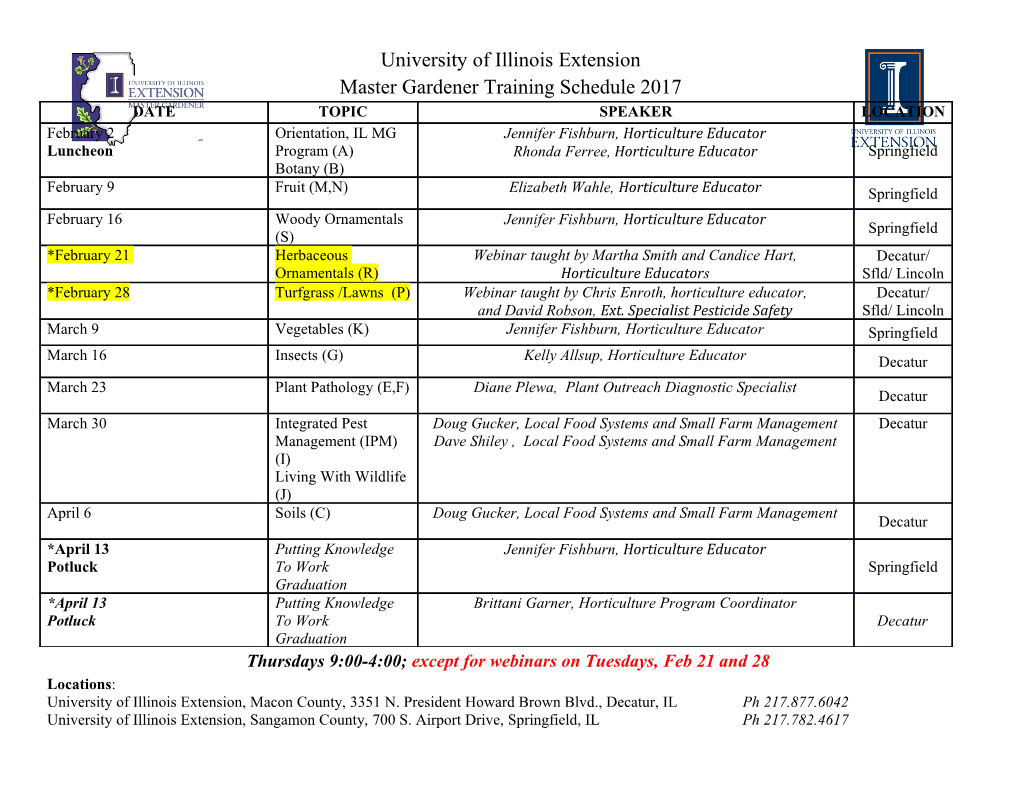
Stabilized Chlorine Dioxide in Fuel Ethanol Fermentation: Efficacy, Mechanisms and Residuals Derrick Okull, PhD Technical Service Manager Dupont Nutrition and Biosciences Additives Stabilized Chlorine Dioxide (ClO2) – What is it? Property Value/Description NOT chlorine/bleach Buffered sodium chlorite solution, antibiotic-free aqueous Crystallization Point -12°C 10°F solution Historically used in food processing/water treatment FreezingPoint -18°C 0°F industries for contamination control/sanitation Boiling Point 106°C 223°F 14yr history in fuel ethanol – GRAS status, with expert concurrence, for use as a processing aid in potable alcohol pH 9.5 to 9.8 and fuel ethanol production with resulting distillers’ grains approved for use in animal feed (cattle, swine, poultry). Density (g/mL) 1.18 to 1.21 Controls lactic and acetic acid producing bacterial @ 20 °C contamination Color Clear lightyellow solution Suitable for ethanol production from sugar and/or grain substrates Odor Faint chlorine-like smell Generated, concentrated solutions traditionally used in paper bleaching Copyright @ 2019 Dupont All Rights Reserved Additives Stabilized Chlorine Dioxide – how it works A solution of 15 – 25 % Sodium Chlorite Chlorine dioxide is formed under acidic pH conditions When applied correctly, inactivates bacteria without harming yeast Activity is pH dependent – Need pH < 5.4 to be effective Chlorite + Acid Chlorous acid + Chlorine dioxide - + ClO2 + H HClO2 + ClO2 Chlorite + Low pH mash/other substrate Low pH/Acidic conditions drive conversion of Chlorite into more active form to kill bacteria on contact Additives Bacterial Contamination in the Ethanol Process: A Primer Copyright @ 2019 Dupont All Rights Reserved Additives ETHANOL PRODUCTION - DRY GRIND PROCESS OVERVIEW Grinding/Slurry / Cook CO2 Liquefaction Back Set Syrup Corn Fermentation Oil Distillation DDGS Ethanol Copyright @ 2019 Dupont All Rights Reserved Additives WHERE DOES CONTAMINATION COME FROM? Mash headers/piping/deadlegs Yeast propagation Dry ground corn Cook Conducive temperature – 88 – 92ºF pH – 4.9 – 5.6 Liquefaction* Food source – sugar, proteins, and trace/micronutrients Heat CO exchangers 2 Moisture – mash Protection - biofilms Drop lactic acid in a contaminated process Distillation Fermentation ~92ºF, 60hrs Beer well Significant source of infection / re-contamination Copyright @ 2019 Dupont All Rights Reserved Additives WHY DOES BACTERIA CAUSE LOSSES? Decline in Ethanol titer from a contaminated process Competition with inoculant yeast for nutrients Increased production of organic acids (lactic and acetic) by contaminant bacteria instead of ethanol Inhibition of yeast Recycle through backset can also compound inhibition Downtime, cleaning costs from fouling as a result of unfermented sugar going into distillation Copyright @ 2019 Dupont All Rights Reserved Additives Controlling Contamination Process Controls Antimicrobials Antibiotics CIP/ Sanitation Hop Acids Temperature Oxidatives Virginiamycin (Lactrol™) Monensin High Solids eg ClO2, H2O2,Iodine High Yeast inoculum HOCl Erythromycin pH Control/ Acids Quaternary Compounds Penicillin Glutaraldehyde Combinations Bacterial Peptides Cellular Targets of some common disinfectants Cellular Targets of antibiotics http://www.connect2cleanrooms.com/news-article/Rotational- Copyright @ 2019 Dupont All Rights Reserved Cleaning Example Plant Data Copyright @ 2019 Dupont All Rights Reserved Additives Lactic acid levels in a process before and after addition of ClO2 Baseline ClO2 added Copyright @ 2019 Dupont All Rights Reserved Additives ClO2 Plant Performance ClO2 was trialed in conjunction