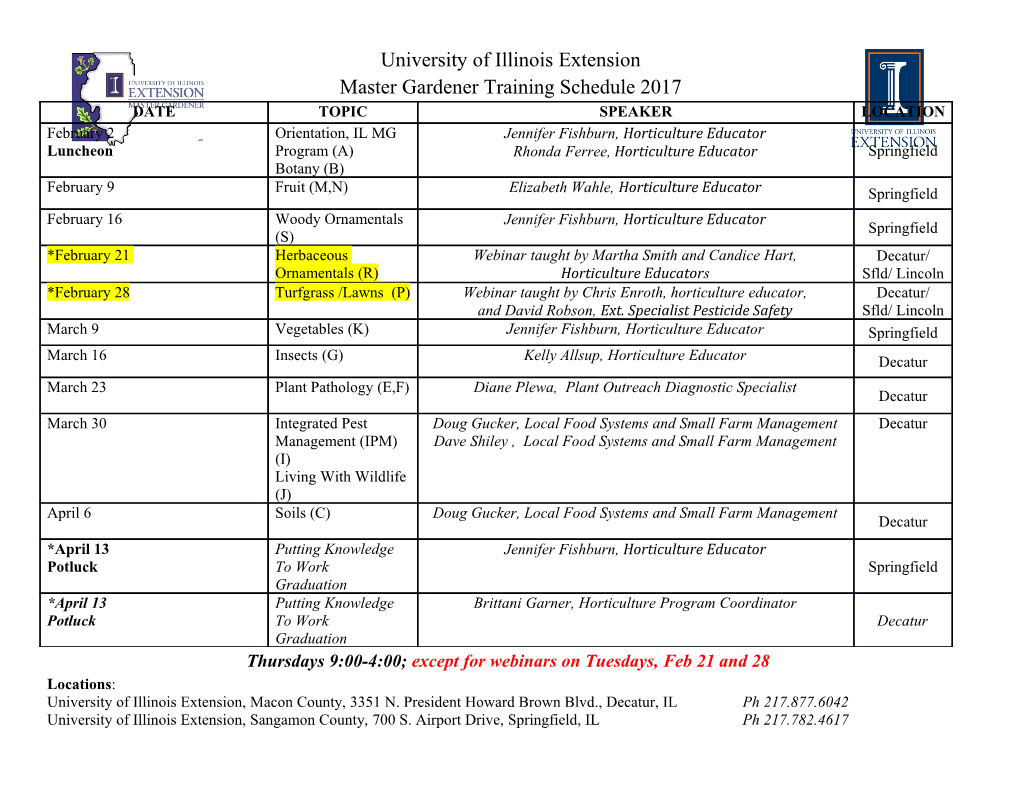
GER-4219 g GE Power Systems IGCC Gas Turbines for Refinery Applications Robert M. Jones Norman Z. Shilling GE Power Systems Schenectady, NY 12345 IGCC Gas Turbines for Refinery Applications Contents Abstract. 1 Introduction . 1 IGCC Refinery Experience. 3 Gas Turbine Advancements . 6 Fuel Flexibility . 7 Environmental Performance. 11 GE IGCC Gas Turbine Product Line . 13 Economic Considerations. 15 Conclusion . 15 List of Figures. 16 GE Power Systems I GER-4219 I (05/03) i GE Power Systems I GER-4219 I (05/03) ii IGCC Gas Turbines for Refinery Applications Abstract deal with a wide range of solid and liquid fuels has been demonstrated in refinery applications Integrated Gasification Combined Cycle fueled by heavy oil and petroleum coke (IGCC) plant designs are successfully operating residues—integrated with systems providing and meeting challenging service requirements both power generation and chemical co-pro- at several world-class refinery locations around duction. Current gas turbine combustion con- the globe. Advancements in gasification, air trol systems provide for full or combined “co-fir- separation, syngas cleanup, and gas turbine ing” of synthesis gas with natural gas or distillate combined cycle equipment designs have con- back-up fuels. tributed to continuous improvements in system performance and operating characteristics. To date, GE gas turbines have accumulated These improvements enhance the prospect for more than 499,000 fired hours on synthesis fuel continued growth in the IGCC refinery seg- gas (of which 132,000 hours were fired on syn- ment. Today's challenge for IGCC systems is to gas derived from refinery feedstocks). This meet market requirements (which demand broad experience—enabled in large part by lower capital costs, improved operating reliabil- developments in gas turbine technology— ity, and increased fuel flexibility) in combina- serves as a superb entitlement for environmen- tion with increasing efficiency and environmen- tally superior value generation from poor quali- tal performance standards. ty, low cost opportunity fuels. This paper focuses on improvements in gas tur- Improvements in gas turbine performance on bine technology that contributed to the com- low heating value syngas fuels have enhanced mercialization and leadership of IGCC systems the economics of IGCC systems to where it is a for the clean conversion of refinery residues clear choice for new power generation at and solid wastes to economical “poly-genera- refineries. GE has a total of ten IGCC projects tion” of power and other high valued by-prod- that have gone into syngas operations, with five ucts used by the refiner. more plants either beginning or planned for Environmental performance is a key bench- operation within the next four to five years. mark for contemporary IGCC plant design. Nine of these fifteen plants are associated with IGCC’s high marks in environmental perform- refinery operations. GE continues to invest in ance stem from both the fundamental charac- turbine product development efforts allowing teristics of the process and advances in gas tur- for increased performance benefits with liquid bine technology. The early breed of commercial