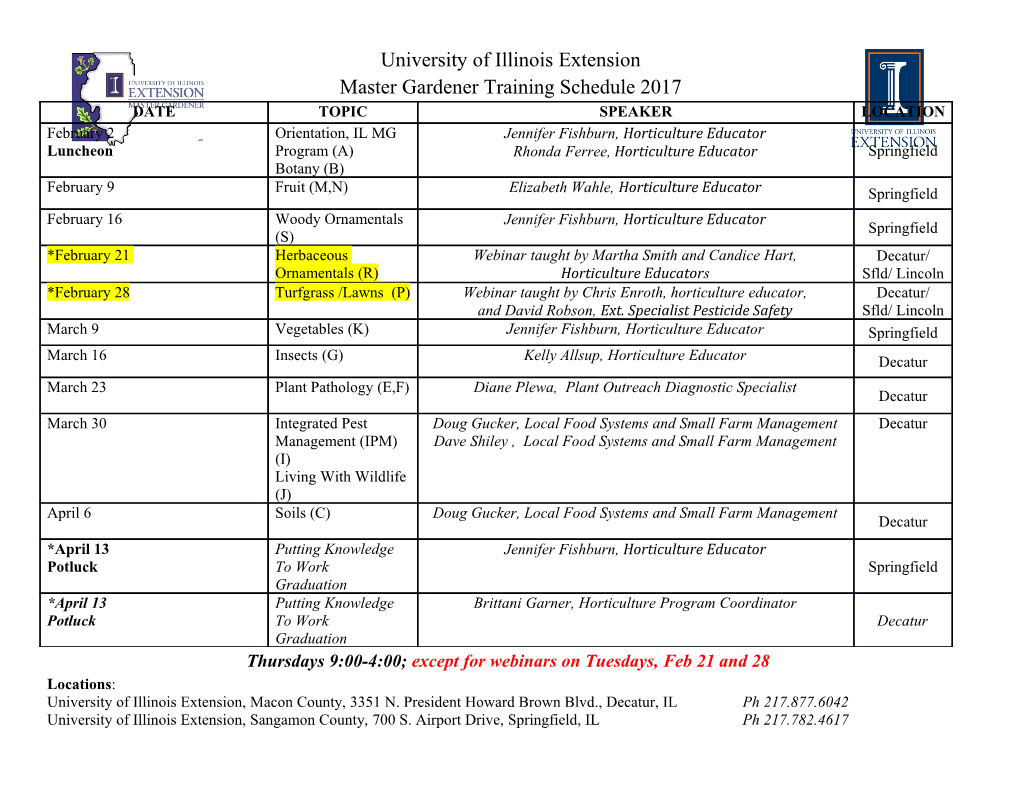
energies Article On the Use of Infrared Thermography and Acousto—Ultrasonics NDT Techniques for y Ceramic-Coated Sandwich Structures Yuxia Duan 1, Hai Zhang 2,* , Stefano Sfarra 3 , Nicolas P. Avdelidis 2, Theodoros H. Loutas 4, George Sotiriadis 4, Vassilis Kostopoulos 4, Henrique Fernandes 5,6 , Florian Ion Petrescu 7, Clemente Ibarra-Castanedo 2 and Xavier P.V. Maldague 2 1 School of Physics and Electronics, Central South University, Changsha 410083, China 2 Computer Vision and Systems Laboratory, Department of Electrical and Computer Engineering, Laval University, Quebec City, QC G1V 0A6, Canada 3 Department of Industrial and Information Engineering and Economics, University of L’Aquila, I-67100 L’Aquila, Italy 4 Department of Mechanical & Aeronautical Engineering, University of Patras, 26504 Rio Achaia, Greece 5 School of Computer Science, Federal University of Uberlandia, Uberlandia 38408-100, Brazil 6 Fraunhofer Institute for Nondestructive Testing, Campus E3 1, 66123 Saarbrücken, Germany 7 Bucharest Polytechnic University, 060042 Bucharest, Romania * Correspondence: [email protected] This paper is an extended version of paper which published in the 10th ECNDT, Moscow, Russia, y 7–11 June 2010. Received: 5 December 2018; Accepted: 20 June 2019; Published: 1 July 2019 Abstract: Ceramic-coated materials used in different engineering sectors are the focus of world-wide interest and have generated a need for inspection techniques that detect very small structural anomalies. Non-destructive testing is increasingly being used to evaluate coating thickness and to test for coating flaws. The main pros of non-destructive testing is that the tested object remains intact and available for continued use afterward. This paper reports on an integrated, non-destructive testing approach that combines infrared thermography and acousto-ultrasonics to evaluate advanced aerospace sandwich structure materials with the aim of exploring any potential for detecting defects of more than one type. Combined, these two techniques successfully detected fabrication defects, including inclusions and material loss. Keywords: non-destructive testing; infrared thermography; acousto-ultrasonics; ceramic coatings; sandwich structure 1. Introduction The interest towards the application of ceramic coatings above all into the aerospace section grows year by year; consequently, techniques which are able to detect small defects must be more sophisticated [1]. The manufacture of ceramic materials is very complex also because they are not limited to the aerospace section, but they have the opportunity to be applied in many advanced engineering applications [2–6]. Insulation properties spelt out in the thermal barrier factor hold bright prospects [7]. A major drawback, is that they catastrophically fail upon reaching critical stress limits, and manufacturing processes or in-service conditions may introduce flaws [8]. Coating functions must be well understood in order to examine or determine its qualities. Decorative or ornamental coatings must meet different requirements to protect against wear and temperature [9]. As described in [10], numerous factors are important to determining coating qualities. Energies 2019, 12, 2537; doi:10.3390/en12132537 www.mdpi.com/journal/energies Energies 2019, 12, 2537 2 of 12 Non-destructive testing (NDT) is coming into wide use to determine coating thickness and detect coating flaws. Its primary advantage is that the object tested remains intact after testing and can continue in service [11]. “Flaws” change the properties of the component and may arise both during the manufacture and operation stages. This happens more and more for components subjected to high-stress, such as those in the aerospace sector. These require a pronounced safety standard, which can be linked to NDI (inspection) and NDE (evaluation) reasons. The present paper proposes a technique that offers advantages for a smart detection and subsequent evaluation of damages caused during operation, while meeting prerequisites for the understanding of component failures and/or lifetimes [12]. Defects in sandwich materials may arise during the same steps above-mentioned for ceramic coatings [13]. Sandwich structures made in composite materials are usually realized by two thin and relatively stiff skins having the lightweight property; in the middle, there is a thick (called core material) that normally has the low strength property. Greater thicknesses, greater bending stiffness and overall low density are at the basis of sandwich composites. Concerning structural applications, sandwich materials are characterized by high stiffness, fatigue resistance, and lightness which provide an increased uniformity in terms of mechanical properties [14,15]. In the present case under analysis, the alumina component