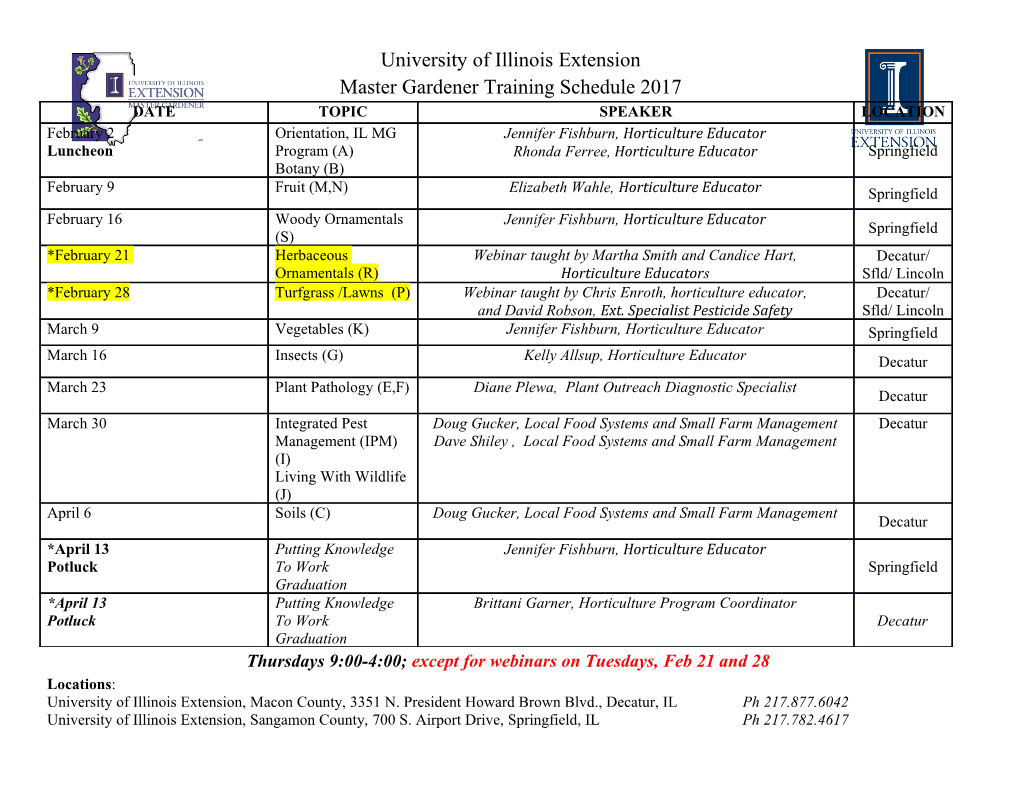
CHAPTER 10 Advances in understanding the fl ow in a centrifugal compressor impeller and improved design A. Engeda Turbomachinery Lab, Michigan State University, USA. Abstract The last 60 years have seen a very high number of experimental and theoretical studies of the centrifugal impeller fl ow physics at government, industry and uni- versity levels, which have been extensively documented. As Robert Dean, one of the well-known impeller aerodynamists stated, “The centrifugal impeller is prob- ably the most complex fl uid machine built by man”. Despite this, it is still the widest used turbomachinery and continues to be a major research and develop- ment topic. Computational fl uid dynamics has now matured to the point where it is widely accepted as a key tool for aerodynamic analysis. Today, with the power of modern computers, steady-state solutions are carried out on a routine basis, and can be considered as part of the design process. The complete design of the impeller requires a detailed understanding of the fl ow in the impeller and aerody- namic analysis of the fl ow path and structural analysis of the impeller including the blades and the hub. This chapter discusses the developments in the understand- ing of the fl ow in a centrifugal impeller and the contributions of this knowledge towards better and advanced impeller designs. 1 Introduction Centrifugal compressors have the widest compressor application area. They are reliable, compact, and robust; they have better resistance to foreign object dam- age; and are less affected by performance degradation due to fouling. They are found in small gas turbine engines, turbochargers, and refrigeration chillers and are used extensively in the petrochemical and process industry. The centrifugal compressor fi nds a wide variety of applications, with each application placing its own demands on the design of the compressor. Given this spectrum of application, WIT Transactions on State of the Art in Science and Engineering, Vol 42, © 2008 WIT Press www.witpress.com, ISSN 1755-8336 (on-line) doi:10.2495/978-1-84564-062-0/10 350 Thermal Engineering in Power Systems it is not surprising that the centrifugal compressor continues to command a great deal of attention, both from compressor designers and from those engaged in understanding the underlying engineering science. Industrial applications require stage pressure ratios of 1.5:1 or even less, whereas helicopter gas turbines require the highest pressure ratios, with 6:1 being common- place and the latest engines demanding 10:1 or more from a single compressor stage. Table 1 and Fig. 1 summarize the application areas of turbocompressors. The wide range of demands on centrifugal compressors brings many design considerations. Most of the design requirements need solutions to two major prob- lems: stress and aerodynamics. The stress problems are caused by the material strength limitations and the capability to accurately predict blade and impeller steady state and vibrational stress for complex impeller shapes and at high rota- tional speeds. The aerodynamic problem is to effi ciently accomplish large air defl ections and diffusion at high fl ow velocity, with the added diffi culty of very small passage fl ow areas required to get good effi ciency and high pressure ratio. Table 1: Application areas of turbocompressors. Pressure ratio Types of Operating compressors Industrial Aerospace Research Effi ciency range Positive Up to 30 – – 78–82% – displacement Centrifugal 1.2–1.9 2.0–7.0 13 75–87% Large 25% Axial 1.05–1.3 1.1–1.45 2.1 80–91% Narrow 3–10% Figure 1: Application areas of turbocompressors. WIT Transactions on State of the Art in Science and Engineering, Vol 42, © 2008 WIT Press www.witpress.com, ISSN 1755-8336 (on-line) Understanding the Flow in a Centrifugal Compressor Impeller 351 Based on one-dimensional (1D) streamline theory, the aerodynamic design of the centrifugal impeller has signifi cantly advanced in the last 60 years simply by using similitude, dimensional analysis, empirical knowledge, and control volume analysis. Most early codes were limited in their applicability in that they were only two-dimensional (2D), or in three dimensions capable of analyzing a single bladed passage or one bladed element. Analyses could include stationary or rotating elements but not both. The loss and/or turbulence models built into the codes were inadequate to properly model the complex fl ows encountered in cen- trifugal compressors. The codes were limited to relatively simple geometric and topological (mesh) confi gurations. Finally, solutions provided were steady state or time averaged, and unsteady effects were not usually considered. As user demands grew for improved performance and more reliable equipment and as compressor vendors sought improved analytical and design methodologies, the application of computational fl uid dynamics (CFD) in the industrial world became a necessity. Figure 2 shows typical centrifugal compressor impellers. As already mentioned, CFD has been used extensively over the past three decades to predict the perfor- mance of compressors