engines. Some of these engine It has proven to be suitable for mass production on both new developments give rise to corrosion and wear issues on the engine blocks and liners, and for repair of worn-out parts. cylinder surfaces. Such coatings will continue to play an important role when it comes to reductions of weight and emissions in internal Internal combustion (IC) engines still have a large potential combustion engines. An example of such a coating solution for further improvement, and significant development will be outlined. It has been carried out in collaboration with activities are ongoing in the areas of turbocharging, engine BRP Powertrain in Austria on a 1.5L 3-cylinder aluminium THIS DOCUMENT IS PROTECTED BY U.S. AND INTERNATIONAL COPYRIGHT. It may not be reproduced, stored in a retrieval system, distributed or transmitted, in whole or in part, in any form or by any means. Downloaded from SAE International by Peter Ernst, Saturday, September 15, 2012 04:51:57 PM Figure 1. Left: schematic representation of the SUMEBore coating process (from left to right, including honing). Right: One SM F210 plasma torch in an aluminum 3-cylinder engine block. control, mechanical design, application of new materials, etc. PROCESS OVERVIEW Along with the optimization of other engine components, the cylinder running surface often gets into the focus of engine The whole APS cylinder surface coating process, except for designers. Honing structures are being optimized on existing, the cleaning/washing step, is portrayed schematically in proven cylinder surfaces such as cast iron blocks and sleeves, Figure 1 on an aluminum engine block. The process flow is hypereutectic aluminum alloys (Alusil), and on various identical for coating of liners that are typically made of cast galvanic coatings (e.g. Nikasil). In parallel, the direct coating iron or steel. of cylinder running surfaces with the application of thermal spray processes has become more and more important. A rotating plasma torch (RotaPlasma) is used to apply the Applying a coating directly to the cylinder surfaces in coating to cylinder surfaces in engine blocks. Powdered aluminum engine blocks can eliminate the need for cast iron material is brought into the plasma plume with a carrier gas. sleeves. This can significantly reduce the weight of the The particles melt, are accelerated, and hit the surface to engine block, leads to improved heat transfer from the build up the coating layer. combustion chamber into the water jacket and can - if required - give corrosion protection of the running surface. Preparation and Surface Activation Before the coating is applied, the bore diameter has to be Apart from the atmospheric plasma spray (APS) technology, oversized to accommodate the coating. The oversize is which has been applied in mass production over the past ten determined by the target coating thickness after final years, other thermal spray processes found its way into niche machining (honing). This pre-machining can be carried out applications in various market segments. The twin wire arc by means of line boring, single point drilling, honing, or other spray (TWAS) and the plasma transferred wire arc (PTWA) processes. An arithmetic roughness average Ra < 4μm is processes are the most important of these alternative thermal required after pre-machining. Thereafter the part has to be spray processes used for cylinder surface coating thoroughly cleaned to remove any oil and grease and residues applications. The capability of the APS process for mass from the machining process from the surface. This is production has been amply proven; it has been used to coat typically done in a dedicated washing machine. The specified more than 2.5 million passenger car cylinder bores over the surface tension after cleaning and drying is about 36mN/m in past 10 years and the developments in the various markets the area where the coating will be applied. The cleanliness have continuously been reported can easily be checked on the part using a test fluid of defined [2,3,4,5,6,7,8,9,10,11,12,13,14,15,16,17,18,19,20,21,22,23,24 surface tension [31]. A clean surface is necessary to ,25,26,27,28,29,30]. Recent developments in this area include guarantee the adhesion of the coating. the industrialization of the process and obtaining the series- production readiness in various additional market segments The next step in the coating process is the so-called activation (including recreational and commercial vehicles, power of the surface. This step consists of a roughening of the generation, marine propulsion, and rail), as well as the substrate surface to increase the surface area and produce a provision of suitable coating materials to cope with the structure which facilitates the mechanical interlocking of the different challenges in these market segments. coating with the substrate. Since the adhesion of the coating is not due to a metallurgical bonding with the substrate, as would be the case for a weld overlay coating, the adhesion of the coating is dependent on this roughening. The activation (roughening) of the surface can be accomplished by a number THIS DOCUMENT IS PROTECTED BY U.S. AND INTERNATIONAL COPYRIGHT. It may not be reproduced, stored in a retrieval system, distributed or transmitted, in whole or in part, in any form or by any means. Downloaded from SAE International by Peter Ernst, Saturday, September 15, 2012 04:51:57 PM Figure 2. Surfaces activated by three different processes. Insets: metallographic sections through plasma coatings on activated surfaces (as sprayed). Top left: grit blasting with Al2O3. Top right: high pressure water jet. Bottom: mechanical activation (machining), with the profile developed by the Braunschweig University of Technology. of methods. Contrary to widespread perception, APS coatings block design. In case of cast iron surfaces, only grit blasting can be applied to all different kinds of activated surfaces, not with corundum (Al2O3) is applied today. only grit blasted surfaces. Activated surfaces generated with the most commonly used activation processes and an APS Grit blasting can be applied to all different substrate coating deposited onto these surfaces are shown in Figure 2. materials. For very high hardness materials, the grit could be SiC. In contrast to the high pressure waterjet activation All of the activation processes shown in Figure 2 have found process, grit blast activation does not enlarge any casting applications with thermal spray processes on cylinder bore pores that may be present on the cylinder surface. This will surfaces. The dovetail profile shown at the bottom of Figure 2 allow a larger acceptable pore size in the casting if grit blast was developed by the Braunschweig University of activation is used, which will increase the casting yield and Technology [32].
Details
-
File Typepdf
-
Upload Time-
-
Content LanguagesEnglish
-
Upload UserAnonymous/Not logged-in
-
File Pages12 Page
-
File Size-