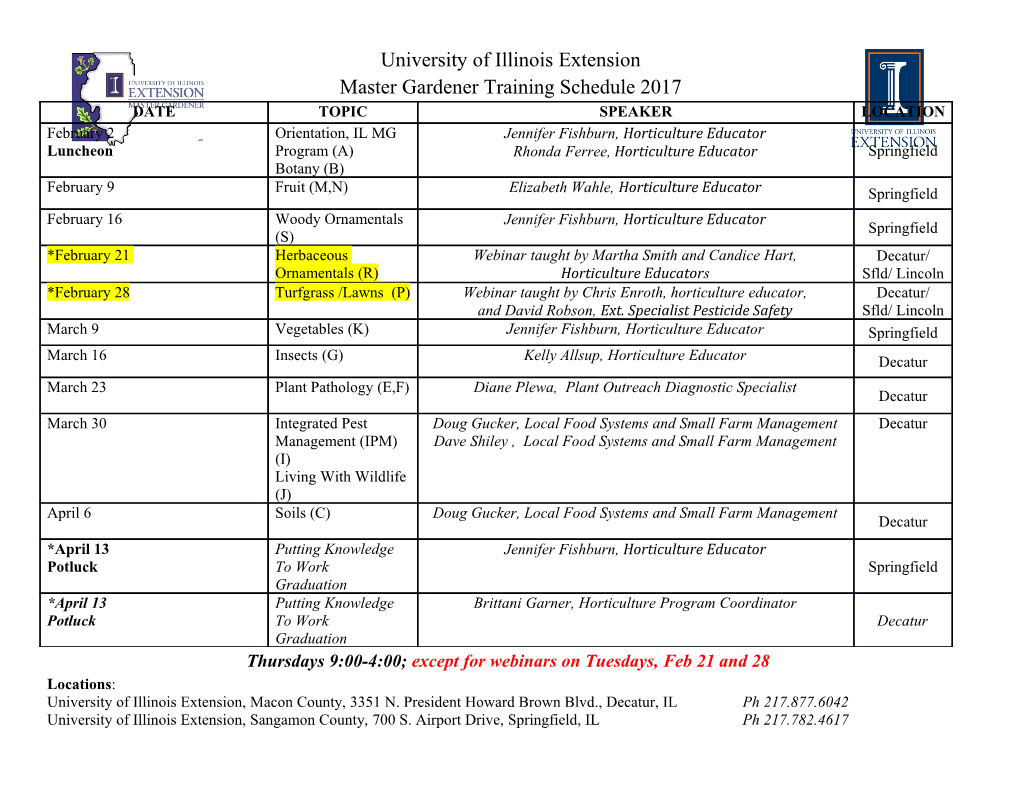
49th International Conference on Environmental Systems ICES-2019-379 7-11 July 2019, Boston, Massachusetts Solid State Electrochemical Oxygen Separation and Compression Michael Reisert1, Ashish Aphale2, Boxun Hu3, Su Jeong Heo4, Junsung Hong5, and Prabhakar Singh6 Department of Materials Science and Engineering, University of Connecticut, Storrs, CT 06269 Dale Taylor7 American Oxygen, Salt Lake City, UT and John Graf8 NASA Johnson Space Center, Houston, TX Ceramic solid state electrochemical oxygen separation and compression systems offer the ease of producing high purity and high pressure oxygen from a variety of gaseous streams representative of ambient and constrained systems exposure conditions (terrestrial and space). The electrochemical cells utilize exclusive oxygen ion conducting membranes (fluorites, doped) and operate in 550-850 °C temperature range. Advanced perovskites synthesized from non-noble and non-strategic materials serve as electrodes for both oxygen reduction and evolution. A number of electrochemical cells, connected in series using dense electronically conducting perovskite interconnect form the basis of “cell stack” for increased oxygen production. Thermochemical-electrochemical principles for oxygen separation and compression will be discussed. Materials for the construction of cells and stack along with fabrication techniques will be examined and basis for the selection will be described. Approaches for the electrochemical performance improvement will be discussed. Nomenclature VN = Nernst voltage LSCF = lanthanum strontium cobalt ferrite R = universal gas constant LSM = lanthanum strontium manganite F = Faraday constant LCM = lanthanum calcium manganite PO2 = partial pressure of oxygen SOEC = solid oxide electrolysis cell I = current SOFC = solid oxide fuel cell jO2 = flux of oxygen CTE = coefficient of thermal expansion QO2 = flow rate of oxygen FEA = finite element analysis OTM = oxygen transport membrane ppm = parts per million MIEC = mixed ionic-electronic conductor ppb = parts per billion YSZ = yttria-stabilized zirconia EVA = extravehicular activity CSO = cerium samarium oxide 1 Graduate Student, Materials Science and Engineering, University of Connecticut, 44 Weaver Rd., Storrs, CT 06269. 2 Postdoctoral Researcher, Materials Science and Engineering, University of Connecticut, 44 Weaver Rd., Storrs, CT 06269. 3 Assistant Professor, Materials Science and Engineering, University of Connecticut, 44 Weaver Rd., Storrs, CT 06269. 4 Postdoctoral Researcher, Materials Science and Engineering, University of Connecticut, 44 Weaver Rd., Storrs, CT 06269. 5 Graduate Student, Materials Science and Engineering, University of Connecticut, 44 Weaver Rd., Storrs, CT 06269. 6 UTC Endowed Chair Professor, Materials Science and Engineering, University of Connecticut, 44 Weaver Rd., Storrs, CT 06269. 7 CEO, American Oxygen, LLC., 4054 S 685 E UNIT F, Salt Lake City, UT 84107. 8 Engineer, NASA Johnson Space Center, 2101 E NASA Pkwy, Houston, TX 77058. Copyright © 2019 University of Connecticut I. Introduction lectrochemical oxygen compression can provide high-purity oxygen for life support systems in both terrestrial E settings and in human spaceflight.1 Currently, oxygen is mechanically pumped to be distributed into portable oxygen tanks for use in medical applications or as a means of supplying oxygen to the confines of space stations or space suits.1 Mechanical pumping requires a great deal of energy and oftentimes cannot be feasible for direct use within structures in space. Tanks which have already been filled on earth are subsequently transported to the space station, which drastically increases payload weights and limits transport of other necessary supplies. Furthermore, these tanks must be presurized to 300 bar for safe handling and proper confinement. It is imperative to determine a means of oxygen compression within the confines of the space station which can pressurize atmospheric-level oxygen up to 300 bar while utilizing the oxygen output of current fuel cell and electrolysis cell systems onboard the station.1 Separation of oxygen from air or other oxygen-containing gases and subsequent oxygen compression are achieved by using conductive ceramic components which foster exclusively oxygen-ionic transport. This transport can be preferentially driven by an applied bias across the selectively-ionic conducting electrolyte.2 Confining or housing the produced oxygen results in a single-step means of pressurization, eliminating the need for mechanical pumping. The electrochemical principles enabling this are the foundation of other systems such as fuel cells and electrolysis cells.2,3 These systems are well-understood and have been implemented in small and large-scale industrial settings. However, these systems often operate under reducing