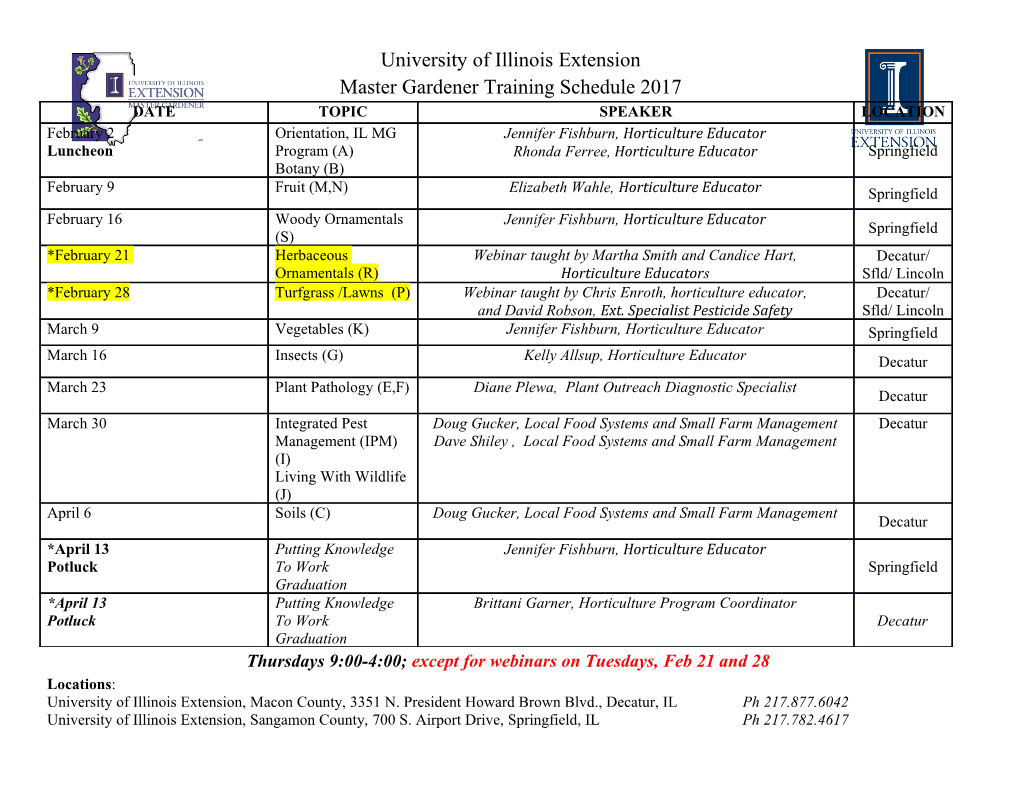
ADVISORY CIRCULAR 43-16A AVIATION MAINTENANCE ALERTS ALERT JULY NUMBER 2006 336 CONTENTS AIRPLANES BEECH ........................................................................................................................................1 CESSNA ......................................................................................................................................3 ENGINES LYCOMING................................................................................................................................3 CONTINENTAL .........................................................................................................................4 PRATT & WHITNEY .................................................................................................................4 ROLLS ROYCE ..........................................................................................................................6 PROPELLERS MC CAULEY ..............................................................................................................................8 ACCESSORIES ELECT. WIRE.............................................................................................................................9 ELECTROSYSTEMS................................................................................................................10 KELLY AEROSPACE ..............................................................................................................10 LAMAR TECHNOLOGY.........................................................................................................11 AIR NOTES ELECTRONIC VERSION OF FAA FORM 8010-4, MALFUNCTION OR DEFECT REPORT ....................................................................................................................11 PAPER COPY OF FAA FORM 8010-4, MALFUNCTION OR DEFECT REPORT..............11 INTERNET SERVICE DIFFICULTY REPORTING (iSDR) WEB SITE...............................12 IF YOU WANT TO CONTACT US.........................................................................................13 AVIATION SERVICE DIFFICULTY REPORTS ...................................................................13 July 2006 AC 43-16A U.S. DEPARTMENT OF TRANSPORTATION FEDERAL AVIATION ADMINISTRATION WASHINGTON, DC 20590 AVIATION MAINTENANCE ALERTS The Aviation Maintenance Alerts provide a common communication channel through which the aviation community can economically interchange service experience, cooperating in the improvement of aeronautical product durability, reliability, and safety. This publication is prepared from information submitted by those who operate and maintain civil aeronautical products. The contents include items that have been reported as significant, but have not been evaluated fully by the time the material went to press. As additional facts such as cause and corrective action are identified, the data will be published in subsequent issues of the Alerts. This procedure gives Alerts’ readers prompt notice of conditions reported via a Mechanical Reliability Report (MRR), a Malfunction or Defect Report (M or D), or a Service Difficulty Report (SDR). Your comments and suggestions for improvement are always welcome. Send to: FAA; ATTN: Aviation Data Systems Branch (AFS-620); P.O. Box 25082; Oklahoma City, OK 73125-5029. (Editor’s notes are provided for editorial clarification and enhancement within an article. They will always be recognized as italicized words bordered by parentheses.) AIRPLANES BEECH Beech (Raytheon): A36; Fuel Tank Bladder Contamination; ATA 2810 A repair station technician states, “A customer reported ‘white particles’ coming from the (aircraft’s) quick drains.” Two fuel bladders were removed and inspected: evidence of the white powder was found in various places in both tanks. They were replaced with new units from the original manufacturer who was made aware of the problem. (Part numbers provided are 2121-9-1 and 2121-10-2.) Part Total Time: 9.7 hours. Beech (Raytheon): E55; Failed Nose Gear Retraction Rod-End; ATA 3230 “After takeoff,” states this repair station technician, “the landing gear was retracted and a banging noise was heard by the pilot. It became apparent the nose gear retract mechanism had broken and that the nose gear did not retract properly. The aircraft was flown to its destination airport where the nose gear collapsed on landing—as expected. Investigation of the mechanism revealed a broken and spread rod-end (Beech P/N HMXL6FG) located under the landing gear transmission. (It is) connected to the nose landing gear push-pull tube (Beech P/N 36-820011-9). The probable cause (of this defect) is suspected to be an out-of-rig condition that eventually caused failure. No evidence of foreign objects was evident. Special inspections of rigging at regular intervals