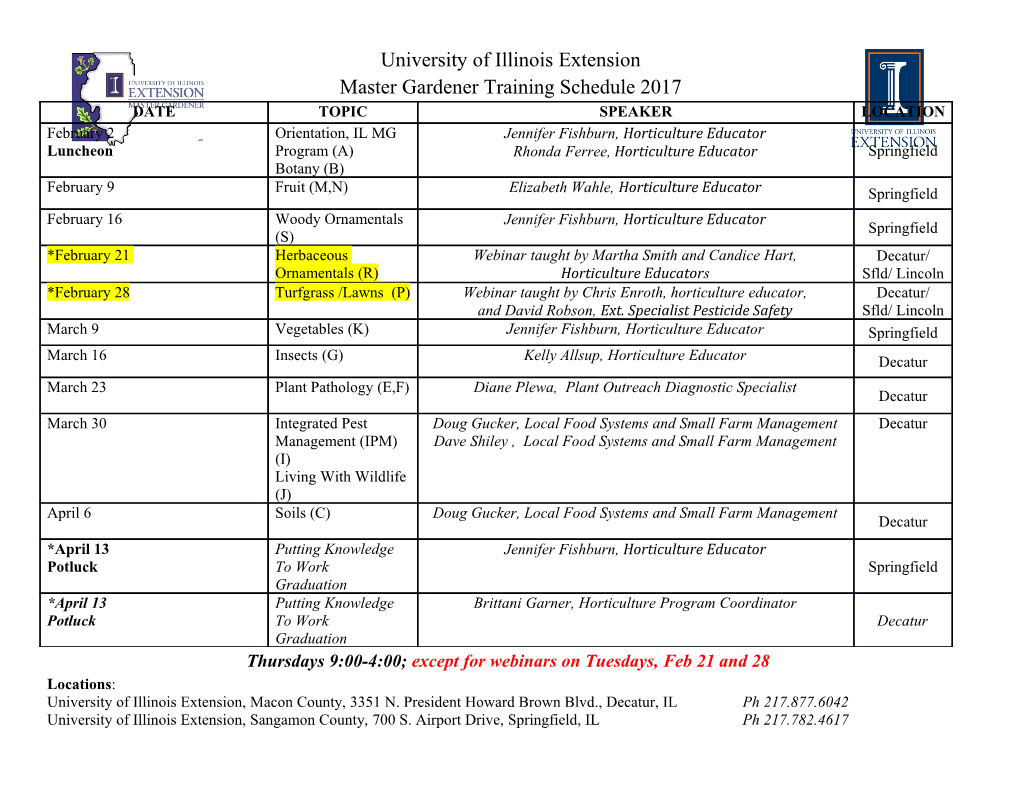
JUN 5 SANDIA REPORT SAND2000-1280 Unlimited Release Printed May 2000/^ Comprehensive Testing to Measure the Response of Butyl Rubber to Hanford Waste Simulant Prepared by / Sandia National Laboratories Albuquerque, New Mexico 87185 and Livermore, California 94550 Sandia is a multiprogram laboratory operated by Sandia Corporation, a Lockheed Martin-Company, for the United States Department of Energy under'ContracTDE-AC04-94AL85000. Approved for public release; further dissemination unlimited. Sandia National Laboratories Issued by Sandia National Laboratories, operated for the United States Department of Energy by Sandia Corporation. NOTICE: This report was prepared as an account of work sponsored by an agency of the United States Government. Neither the United States Government, nor any agency thereof, nor any of their employees, nor any of their contractors, subcontractors, or their employees, make any warranty, express or implied, or assume any legal liability or responsibility for the accuracy, completeness, or usefulness of any information, apparatus, product, or process disclosed, or represent that its use would not infringe privately owned rights. Reference herein to any specific commercial product, process, or service by trade name, trademark, manufacturer, or otherwise, does not necessarily constitute or imply its endorsement, recommendation, or favoring by the United States Government, any agency thereof, or any of their contractors or subcontractors. The views and opinions expressed herein do not necessarily state or reflect those of the United States Government, any agency thereof, or any of their contractors. Printed in the United States of America. This report has been reproduced directly from the best available copy. Available to DOE and DOE contractors from U.S. Department of Energy Office of Scientific and Technical Information P.O. Box 62 Oak Ridge, TN 37831 Telephone: (865)576-8401 Facsimile: (865)576-5728 E-Mail: [email protected] Online ordering: http://www.doe.gov/bridge Available to the public from U.S. Department of Commerce National Technical Information Service 5285 Port Royal Rd Springfield, VA 22161 Telephone: (800)553-6847 Facsimile: (703)605-6900 E-Mail: [email protected] Online order: http://www.ntis.gov/ordering.htm DISCLAIMER Portions of this document may be illegible in electronic Image products. Images are produced from the best available original document SAND2000-1280 Unlimited Release Printed May 2000 Comprehensive Testing to Measure the Response of Butyl Rubber to Hanford Tank Waste Simulant P. J. Nigrey Transportation Safety & Security Analysis Department Sandia National Laboratories P.O. Box 5800 Albuquerque, NM 87185-0718 Abstract This report presents the findings of the Chemical Compatibility Program developed to evaluate plastic packaging components that may be incorporated in packaging mixed-waste forms for transportation. Consistent with the methodology outlined in this report, we performed the second phase of this experimental program to determine the effects of simulant Hanford tank mixed wastes on packaging seal materials. That effort involved the comprehensive testing of five plastic liner materials in an aqueous