with antibiotics at a 100 MGPY Dry Grind Ethanol Plant experiencing an active infection resulting in elevated lactic acid levels, high drop sugars, and decreased ethanol yields. Lactic Acid (%w/v) Ethanol Yield (EtOH/Solids) 0.35 0.419 0.418 0.30 0.418 0.417 0.25 0.416 0.20 0.415 0.15 0.414 Conc. (%w/v) 0.413 0.10 0.413 Ethanol/Solids 0.412 0.05 0.411 0.00 0.41 0 10 20 30 40 50 60 70 Time(Hrs) 0.409 Baseline Contaminated Baseline Contaminated Copyright @ 2019 Dupont All Rights Reserved Additives ClO2 Performance During Active Contamination Drop Glucose (%w/v) Lactic Acid (%w/v) 0.16 0.35 0.14 0.30 0.12 0.25 0.10 0.20 0.08 0.15 0.06 Conc. (%w/v) 0.10 Conc. (%w/v) 0.04 0.05 0.00 0.02 0 10 20 30 40 50 60 70 0.00 Time(Hrs) Time(Hrs) Baseline Contaminated FERMASURE® XL Baseline Contaminated FERMASURE® XL ClO2 ClO2 Dosing with ClO2 helped to reduce the contamination in the system and move the plant back towards baseline profiles than treatment with antibiotics alone. Copyright @ 2019 Dupont All Rights Reserved Additives ClO2 Performance During Active Contamination Ethanol (%w/v) Ethanol Yield (EtOH/Solids) 16.0 0.419 0.418 14.0 0.418 0.418 12.0 0.417 10.0 0.416 8.0 0.415 6.0 0.414 Conc. (%w/v) 4.0 0.413 0.413 2.0 Ethanol/Solids 0.412 0.0 0.411 0 10 20 30 40 50 60 70 0.41 Time(Hrs) 0.409 Baseline Contaminated FERMASURE®ClO2 XL Baseline Contaminated FERMASURE®ClO2 XL Dosing with ClO2 helped to decrease lactic acid concentration in the system and move yields and sugar data back to baseline. Copyright @ 2019 Dupont All Rights Reserved Additives Grain Product Trail Customer must receive guidance on Feedstock recommended material safe (Corn/Wheat) handling, PPE and storage requirements Milling Engineering controls in place to limit Transport to Customer Possible customer by Liquefaction exposure potential to workers storage tote Dosing Points Sodium Chlorite Yeast Propagation (NaClO ) 2 Customer Process Blending Packaging/Storage/ H2O Stable Product Fermentation CO Atm. Process Transportation 2 Solids Other Distillation Dehydration Ingredients Separation Evaporation Ethanol Blending Process at Toll Manufacturing facility DDGS Proven safe Ethanol to (GRAS status) and Distillers Corn Market Oil approved for use in EtOH-blended Transfer to Animal production of potable gasoline Feed producer alcohol and fuel ethanol production with co- Blended Animal Feed products intended for use in animal feed. Copyright @ 2019 Dupont All Rights Reserved Additives Residuals in DDGS Vol ClO2 dose (ppm) Vol of FXL (gal) Wgt (kg) NaClO2 (kg) Preferm vol 180000 1000 180 720 159 Ferm 1 387000 1000 387 1548 341 Total working vol 1211000 468.2 567 2268 499 Assumptions: Continuous fermentation – vessels in series Dosing in the first two vessels in the train at up to 1000ppm (0.1% of working volume of dosed vessels) At drop, dilution has occurred across the system – total working volume includes all vessels in the train Stabilized ClO2 contains 15-22% sodium chlorite (NaClO2) At this dose, the system will have an estimated 499kg of chlorite End products of reaction in acidic environment are NaCl (salt) and NaClO3 (chlorate)at about a 2:1 ratio, with the chlorate getting further reduced to NaCl Copyright @ 2019 Dupont All Rights Reserved Additives Typical Sodium in DDGS ~ (2000 ppm) 0.2% Potential from high dose ClO2 – 155 ppm (0.0155%) https://www.card.iastate.edu/products/books/distillers_grains /pdfs/chapter5.pdf (K. Bregendhal, Chapter 5) Copyright @ 2019 Dupont All Rights Reserved Thank you! Copyright @ 2019 Dupont All Rights Reserved.
Details
-
File Typepdf
-
Upload Time-
-
Content LanguagesEnglish
-
Upload UserAnonymous/Not logged-in
-
File Pages17 Page
-
File Size-