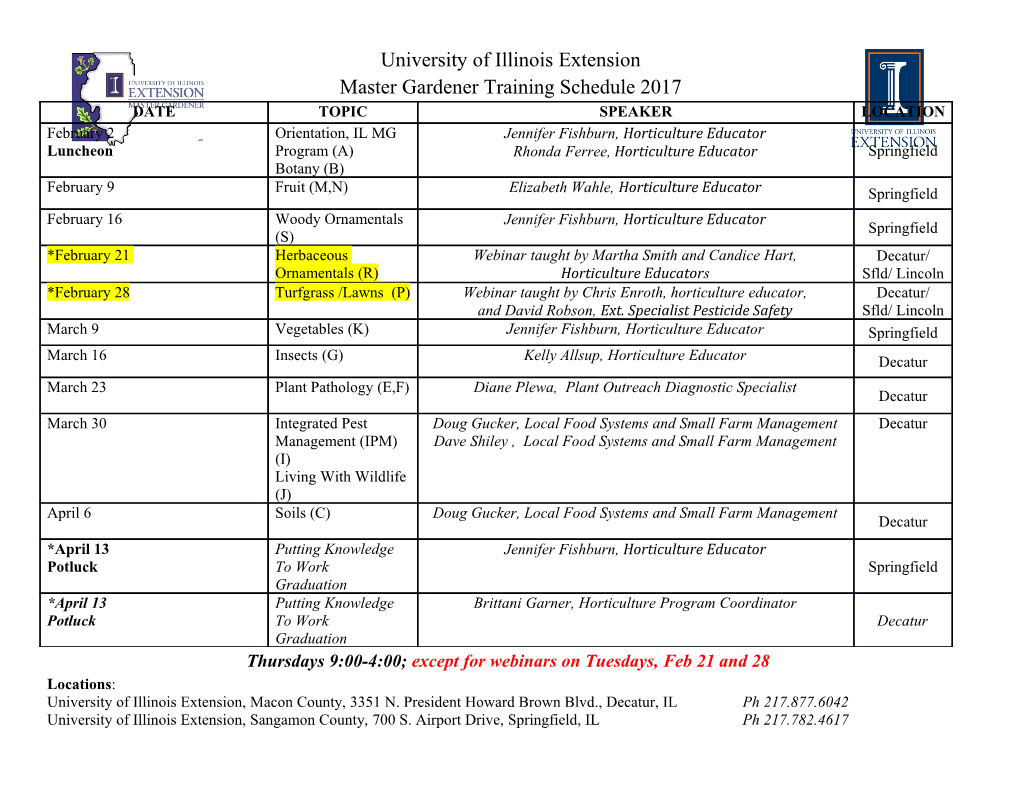
Integrating Air Systems in Aircraft Multidisciplinary Design Optimization Ali Tfaily Department of Mechanical Engineering McGill University, Montreal August 2018 A thesis submitted to McGill University in partial fulfillment of the requirements of the degree of Master of Engineering ACKNOWLEDGEMENTS I would like to thank my supervisor, Prof. Michael Kokkolaras, for his support and guidance throughout my time as his student. I am honored to have worked along a supervisor that always helped me in my work and even my personal life. I am grateful to members of Bombardier’s Advanced Product Development department for their insights on aircraft design and optimization. Special acknowledgment is given to the Thermodynamics department at Bombardier Product Development Engineering, namely Sebastien Beaulac, Hongzhi Wang, Jean-Francois Reis, and Emmanuel Germaine, who provided expertise that greatly assisted this research. I would also like to thank Jean Brousseau for sharing his knowledge on air systems design. I am very grateful to John Ferneley, Susan Liscouët-Hanke, Pat Piperni, and Fassi Kafyeke who were supportive of my career goals and provided me the means to pursue these goals. Finally, I am grateful to my friends and family for their constant support and encouragement throughout the ups and downs of my studies. ABSTRACT The strong interactions between aircraft and air systems necessitate the integration of the latter to multidisciplinary design optimization (MDO) considerations of the former. This research presents such a methodology considering environmental control and ice protection systems. These systems consume pressurized bleed air from the aircraft’s engines to perform their respective functions. We first describe the models used to predict the behavior of these systems and then propose different approaches to their integration into an existing aircraft MDO environment. A business jet test case was studied using the developed methodology. The comparison of MDO results obtained with and without the considered air systems demonstrate the impact on optimal aircraft design and confirm the importance of integrating air systems in the aircraft MDO environment in early design stages. i Table of Contents 1. INTRODUCTION ......................................................................................................... 1 2. LITERATURE REVIEW ............................................................................................... 4 3. AIR SYSTEMS MODELING ......................................................................................... 5 3.1 Architecture Assumptions ................................................................................................5 3.2 Environmental Control System Model ..............................................................................8 3.2.1 Heat Loads Calculation ________________________________________________________________ 9 3.2.2 Flow Schedule Determination __________________________________________________________ 13 3.2.3 Aircraft Ventilation Requirements ______________________________________________________ 15 3.2.4 Aircraft Air Leakage Estimation ________________________________________________________ 16 3.2.5 Depressurization Analysis _____________________________________________________________ 17 3.2.6 Air Cycle Machine Model _____________________________________________________________ 18 3.3 Wing Ice Protection System Model ................................................................................. 20 3.3.1 Ice Catch Rate Prediction _____________________________________________________________ 20 3.3.2 Ice Protection Power Requirement Model ________________________________________________ 22 3.3.3 WIPS Bleed Demand Calculation _______________________________________________________ 23 3.4 Pneumatic System Model ................................................................................................ 24 3.5 Systems Drag Prediction Models..................................................................................... 26 3.6 Systems Weight Prediction Models ................................................................................. 26 4. MDO INTEGRATION ................................................................................................. 27 4.1 Aircraft MDO Environment ........................................................................................... 27 4.2 Integrated Engine-Air Systems Model within MDO ....................................................... 30 5. ANALYSIS .................................................................................................................. 34 5.1 Sensitivity Analyses ........................................................................................................ 