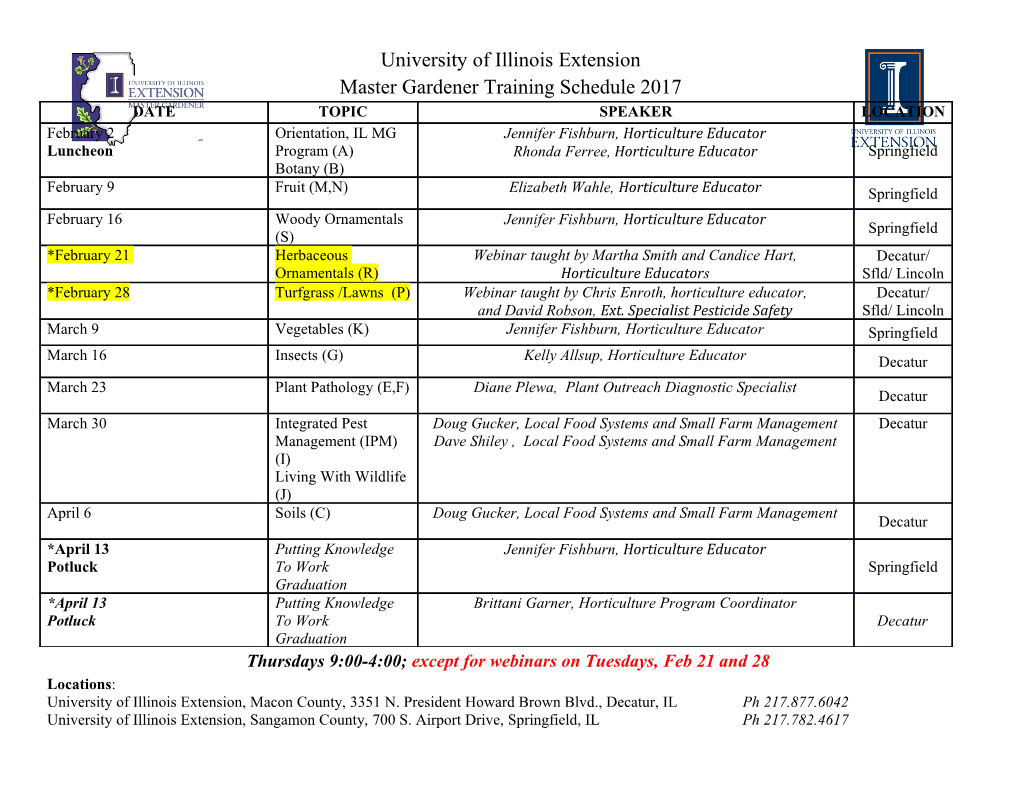
Integrated Design-Bid-Build and its Effects on Integrated Project Delivery Drivers Alexander G. Sargiss California Polytechnic State University San Luis Obispo, California Integrated project delivery is becoming a more common and successful delivery method in the construction industry compared to more traditional methods such as design-bid-build. Integrated Design-Bid-Build is a hybrid between the two which has been implemented very few times to test if it can be used as a more viable delivery method in the future. There has been very little research in to Integrated Design-Bid-Build that is accessible for analysis. This research study examines case studies of projects completed using IPD and analyzes their “IPD Profiles” which are measured using five primary project drivers. These project drivers are: cost predictability, schedule predictability, risk management, technical complexity, and market position. Each have proven to play key roles when choosing to use IPD. The purpose of this study is to take the Integrated-Design-Bid-Build delivery method and apply it some of these projects completed using IPD and interpret how this new integrated delivery approach would affect each of those project drivers. Keywords: Integrated Project Delivery (IPD), Integrated Design-Bid-Build (IDBB), Project Drivers, Collaboration Introduction Integrated project delivery [IPD] is a collaborative delivery method which takes the owner, contractor, architect, and other key players of a project and creates an environment focused on the best interests of a project rather than their individual goals. This type of collaboration is built on trust and when effectively structured has proven to yield successful results. IPD is still a fairly new approach for the construction industry, but is rapidly evolving and lessons learned from completed projects are already being carried on to the next IPD project. Many believe in an industry like construction where productivity has been on the decline since the 1960s that IPD could be the solution when applied to the correct project through the correct project team. Projects today face this lowered productivity due budget and scheduling conflicts as well as adverse relations between the owner, contractor, and engineer. The contracts utilized in integrated project delivery offer new shared risk strategies that more accurately reflect the roles of the owner, architect, and contractor of a project. In more traditional delivery methods key players of a project focus on more on their respective roles and how to mitigate their own risk while simultaneously shifting risk to the other parties. This ideology does not encourage a collaborative work ethic like IPD does through shared risk and reward clauses implemented in contract documents. Integrated project delivery is a comprehensive process which encompasses the entire process of programming, design, construction, and building operations. Key Principles of Integrated Project Delivery In an integrated project, key participants are involved early in the design phase to make informed decisions that are going to significantly impact the project in the long run. Having all the key players together early on encourages discussion between the different disciplines and keeps everyone on the same page. The architect can propose different design options while the contractor can offer cost and feasibility analysis that meet the owner’s expectations. This meeting of the minds early in the design phase helps create a more reliable budget and schedule that participants can get behind. Upfront costs do increase as a result, but in theory this early collaboration should greatly reduce conflicts during construction and savings in the long run should outweigh the increased cost of early involvement. Shared risk and reward is also a key aspect of IPD through providing incentive to work collaboratively to meet common goals for the project and either reap the benefits together or share the losses equally. The sharing of risk and reward ties participants together and emphasizes a more balanced effort on meeting cost, time, and quality goals which avoids the tunnel vision tax of focusing on one of these goals and failing to meet the rest. Multi-party contracts are a fundamental component of IPD because it ties all the stakeholders together. In traditional delivery methods, the owner would likely hold separate contracts with the contractor and architect, but a multi-party contract holds all parties responsible to each other. Collaborative decision making and control is essential to ensuring all key participants are operating together in the best of interest of the project. Integrated projects have frequent meetings between the owner, architect/associated consultants, contractor/ key subcontractors. The objective of these