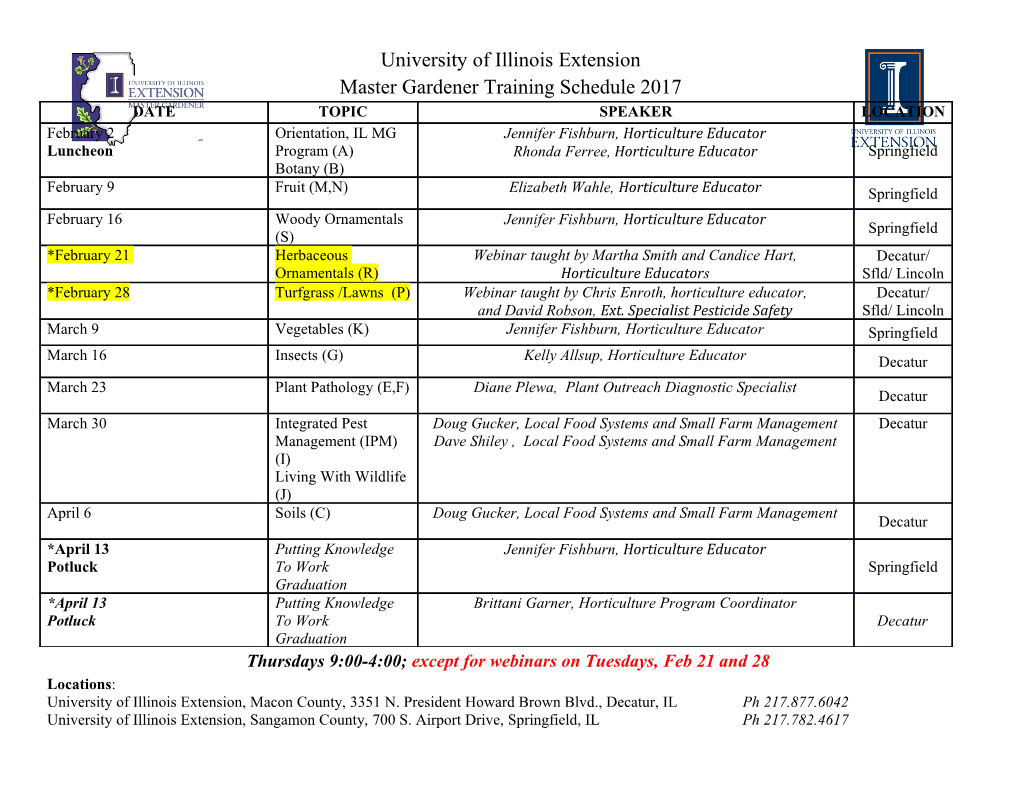
Hamilton et al Supp Sept 2010layout:Layout 1 8/12/10 10:49 AM Page 189 Characteristic Temperature Curves for Aluminum Alloys during Friction Stir Welding An empirically derived relationship between temperature and weld energy is used to predict maximum friction stir welding temperatures in aluminum alloys BY C. HAMILTON, S. DYMEK, AND A. SOMMERS Ulysse (Ref. 7) studied the impact of vary- ABSTRACT ing weld parameters on the temperature distribution in 7050-T7451 plate. Also, Review of published friction stir welding (FSW) data across numerous aluminum Khandkar et al. (Refs. 8, 9) introduced a alloys demonstrates that a characteristic relationship between the temperature ratio heat input model based on the torque of (the maximum welding temperature divided by the solidus temperature of the alloy) the FSW tool and successfully applied the and the energy per unit length of weld exists. When the temperature ratio is plotted as model to friction stir welded aluminum a function of the energy per unit length of weld, a linear relationship whose slope is de- 6061-T651 plate. pendent on the thermal diffusivity of the alloy is revealed. Utilizing these characteris- A commonality to each of these ap- tic curves, the maximum welding temperatures were estimated for Sc-modified Al-Zn- proaches, however, is the need to develop Mg-Cu alloy extrusions joined through FSW at 225, 250, 300, and 400 rev/min (all other a computer simulation to satisfactorily weld parameters held constant). The characteristic curves successfully predict the max- solve the heat transfer equation for the imum weld temperatures at the lower energy weld conditions, i.e., 225 and 250 rev/min, alloy and welding conditions of interest, but for the high-energy welds, 300 and 400 rev/min, the curves overpredict the maxi- and to calculate the thermal profile and mum weld temperatures. Despite this discrepancy, the characteristic curves demon- maximum welding temperature. To cir- strate that it is feasible to predict the maximum FSW temperature in an alloy if the cumvent this sometimes work-intensive thermal diffusivity, welding parameters, and tool geometry are known. process, Roy et al. (Ref. 10) utilized the Buckingham π-Theorem and proposed a dimensionless parameter based on mate- Introduction welds (Refs. 3, 4). Since its introduction, rial properties and process parameters to numerous investigations have sought to predict the maximum weld temperature during friction stir welding. Colegrove et Friction stir welding (FSW) is a novel characterize the principles of FSW and to al. (Ref. 11) also pursued a technique that solid-state joining process that is gaining model the microstructural evolution and would predict the heat generation in alu- WELDING RESEARCH popularity in the manufacturing sector temperature behavior. The current status minum alloys during FSW based solely on and, in particular, the aerospace industry of FSW research has been well summa- material properties, in particular the (Refs. 1, 2). Because no melting occurs rized by Mishra and Ma (Ref. 5). solidus temperature of the alloy and flow during FSW, the process is performed at Researchers have found success in stress. Defining the “contact radius” be- much lower temperatures than