is recommended to avoid recurrence of this incident.” Part Total Time: (unknown). Beech (Raytheon): E90; Cracked Main Gear Torque Plate; ATA 3242 A mechanic states, “During a phase 1 and 2 inspection a crack was found in this Cleveland part attached to the R/H gear assembly. The crack is on the torque plate upper forward brake cylinder pin attach hole. A bushing installed in this hole has no sign of damage. Probable cause of cracking would be stress related.” (Torque plate P/N 075-15500.) Page 1 AC 43-16A July 2006 Part Total Time: 8,273.7 hours. Beech (Raytheon): 200; Broken Chain Link in Gear Extension: 3230 “The link in the landing gear extension chain was found broken and in the belly of the aircraft,” says this submitter. “This breakage prevented the extension of the nose gear.” (Connecting link P/N 131378-25-CL.) Part Total Time: (unknown). Beech (Raytheon): A200; Sheared Cabin Door Bolt; ATA 5210 (Not shown here are reference page copies that were included with this report: Beech C-12 Internal Parts Catalog 52-10-02 item 68 and Beech A200 52-10-02 item 122.) Page 2 July 2006 AC 43-16A A mechanic states, “During routine maintenance to replace the cabin door hardware (as required by the maintenance manual) a bolt was found sheared inside the (latch) bracket. (Bolt P/N NAS 1103-21D; Bracket P/N 50-430062-19.) There have been multiple SDRS (Service Difficulty Reports) of cabin doors opening in flight due to failure of similar hardware. We recommend replacement of the door latch mechanism (and its) pins and bolts at 5,000 cycles rather than the manufacturer’s recommended 10,000 cycles.” Part Total Time: (unknown). Beech (Raytheon): B200; Loose Elevator Torque-Tube Rivets; ATA 2730 The mechanic writing this report describes finding free play in the L/H elevator. “(I) found the L/H elevator torque tube (P/N 101-610019-5) mounting flange—from the tube assembly (itself) to the elevator (structure)— with its rivets working loose. This allowed the elevator to have 1.5 inches of play. This (defect) was found during a 400 hour lubrication inspection. The recommendation to prevent reoccurrence is (for the manufacturer) to use solid rivets, not blind rivets.” Part Total Time: 3,808.4 hours. CESSNA Cessna: 210; Cracked Hydraulic Line; ATA 2910 A landing gear hydraulic line described as the (door open line) failed, resulting in the aircraft landing with the main landing gear up. The submitting mechanic states, “The ferule on the nose landing gear door open line cracked along stress risers created by a flaring tool vice. (This) resulted in loss of hydraulic fluid to operate the landing gear.” (The part number for this line was not provided. This defect is yet another example of little things creating great consequences. SDRS data reflects at least three similar failures.) Part Total Time: (unknown). Cessna: 560XL; Arcing Fuel Level Switch; ATA 2842 A submitter describes the following difficulty with a fuel level switch. “The right low fuel level system was inoperative. (I) removed the switch and found signs of arcing on the top side of the switch. (I) troubleshot further and found the PC (printed circuit) board was defective. It is not known if the switch damaged the PC board. This is not the first time we have seen a defective float switch with signs of arcing. However, it is the first time that a damaged PC board was associated with it. It was noted when the float switch is in the ‘high fuel level’ position the contact surfaces are aligned. When the switch is in the ‘low fuel level’ the contacts are (almost) completely misaligned.” (Part number for this switch is 99144272.) Part Total Time: 2,291.0 hours. ENGINES LYCOMING Lycoming: O-320-E3D; Premature Camshaft Wear; ATA 8520 “During an annual inspection, ferrous metal flakes were found in the oil filter,” states the submitter. “Several pieces (were also) found in the finger strainer. (All of these pieces) were sent to Textron Lycoming for analysis. It was reported by them that the ferrous metal came from the camshaft and tappet bodies. The engine was removed Page 3 AC 43-16A July 2006 for overhaul. Time since overhaul is 2,092.9 hours. The camshaft was replaced at 1,164.4 hours since overhaul. Total time on the Camshaft is 928.5. The average oil change interval since overhaul is 91 hours. (I) recommend the 50 hour oil change interval recommended by Textron Lycoming be strictly adhered to.” (The camshaft P/N LW-18837 returns five additional entries from SDRS data.) Part Total Time: 928.5 hours. Lycoming: O360 A4M; Premature Camshaft Wear; ATA 8520 Quite similar to the previous report, another mechanic writes, “At annual inspection, metal was found in the oil filter. The engine was torn down and the camshaft and lifter bodies
Details
-
File Typepdf
-
Upload Time-
-
Content LanguagesEnglish
-
Upload UserAnonymous/Not logged-in
-
File Pages192 Page
-
File Size-