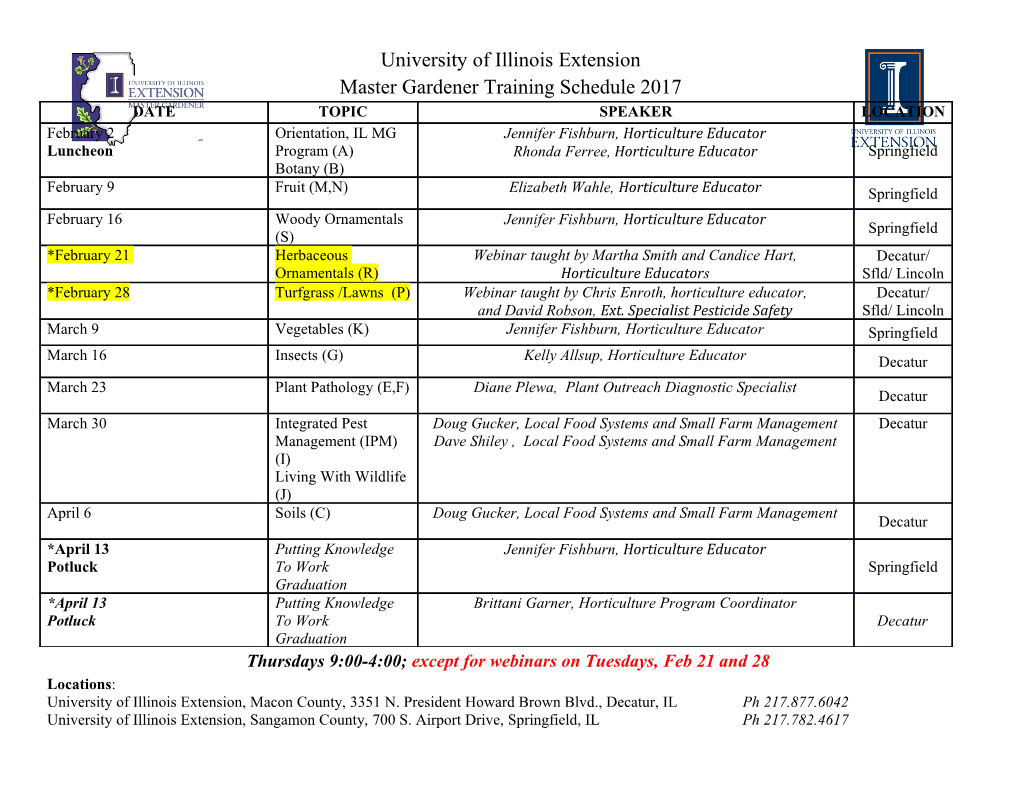
Introduction • Feasible when 1. the melting point of a metal is too high such as W, Ta, Mo POWDER METALLURGY 2. the reaction occurs when melting such as Zr and for superhard tool materials (P/M) • Powder Metallurgy (PM) (around 1800s) – Pressing – Powders are compressed into the desired shape 1. Characterization of Powder in a press-type machine using punch-and-die tooling designed specifically for the part. 2. Production of Metallic Powder – Sintering - Heating at a temperature well below melting. 3. Conventional Processing and Sintering • Advantage – Near-net shape, No waste, controlled porosity, 4. Alternative Processing Dimension control better than casting 5. Materials and Products for PM • Disadvantage 6. Design Consideration – High cost of tooling and powder, Powder Harder to handle Geometric & Size limitation, Density variation ME477 Kwon 1 ME477 Kwon 2 1. Characterization of Powders Particle Shapes and sizes • Particle Shape • P/M materials – Alloys of iron, steel, and aluminum, copper, nickel, and refractory metals such as molybdenum and tungsten and metallic carbides • Geometric feature – Particle shape • Particle Size (PS) Mesh count refers to the number of openings per – Particle size linear inch of screen. Thus, higher mesh count – Particle distribution means smaller particle size 1 PS = − t – They affects surface area, packing density, porosity, interparticle MC w friction (Flow Characteristics), Green Strength where PS = particlesize • Other Factors MC = mesh count t = wire thickness – (Chemistry and Surface Film) w πD3 A 6 • Surface Area (SA) For spherical powder, A = πD2 ; V = ; = 6 V D How do SA and PS affect the final product? ME477 Kwon 3 ME477 Kwon 4 2. Production of Metallic Gas and Water Atomization Powders Collection Chamber •Atomization Nozzle Gas – The molten metal is injected in a stream of Gas, Metal Water or Centrifugal forces (e.g. rotating disk) Siphon Powder • Chemical Reduction – Liberation of metals Molten from oxides. (Iron, Tungsten and Copper) Metal • Precipitation of metallic elements from the salts dissolved in water Molten Metal • Electrolytic: Anode made of desired metal is Water Water dissolved into the solution. Cathode collects the deposit. (Beryllium, Copper, Iron, Silver, Metal Tantalum and Titanium powder Collection Chamber ME477 Kwon 5 ME477 Kwon 6 1 Friction Packing Factor (PF) • True density • Interparticle Friction & Flow Characteristics – Friction between particles affects ability of a powder to flow – density of the true volume of the sintered material readily and pack tightly • Bulk density – A common test of interparticle friction is the angle of repose, which is the angle formed by a pile of powders as they are – density of the powders in the loose state after poured from a narrow funnel pouring – Smaller particle sizes generally – bulk density ? true density • greater friction and steeper angles Funnel • Typical PF for loose powders: 0.5 and 0.7 – Spherical shapes • the lowest interpartical friction – powders of various sizes vs. uniform size – As shape deviates from – Compaction Pressure increases packing spherical, friction between Pile of powders • Porosity (P) - Ratio of the volume of the particles