has been used as “coating” function, by simulating, e.g„ the AETB-8 material (Alumina Enhanced Thermal Barrier). It is important to remark that by adding Al2O3 into the component, the main thermal properties increase; in addition, the weight remains practically the same, as well as the resistance. [16]. An adhesive tape was placed between the sandwich structure and the alumina tile in order to fix them each other. Due to the complexity of material structure and bonding process in production, several types of defects that affect the load carrying capacity may occur during the manufacturing process, such as void, inclusion, and disbonding. A kissing bond is a special type of disbond, which is crucial in terms of structural integrity as they can deteriorate due to in-service loading or environmental conditions [17–19]. Detecting a kissing bond is a challenge because there is no air pocket or void that can be detected thanks to pulsed thermography (PT) and acousto-ultrasonics (AU) techniques. The defect detection in this study involved scratch, inclusion, and material loss, which may be caused by high-speed impact in-service. The test analyzed the complex structure by using the above-mentioned NDT techniques. The purpose was to identify every possible defect using an integrated approach. Both the sandwich structure in carbon fiber reinforced plastic (CFRP) and the alumina tile are presently in common use in the aerospace industry and were provided by the Thales Alenia Space Company. It is well-known that space structures are strongly subjected to sudden fluctuations of ambient conditions, therefore, safe operation requires that damage must be recognized quickly to prevent catastrophic component failure [20]. NDT techniques may help a lot to guarantee the structural integrity. Early imperfection detection in materials and construction is critical. Component diversity and complexity demand skills in several complementary inspection methods [21–25]. Thermographic tests are increasingly important in composite material inspections. On the one hand, these tests have a lot of pros, although a number of technical problems limit their use. These limitations are now being overcome [26–33]. On the other hand, AU technique, which is based on digital signal processing and pattern recognition algorithms, is able to characterize the defects detected in the component under inspection. This manuscript reports on a proposed integrated testing approach using both IRT and AU for complex sandwich structures manufactured on the basis of advanced aerospace materials. It explores their potential in detecting various defects. 2. Sandwich Structure Sample Construction and General Characteristics The sample used in this study is 102 mm 102 mm 7 mm and is illustrated in Figure1. × × The materials composing the sample are a honeycomb core made by carbon fibers which is located in Energies 2019, 12, x FOR PEER REVIEW 3 of 13 This manuscript reports on a proposed integrated testing approach using both IRT and AU for complex sandwich structures manufactured on the basis of advanced aerospace materials. It explores their potential in detecting various defects. 2. Sandwich Structure Sample Construction and General Characteristics Energies 2019, 12, 2537 3 of 12 The sample used in this study is 102 mm × 102 mm × 7 mm and is illustrated in Figure 1. The materials composing the sample are a honeycomb core made by carbon fibers which is located in the themiddle middle between between two two 6 mm-thick 6 mm-thick CFRP CFRP layers layers (0, (0, 90 90).). This This component component was was linked linked to aa 11 mm-thickmm-thick alumina ceramic plate through a double-sided adhesive tape. A 3MTM Scotch-WeldTM structural alumina ceramic plate through a double-sided adhesive tape. A 3MTM Scotch-WeldTM structural adhesiveadhesive filmfilm AFAF 191191 waswas usedused intointo thethe entireentire component.component. TheThe samplesample corecore waswas piercedpierced fromfrom sideside 1.1. TheseThese are are hole hole defects defects A A and and C (FigureC (Figure1b,c), 1b,c), although although they they seem seem to be to cylindrical be cylindrical defects defects looking looking at side at 1.side This 1. isThis caused is caused by the by fact the that fact the that materials the materi usedals for used the for inclusions the inclusions are very are elastic very andelastic they and adapt they ' theadapt shape the toshape the cells to the present cells present on the sideson the of sides the sample. of the sample. Both holes Both were holes diameter were diameter ( = 5 mm), (φ = length5 mm), (Llength= 70 mm),(L = 70 and mm), depth and (z =depth0.5 mm). (z = The0.5 holesmm). wereThe realizedholes were by usingrealized
Details
-
File Typepdf
-
Upload Time-
-
Content LanguagesEnglish
-
Upload UserAnonymous/Not logged-in
-
File Pages12 Page
-
File Size-