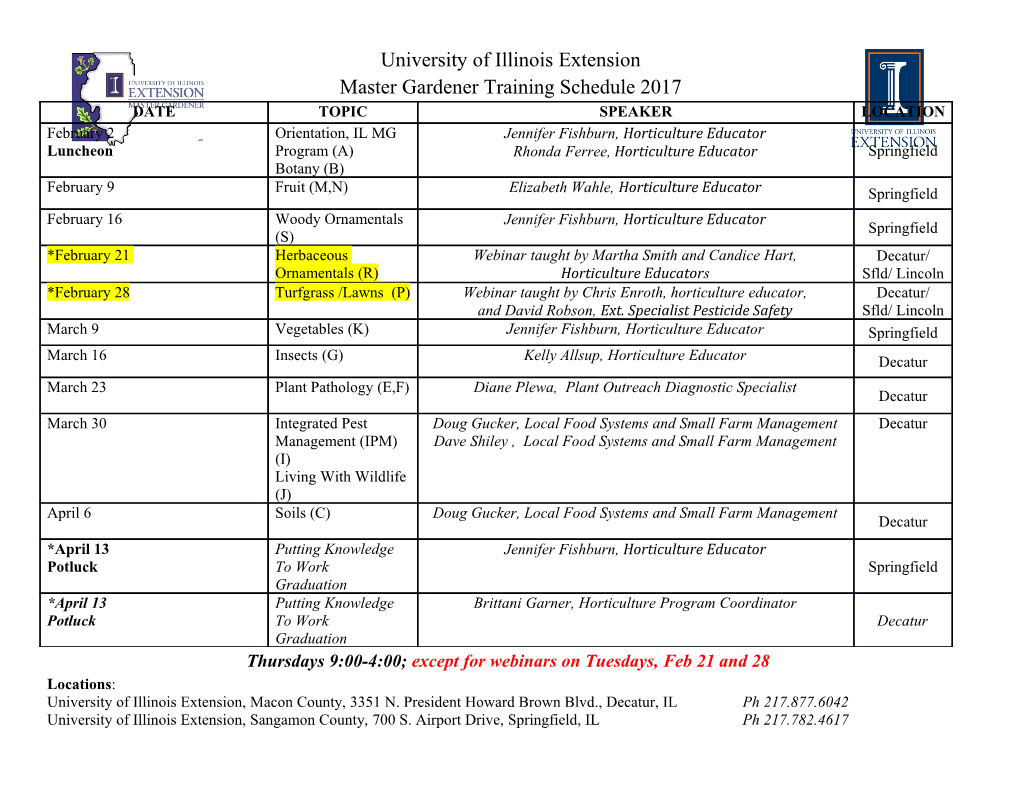
Applications – Car body – Crash Management Systems Table of contents 4 Crash management systems ........................................................................................................ 2 4.1 Aluminium extrusions for crash management systems ............................................................ 4 4.1.1 Bumper beams ............................................................................................................ 5 4.1.2 Front crash management system ................................................................................. 11 4.1.3 Rear crash management systems ................................................................................ 21 4.1.4 Pedestrian protection requirements ............................................................................. 23 4.1.5 Bull bars .................................................................................................................. 24 4.2 Roll-over protection .......................................................................................................... 25 Version 2013 © European Aluminium Association ([email protected]) 1 4 Crash management systems In the design of an automobile, a most important task is to minimize the occurrence and consequences of automobile accidents. Automotive safety can be improved by "active" as well as "passive" measures. Active safety refers to technology which assists in the prevention of a crash. Passive safety includes all components of the vehicle that help to reduce the aggressiveness of the crash event. Crash protection priorities vary with the speed of the car when crash occurs: at speeds up to 15 km/h, the main goal is to minimize repair costs; at speeds between 15 and 40 km/h, the first aim is to protect pedestrians; at speeds over 40 km/h, the most important concern is to guarantee occupant protection. The term “Crash Management System” is generally used to describe the structural module consisting of the bumper and the related attachments which connect to the longitudinal beams of the car. Front bumpers are normally connected to the front longitudinal beam by a separate deformation element (“crash box”). Rear bumpers are, however, mounted directly to the rear longitudinal beam. But the bumper system can’t be considered as an isolated structural module. Its design must be optimized taking into account the crashworthiness of the overall body structure, in particular the deformation characteristics of the safety cell and the crumple zones. The purpose of the front/rear bumper system is: To absorb energy at the start of a crash and to guide the remaining crash forces into the rest of the body structure. At low and medium speed: to minimize the damage of the vehicle in order to reduce insurance cost. At higher speed: to guide the crash forces into the body structure in such a way that the probability for a disintegration of the body structure is low and the survival of the occupants is ensured. To meet the legal (as well as any higher, OEM-specified) requirements regarding the energy absorbing ability. Another important (and often quite challenging) function of the front/rear bumper system is the towing function. This function requires both stiffness and strength. Bumper design concepts have changed drastically over the last 20 to 30 years. In the past, cars were equipped with bulky, protruding bumpers to comply with the bumper standards of the 1970s and early 1980s. More demanding safety regulations and different styling concepts have resulted in new designs. Styling fashion has drastically changed the visual appearance of the bumpers. Whereas in the past, bumpers also served as a bright shiny decorative design element, they are now predominately concealed by a painted thermoplastic fascia. Since the late 1980s, most bumpers fascia systems are colour coordinated with the body. The four basic bumper design principles (where specific features can also be combined) are: The traditional design with a visible metallic transverse beam that decorates the front or rear end of the vehicle and acts as the primary energy absorber in a collision. This concept has been popular in the past, but is seldom used today. The plastic fascia and reinforcing beam system that is fastened directly to the front/rear longitudinal beams. The reinforcing beam also serves as the first structural cross- member. While this arrangement leads to a small sacrifice in bumper performance, it increases the overall vehicle crashworthiness The system consisting of a plastic fascia, a reinforcing beam and mechanical energy absorbers. The energy absorbers are either of a reversible type (“shock absorbers”) or deformation elements (“crash boxes”) which are replaced after a crash. A system which includes a plastic fascia, a reinforcing beam and a propylene foam