tends to increase empty spaces in the powder to the bulk Angle of Repose volume. (P+PF=1) ME477 Kwon 7 ME477 Kwon 8 3. Conventional Pressing & Blending, compacting & sintering Sintering (Pressing) • Blending and Mixing – Blending – intermingling of powders – Mixing – combining powders of different chemistries – Additives – Lubricants, binders and deflocculants • Pressing (Compaction) – green compact, low density and strength • Sintering – increases strength and density – Reduction of surface energy Die – Necking, reduction of pore and grain growth • Secondary Operation – Densification & sizing, Impregnation & Infiltration, Heat Treating & Loose powder a green compact A Fully sintered part Finishing ME477 Kwon 9 ME477 Kwon 10 Sintering on a microscopic Pressure Distribution in scale Compaction po Sintering at between 70% and 90% of ⎛ πD2 ⎞ ⎛ πD2 ⎞ ⎜ ⎟ ⎜ ⎟ ⎜ ⎟ px − ⎜ ⎟()()()px + dpx − πD µσ r dx = 0 the metal's melting point (absolute scale) ⎝ 4 ⎠ ⎝ 4 ⎠ p Ddpx + 4µσ r dx = 0 Assuming σ r = kpx (interparticlefriction) dx dpx 4µkdx L = − px D p x For px = po at x = 0 −4µkx / D px = p0e (1) particle bonding is initiated at contact points; σr (2) contact points grow into "necks"; µσr D (3) the pores between particles are reduced in size; and px+dpx (4) grain boundaries develop between particles in place of x the necked regions ME477 Kwon 11 ME477 Kwon 12 2 Densification and Sizing Impregnation & Infiltration • Impregnation - when oil or other fluid is • Secondary operations to increase density, permeated into the pores of a sintered part. improve accuracy, or accomplish additional – oil-impregnated bearings, gears, and similar shaping components – Repressing - pressing the sintered part in a closed die – An alternative application is when parts are to increase density and improve properties impregnated with polymer resins to create a – Sizing - pressing a sintered part to improve pressure tight part dimensional accuracy • Infiltration - An operation in which the pores – Coining - pressworking operation on a sintered part to of the PM part are filled with a molten metal press details into its surface with a lower melting point – Machining - creates geometric features that cannot be – capillary action draws the filler into the pores achieved by pressing, such as threads, side holes, – Relatively nonporous, and more uniform density, and other details as well as improved toughness and strength ME477 Kwon 13 ME477 Kwon 14 PM Parts Classification System 4. Alternative Pressing The Metal Powder Industries Federation (MPIF) defines • Isostatic Pressing four classes of powder metallurgy part by level of difficulty – Cold Isostatic Pressing (CIP) – Hot Isostatic Pressing (HIP) • Powder Injection Molding (Metal & Ceramics) – Powder mixed with binder to form granular pellets – Pellets are heated to remove binder – Sintering and Secondary operation • Powder Rolling, Powder Extrusion (powder (a) Class I - simple thin shapes, pressed from one direction; in a container) and Powder Forging (b) Class II - simple but thicker shapes require pressing from two directions; (c) Class III - two levels of thickness, pressed from two directions; and • Hot pressing and Spark pressing (high (d) Class IV - multiple levels of