mixed-waste simulant. The testing protocol involved exposing the materials to -143,286, 571, and 3,670 krad of gamma radiation and was followed by 7-, 14-, 28-, 180-day exposures to the waste simulant at 18, 50, and 60°C. Butyl rubber samples subjected to the same protocol were then evaluated by measuring seven material properties: specific gravity, dimensional changes, mass changes, hardness, compression set, vapor transport rates, and tensile properties. From the analyses, we determined that butyl rubber has relatively good resistance to radiation, this simulant, and a combination of these factors. These results suggest that butyl rubber is a relatively good seal material to withstand aqueous mixed wastes having similar composition to the one used in this study. ACKNOWLEDGMENTS The support of our sponsor, the U.S. Department of Energy, Office of Transportation (EM-24), is gratefully appreciated. Specifically, the encouragement provided by Arnie Justice and Mona Williams in the DOE National Transportation Program Office is acknowledged. The technical assistance provided by Tatianna G. Dickens was responsible for the timely completion of this work. CONTENTS ACKNOWLEDGMENTS 2 INTRODUCTION 7 TEST DESCRIPTION 11 Materials 11 Simulant Preparation 11 Sample Preparation 11 Sample Quantities 12 Sample Irradiation 13 Sample Exposure to Simulant 13 Experimental Approach 14 RESULTS 17 Specific Gravity 17 Dimensional Properties 18 Hardness Properties 20 Compression Set 22 Vapor Transport Rates 26 Tensile Properties 28 Tensile Strength 29 Elongation at Break or Ultimate Elongation 31 Tensile Stress or 100% Modulus 34 DISCUSSION 39 CONCLUSIONS 43 REFERENCES 45 APPENDIX A. BUTYL RUBBER MATERIAL INFORMATION 47 APPENDDC B. BUTYL RUBBER SPECIFIC GRAVITY DATA 48 APPENDLX C. BUTYL RUBBER MASS DATA 49 APPENDIX D. BUTYL RUBBER DIMENSIONAL DATA 50 APPENDIX E. BUTYL RUBBER HARDNESS DATA 52 APPENDIX F. BUTYL RUBBER COMPRESSION SET DATA 53 APPENDIX G. BUTYL RUBBER VAPOR TRANSPORT RATE DATA 54 APPENDIX H. BUTYL RUBBER TENSILE STRENGTH DATA 55 APPENDIX I. BUTYL RUBBER ULTIMATE ELONGATION DATA 56 APPENDIX J. BUTYL RUBBER TENSILE STRESS DATA 57 LIST OF FIGURES 1. Comprehensive Seal Testing Strategy 16 2. Specific gravity (S. G.) changes in butyl rubber after exposure to ~0, 143, 286, 571, and 3,670 krad of gamma radiation followed by exposure for 7 days (a), 14 days (b), 28 days (c), and 180 days (d) to the aqueous simulant waste at 18, 50, and 60°C 17 3. Mass changes in butyl rubber after exposure to ~0,143, 286, 571, and 3,670 krad of gamma radiation followed by exposure for 7 days (a), 14 days (b), 28 days (c), and 180 days (d) to the aqueous simulant waste at 18, 50, and 60°C 19 4. Volume (Vol.) changes in EPDM after exposure to ~0,143, 286, 571, and 3,670 krad of gamma radiation followed by exposure for 7 days (a), 14 days (b), 28 days (c), and 180 days (d) to the aqueous simulant waste at 18, 50, and 60°C 21 5. Hardness (Hard.) changes in butyl rubber after exposure to ~0, 143,286, 571, and 3,670 krad of gamma radiation followed by exposure for 7 days (a), 14 days (b), 28 days (c), and 180 days (d) to the aqueous simulant waste at 18, 50, and 60°C 22 6. Compression set fixture, (a) A partly assembled fixture with the 4.5 mm