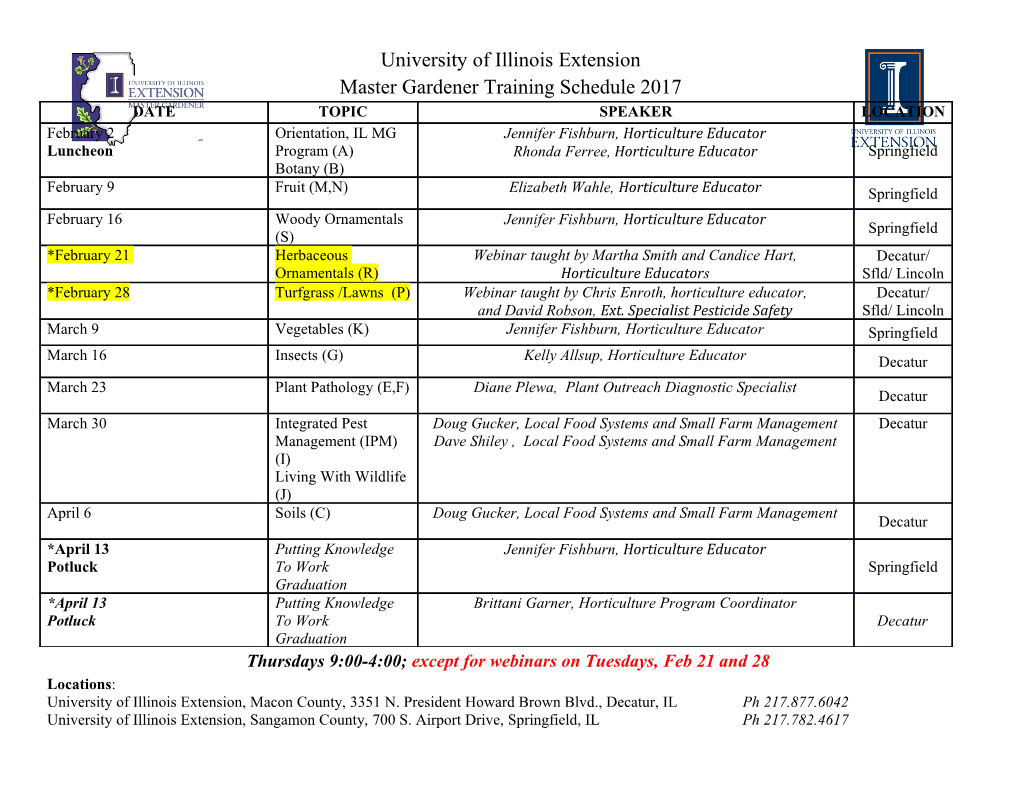
Laser-GMA Hybrid Welding: Process Monitoring and Thermal Modeling E.W. Reutzel, S.M. Kelly, R.P. Martukanitz Applied Research Laboratory, Pennsylvania State University, State College, PA, USA M.M. Bugarewicz, P. Michaleris Dept. of Mechanical and Nuclear Engineering, Pennsylvania State University, University Park, PA, USA Abstract in some welding applications because of insu±cient gap bridging capabilities, requiring high precision during edge Laser-Gas Metal Arc (GMA) hybrid welding is an preparation and setup. Additionally, the focussed energy increasingly accepted technology for a variety of commercial of the laser beam results in a narrow heat a®ected zone applications, from industries as diverse as shipbuilding to (HAZ) that can lead to steep spatial and temporal thermal automobile manufacture. As applications become more gradients that sometimes result in brittle microstructures. widespread, there is a growing need to understand the In contrast, conventional GMAW o®ers the ability to relationship between the numerous process parameters and easily bridge gaps in the joint by introducing ¯ller metal the process results, including weld quality and distortion. to the process. The composition of the ¯ller materials can To build upon the body of knowledge supporting this, two be customized to produce improved material properties. The separate experiments are performed. additional heat results in reduced cooling rates, often leading In the ¯rst, hybrid welds are performed with a 2.6 kW to improved ductility. However, the high heat can result in Nd:YAG laser and sensors are used to monitor GMA voltage undesirable distortion or buckling, and the physics of the and current, as well as the arc-plasma electromagnetic process result in an inability to produce deep penetration emissions in both the ultraviolet and infrared regions. welds. As a result, thick sections are often welded with Process perturbations, such as fluctuations in GMAW multiple weld passes. voltage and wire speed, laser angle of incidence, and These shortcomings can be overcome by combining the laser/GMAW torch head separation distance, are introduced laser with an arc welding technique such as GMAW. Not only to study their e®ect on sensor output. is this helpful in accommodating gaps and reducing weld- Finally, thermal ¯nite element models are developed and head positioner tolerance requirements while maintaining used to quantify the varying heat input per unit length deep penetration [3], but it has also been known to produce when compared with conventional GMAW and laser welding even greater welding speeds and to provide an improved weld processes, particularly as applied to joining of thin steel microstructure upon cooling [4]. structures. The onset of buckling during weld fabrication This document outlines recent results of various has been shown to be strongly dependent upon the heat investigations into both practical and theoretical aspects of input used to produce the weld. A thermal model of the laser-GMA hybrid welding. The ¯rst section discusses how laser-GMA hybrid welding process is developed to serve as various sensors can provide information regarding the state a representation of this complex process. of the hybrid welding process. The next section presents results of experiments to introduce a single-pass hybrid weld as a substitute for a multi-pass conventional weld for thick Introduction substrates. The ¯nal section discusses initial attempts to de¯ne a theoretical thermal model of the hybrid welding It has been nearly a quarter of a century since researchers process that will be used to quantify distortion and buckling ¯rst conceived of combining a conventional welding arc with for comparison of the laser, gas metal arc, and hybrid a laser beam in a hybrid process [1, 2], but only recently has welding processes. laser-GMA hybrid welding begun to be utilized in industrial applications. Laser beam welding o®ers relatively high welding speed Process Monitoring compared to conventional processes and high penetration that is achieved due to the keyhole e®ect. Unfortunately, Detection of weld defects using real time monitoring due to the small spot size of the laser, it has limited success methods is of signi¯cant concern in industry. This is largely due to the increased production and liability costs to observe variations in sensor output. A variety of di®erent that result when weld defects are not identi¯ed early in voltage set-points were tested. The arc currents obtained the production cycle. Weld monitoring systems must be during these experiments are shown in Figure2. For a reliable, flexible and cost e®ective in non-clean, high-volume given wire feed speed (WFS), at lower voltages there was production environments. Various sensors in the ¯eld of real a dramatic increase in current when the laser was removed time weld monitoring have shown promise in detecting weld from the system. At 18 V it can be seen that there is an process