or mixed reducing/oxidizing gas atomspheres with ppm-ppb contaminant levels, which has historically lead to certain material selection issues due to electrode poisoning.3–5 The oxygen compressor of question would operate in a pure or relatively pure oxygen atmosphere, which influences material selection and avoids some contaminant issues which will be later discussed. This all-oxygen atmosphere and past demonstration of material functioning in electrochemical systems highlights the feasibility of an all solid-state and single-step electrochemical oxygen separator/compressor. In this paper, the different ceramic components of the specified oxygen separator/compressor will be discussed from a materials standpoint. This discussion will emphasize why these materials have been chosen for pure oxygen separation and compression. Furthermore, fabrication methods for system production will be discussed. This will culminate in a discussion of the current trends in this technology and the means by which this particular system compares and may be improved. II. Oxygen Transport Membrane Operating Principles The electrochemical oxygen separator/compressor operates as an oxygen/ionic transport membrane (OTM/ITM). These systems can be either pure oxygen conducting or a mixed ionic/electronic conductor (MIEC).2 Pure oxygen conduction is achieved using an electrolyte which only allows transport of oxygen ions. This is used in conjunction with an anode and a cathode, where an applied electric potential allows oxygen within the feed gas to ionize at the cathode and move through the electrolyte towards the anode.2,3 The application of a bias makes this OTM electrically driven or passive. A MIEC transports oxygen ions and electrons Figure 1. Schematic of an electrically-driven oxygen transport simultaneously due to an oxygen partial membrane pressure differential across the singular ceramic membrane. This membrane is advantageous for systems which lack an external power source.2 However, for high-purity oxygen and control of oxygen volume produced via external voltage control, the use of a passive OTM is most efficient.2,6 This variation of OTM is pictured in Figure 1. With the constant application of bias, constant feed of gas at the cathode, and a means of housing the pure oxygen at the anode, the production oxygen can be concentrated at high pressure. This pressurized oxygen is needed for proper containment and controlled flow in life-support systems and can feed oxygen to cabin air supplies within confined areas. This 2 International Conference on Environmental Systems device provides a means of both separating and compressing oxygen from various gas streams, however in the particular setting with a pure oxygen inlet gas, only compression is required and will be subsequently discussed. The partial pressure of the production oxygen at the anode is related to the applied bias via the Nernst equation in Eq. (1).7 RT pO2(anode) VN = ln( ) (1) 4F pO2(cathode) By applying an electrical bias at or above the Nernst voltage (VN), low pressure air can be fed at the cathode and electrically driven toward the anode, where it can then be housed within a pressure vessel. This means of oxygen separation and compression is robust and efficient, delivering compressed, extremely pure oxygen in a single step. A device designed by Meixner et al., which provided the basis for this design, produced 99.99% purity oxygen by the principle outlined in Eq. (1).7 A source of oxygen can be fed into the cathode region of the OTM, where oxygen is reduced by the electric potential via the following reaction in Eq. (2): − 2− O2 + 4e = 2O (2) Oxygen ions can now travel through the electrolyte via oxygen vacancy diffusion, being driven by the electric potential. Ions reach the anode and lose the excess electrons to again form diatomic molecular oxygen via the reaction in Eq. (3). 2− − 2O = O2 + 4e (3) These reactions are nearly identical, however they differ in the oxygen species that is produced: whether that be ionized oxygen or diatomic oxygen gas. The flux of oxygen through the electrolyte is determined using a general form of the Wagner equation shown in Eq. (4).8 ′′ RT lnP j = − ∫ O2 σ dlnP (4) O2 16F2L lnP′ i O2 O2 2 In Eq. (4), 푗푂2 is the oxygen flux in mol/m s, R is the universal gas constant, T is temperature, F is the Faraday constant, ′′ ′ L is the electrolyte thickness, 푃푂2 and 푃푂2 are the partial pressures of oxygen at the outlet and the feed side, respectively, and 휎푖 is ionic conductivity. The electrolyte thickness directly correlates with oxygen flux and dictates the electrolyte material’s ability to conduct oxygen ions. The above equation correctly assumes that bulk diffusion and ionic conductivity
Details
-
File Typepdf
-
Upload Time-
-
Content LanguagesEnglish
-
Upload UserAnonymous/Not logged-in
-
File Pages10 Page
-
File Size-