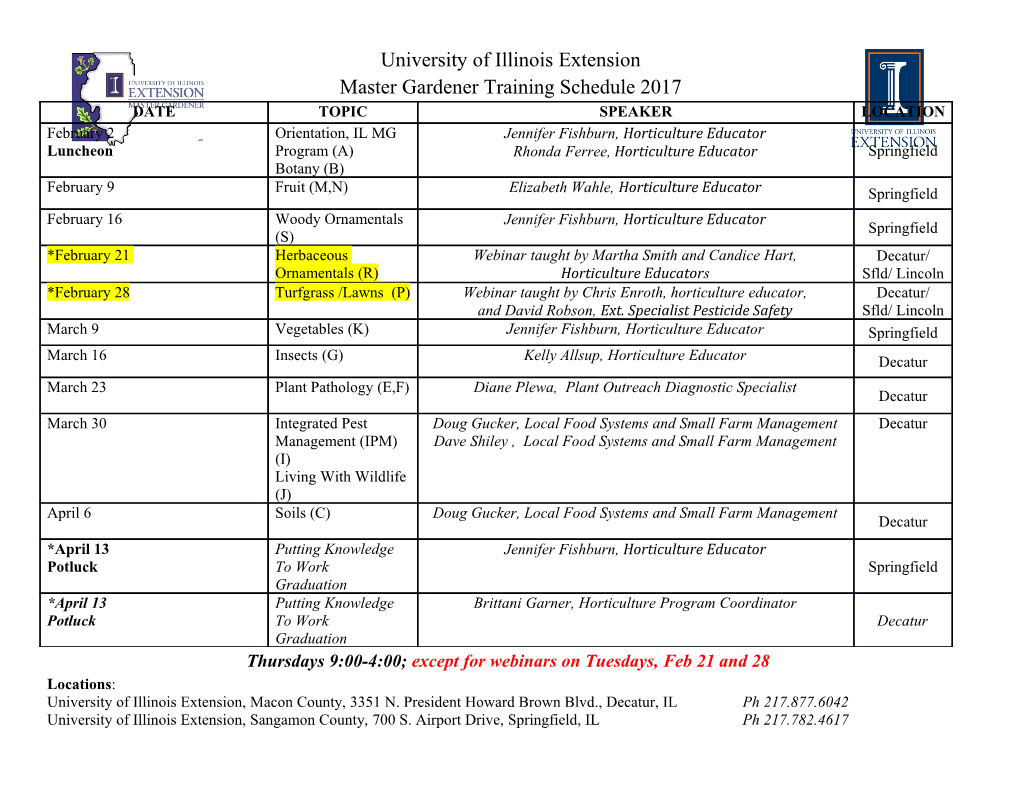
ADNS-2620 Optical Mouse Sensor Data Sheet Description Features The ADNS-2620 is a new entry level, small form factor • Precise optical navigation technology optical mouse sensor. It is used to implement a non- • Small form factor mechanical tracking engine for computer mice. Unlike (10 mm x 12.5 mm footprint) its predecessor, this new optical mouse sensor allows for • No mechanical moving parts more compact and affordable optical mice designs. • Complete 2D motion sensor It is based on optical navigation technology, which mea- • Common interface for general purpose controller sures changes in position by optically acquiring sequential surface images (frames) and mathematically determining • Smooth surface navigation the direction and magnitude of movement. • Programmable frame speed up to 3000 frames per sec (fps) The sensor is housed in an 8-pin staggered dual inline package (DIP). It is designed for use with the • Accurate motion up to 12 ips HDNS-2100 Lens, HLMP-ED80-xx000, and the • 400 cpi resolution HDNS-2200 LED Clip, providing an optical mouse solu- • High reliability tion that is compact and affordable. There are no moving • High speed motion detector parts, so precision optical alignment is not required, thereby facilitating high volume assembly. • Wave solderable • Single 5.0 volt power supply The output format is a two wire serial port. The current X and Y information are available in registers accessed via • Conforms to USB suspend mode specifications the serial port. • Power conservation mode during times of no move- ment Resolution is 400 counts per inch (cpi) with rates of motion up to 12 inches per second (ips). • Serial port registers – Programming Theory of Operation – Data transfer The ADNS-2620 is based on Optical Navigation • 8-pin staggered dual inline package (DIP) Technology. It contains an Image Acquisition System (IAS), a Digital Signal Processor (DSP) and a two wire Applications serial port. • Mice for desktop PC’s, workstations, and portable PC’s The IAS acquires microscopic surface images via the lens and illumination system provided by the • Trackballs HDNS-2100, HDNS-2200, and HLMP-ED80-xx000. These • Integrated input devices images are processed by the DSP to determine the direc- tion and distance of motion. Pinout of ADNS-2620 Optical Mouse Sensor Pin Number Pin Description 4 SCK 1 OSC_IN Oscillator input LED_CNTL 5 3 SDIO 2 OSC_OUT Oscillator output GND 6 3 SDIO Serial Port Data (input and output) 2 OSC_OUT VDD 7 4 SCK Serial Port Clock (Input) 1 OSC_IN REFA A2620 XYYWWZ 5 LED_CNTL Digital Shutter Signal Out 8 6 GND System Ground Figure 1. Mechanical drawing: top view. 7 VDD 5V DC Input 8 REFA Internal reference Figure 2. Package outline drawing. CAUTION: It is advisable that normal static precautions should be taken in the handling and assembly of this component to prevent damage and/or degradation which may be induced by ESD. Overview of Optical Mouse Sensor Assembly 32.46 1.278 (Top view) NOTE: Pin 1 of optical mouse sensor should be inserted