spacer bars and butyl rubber samples, (b) An assembled fixture with butyl rubber samples 23 7. Compression set (C. S.) changes in butyl rubber after exposure to -143, 286, 571, and 3,670 krad of gamma radiation followed by exposure for 7 days (a), 14 days (b), 28 days (c), and 180 days (d) at 18, 50, and 60°C 24 8. Compression set (C. S.) changes in butyl rubber after exposure to ~0,143, 286, 571, and 3,670 krad of gamma radiation followed by exposure for 7 days (a), 14 days (b), 28 days (c), and 180 days (d) to the aqueous simulant waste at 18, 50, and 60°C 25 9. Vapor Transmission Rate cells 27 10. VTR for butyl rubber after exposure to -0, 143, 286, 571, and 3,670 krad of gamma radiation followed by exposure for 7 days (a), 14 days (b), 28 days (c), and 180 days (d) to the aqueous simulant waste at 18, 50, and 60°C 28 11. Tensile strength (T. S.) changes in butyl rubber after exposure to -143, 286, 571, and 3,670 krad of gamma radiation followed by exposure for 7 days (a), 14 days (b), 28 days (c), and 180 days (d) at 18, 50, and 60°C 30 12. Tensile strength (T. S.) changes in butyl rubber after exposure to -0,143, 286, 571, and 3,670 krad of gamma radiation followed by exposure for 7 (a), 14 (b), 28 (c), and 180 days (d) to the aqueous simulant waste at 18, 50, and 60°C 32 13. Ultimate elongation (U. EL.) changes in butyl rubber after exposure to -143,286, 571, and 3,670 krad of gamma radiation followed by exposure for 7 days (a), 14 days (b), 28 days (c), and 180 days (d) at 18, 50, and 60°C 33 14. Ultimate elongation (U. EL.) changes in butyl rubber after exposure to ~0,143,286, 571, and 3,670 krad of gamma radiation followed by exposure for 7 (a), 14 (b), 28 (c), and 80 days (d) to the aqueous simulant waste at 18, 50, and 60°C 34 15. Tensile stress (T. ST.) changes in butyl rubber after exposure to -143, 286, 571, and 3,670 krad of gamma radiation followed by exposure for 7 (a), 14 (b), 28 (c), and 180 days (d) at 18, 50, and 60°C 36 16. Tensile stress (T. ST.) changes in EPDM after exposure to -0, 143, 286, 571, and 3,670 krad of gamma radiation followed by exposure for 7 (a), 14 (b), 28 (c), and 180 days (d) to the aqueous simulant waste at 18,50, and 60°C 37 This page intentionally left blank. INTRODUCTION Hazardous and radioactive materials packaging is designed to facilitate the transport and storing of materials without posing a threat to the health or property of the general public. U.S. regulations establish general design requirements for such packagings. While no regulations have been written specifically for mixed waste packaging, regulations for the constituents of mixed wastes, that is, hazardous and radioactive substances, have been codified by the U.S. Department of Transportation (U.S. DOT, 49 CFR 173) and the U.S. Nuclear Regulatory Commission (NRC, 10 CFR 71). The packaging materials and contents must be chemically compatible. Furthermore, Type A [49 CFR 173.412 (g)] and Type B (10 CFR 71.43) packaging design requirements stipulate that there be no significant chemical, galvanic, or other reaction between the materials and contents of the package.
Details
-
File Typepdf
-
Upload Time-
-
Content LanguagesEnglish
-
Upload UserAnonymous/Not logged-in
-
File Pages63 Page
-
File Size-