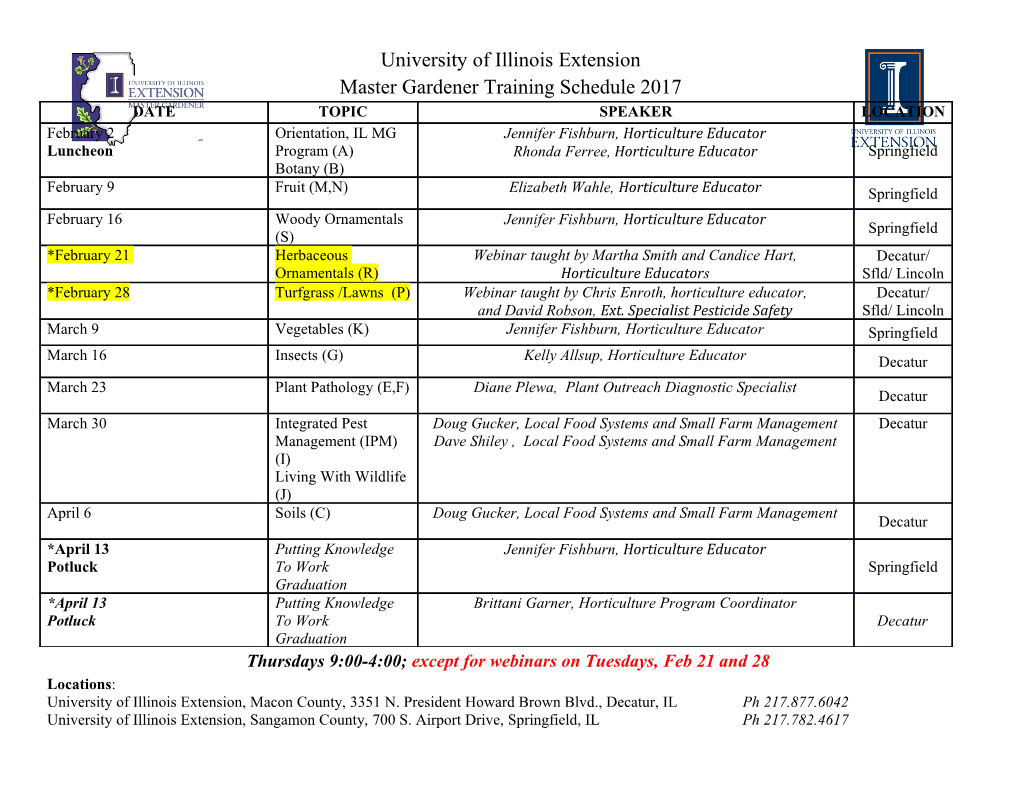
energies Article Variable Pitch Propeller for UAV-Experimental Tests Maciej Pods˛edkowski 1,*, Rafał Konopi ´nski 1, Damian Obidowski 2 and Katarzyna Koter 1 1 Institute of Machine Tools and Production Engineering, Lodz University of Technology, 90924 Łód´z,Poland; [email protected] (R.K.); [email protected] (K.K.) 2 Institute of Turbomachinery, Lodz University of Technology, 90924 Łód´z,Poland; [email protected] * Correspondence: [email protected] Received: 1 September 2020; Accepted: 3 October 2020; Published: 10 October 2020 Abstract: Growth in application fields of unmanned aerial vehicles (UAVs) and an increase in their total number are followed by higher and higher expectations imposed on improvements in UAV propulsion and energy management systems. Most commercial vertical takeoff and landing (VTOL) UAVs employ a constant pitch propeller that forces a mission execution tradeoff in the majority of cases. An alternative solution, presented here, consists of the use of a variable pitch propeller. The paper summarizes experimental measurements of the propulsion system equipped with an innovative variable pitch rotor. The investigations incorporated characteristics of the rotor for no wind conditions and a new approach to optimize pitch settings in hover flight as a function of UAV weight and energy consumption. As UAV battery capacity is always limited, efficient energy management is the only way to increase UAV mission performance. The study shows that use of a variable pitch propeller can increase the maximal takeoff weight of the aircraft and improve power efficiency in hover, especially if load varies for different missions. The maximal thrust measured was 31% higher with respect to the original blade settings. The coefficient of thrust during hover showed an increase of 2.6% up to 7.5% for various pitch angles with respect to the original fixed propeller. Keywords: UAV; variable pitch propeller; drone rotor; energy optimization; drone; experimental aerodynamics 1. Introduction Since the early 1990s, dynamic development of small unmanned flying vehicles [1] can be observed. An important issue when designing and building them is to ensure best performance, which includes flight time [2], load capacity [3], the maximal distance that the unit can cover [4] and the maximal speed [5]. Currently, great emphasis is placed on high flight parameters resulting directly from the quality of propulsion system [6] and trajectory optimization [7]. Such a system usually consists of a battery, an engine speed controller (ESC), an engine and a propeller [8]. Propellers, which are usually used, have a constant pitch due to their simple construction [9]. Consequently, such propellers are adapted to specific flight conditions [10]. Therefore, it is impossible to achieve optimal performance while changing flight conditions. A significant increase in interest in the commercial use of unmanned aerial vehicles (UAVs) for moving packages is visible [11,12]. It allows parcels to be delivered on time, even when the area is geologically unfavorable. Considering this advantage, many companies such as Amazon or DHL decided to introduce unmanned aerial vehicles into the transport industry [13]. There are also attempts to introduce small autonomous units to transport people [14]. The main priority in newly developed transport UAVs is the possibility of vertical takeoff and landing combined with a large operational range of these units. This goal requires the highest possible Energies 2020, 13, 5264; doi:10.3390/en13205264 www.mdpi.com/journal/energies Energies 2020, 13, 5264 2 of 16 efficiency from the drone propulsion system. Since the drone flies in two basic configurations, with and without load, operating conditions of UAVs in the air are significantly different. Flight conditions largely depend on the total weight of unit; therefore, the weight of load compared to the weight of drone has to be considered. To achieve optimal flight conditions, the right propeller should be selected for each configuration. However, it is practically impossible to exchange the propeller during flight. Therefore, a suitable solution would be to install mechanisms to change the rotor geometry, which would allow the propulsion system to adapt to flight conditions. Many innovative designs of the powered-lift aircraft have been presented, such as a plane airframe structure with additional engines for vertical flight [15], a tail-sitter [16–18], a tiltrotor [19,20] and a tiltwing [21]. The majority of these solutions involve the use of fixed pitch propellers. They affect the selection options of propellers, since flight of the aircraft involves at least three phases, namely, takeoff, landing and cruise flight. Although takeoff climb speed is low for powered-lifts, very high thrust during takeoff is necessary to lift up the entire aircraft with load. This requires propellers adapted to low flight speeds, i.e., those with a small pitch. For cruising flight, larger pitch propellers are demanded to maintain optimal performance. Since cruising speed can be very high, propeller selection is averaged. As a result, tradeoff must be defined; the outcome of this