into the reference point of mechanical cutouts. +X Figures 3 and 4 are shown with HDNS-2100, HDNS-2200 19.10 and HLMP-ED80-xx000. +Y 0.752 Avago Technologies provides an IGES file drawing de- scribing the base plate molding features for lens and PCB alignment. BASE PLATE The components shown in Figure 5 interlock as they are Dimensions in mm/in. mounted onto defined features on the base plate. ESD LENS RING (Side view) PLASTIC SPRING The ADNS-2620 sensor is designed for mounting on a CLIP through hole PCB, looking down. There is an aperture stop and features on the package that align to the lens. 14.58 10.58 13.82 7.45 0.574 0.417 0.544 The HDNS-2100 lens provides optics for the imaging of 0.293 the surface as well as illumination of the surface at the optimum angle. Features on the lens align it to the sensor, PCB SENSOR BASE PLATE ALIGNMENT POST base plate, and clip with the LED. The lens also has a large round flange to provide a long creepage path for any ESD Figure 4. 2D assembly drawing of ADNS-2620 shown with the HLMP-ED80 events that occur at the opening of the base plate. (top and side view). The HDNS-2200 clip holds the LED in relation to the lens. The LED’s leads must be formed first before inserting into HDNS-2200 (Clip) the clip. Then, both LED and clip is loaded on the PCB. The HLMP-ED80-xx000 clip interlocks the sensor to the lens, and through the lens to the alignment features on the base plate. ADNS-2620 (Sensor) Customer supplied PCB The HLMP-ED80-xx000 is recommended for illumination. If used with the bin table (as shown in Figure 8), sufficient HDNS-2100 (Lens) illumination can be guaranteed. Customer supplied base plate with recommended alignment 28.00 features per IGES drawing 1.102 18.94 0.746 9.06 0.357 Clear Zone 1.00 0.039 φ 3.50 0.138 Figure 5. Exploded view drawing. SCK OSC_IN SERIAL SERIAL 12.60 13.73 OSCILLATOR RESONATOR 11.10 PORT PORT 0.496 0 0.541 SDIO OSC_OUT 0.437 4.91 7.45 1.35 0.293 1.25 0.053 0.193 0.049 IMAGE VOLTAGE REFA 29.15 PROCESSOR REFERENCE 1.148 MM TOR ALL DIMENSIONS 0 INCH 8X φ 0.80 0.031 AGE REGULA VDD Figure 3. Recommended PCB mechanical cutouts and spacing. T 5 VOLT VOL AND POWER CONTROL POWER GND LED LED CONTROL CONTROL Figure 6. Block diagram of ADNS-2620 optical mouse sensor. PCB Assembly Considerations Design Considerations for Improving ESD Performance 1. Insert the sensor and all other electrical components The flange on the lens has been designed to increase into PCB. Note: Pin 1 of the sensor should always be the creepage and clearance distance for electrostatic the reference point of mechanical cutouts. discharge. The table below shows typical values assum- 2. Bend the LED leads 90° and then insert the LED into ing base plate construction per the Avago supplied IGES the assembly clip until the snap feature locks the LED file and HDNS-2100 lens flange. base. Typical Distance Millimeters 3. Insert the LED/clip assembly into PCB. Creepage 16.0 4. Wave solder the entire assembly in a no-wash solder Clearance 2.1 process utilizing solder fixture. The solder