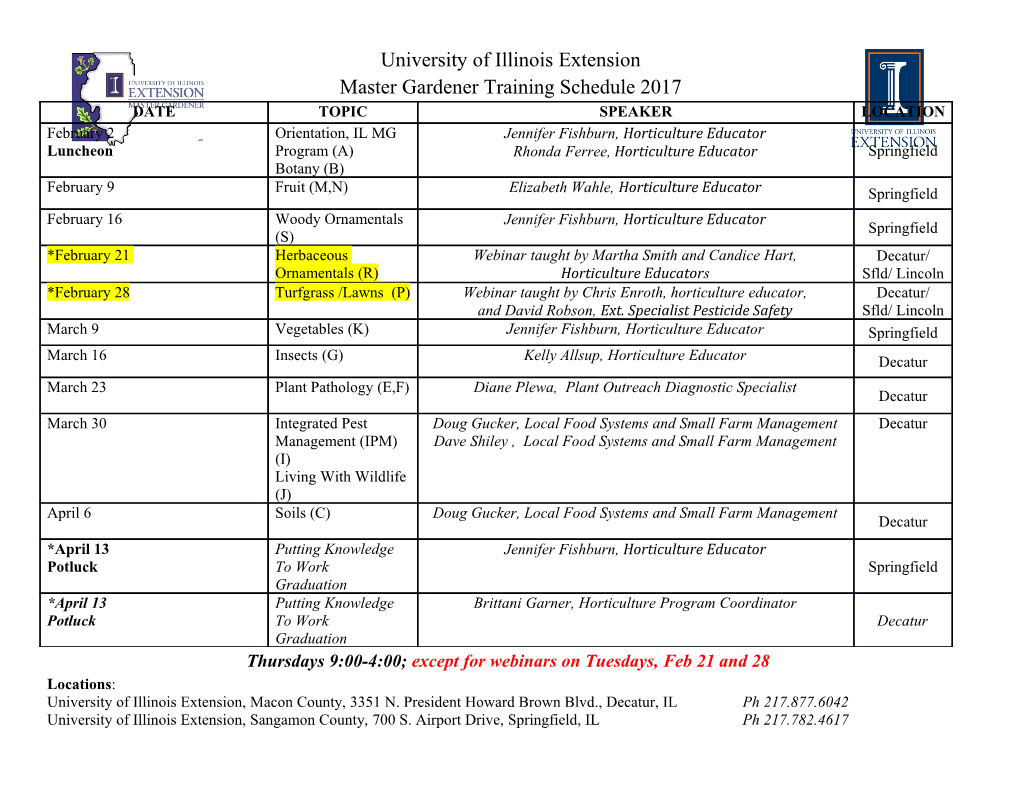
CHARACTERIZATION OFBLOOMERY SLAGS Morphology, composition and furnace operation Arne Espelund ABSTRACT Nobody has been able to reproduce the successful ironmaking, in the way it was achieved during the Roman iron age and the Middle ages. On the basis of mainly the morphology of bloomery slags from the rich finds from about year 200 BC to 1800AD in Mid- Norway,combined withmetallurgical reasoning and written documents from the 18ncen- tury, certain alternative models for the operation of the furnaces are presented. These agree well with the viewpresent"d by Dr L. Beck in 1891 on eady ironmaking among the Germanic people. Introduction The blast furnace slag is composed mainly of gangue material with certain additions, in order to enhance reducibility at moderate temperatures and fluidity at Slag is a waste product with little aesthetic value. It characteristic the has no direct connection with subjects like the hi- the conditions, which are for hearth. Steelmaking slags are composed mainly of story of art or religion. It is thus frequently disre- material added the furnace, together with certain garded or misinterpreted when found during archae- to elements from the melal, transformed into oxides ological excavations. However, it can provide im- poriant information about the smelting process, during refining. Some essential features are shown above all in bloomery ironmaking. A characteristic in table 1. X-ray pattem of solid slag with free FeO and FerSiOo Table L. Typical features of modern slags. is shown in figure 1. Blast furnace Steelmaking In the bloomery process, iron is made in shaft or slag slag hearth furnaces. Reduction at a high temperature is achieved while the necessary heat is generated by a Range of oxygen pressure 10.' 10'' - 10'' combustion process the same reactor. The metal in Main function:. removal ofgangue controlled must be acceptable for the blacksmith. This requires in liquid state oxidation, a minimum size of each piece of metal, the correct dissolution analysis in terms of Vo C,little impurities such as S of impurities inclusions. us thus % FeO <t% - t0% and P, and no harmful slag Let 'R6le" 'passive" 'active' consider a shaft furnace, where solid ore and the reducing agent are added from the top while air is blown into the furnace near the bottom. Evidently a Based upon the metallurgy ofthe process, I claim that a normal bloomery slag is an active slag, while it also is a medium for the countercurrent motion with heat exchange takes removal ofgangue in the ore. place. Liquid slag is tapped while the meial is re- moved as a solid lump, a bloom. The standard approach in extractive metallurgy is 1) to evaluate equilibria at an estimated temperature, The slag from this process can be compared with representative for the hearth of the furnace 2) to two other types: blast furnace slags and steelmaking make a corresponding heat balance, in order to .r/ags, whose origin and function are better known: evaluate the true process temperature 3) to find out 135 ^ I Sorple; 902?89 BRILESET SLAG File: 90ae89.RD 07-SEP-90 1ts:39 x10 r e. B0 1 .60 1.eE 8.88 0.4CI 18. E 40.0 30.0 40.0 50.0 60.0 100.0 FEYALITE 88.0 e8-1 1 39 60.8 48.0 40.8 18. B 40.8 30. g 40.0 59.0 60. E 180.0 SiOA OUARTZ LOU 80.8 33-1 1 61 68.0 40.0 40.0 1 ts.0 e0. 0 38. E 48. B 50.0 6CI. 0 108.8 g UUESTITE 80. 6- 615 68.0 40 .8 40.0 1 0.9 eB.0 30.0 40.8 50.0 68.0 Fig 1. X-ray patterns. about the prior history and thus the composition of metal with practically no carbon dissolved present. the phases entering the reaction zone. The full calculation is "iterative". However, temperatures in the range 700 - 900"C are much too low for proper sintering of metal particles The equilibria to a bloom and the decantation of slag. If the tem- perature is increased to the normal melting point of The product of the bloomery process is iron with a a bloomery slag, say 115OC, the metal will dissolve carbon content near 0 %. T\erc are four phases an excessive amount of carbon'. present in the bottom of the furnace: solid metal, liquid slag, carbon and gas. At such temperatures, the low carbon content can only be obtained if it is controlled by a relatively In figure 2 a-c the four phases present in the bottom oxidizing gas or a Fe0-rich slag, requiring a non- of a blast furnace and in two situations in bloomery equilibrium situation carbon - slag and/or carbon - furnaces with their corresponding analyses are gas. A gas will vary in composition and have a very