conven- modeling the heat transfer characteristics tween the tool and workpiece as a meas- tional welding techniques and circum- of FSW. For example, Frigaard et al. (Ref. ure of heat transfer efficiency between vents many of the environmental and 6) developed a finite difference thermal them, their work showed good agreement safety issues associated with these welding model for a moving heat source and cor- between predicted and experimental tem- methods. The plastic deformation and related the predicted temperature profile peratures when applied to 7449-T73, 2024- temperature profile during FSW produce with the measured temperature profile for T3, and 6013-T6 sheets. a microstructure characterized by a cen- friction stir welded 6082-T6 and 7108-T79 Through similar motivation to derive a tral weld nugget surrounded by a thermo- extrusions. Utilizing a visco-plastic model, more direct approach to predict friction mechanically affected zone (TMAZ) and stir welding temperatures in aluminum al- heat-affected zone (HAZ). The welded loys, the current investigation utilizes joint is fundamentally defect free and dis- KEYWORDS Khandkar’s torque-based heat input plays excellent mechanical properties model to develop a relationship between when compared to conventional fusion Friction Stir Welding the maximum welding temperature, Peak Temperature solidus temperature, and energy per unit C. HAMILTON ([email protected]) and Aluminum Alloys length of weld. This empirically derived A. SOMMERS are with Miami University, De- Specific Energy relationship generates temperature partment of Mechanical and Manufacturing En- Thermal Modeling curves characteristic to specific thermal gineering, Oxford, Ohio. S. DYMEK is with AGH diffusivities that correlate the tempera- University of Science and Technology, Faculty of ture ratio (the ratio of the maximum weld Metals Engineering and Industrial Computer Sci- ence, Kraków, Poland. temperature to the solidus temperature) WELDING JOURNAL 189-s Hamilton et al Supp Sept 2010layout:Layout 1 8/11/10 11:13 AM Page 190 ture data were used to verify the efficacy of the characteristic curves proposed from this investigation. Discussion Energy per Unit Length of Weld Because the weld velocity (vw), tool ro- tation speed (ω), and applied force (F) all influence the total energy imparted to the workpieces, the total heat input more ap- propriately indicates the welding condi- tions than any individual welding parame- ter. The energy per unit length of weld was derived by Khandkar (Ref. 8) from a torque-based model for which the total torque, Ttotal, is expressed as the sum of torque contributions from the tool shoul- der against the workpiece, bottom of the tool pin against thickness material, and pin surface against thickness material. For the FSW representation in Fig. 1, where ro is the radius of the tool shoulder, ri1 is the WELDING RESEARCH radius of the pin at the tool shoulder, ri2 is Fig. 1 — Friction stir weld configuration, tool coordinate system, and tool geometry. the radius of the pin at the pin bottom, h is the pin height, τ is the shear stress dur- ing welding, and F is the applied force, the total torque then becomes =+rroiτπ2 τ Trrdrrtotal ∫∫()()2 () with the weld energy. From these curves, More specific details