fixture is needed to protect the sensor during the solder process. The fixture should be designed to expose For improved ESD performance, the lens flange can be the sensor leads to solder while shielding the optical sealed (i.e. glued) to the base plate. Note that the lens aperture from direct solder contact. The solder fixture material is polycarbonate and therefore, cyanoacrylate is also used to set the reference height of the sensor based adhesives or other adhesives that may damage the to the PCB top during wave soldering (Note: DO NOT lens should NOT be used. remove the kapton tape during wave soldering). 5. Place the lens onto the base plate. 6. Remove the protective kapton tape from optical aperture of the sensor. Care must be taken to keep contaminants from entering the aperture. It is recom- mended not to place the PCB facing up during the entire mouse assembly process. The PCB should be held vertically for the kapton removal process. 7. Insert PCB assembly over the lens onto the base plate aligning post to retain PCB assembly. The sensor ap- erture ring should self-align to the lens. 8. The optical position reference for the PCB is set by the base plate and lens. Note that the PCB motion due to button presses must be minimized to maintain optical alignment. 9. Install mouse top case. There MUST be a feature in the top case to press down onto the clip to ensure all components are interlocked to the correct vertical height. Sensor Clip PCB LED Lens/Light Pipe Base Plate Surface Figure 7. Sectional view of PCB assembly highlighting optical mouse components (optical mouse sensor, clip, lens, LED, PCB and base plate). R1 4.7 µF 0.1 µF HDNS 0.1 µF 7 2100 100K ohms 11 Lens VDD Internal VDD Image HLMP-ED80-xx000 7 Sensor VDD Vpp 13 SURFACE D+ D+ 6 1K ohms GND 5 12 LED_CNTL 2N3906 D- D- 1.3 K 8 17 3 GND Vreg P0.5 SDIO 5 16 1 Ceramic Resonaator GND QA P1.0 P0.6 ADNS-2620 OSC_IN SHLD 14 15 4 24 MHz VDD VDD QB P1.1 P0.7 SCK 2 OSC_OUT CYPRESS 4 Murata CSALS24M0X53-B0 P0.3 L CY7C63723C-PC TDK FCR24.0M2G R 8 3 REFA P0.2 M 2.2 µF 1 2 P0.0 P0.1 R Z LED HLMP-ED80 R1 VALUE Buttons Bin (Ohms) 6 K 32.0 VSS L 32.0 M 32.0 N 32.0 XTALOUT XTALIN P 32.0 to 61.2 10 9 Q 32.0 to 73.9 R 32.0 to 84.4 S 32.0 to 103 T 32.0 to 130 6 MHz (Optional) Figure 8. Circuit block diagram for a typical corded optical mouse using an Avago ADNS-2620 optical mouse sensor. Notes on Bypass Capacitors Regulatory Requirements • Caps for pins 6,7 and 8 to ground MUST have trace • Passes FCC B and worldwide analogous emission limits lengths LESS than 5 mm. when assembled into a mouse with unshielded cable • The 0.1 uF caps must be ceramic. and following Avago recommendations. • Caps should have less than 5 nH of self inductance • Passes EN61000-4-4/IEC801-4 EFTB tests when assem- • Caps should have less than 0.2 ohms ESR bled into a mouse with shielded cable and following • Surface mount parts are recommended Avago recommendations.
Details
-
File Typepdf
-
Upload Time-
-
Content LanguagesEnglish
-
Upload UserAnonymous/Not logged-in
-
File Pages27 Page
-
File Size-