and solid fuel IGCC projects. IGCC refinery projects (at Texaco El Dorado and Shell Pernis) still achieve performance in Introduction criteria pollutants that are better than that of Integrated Gasification Combined Cycle many direct-combustion technologies. IGCC’s (IGCC) systems are receiving increased recog- viability is ensured by its capability to meet nition as flexible, environmentally superior tighter emissions standards for criteria pollu- solutions for the conversion of solid and heavy tants including NOx, SOx, and particulates. liquid feedstock to power, co-generation steam, Fuel flexibility provides a hedge against poten- and other chemical production purposes. The tial excursions in both fuel cost and availability. capability of IGCC systems to use opportunity The robustness of gasification technology to fuels to produce high value co-products along GE Power Systems I GER-4219 I (05/03) 1 IGCC Gas Turbines for Refinery Applications with power generation enhances the economic U.S. refiners continues to reflect increasing sul- viability of new projects. The co-production of fur content and decreasing quality as more chemicals and other utility products required diversified supplies come to market. (See by refineries is a key advantage afforded by Figure 1.) At the same time there is an increas- IGCC technology. By fully utilizing the capabil- ing demand for middle distillates. The incre- ities of modern combined cycle designs, IGCC mental capital cost to refiners to meet these systems are able to achieve exceptional levels of requirements is projected to be more than $8 environmental performance, availability, and billion, which figures to add $0.06 per gallon to efficiency at a competitive cost of electricity. current fuel pump prices nationwide. Similarly, With the production of conventional syngas the hydro-treatment needed to increase light fuel components, the opportunity exists to fur- petroleum production requires hydrogen from ther separate carbon elements prior to combus- the expansion of coking facilities. The net effect is an increase in petroleum coke produc- tion and sequester CO2 when necessary. Improvements in advanced gas turbine tech- tion coming from U.S. refining, which is either nologies—allowing for increased power densi- stockpiled or marketed for export. Given ties, improved cycle efficiencies, and lower increased worldwide environmental awareness, installed costs—will continue to enhance IGCC combined with a general acceptance of the systems to provide increased benefits and capa- Kyoto agreements, there is a shrinking global bilities to refineries for the foreseeable future. market available for petroleum coke. The environmental legislation proposed in the The logical solution for refiners is to utilize pet U.S. to reduce sulfur content in transportation coke on site as a ready fuel source for the bene- fuels from >250 ppm to <15 ppm by the year ficial production of power and/or steam prod- 2006 has many refiners facing costly process ucts. The qualifying technologies suitable for design changes. The crude slate available to providing this energy conversion are quickly RefineryRefinery Segment Segment 1.3 Higher Sulfur Residuals Sulfur Content 1.2 Favor IGCC 1.1 • Transportation fuel Sulfur will change from >250 ppm to <15 ppm by '06 1.0 1987 1989 1991 1993 1995 1997 1999 Increased Petroleum Coke 32.5 Production Crude Quality 32.0 • Increasing demand for middle distillates • Hydrogen from expansion of coking 31.5 facilities and IRCC API Gravity31.0 Wt % Sulfur 30.5 Kyoto & Enviro Shrinking 1988 1989 1990 1991 1992 1993 1994 1995 1996 1997 1998 1999 SPENDING SPENDING $B Market for Pet Coke Ref. & Mktg. Env'tl Base 8 6 7 ROIC 6 5 • Pet coke stockpiled or handled by 5 4 4 middlemen for blending to saleable fuel 3 3 2 2 • Several countries are restricting new 1 1 0 coking capacity or import pending 0 -1 environmental solutions '92 '93 '94 '95 '96 '97 '98 '99 '00 '01 '02 '03 '04 '05 '06 Figure 1. Refinery drivers GE Power Systems I GER-4219 I (05/03) 2 IGCC Gas Turbines for Refinery Applications reduced to IGCC and CFBC (Circulating owner to form an optimized design that meets Fluidized Bed Combustion), owing to strict demanding process and environmental require- environmental emissions standards. A technol- ments. Figure 3 shows the five major technolo- ogy assessment illustrating comparative source gies contributing to this design: volume reduction, air emissions, and annual I Gasification island disposal costs is shown in Figure 2. IGCC tech- I Gas treatment nology clearly provides significant environmen- I tal advantages for air emissions and lower dis- Air separation posal costs albeit at higher initial capital invest- I Combined-cycle power block ment. When operating costs, flexibility for co- I Integration production, and collateral environmental costs Typically for existing refinery applications, are factored into the financial analysis, IGCC IGCC plants provide a number of useful by- can provide improved project net present value. products which contribute to the economic via- This paper discusses the features, capabilities, bility of the overall integrated facility. These and experience of gas turbines applied to IGCC products can include power, steam, and hydro- systems designed for efficient conversion of gen—depending upon project specific needs. refinery waste liquid and solid petroleum There have been five refinery-based IGCC proj- residues to useful energy products. ects using GE-designed gas turbines that have gone into commercial operation during the IGCC Refinery Experience past six years. (See Figure 4.) Included among An IGCC plant is the product of collaboration these are two petroleum coke refineries between major subsystem providers and the (Texaco El Dorado and Motiva Enterprises) and SourceSource Volume Volume Reduction Reduction AirAir Emissions Emissions IGCC IGCC vs. CFBCCFBC Solids Volume Production by Power Generation Technologies Air Emissions of IGCC vs. Fluidized Bed Power Generation Using Petroleum Coke 0.6 0.45 0.51 0.5 0.40 0.35 0.4 0.36 0.30 CFBC 0.3 0.25 IGCC 0.20 0.2 0.15 Source: Black & Veatch Pritchard Pounds per Million Btu’s 0.10 0.1 Pounds per Million Btu's 0.06 Cubic meter of solids/metric ton feed 0.05 0 0.00 CFB FGD IGCC SO2 NOx CO Particulates Annual Disposal Costs Net Annual Solid Waste
Details
-
File Typepdf
-
Upload Time-
-
Content LanguagesEnglish
-
Upload UserAnonymous/Not logged-in
-
File Pages20 Page
-
File Size-