thickness, pressed from two directions, electric current) with separate controls for each level • Liquid-phase sintering ME477 Kwon 15 ME477 Kwon 16 Design Guidelines Processing Capabilities • Economics usually require large quantities to justify cost of equipment and special tooling L/D= 2 (single action press) – Minimum quantities of 10,000 units are suggested L 4 (double action press) • PM is unique in its capability to fabricate parts with a controlled level of porosity (up to 50%) D • PM can make parts out of materials that would be difficult if not impossible to produce by other means x If x>L/4, high density gradient breaks the compact • The part geometry must permit ejection from die L If x<L/4, density gradient is not high enough breaks after pressing. the compact • Wall thickness should be a minimum of 1.5 mm (0.060 in) between holes or a hole and outside wall • Minimum recommended hole diameter is 1.5 mm (0.060 in) ME477 Kwon 17 ME477 Kwon 18 3 Design features for PM Features to avoid: Feasible features PROCESSING OF CERAMICS AND CERMETS 1. Traditional Ceramic Processing Punch end become fragile. 2. New Ceramic Processing 3. Cermet Processing 4. Product Design Consideration ME477 Kwon 19 ME477 Kwon 20 Introduction 1. Traditional Ceramic Processing • Processing sequence • Traditional Ceramics – Minerals in nature – Preparing powders and clay (mainly hydrous aluminum silicate). – Shaping of wet clay – Drying • New Ceramics - synthetically produced raw – Firing materials. • Preparation of Raw Materials • For traditional ceramics, powders are mixed – Comminution with water, shaped, dried and fired. • Crushing • Grinding • For new ceramics, powders are mixed with • The more water in the mixture, the easier to binders, pressed to form a green part and form. But cracking during drying and sintered into a final part. sintering. ME477 Kwon 21 ME477 Kwon 22 Processing steps Crushing Gyratory Crusher Jaw Crusher Hammer Mill ME477 Kwon 23 ME477 Kwon 24 Roll Crusher 4 Grinding Shaping, Drying & Firing Ball • Depending on the consistency in mixture (required pressure to form) – Slip (A suspension of ceramic powders in water) casting (>25%) – Plastic forming (15 to 25%) Roller Milling – Semidry pressing (10 to 15%) + + – Dry pressing (<5%) • Drying Ball Milling – First stage - rapid drying with shrinkage – Second stage – slow drying with no shrinkage • Firing – green part in a furnace call kiln • Glazing – firing second time to coat ME477 KwonImpact Grinding 25 ME477 Kwon 26 Four categories based on water Slip Casting content and pressure • A slip (a suspension of ceramic powders in water (25% to 40%)) is poured into a porous plaster of paris mold • Two principal variations: – Drain casting – Solid casting ME477 Kwon 27 ME477 Kwon 28 Plastic Forming Jiggering • 15% to 25% water • Manual and mechanized methods – Hand modeling (manual method) • Hand molding • Hand throwing (e.g.: Potter's wheel) – Jiggering (mechanized method) – Plastic pressing (mechanized method) (1) wet clay slug is placed on a convex mold; – Extrusion (mechanized method) (2) batting; and (3) a jigger tool imparts
Details
-
File Typepdf
-
Upload Time-
-
Content LanguagesEnglish
-
Upload UserAnonymous/Not logged-in
-
File Pages7 Page
-
File Size-