34 5.2 Numerical Investigation .................................................................................................. 35 5.3 Recommendations ........................................................................................................... 43 6. CONCLUSIONS AND OUTLOOK .............................................................................. 45 REFERENCES ................................................................................................................... 46 ii List of Tables Table 1: Oxygen pressure in the atmosphere at various altitudes [22]. ........................................ 15 Table 2: Comparison of optimization results with and without air systems for test case 1 .......... 37 Table 3: Comparison of optimization results with and without air systems for test case 2 .......... 39 Table 4: Comparison of optimization results of the two test cases............................................... 42 Table 5: Comparison of aerodynamic coefficients for the two test cases ..................................... 42 iii List of Figures Figure 1: Impact of different aircraft design stages on cost, maturity, ease of change in design, and configuration commitment (adapted from [4]) ........................................................................ 1 Figure 2: Typical aircraft air systems architecture showing the studied subsystems of this research (enclosed in dashed box) .................................................................................................. 5 Figure 3: Typical aircraft pneumatic system [11]. .......................................................................... 6 Figure 4: Cabin temperature control system example [11]. ............................................................ 7 Figure 5: Typical wing ice protection system [11]. ........................................................................ 8 Figure 6: Environmental control system top level design flow chart. ............................................ 9 Figure 7: Solar flux (irradiance) versus altitude [15] .................................................................... 12 Figure 8: Sample flow schedule versus altitude ........................................................................... 15 Figure 9: Fuselage air leakage rate correlation using existing aircraft test data ........................... 17 Figure 10: Example of a depressurization analysis studying aircraft and cabin pressure. ........... 18 Figure 11: Architecture of a typical air cycle machine ................................................................. 19 Figure 12: Temperature versus entropy diagram of an aircraft air cycle machine [21]. .............. 20 Figure 13: Comparison of a high fidelity ice shape prediction method (CANICE-BA) with experimental results (Experimental 1, 2) [29] .............................................................................. 21 Figure 14: Schematic showing the interaction of air systems with other disciplines within the aircraft MDO problem. ................................................................................................................. 29 Figure 15: Sequence of modules within the existing MDO environment showing the chosen sequence for the developed air systems module ........................................................................... 29 Figure 16: Mind map showing the impacts and dependencies implemented by adding air systems into the MDO environment ........................................................................................................... 31 iv Figure 17: Sensitivity of aircraft takeoff weight ........................................................................... 34 Figure 18: Sensitivity of WIPS bleed air flow rate demand in holding flight in icing conditions 35 Figure 19: Convergence history of test case 1 run with air systems modules .............................. 36 Figure 20: Comparison results of aircraft wings optimized with and without the air systems (Test case 1) ........................................................................................................................................... 38 Figure 21: Comparison results of aircraft wings optimized with and without air systems considerations (Test case 2) .......................................................................................................... 40 Figure 22: An example of a true optimum existing out of design space [7] ................................. 44 v Nomenclature Acronyms ACM Air cycle machine ECS Environmental control system FAA Federal Aviation Administration FAR Federal Aviation Regulations HP High pressure MDO Multidisciplinary design optimization WIPS Wing ice protection system Symbols
Details
-
File Typepdf
-
Upload Time-
-
Content LanguagesEnglish
-
Upload UserAnonymous/Not logged-in
-
File Pages57 Page
-
File Size-