conditions. These include acoustic, plasma-based, increase in current of approximately 30 A upon deactivation optical (infrared, ultraviolet and x-ray) and electromagnetic of the laser. In all cases, WFS was 76 mm/s (180 ipm), gas sensors. In the laser welding process alone, the range of (Ar-25% O2) flow rate was 35 CFH, and the laser was applied signal emissions from the weld zone has led to a wide range for the ¯rst half of the weld, then deactivated for the second of techniques being applied to sensing of the process [5, 6, 7]. half. With increasing arc voltage, these e®ects became much In conventional arc welding, parameters such as voltage and less pronounced. current have been monitored to determine characteristics and health of the weld process [8, 9]. 18 V When the laser welding process is combined with conventional GMAW, it is clear that the processes will interact and necessarily a®ect one another (See Figure 1). With a constant voltage welding power supply, the resistance 21 V of the wire stick-out and arc are inversely proportional to the output current of the power supply. It is reasonable to expect that the additional heat deposited by the laser 24 V beam, and the additional metal vapor and ions that are expelled from the keyhole during welding will a®ect the arc resistance, and therefore the arc current. It is relatively 33 V simple to measure the arc current using a Hall-e®ect probe, and experiments revealed that the arc current correlates closely with changes in many process variables. It is Laser + GMAW GMAW Only believed monitoring of this single parameter could enable determination of a variety of process variables that are Figure 2: A®ect of laser at di®erent voltage set-points on di±cult to monitor otherwise. A few examples are discussed arc current. below. Laser-Gas Metal Arc Hybrid Welding Process (Laser Leading Arc) A possible explanation for this behavior can be developed Focused Laser Beam by considering that as arc length increases, resistance also increases since the electrons have a greater distance to travel. An increase in arc length can be caused by increasing Keyhole Gas Metal Arc Welding Torch penetration depth, therefore the value of the current can be strongly correlated to penetration. The constant voltage Inert Shielding Gas power supply used during the experiments exhibits a positive Electric Arc slope for the voltage and current characteristics in order to Work-piece maintain Ohm's Law, V = IR (where V is voltage, I is Molten Pool current, and R is resistance). Therefore, penetration and welding current are directly proportional. As penetration decreases when the laser is deactivated, the arc length is reduced and current must increase. In GMA welding, the penetration has been shown to increase as the voltage is increased. At lower voltage set- Figure 1: Schematic of the hybrid welding process. points, such as 18 V, the di®erence between the penetration of the hybrid and the GMAW process is more pronounced. This could explain the relatively large increase in current when deactivating the laser. As voltage is increased and A®ect of laser on arc current arc force increases, one can expect less of a di®erence in penetration when the laser is deactivated and therefore To investigate the a®ect of laser on the arc current, a hybrid a smaller increase in current. However, other hybrid laser-GMA bead-on-plate weld was performed, and the laser experiments involving an increase of laser power, and was terminated halfway through the weld length, in order therefore penetration, did not demonstrate this same decrease in current, and therefore raises questions with this Thermal Modeling of Hybrid theory. Other explanations are discussed in Travis et al Welding [10, 11]. Objective This portion of the paper focuses on the development A®ect of laser-to-arc spacing on arc current of a thermal model for hybrid welding to calculate the temperature history of the part during the weld process. In the next phase of research, this temperature history will It has been reported that varying the laser position relative be used as input to an elasto-plastic ¯nite element model to the GMAW torch a®ects the welding process [12, 13]. To in order to predict the e®ect of stress and the degree of evaluate this e®ect, this distance was varied using 22 V and distortion in structures that are welded by this method. 91 mm/sec (215 ipm) WFS as constant process parameters. The heat source model outlined by Goldak et al is used The arc current was measured during the weld when the to determine the e®ects of the thermal load in the laser- laser was positioned to interact at various positions along GMA Hybrid welding process [14]. First, a GMA welding the weld direction relative to the GMAW torch, including model and a laser welding model are individually generated, laser leading, lagging, and coincident with the GMAW torch.
Details
-
File Typepdf
-
Upload Time-
-
Content LanguagesEnglish
-
Upload UserAnonymous/Not logged-in
-
File Pages6 Page
-
File Size-