or a honeycomb energy absorber which is placed between the plastic fascia and reinforcing Version 2013 © European Aluminium Association ([email protected]) 2 beam. This approach offers in particular also an improved pedestrian protection (leg impact). Basic bumper design principles (Source: autosteel) In principle, aluminium can also be used for both foam and honeycomb energy absorber. Aluminium foams as well as aluminium honeycomb structures offer excellent energy absorption characteristics and have been successfully used in prototype and niche applications. But up to now, there are no known applications in larger series. As an example, Faurecia is working on modules that combine an aluminium honeycomb structure with foam or plastic energy absorbers. The weight saved is 25% to 30% compared to all-metal solutions. Another benefit is the extra space gained by reducing the vehicle's front overhang. Version 2013 © European Aluminium Association ([email protected]) 3 4.1 Aluminium extrusions for crash management systems Crashworthy aluminium structures are the result of a total systems approach taking into account the benefits achieved by specifically developed alloy qualities, design concepts and appropriate fabrication methods. Vehicle safety considerations have led to a conceptual approach where the front and rear crash management systems are part of the structural load path. Thus compliance with the supporting longitudinal beams and other vehicle components must be recognized. The impact energy is typically distributed between the following standard elements of the crash management system: The beam where the impact energy results in elastic flexure and plastic deformation. The crash boxes which absorb energy by plastic deformation. Possible hydraulic spring-damper energy absorbing units that may fully or partially recover. The attachment brackets which may or may not plastically deform, depending on the design and the specific requirements. Possible foam inclusions which absorbs energy when compressed. Furthermore a total system approach needs to take into account also the energy dissipation in vehicle rebound and tire scrub. Depending on the nature of the impact and the vehicle involved, different criteria are used to determine the crashworthiness of the structure. Today, crashworthiness is normally assessed using computer models and confirmed by experiments. There are several factors that must be considered in the design of a crash management system. The most important factor is the ability of the system to absorb sufficient crash energy to meet the OEM’s internal standard. Another important factor is the requirement to stay intact even at high-speed impacts. Weight, manufacturability and cost are also issues that must be considered during the design phase. Both initial cost and repair cost are important. The design of aluminium crash management systems is not covered in this section. For a detailed description of the design process, see the case study “Crash Management System” in the Design section of this manual. The specific characteristics of aluminium alloys offer the possibility to design cost-effective lightweight structures with high stiffness and excellent crash energy absorption potential. In principle, bumper beams can be manufactured from rolled aluminium sheet as well as aluminium extrusions. Today, 100% of the aluminium beams for crash management systems are extrusions, and more than 95% possess closed cross sections. Sheet designs exist only in niche markets. Sheet-based bumper designs were more prominent in the past when visible bumper beams were in fashion. Lightweight, polished and brightly anodized aluminium sheet and extruded bumpers could compete favourably with chrome-plated steel bumpers. Version 2013 © European Aluminium Association ([email protected]) 4 BMW 325e sedan (produced for the North American market in 1984–1987) with elongated front and rear aluminium bumpers The main reason for the preference of the aluminium extrusion technology is the design freedom (i.e. the possibility to realize multi-chamber profiles with varying wall thicknesses) and the cost-efficiency. Aluminium profiles can be reliably joined by various methods and combined with other aluminium product forms as well as with steel or other materials to form complete structural modules. Because of the low cost of the extrusion tools and the small lead times for tool manufacturing, aluminium crash management solutions are highly flexible and enable fast and simple modifications to adjust for specific crash conditions reducing both development times and costs. 4.1.1 Bumper beams Bumper systems were originally installed to protect the engine and radiator at the front of the vehicle.
Details
-
File Typepdf
-
Upload Time-
-
Content LanguagesEnglish
-
Upload UserAnonymous/Not logged-in
-
File Pages26 Page
-
File Size-