for both single and multiple blade row confi gurations. As CFD algorithms and software have continued to be developed and refi ned, it remains essential that validation studies be conducted to ensure that the results are both suffi ciently accurate and can be obtained in a robust and predictable manner. The complete design of the impeller requires aerodynamic analysis of the fl ow path and structural analysis of the impeller including the blades and hub. A typical impeller design procedure follows the pattern of specifying blade and hub geom- etry, performing aerodynamic and structural analysis, and iterating on geometry until acceptable aerodynamic and structural criteria are achieved. This requires the geometry generation to focus not only on blade shape but also on hub geometry. Thus, for interactive blade design to be an effective design tool, iterations in blade geometry, aerodynamic analysis, and structural analysis must be completed in a timely manner. This requires an integrated design system that is easy to use and capable of controlling the complete rotor geometry, and aerodynamic and struc- tural analysis. To develop such a design system, it is critical that the impeller geometry generation procedure be clearly understood. Modern solvers use robust schemes, which can accurately predict compressible and viscous fl ows around and in complex geometries. Current impeller design systems integrate geometry generation with aerodynamic analysis. Such design systems allow for graphical geometry manipulation of the impeller cross-section shapes, area diffusion and distributions, and outline connections. Aerodynamic analysis is performed using CFD. The CFD mesh node spacing and boundary conditions are automatically generated from within such design system, thus elim- inating the need to manually setup third party mesh generators. Program output includes information for CAD and 3D viewing of the impeller. Currently two design approaches are practiced using CAD and CFD interactions: • CAD system approach • Design system approach WIT Transactions on State of the Art in Science and Engineering, Vol 42, © 2008 WIT Press www.witpress.com, ISSN 1755-8336 (on-line) 352 Thermal Engineering in Power Systems Figure 2: Examples of centrifugal impellers and modeling. WIT Transactions on State of the Art in Science and Engineering, Vol 42, © 2008 WIT Press www.witpress.com, ISSN 1755-8336 (on-line) Understanding the Flow in a Centrifugal Compressor Impeller 353 2 The historical development of the centrifugal impeller Prior to 1800, the centrifugal compressor was able to deliver only 1 m head of water. It was Rateau [1], in 1899, who fi rst showed that the centrifugal compressor can develop higher pressure and effi ciency than ever thought. He was able to show that a centrifugal compressor impeller can achieve a tip speed of 250 m/s or higher. He fi rst designed and tested a centrifugal compressor with an impeller of 250 mm diameter. This compressor developed 5.8 m head of water and 2000 m3/h inlet fl ow while operating at 264 m/s tip speed and 20,200 rpm rotational speed. Fol- lowing the success of this compressor, Rateau [1] designed two more centrifugal compressors. The fi rst one was in 1903 for the steel industry; it developed 3.4 m head of water and 10,000 m3/h inlet fl ow while operating at 14,500 rpm rotational speed. The second was a similar compressor in 1904 for a sugar refi nery. Just immediately before and after 1900, the major users of gas compressors were the steel and mining industries. As these industries grew, their demand for compressors with higher pressures increased. To respond to this need for higher pressure, Rateau [1] followed the experience from centrifugal pumps and designed the fi rst multistage centrifugal compressor. The fi rst known multistage centrifugal compressor was built in 1905 with fi ve stages on the same shaft. It was designed for 2500 m3/h inlet fl ow, 4 m head of water and 4500 rpm rotational speed. About the same time as Rateau [1], Parsons [2] was investigating axial com- pressors for gas turbine applications but results showed that this compressor was poor in terms of effi ciency and stability. Parsons [2] investigated some 30 differ- ent compressors and stopped the work with dissatisfaction. It took several decades afterwards to discover the superior qualities of the axial compressor. Following Rateau’s [1] success in the period 1905–1910, many compressor manufacturing companies licensed Rateau’s [2] patent. In the period 1910–1920, due to increased industrial application areas of the centrifugal compressor, the impeller designer focused more towards producing higher fl ow capacity, effi - ciency, and tip speed. Since the beginning of the 20th century the theory of hydrodynamics and aero- dynamics of centrifugal pumps and compressors has developed slowly. The major initial task was to establish the relationship between the performance parameters of the impeller, the form of the fl ow, and the form of the fl uid passages.
Details
-
File Typepdf
-
Upload Time-
-
Content LanguagesEnglish
-
Upload UserAnonymous/Not logged-in
-
File Pages24 Page
-
File Size-