is a situation where the rotor does not reach its maximal speed and thrust during the start due to a high resistance torque of the propeller, and, on the other hand, the maximal speed is limited by the propeller pitch. A solution to problems with limited propeller pitch capabilities is to use variable pitch propellers. This is a direction of drone development that was once seen for flying units. At the beginning of aviation development, propellers with a fixed pitch were used to propel the aircraft, but soon it turned out to be inefficient. Therefore, mechanisms allowing the pitch of propellers to be changed began to be used. At first, a ground adjustable pitch propeller, which allows pitch to be changed only on the ground when the device is stationary, was introduced. Then, mechanisms that could change the blade wedge angle during flight were introduced. The cause of those attempts was to achieve the best flight performance, especially speed. Nowadays, the drone market is entering a similar phase of development. A technological development entails a possibility to miniaturize flying units. However, further extension of their capabilities requires optimization of flight parameters and an increase in performance. In order to adjust to this development trend, it is necessary to conduct research in the field of pitch change mechanisms adapted to small aircrafts and to analyze available propellers in terms of their applicability and performance. Experimental and numerical studies were carried out on fixed pitch propellers for UAVs [22,23]. The research included examination of propeller parameters in stationary air [24] and in the wind tunnel [25,26], where the characteristics of propeller work during flight were examined. The research also concerned noise generated by propellers [27] and propeller behavior in crosswinds [28]. Rotors with variable pitch blades, intended for drones, were tested for helicopters [29–31], but there are still no data for small rotors for small unmanned fixed-wing or multi-rotor drones. The main reason for this is that on the market there are no readily available mechanisms that allow for a change of the blade pitch in an effective way. However, there are mechanisms adapted to small units [32–34]. These systems are primarily designed for elastic propellers with a diameter of about 10 inches and are not suitable for use in industry where a high load capacity is required. In addition, variable pitch propellers are used in flight control of quadrotor drones instead of controlling engine speed [35]. Mathematical models of variable pitch propellers, characterized by different levels of complexity, to calculate thrust and torque in particular, were investigated in [36]. A possible method to control motors in order to reduce drag was developed based on those models. The models were experimentally tested on a symmetrical airfoil blade propeller and one of them fits best the experimental data for this specific solution. Energies 2020, 13, 5264 3 of 16 Energies 2020, 13, x FOR PEER REVIEW 3 of 15 Currently, commercially available unmanned aerial vehicles solutions based on fixed pitch propellersdemand. A are solution not always that can su ffisignificantlyciently efficient; increase therefore, the capabilities they are of not drones able tois meetto use global rotors market with a demand.variable pitch A solution mechanism. that can A significantlypropulsion system increase equipped the capabilities with a ofmechanism drones is tochanging use rotors the with rotor a variableblade pitch pitch angle mechanism. can increase A propulsion hovering system thrust. equipped This mechanism with a mechanism is especially changing devoted the rotorto vertical blade pitchtakeoff angle and can landing increase (VTOL) hovering systems, thrust. where This mechanism takeoff and is landing especially require devoted high to verticalthrust. takeoIt is worthff and landingmentioning (VTOL) that systems, the time where of these takeo operationsff and landing is usually require much high thrust.shorter It compared is worth mentioning to the time that of the timeentire of flight. these Thus, operations after istakeoff, usually it muchis necessary shorter to compared adjust the to pitch the timeof the of blades the entire to the flight. flight Thus, speed after in takeoorderff to, it maximize is necessary efficiency. to adjust the pitch of the blades to the flight speed in order to maximize efficiency. The present present paper paper presents presents test test results results of a of modified, a modified, commercially commercially available available Fluxer Fluxer16 × 6 16 6 propeller. A novelty of the solution, with respect to current UAV power and thrust control propeller.× A novelty of the solution, with respect to current UAV power and thrust control systems, systems,lies in a possibility lies in a possibility to control to variable control variablepitch to increase pitch to increaseefficiency effi ofciency the hovering of the hovering propulsion propulsion system systemand to andproduce to produce large largethrust.
Details
-
File Typepdf
-
Upload Time-
-
Content LanguagesEnglish
-
Upload UserAnonymous/Not logged-in
-
File Pages16 Page
-
File Size-