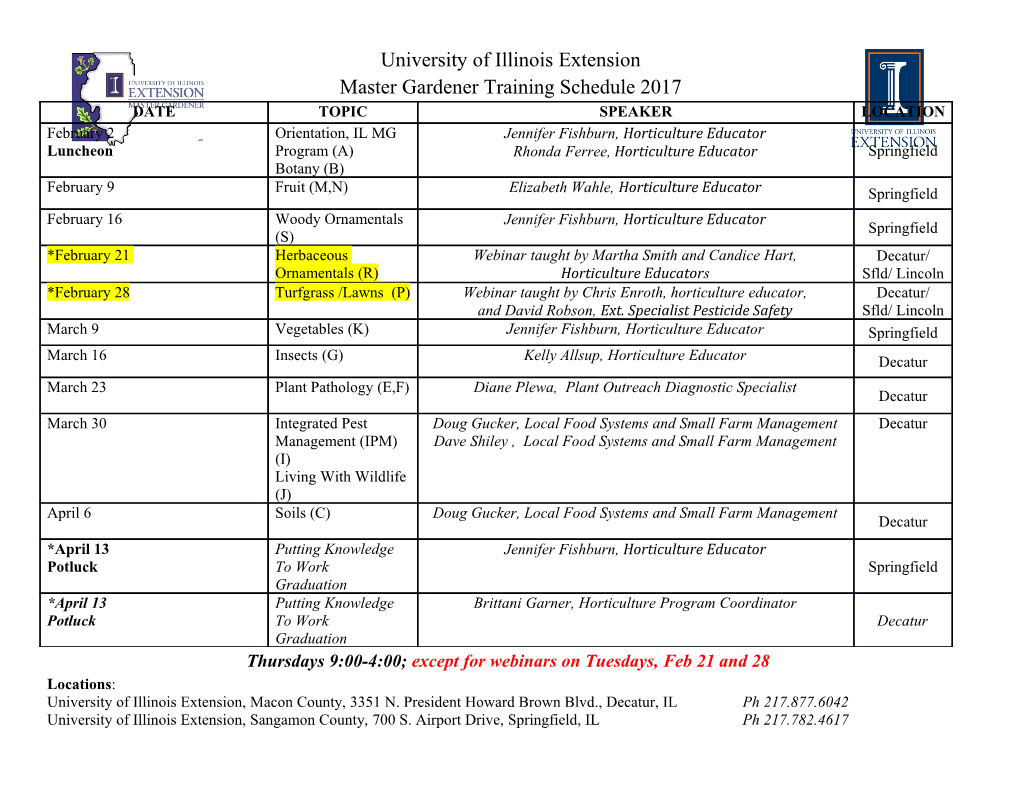
CHINESE JOURNAL OF MECHANICAL ENGINEERING Vol. 28,aNo. 2,a2015 ·285· DOI: 10.3901/CJME.2015.0106.006, available online at www.springerlink.com; www.cjmenet.com; www.cjme.com.cn Generalized Internal Model Robust Control for Active Front Steering Intervention WU Jian1, 2, ZHAO Youqun1, *, JI Xuewu3, LIU Yahui3, and ZHANG Lipeng2 1 College of Energy and Power Engineering, Nanjing University of Aeronautics and Astronautics, Nanjing 210016, China 2 School of Mechanical and Automotive Engineering, Liaocheng University, Liaocheng 252059, China 3 State Key Laboratory of Automotive Safety and Energy, Tsinghua University, Beijing 100084, China Received January 6, 2014; revised October 9, 2014; accepted January 6, 2015 Abstract: Because of the tire nonlinearity and vehicle’s parameters’ uncertainties, robust control methods based on the worst cases, such as H∞, μ synthesis, have been widely used in active front steering control, however, in order to guarantee the stability of active front steering system (AFS) controller, the robust control is at the cost of performance so that the robust controller is a little conservative and has low performance for AFS control. In this paper, a generalized internal model robust control (GIMC) that can overcome the contradiction between performance and stability is used in the AFS control. In GIMC, the Youla parameterization is used in an improved way. And GIMC controller includes two sections: a high performance controller designed for the nominal vehicle model and a robust controller compensating the vehicle parameters’ uncertainties and some external disturbances. Simulations of double lane change (DLC) maneuver and that of braking on split-μ road are conducted to compare the performance and stability of the GIMC control, the nominal performance PID controller and the H∞ controller. Simulation results show that the high nominal performance PID controller will be unstable under some extreme situations because of large vehicle’s parameters variations, H∞ controller is conservative so that the performance is a little low, and only the GIMC controller overcomes the contradiction between performance and robustness, which can both ensure the stability of the AFS controller and guarantee the high performance of the AFS controller. Therefore, the GIMC method proposed for AFS can overcome some disadvantages of control methods used by current AFS system, that is, can solve the instability of PID or LQP control methods and the low performance of the standard H∞ controller. Keywords: active front steering system, generalized internal model robust control, H∞ optimization, PID, split-μ road disturbances. And MPC system will also become unstable 1 Introduction when the constraints are violated by emergency disturbances or cornering stiffness variation, moreover Active front steering system (AFS) as an active safety MPC method requires online optimization. IMC is only system can improve vehicle’s handling and safety even in applicable to a stable controlled plant, in addition it is extreme situations and thus avoid accidents. Considering always combined with other control methods to overcome the strong nonlinearity and uncertainty in vehicle motion, the shortcomings. the control methods for AFS