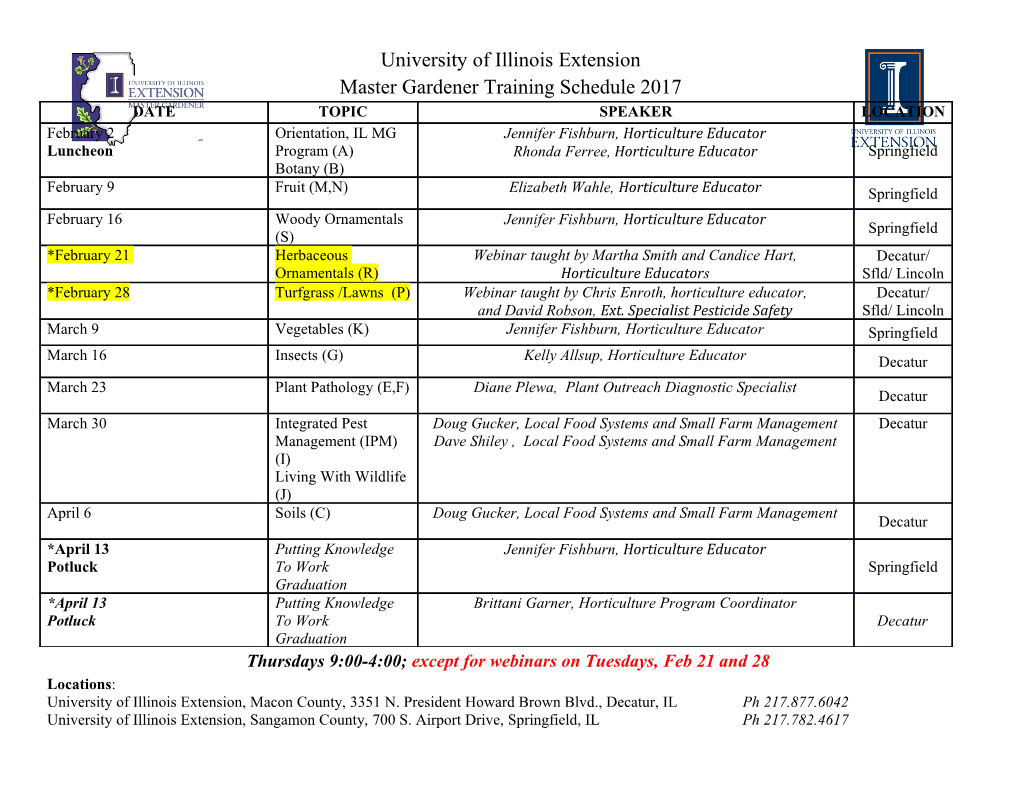
The Mathematics of Pumping Water AECOM Design Build Civil, Mechanical Engineering Please observe the conversion of units in calculations throughout this exemplar. INTRODUCTION Water is pumped from the reservoir into a In any pumping system, the role of the pump is to receiving tank. This kind of arrangement is used provide sufficient pressure to overcome the to lift water from a reservoir, or river, into a water operating pressure of the system to move fluid at treatment works for treatment before the water a required flow rate. The operating pressure of goes into the supply network. The water level in the system is a function of the flow through the the reservoir varies but the discharge level in the system and the arrangement of the system in receiving tanks remains constant as the water is terms of the pipe length, fittings, pipe size, the discharged from a point above the water level. The pump is required to pass forward a flow of change in liquid elevation, pressure on the liquid 3 surface, etc. To achieve a required flow through a 2500 m /hr to the receiving tank. pumping system, we need to calculate what the The operating pressure of a pumped system is operating pressure of the system will be to select calculated in the SI unit of meters (m). To a suitable pump. maintain dimensional consistency, any pressure values used within the calculations are therefore converted from kPa into m using the following conversion; 1 kPa = 0.102 m (as measured by a water filed U tube manometer) For the above system, the operating pressure or the total system head, HTo tal , is defined as: HTo tal = H s + H D + (P RT - PRES ) … (1) where, H s = Static head (m) H D = Dynamic head (m) Pressure on the surface of the water in P = RT the receiving tank (m) Pressure on the surface of the water in P = RES the reservoir (m) Although the atmospheric pressure changes with Figure 1: Typical Vertical Turbine Water Pumps height, the change in pressure that occurs over MATHEMATICAL MODEL AND CALCULATIONS the pumping height is often so small that it can be Consider the pumping arrangement shown in considered negligible. In this exemplar, the Figure 2 below: change in pressure over the elevation from the reservoir to the receiving tank is not that significant and hence is negligible, i.e., PRT - PRES » 0 . Therefore, equation (1) becomes: HTo tal = H s + H D … (2) The static head H s is the physical change in elevation between the surface of the reservoir and the point of discharge into the receiving tank. As the water level in the reservoir can vary, the static head for the system will vary between a maximum Figure 2: Pumping Arrangement and a minimum value: H = discharge level - reservoir T WL reservoir to the receiving tank. Values can be S min obtained from standard tables and a total K and fittings value can be calculated by adding all the K H = discharge level - reservoir BW L fittings S max values for each individual fitting within the system. where The following table shows the calculation of TWL = Top Water Level (reservoir) K fittings for the system under consideration: BWL = Bottom Water Level (reservoir) No. of K Item Fitting Items fittings If the discharge point is at a level of 110.5 m Items Value Total above the mean sea level (also known as Above Pipe Entrance Ordnance Datum (AOD) in technical language) 1 0.05 0.05 and the reservoir level varies between 105.2 m (bellmouth) AOD and 101.6 m AOD, then: 90 o Bend 10 0.75 7.5 H = 110 .5 - 105 .2 = 5 .3 m (short radius) S min 45 o Bend H S = 110 .5 - 101 .6 = 8 .9 m 2 0.3 0.6 max (short radius) As a result of the variation in the static head, the Butterfly Valve total system head, H , will also have a 2 0.3 0.6 Total (Fully Open) maximum and minimum value which we need to Non Return calculate here. 1 1.00 1.00 Valve The dynamic head is generated as a result of friction within the system. The dynamic head is Bellmouth Outlet 1 0.2 0.2 calculated using the basic Darcy Weisbach Total K fittings equation given by: 9.95 Value 2 Kv Table 1: Calculating K for the system under H D = … (3) fittings 2 g consideration where Hence, the total K fittings for the system under K = loss coefficient consideration is 9.95. v = velocity in the pipe (m/sec) K pipe is associated with the straight lengths of g = acceleration due to gravity (m/sec 2 ) pipe used within the system and is defined as: We can calculate the velocity in pipe using the fL following formula: K = … (6) pipe D Q v = … (4) A where where f = friction coefficient 3 = pipe length (m) Q = flow rate through the pipe (m /sec) L D = pipe diameter (m) A = pipe cross sectional area (CSA) (m 2 ) The friction coefficient f can be found using a If Q is 2500 m 3 /hr and the flow is pumped modified version of the Colebrook White equation: through a 0.8 m diameter pipe then: 0 . 