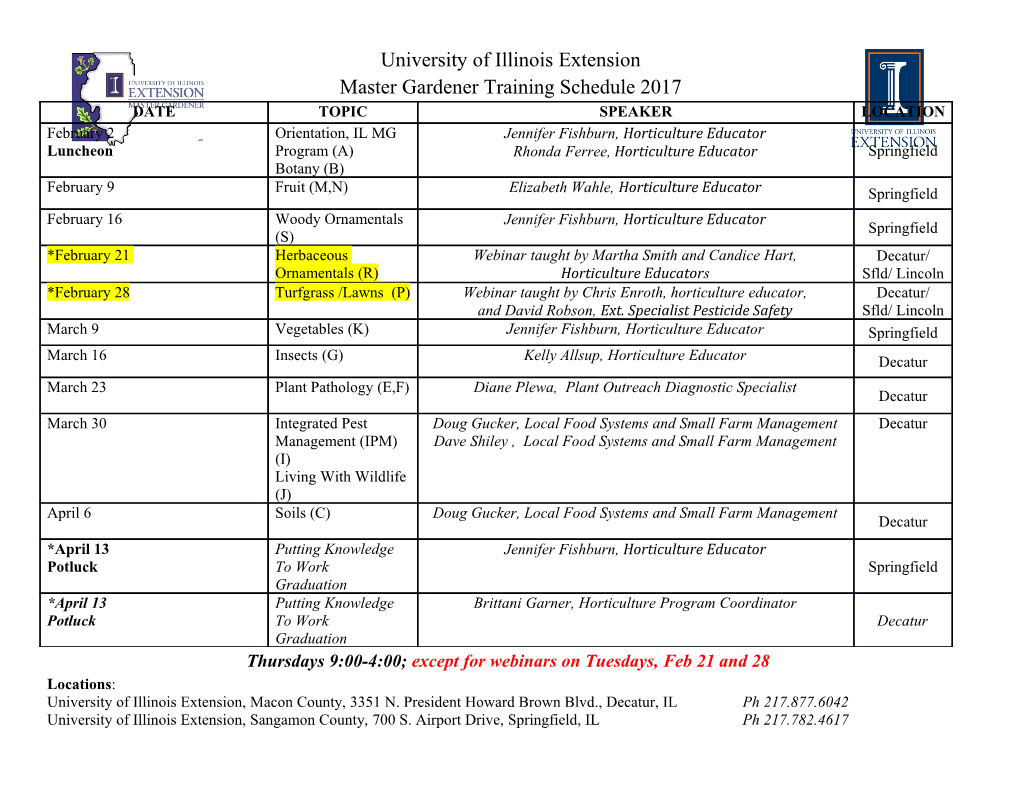
8.4 Batch Processes and Their Automation A. GHOSH (1995, 2005) INTRODUCTION sive objectives, and many possible solutions. Most real-life problems tend to be complex. The solution of a complex Batch automation and batch control are discussed in this problem involves its progressive decomposition into simpler section from both a process characteristics and a modeling functional modules and their proper integration. point of view. This discussion covers the various control This section deals with batch control problems and their functions, distributed control systems (DCS) capabilities, and solutions in general. Specific details on batch reactor control reliability aspects. Other sections in this chapter also deal can be found in Section 8.8. with the subject of batch control. Section 8.3 describes ter- minology, and Section 8.8 is devoted to the control of batch reactors. BATCH CONTROL STANDARDS In a continuous process, such as the distillation of crude oil or the manufacture of bulk chemicals and fertilizers, the The ANSI/ISA-88 (IEC 61512) batch control standard1–3 is product is manufactured on a continuous basis. In batch pro- providing significant benefits to users and suppliers of batch cesses, used in the food, pharmaceutical, and fine chemical control systems worldwide. The standard is in three published industries, products are manufactured in batches. Batch pro- parts, while the fourth part is under development (Table 8.4a). cesses are sequential, where the control functions (called phases), such as charging, mixing, heating, cooling, and test- Part 1: Models and Terminology ing, are performed in an ordered fashion. Each phase may require many process steps, such as the opening and closing Part 1 defines standard terminology and a number of models of valves, starting and stopping of pumps, and setting and for batch control. The key models are procedure, physical, resetting of control loops. In addition to the normal step-by- and control activity (Figure 8.4b). The terminology, struc- step control actions, batch process control requires many tures, and concepts used in the standard are affecting every- other functions; for example, responding to abnormal or fail- one in the batch control business. Most major suppliers have ure conditions, keeping batch records, maintaining recipes, adopted standard terminology and have designing batch con- and scheduling batches. trol systems with a modular set of functions and hierarchy Batch process control is a complex task rather than a based on the control activity model. This modularity allows difficult one. A difficult problem is one that is mathematically for easier integration of third party-packages to do functions or scientifically difficult to solve and usually has a single such as production planning, scheduling, and production solution. A complex problem, on the other hand, is logisti- information management. It also makes a control system cally more challenging. A batch process is characterized by easier to integrate with production management and business numerous interrelationships and constraints, mutually exclu- planning systems. TABLE 8.4a Batch Control Standards Batch Year International US standard Scope standard published standard Part 1 1995 ANSI/ISA-88.00.01 IEC 61512-01 Models & terminology Data structures & Part 2 2001 ANSI/ISA-88.00.02 IEC 61512-02 language guidelines Part 3 2003ANSI/ISA-88.00.03 IEC 61512-03 General & site recipes 1544 © 2006 by Béla Lipták 8.4 Batch Processes and Their Automation 1545 Procedure Physical Control activity model model model Recipe Prod. planning Prod. info management & scheduling management Recipe Process Process procedure cell management Unit Unit Unit procedure supervision Equipment Operation Process module control Phase Control module FIG. 8.4b Batch standard models. (Note: Arrows show relationships, not data flow.) The main benefits of Part 1 of the batch control standard nance and version upgrades. It is felt that PFC notation will are: soon become the common way for representing procedural elements in a recipe. • Improved communication between suppliers and users of batch control Part 3: General and Site Recipes • Easier identification of end-user needs • Straightforward recipe development Recipes are of four types: general, site, master, and control • Reduced cost of automating batch processes (Figure 8.4d). A general recipe contains generic information • Reduced life-cycle engineering effort for the manufacture of a product and does not include equip- ment or site-specific information. This is the first recipe that Part 2: Data Structures and Language Guidelines may be generated when a new product has been developed in a pilot plant. The ISA-88 Part 2 standard is in three parts: data models, information exchange tables, and procedure function charts. The data model