have been a key issue. For the reasons mentioned above, the robust control [1−2] ORABY, et al , presented an AFS control scheme based on the worst cases, such as H∞, μ-synthesis, etc, have based on optimal control theory. LI, et al[3], presented a PID been widely used in active front steering. DU, et al[8], plus fuzzy logic controller for vehicle dynamics control. A presented a robust yaw-moment controller design for model predictive control (MPC) scheme was applied to the improving vehicle handling and stability with vehicle dynamics control[4]. MEN, et al[5], proposed internal considerations of model uncertainties and control saturation. model control (IMC) based on combined brake and active ZHENG, et al[9], proposed a method to achieve the robust front steering for vehicle stability control. LI, et al[6−7], decoupling of the lateral and yaw motion. YOU, et al[10], researched parameter estimation techniques to make the put forward a two degree of freedom control system based control method adapt to different driving conditions. on H∞ loop-shaping control for automatic steering. To PID control and optimal control as high performance reduce the external uncertainties and disturbances, controller are simple and practical, but have very little nonlinear H∞ control theory with L2 gain performance was robustness against the model uncertainties and external applied in the vehicle dynamics control[11]. Linear fractional transformations (LFT) based on feedforward and feedback * Corresponding author. E-mail: [email protected] H control for vehicle handling improvement was Supported by National Natural Science Foundation of China(Grant Nos. ∞ [12] [13] 11072106, 51375009) presented . ESKI, et al , presented a neural © Chinese Mechanical Engineering Society and Springer-Verlag Berlin Heidelberg 2015 ·286· Y WU Jian, et al: Generalized Internal Model Robust Control for Active Front Steering Intervention network-based robust control system design for the active mass moment of inertia about the rotation axis, Ix is the roll steering system. moment of inertia (about vehicle x-axis), Ixz is the roll-yaw The robust control methods used in the above situations product of inertia, Iy is the pitch moment of inertia (about have achieved relatively good results, but still have some vehicle y-axis), Iz is the yaw moment of inertia (about problems to be solved. As everyone knows, a contradiction vehicle z-axis), Qu is the general force along vehicle x-axis, between performance and stability exists in the robust Qy is the general force along vehicle y-axis, Qr is the control, therefore a trade-off between performance and general force for yaw motion, Q is the general force for stability against disturbances and parameters’ variations roll motion of roll part, ω is the wheel rotation speed. must be made. Unfortunately, the robust controller design is usually at the cost of performance, so that the robust controller is always conservative because most robust control design methods are based on the worst possible case. In this paper, a generalized internal model robust control (GIMC) that can overcome the contradiction between performance and stability is used in the AFS control. The Youla parameterization is used by GIMC in an improved way[14‒15]. GIMC controller includes