of the tool design are ri1 0 ππτ+ 2 the maximum welding temperature may proprietary to EWI, but Mishra and Ma (22rdr ) ri h be estimated for a given aluminum alloy if (Ref. 5) have reviewed many of the com- To simplify the evaluation of Equation 1, the tool geometry, welding parameters, mon FSW tool designs that are indicative the taper of the welding pin is ignored, i.e., solidus temperature, and thermal diffusiv- of that utilized in this investigation. With r = r , and defining τ as the product of ity are known. a constant weld velocity of 2.1 mm/s and i1 i2 the coefficient of friction between the tool an applied force of 22 kN, unique welds and workpieces, μ, with the average pres- were produced at the following tool rota- Experimental Procedure sure (F/πr2), Equation 1 becomes tion speeds: 225, 250, 300, and 400 ⎛ 2 ⎞ For this investigation, Sc-modified Al- rev/min. Even though the applied force =+μ rroi TFtotal 2 ⎜ 2 h⎟ ()2 Zn-Mg-Cu billets (SSA038) were pro- during FSW was set to 22 kN, real-time ⎝ 3 ro ⎠ data from the welding trials revealed that duced by UES, Inc., through direct chill The coefficient of sliding friction between × the load oscillated as the machine contin- casting and then extruded as 50.4- 6.35- aluminum and steel depends on the tem- uously corrected the load toward the set mm bars. The chemical compositions of peratures produced by the welding condi- point. Consequently, the average load SSA038 is summarized in Table 1 along tions. Frigaard et al. (Ref. 6) reasoned that during welding deviated from the desired with that of aluminum 7075 for reference the coefficient of friction between alu- and comparison (Ref. 12). Following ex- set point; therefore, the average load was trusion, the bars were heat treated to a–T6 determined from the recorded data for temper through the following schedule: 1) each weld condition and was utilized in the solution heat treat at 460°C for one hour analysis of that condition. These average Table 1 — Chemical Compositions of followed by an additional hour at 480°C, 2) load values are 21.4, 20.1, 22.8, and 20.1 SSA038 with 7075 as Reference rapid quench in water to room tempera- kN for 225, 250, 300, and 400 rev/min, re- ture, and 3) age at 120°C for 19 h. The den- spectively. The recorded data verified that sity of SSA038 is 2820 kg/m3, and the the weld velocity remained constant at 2.1 Element Wt-% solidus temperature is 528°C. mm/s for all welding trials. SSA038 7075 After heat treatment, the bars were cut By utilizing a Mikron M7815 thermal Zn 7.11 5.60 into eight, 305-mm lengths and sent to the imaging camera during welding, the tem- Mg 2.14 2.50 Edison Welding Institute (EWI, Colum- perature profile across the weld was ex- Cu 1.56 1.60 bus, Ohio) to produce four friction stir perimentally recorded for each condition. Mn 0.25 0.30 welds in the configuration represented — The thermal emissivity for the infrared Zr 0.17 < 0.05 Fig. 1. As shown in the diagram, FSW oc- data was calibrated by imaging an extru- Sc 0.38 — curs along the L direction of the extrusions sion length heated to 460°C and adjusting Cr < 0.05 0.23 with a clockwise tool rotation.
Details
-
File Typepdf
-
Upload Time-
-
Content LanguagesEnglish
-
Upload UserAnonymous/Not logged-in
-
File Pages6 Page
-
File Size-