section provides formal representation of entities specified in Part 1 of the standard, such as recipe, equipment, planning and scheduling, and information man- agement using Universal Modeling Language (UML) nota- tion. The information exchange section uses SQL relational Initialize tables to specify exchange requirements between recipes, Implicit transition process equipment, schedules, and batch production. + + The final part of the standard deals with a graphical Charge “ ” indicates that representation of procedures, such as master and control rec- this operation has a procedure ipes and using Procedure Function Chart (PFC) notation + (Figure 8.4c). PFC is somewhat similar to Sequential Func- React Explicit tion Chart (SFC) notation as defined in IEC 61131-3 stan- transition dard.4 PFC notation addresses procedural control and execu- tion, while SFC notation was developed primarily for state Transfer variable Transfer variable = storage = shipping machines. PFC notation meets the requirements of recipe ++ Transfer to Transfer to procedures better than SFCs. storage shipping PFC notation is intuitive and easy to follow. Users famil- iar with SFC notation will find many similarities between the Transfer Transfer complete complete two. However, explicit specification of functions such as process equipment allocation and synchronization of phases makes PFC easier to follow than SFC notation. Providing tools for information exchange, as specified in the standard, allows suppliers to design more modular batch FIG. 8.4c control systems. This will reduce the high cost of mainte- Unit procedure using procedure function chart (PFC) notation © 2006 by Béla Lipták 1546 Control and Optimization of Unit Operations Generic & transportable General/site Master/control GeneralGeneral Recipe recipe recipes recipes Process Procedure SiteSite Recipe recipe Process Unit stages procedures MasterMaster Recipe recipe Process Operations operations Process Phases ControlControl Recipe recipe actions Specific & local FIG. 8.4e FIG. 8.4d Mapping between general/site recipes and master/control recipes. Recipe model. General and site recipes contain the same categories of In the increasing complexity of global manufacturing, information, such as header, formula, procedure, equipment many process manufacturers find it challenging to maintain requirements, and other information, as in master and control a single definition of a product in different manufacturing recipes. The procedure elements of general and site recipes facilities. General and site recipes provide an equipment- map well with master and control recipes (Figure 8.4e). independent means of describing batch manufacturing pro- cesses, accelerating both time to market and time to volume Part 4: Production Records production. A standardized general recipe meets this chal- lenge as a central repository for product manufacturing infor- This part of the batch control standard defines a logical data mation. General and site recipe functions were identified in model and means of data exchange for production records Part 1 of the ISA-88 batch control standard, however, little containing information about batches and other production was specified about them in either Part 1 or 2. segments. The standard is under development. Part 3 of the batch standard, which deals with these functions, was published in 2003. The Benefits of Standards A general recipe is an enterprisewide recipe for a man- ufactured product that serves as the basis for both site and The benefits of the ANSI/ISA-88 (IEC 61512) batch control master recipes. Chemists and chemical engineers with inti- standard reach beyond batch process control. Although the mate knowledge of both the product’s chemistry and process- standard is primarily designed for batch processes, it is also ing requirements are generally responsible for creating it. It being applied successfully in various manufacturing indus- identifies raw materials, their relative quantities, the required tries. This is because the standard is not just for software, processing, and the order of processing. It may define the equipment, or procedures. It is a way to conceptualize your processing capabilities required, such as cooling or heating, production processes that helps you better design your plants or the generalized equipment requirements, such as glass- and manufacture your products. lined reactors, but does not define the specific equipment that The data models and information exchange tables pro- may be used to manufacture the product. A general recipe vide significant advantage in the automation and modulariza- may also serve as input for corporate production planning tion of any manufacturing process. The shift from monolithic
Details
-
File Typepdf
-
Upload Time-
-
Content LanguagesEnglish
-
Upload UserAnonymous/Not logged-in
-
File Pages14 Page
-
File Size-