shown. The blast furnace is operating near equilibri- low buffer capacity, giving a scatter in metal analy- um in the hearth: The slag contains less than 1% ses. Howewer, a sufficient quantity of slag containing FeO while the metal is near carbon-saturation at "free" FeO can result in a reliable meial analysis'. about 4% C. In the bloomery process, however, the lowcarbon content of the metallic phase can onlybe The only bloomery process, for which we have obtained by an equilibrium at temperatures below written information from the 18" century, cleady 90OC, rendering cu - iron, (fig 3). There is an invari- tells that a certain amount of FeO-rich slag had to be ant point near 700'C with FeO at unit activity, a gas present (Evenstad 1782, Rinman 1794). As will be mixture of C0 and C0, near l:l,pure carbon and a shown later, this is supported by archaeological finds 136 a. Blastfurnaca b. Bloomeryfurnace c. Bloomery furnaca Reactions in the shafi - 1500c - 900t " 11508 a. Equiljbrla In b. Equlllbrla c. Only partial the hBarth equllbrla A successful extraction and separation of slag from the metal in the bloomery process is dependent on i!3,J'"--] [_il5å,|il; a gradual reduction of Fer03 to lower oxides and me- f-; t--ilj-m; co' N' sras (r) I Ccj. r.r-isiå"-----l-,.r"7r"o1 föö; | I I tal in the shaft. This reduction is taking place as long (coJ'lsio,(s)'ii-iF'öi;i-l- I I | | loozreo I as the ore has maintained its great surface area, characteristic for a precipitated oxide. This is the principle of "reduction before melting'.If the oppo- site takes place, ie sintering or fusion of the ore at four phases in ironmaking. a) the hearth of the blast Fig 2.The a low temperature, prior to reduction, the reactivity firrnace. b) possible equilibria in the bloomery furnace below 900"C.c) partial equilibria near 1150"C. is greatly reduced. Little or no metal is achieved. This in turn may lead to a high liquidus temperature for the slag. Even at 120CPC the slag will contain also solid FerOo, and no proper separation occurs. The actual finds In Mid-Norway,alarge number of bloomeries have been reported during the last 10 years. They are situated near the tree line and are mostly in a well preserved condition. raC analysishas placed the three methods between 200 BC - 600 AD (I), 700 - 1300 I AD (ID and 1400- 18504D (IID (Espelund 1988). I I The furnaces are outlined in figure 4. I o Without doubt, the technology of period I is the most striking. At a normal site from eg 2OO AD four furnaces are placed in a regular pattern next to each -:!.",,,),'r"7, other along a terrace facing a river. The slag heap in (,,,,,'/i front of every furnace conlains about 10 tons of slag. ,,rf':)rt Some hundred sites have been registered, with a ,/ )' 4o' ,,/ possible total of at least 5000 tons of slag. It is likely ,"' t"' ,"' that a total amount of 20 000 tons of slag and 10 000 o o o./ö o.o o,. o tons of metal was produced during this period. A characteristic site is shown figure 5. 7 8 9 t0 il ll tJ in lotlf . The sites from the next periods are less spectacular, Fig 3. Equilibria in the system Fe-C-O as a function of 1/T@o- - slag - senqvist 1974). with individual furnaces, heaps in the range I 10 tons and no striking topographical feature. As re- and experimental work. There is a certain similarity ported finds they are definitely underrepresented. with the Catalan process (Åkerman 1844). The heat balance The slag from period I will be discussed in detail: The adiabatic temperature is highly influenced by Slag pieces are found in all sizes with one dimension the C0r/C0 ratio created by the combustion of car- not exceeding about 40 cm. Visual examination of bon. If equilibrium is prevailing when excess carbon the surface shows a large number of cavities with the burns in air, a gas mixture containing C0 and N, is grain structure of wood, at other sites the cavities created, giving a temperature of 120OC. - If car- have a less evident surface character. The slag also bon(charcoal) is preheated in a shaft by hot gas, the has a flowpattern, some times with a reddish colour. adiabatic temperature may increase to about 1350'C. Certain parts have a smooth surface, like candle Higher temperatures reported can only be due to wax,that has solidified on a cold surface. In situ slag COr-generation or other measures, such as preheat- in each furnace is of the same kind.
Details
-
File Typepdf
-
Upload Time-
-
Content LanguagesEnglish
-
Upload UserAnonymous/Not logged-in
-
File Pages7 Page
-
File Size-