two sections: a high performance controller designed for the nominal vehicle model and a robust controller. The high performance controller will solely work when there is no model uncertainties and external disturbances, while the robust controller will be active only when there are model uncertainties or external disturbances. This paper is arranged as follows. The second section introduces the nonlinear vehicle model, the tire model and driver model. The third section describes the GIMC robust method for AFS. In the fourth section, the simulation results of the several control strategies are shown, and a comparison is made among these control strategies. Finally, conclusions are drawn in the fifth section. Fig. 1. A full vehicle model 2 Vehicle and Driver Models The equations of motion are as follows: The simulation models of the vehicle, tire and driver are presented in this section to evaluate GIMC control method. ïì ïmu()-- rv mh (2), r + r = Qu ï ïmv() +- ru mh ( - r2 ), = Q 2.1 Vehicle model ï v [16] ï It is shown in Fig. 1 that is an eight-DOF nonlinear ï íIrzzrxz+--()(), I I mh u -= rv Q r (1) vehicle model including the four wheels rotational, yaw, ï ï 2 ï()()(),I xzrxz++++-mh mh v ru I I r longitudinal, lateral, and roll motions. Meanings of the ï ï 22 variables and the parameters in Fig. 1 and in Eqs. (1) and (2) ï-+-+- = îï ()().mh Iyz I r C mgh Q are given in the latter part of this section. In Fig. 1, a is the horizontal distance between vehicle CG and front axle, b is And the general forces are given by the following horizontal distance between vehicle CG and rear axle, tw equations: is the wheel track, u is the longitudinal velocity, V is the velocity vector, v is the lateral velocity, β is the tire side slip ìQF=-+cos( ) F sin( ) F , ï uxf yf xr angle, r is the yaw rate, δ is the mean steering angle of front ï ïQF=-+sin( ) F cos( ) F , ï vxf yf yr wheels, K is the total roll damping, m is the total vehicle ï ïQaF=+-+sin( ) aF cos( ) bF mass, m is the mass of roll part, is the roll angle around ï rxfyf yr í (2) ï roll axis of vehicle, μ is the nominal tire-road friction ï tFwxflxfr[(---+ F )cos( ) ( Fyflyfr F )sin( ) ï coefficient, C is the total roll stiffness, Fx is the ï ()]/2,FF- ï xrl xrr longitudinal force in x-axis, Fy is the lateral force in y-axis, ï ïQK=- . Fz is the vertical force on tire, h is the CG height of total îï vehicle mass with regards to ground, h is the CG height of roll part (m) with regards to roll axis, Iw is the wheel total Parameters of vehicle model are shown in Table 1. CHINESE JOURNAL OF MECHANICAL ENGINEERING ·287· Table 1. Parameters of vehicle model driver-vehicle system block can be presented as shown in Parameter Value Fig. 3. Where, f(s) is the road input, y(s) is the lateral m/kg 1230 displacement response, V(s) is the vehicle’s transfer m/kg 1010 function, T is the driver preview time, TaTc (, ) is the a/m 1.0 correction time, Td is neural lag time, Th is operation b/m 1.35 * lag time, C0 is the correction parameter, y is ideal tw/m 1.49 * −1 lateral acceleration, sw is the ideal steering wheel angle, Cf/(N • m • (°) ) 1580.4 −1 is actual steering wheel angle.
Details
-
File Typepdf
-
Upload Time-
-
Content LanguagesEnglish
-
Upload UserAnonymous/Not logged-in
-
File Pages9 Page
-
File Size-