25 2 2 f = … (7) pD p ´ 0 . 8 2 A = = = 0 . 5 m 2 é ì k 5 . 74 ü ù 4 4 êl ogí + 0 . 9 ý ú î 3 . 7 ´ D Re þ Hence, using equation (4), we get: ë û where 25000 1 v = ´ = 1 .3 9 m/sec 3600 0 .5 k = Roughness factor (m) The loss coefficient K is made up of two Re = Reynolds number elements: The pipe roughness factor k is a standard value K = K + K … (5) obtained from standard tables and is based upon fittings pipe the material of the pipe, including any internal coatings, and the internal condition of the pipeline K fittings is associated with the fittings used in the i.e. good, normal or poor. pipeworks of the system to pump the water from Reynolds number is a dimensionless quantity use a variable speed pump by adjusting the pump associated with the smoothness of flow of a fluid speed we can control the flow to the receiving and relating to the energy absorbed within the tank to 2500 m 3 /hr over the entire head range. fluid as it moves. For any flow in pipe, Reynolds PUMP SELECTION number can be calculated using the following formula: By repeating the calculation for H D for a range of vD flows we can generate a pair of system curves Re = … (8) that define the relationship between head and u flow for the top and bottom water conditions. where These curves define the envelope of the pumping u = Kinematic viscosity (m 2 /s) system. If the total pipe length is 250 m, the pipe has a A pump has been selected from manufacturer’s roughness factor of 0.3 mm and the kinematic details that can achieve the required flow at the BWL at a speed of 675 rpm. The characteristic viscosity of water is -6 m 2 /sec, then from 1 . 31´ 10 hydraulic curve for the selected pump has been equation (8), we get: overlaid onto the system curves (see Figure­3 on 1 .3 9 ´ 0 .8 the next page) and the effect of running the pump Re = = 8 .4 9 ´ 10 5 1 .3 1 ´ 10 - 6 at this speed but at the TWL can be seen. The Intersection of the TWL and BWL System Curves Using this value in equation (7), we get: with the Speed Curves define the Pump’s 0 . 25 maximum and minimum operating speeds. In this f = 2 instance, the pump would run to the right hand é ì 0 . 0003 5 . 74 ü ù end of its hydraulic curve possibly causing ê ï ï ú logí + 0 . 9 ý cavitations. ê ï 3 . 7 ´ 0 . 8 8 . 49 ´ 10 5 ï ú ë î ( ) þ û The pump speed needs to be reduced in order to = 0 . 0165 achieve the required flow at the TWL and the required speed can be calculated using the Using this value in equation (6), we get: affinity laws: 0 .0 165 ´ 250 First affinity law – Flow is proportional to the K pipe = = 5 .1 6 0 .8 shaft speed, i.e., Finally, using equation (5), the total K value for Q1 N 1 the system is: = … (9) Q 2 N 2 K = 5 .1 6 + 9 . 95 = 15 .1 1 where We can now calculate the dynamic head using 3 equation (3) as follows: Q = Flow through the pipe (m /sec) N = Shaft speed (rpm) 15. 11´ (1 . 39 )2 H D = = 1 . 49 m Second affinity law – Head is proportional to the 2 ´ 9 . 81 square of the shaft speed, i.e., The dynamic head is the same for both the H (N )2 maximum and minimum static head conditions as 1 = 1 … (10) the dynamic head is independent of the system 2 H 2 (N 2 ) elevation. where Hence, the maximum and minimum total head values for the system at a flow of 2500 m 3 /hr can H = Head (m) now be calculated using equation (2): Using an iterative process of adjusting the pump speed and calculating the resultant flow and head H = 8 .9 + 1 .4 9 = 10 .3 9 m Total max using the above laws, we can determine the H = 5 .3 + 1 .4 9 = 6 .7 9 m required speed of the pump for the TWL Total min condition.
Details
-
File Typepdf
-
Upload Time-
-
Content LanguagesEnglish
-
Upload UserAnonymous/Not logged-in
-
File Pages9 Page
-
File Size-