meetings is to address any issues collectively and early to avoid further complication, while also focusing on the future of the project. Many integrated projects implement a committee approach to decision-making which is beneficial in being collaborative and consistent over the course of the project. The downside is that these committees are typically made up of core members from the key participants of the project, and it can be burdensome to gather them frequently. Building information technology [BIM] is a great tool used in IPD, which aids this collaborative process and accelerates the transfer of data between the parties to aid in making more collaborative decisions. Lastly, goals for the project must be developed jointly between the key participants to cultivate a common understanding of how the project is to be executed. Outlining these goals clearly and concisely will aid in decision making over the course of the project. Aligning these goals early is also important to ensure all participants are working towards these common goals as early as possible. Integrated Project Delivery in Industry Today IPD is being utilized more often and more effectively across the nation as owners, contractors, and architects are gaining experience utilizing this approach and prospective owners are becoming open to new delivery methods to meet more aggressive goals. IPD is being used on a wide variety of project which is allowing better research to be conducted on how IPD can be best utilized. The range of projects IPD has been implemented on allows us to better compare IPD against traditional delivery methods and how different variables like: project type, size of project, contract amount, and location play a significant role in the outcome of the project. Furthermore, how important the process of selection is for key participants based on their experience in IPD and relationships with other stakeholders for a project. Research published by Jonathan Cohen of the FAIA shows that IPD is gaining noticeable traction in the healthcare construction industry. Cohen believes this is due to, “owners’ focus on lean operations and whole systems thinking now considered “best practice” in healthcare delivery.” IPD has also been implemented on K-12, education, higher education, office work, and even government work. Federal construction projects are typically not conducted using IPD, but AECOM recently announced a plan to hire three thousand workers in the next six months. This news came after their decision to form a federal contracting division. AECOM said, “the goal of the new division is to utilize design-build and integrated project delivery on projects for its federal clients, which include the military, General Services Administration [GSA], and the State Department” (Slowey, 2017). This is an unprecedented move in the IPD market and will produce some interesting data regarding the how IPD mixes in with federal construction contract requirements and Federal Acquisition Regulation [FAR]. Federal Project Integrated Project Delivery Hybrid Procurement restrictions for federal projects are very strict and sometimes even hinder the quality of project delivery potential a project would have had it been pursued through a different delivery method. Under the Brooks Act and Federal Acquisition Regulation [FAR], design services are selected through a qualification-based selection process (GSA, n.d.). Firms competing for design contracts on federal projects are ranked based on their technical qualifications, and negotiations are conducted with the top ranked firm (GSA, n.d.). Construction contracts for federal projects under the prospectus level are awarded to the lowest responsive bidder through the traditional design-bid-build delivery method. Major federal construction contracts are selected through the FAR’s “Source Selection” Method (GSA, n.d.). There are some variations to the Source Selection method, but typically management proposals and a price proposal are requested from bidders. These proposals are evaluated “technically, and then evaluated in terms of price” (GSA, n.d.). The process does allow tradeoffs, but is selected on a best value basis rather than lowest price. Discussion and negotiation can occur to allows bidders to correct technical proposals and clarify pricing before the contract that is the best value for the government is selected (GSA, n.d.). Despite these strict procurement restrictions exceptions have been made for various federal projects to test different delivery methods and their success. The NGA New Campus East Engineer Proving Ground in Fort Belvoir, VA was an Integrated Design-Bid-Build [IDBB] project, which was similar to design-bid-build due to its contractual
Details
-
File Typepdf
-
Upload Time-
-
Content LanguagesEnglish
-
Upload UserAnonymous/Not logged-in
-
File Pages8 Page
-
File Size-