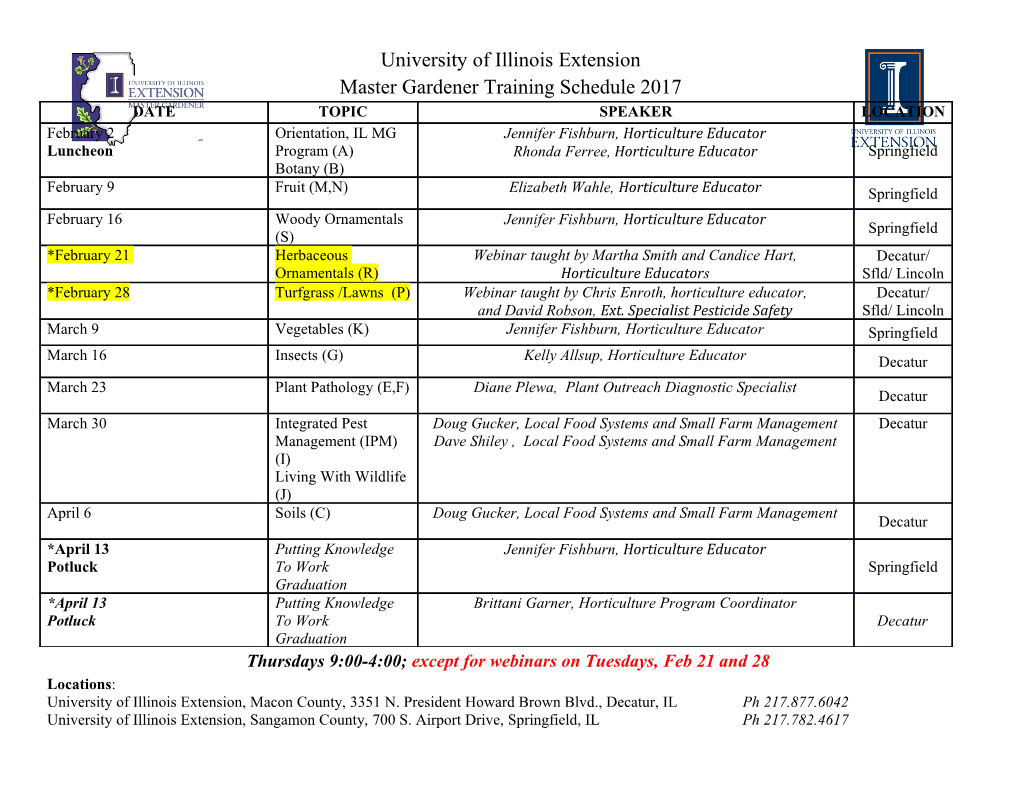
ASM Handbook, Volume 15: Casting Copyright © 2008 ASM International® ASM Handbook Committee, p 667-673 All rights reserved. DOI: 10.1361/asmhba0005257 www.asminternational.org Centrifugal Casting Sufei Wei, The Centrifugal Casting Machine Company, and Steve Lampman, ASM International CENTRIFUGAL CASTING is one of the density and freedom from oxides, gases, and the rotating mold. For example, with a vertical largest casting branches in the casting industry, other nonmetallic inclusions. When casting mold axis, the resultant force on the liquid is accounting for 15% of the total casting output solid parts, the pressure from rotation allows constant. This is not the case in a horizontal of the world in terms of tonnage. Centrifugal thinner details to be cast, making surface details mold. The other difference between horizontal casting was invented in 1918 by the Brazilian of the metal-cast components more prominent. and vertical mold orientation is the speed Dimitri Sensaud deLavaud, after whom the pro- Another advantage of centrifugal casting is the obtained by the molten metal as it spins around cess was named. DeLavaud’s invention elimi- elimination or minimization of gates and risers. the mold. When metal is poured into the hori- nated the need for a central core in the pipe zontally rotating mold, considerable slip occurs mold, and the mold was water cooled, allowing between the metal and the mold such that the for a high rate of repeated use. The technique Centrifugal Casting Methods metal does not move as fast as the rotating uses the centrifugal force generated by a rotat- mold. To overcome this inertia, the metal must ing cylindrical mold to throw molten metal Centrifugal casting machines are categorized be accelerated to reach the mold rotation speed. against a mold wall to form the desired shape. into three basic types based on the direction of This is not a problem in the vertical centrifugal Therefore, a centrifugal casting machine must the spinning axis: horizontal, vertical, or process, where the molten metal reaches the be able to spin a mold, receive molten metal, inclined. Centrifugal casting processes also have speed of the mold soon after pouring. However, and let the metal solidify and cool in the mold three types (Fig. 1): with a vertical mold axis, there is a tendency in a carefully controlled manner. for the molten metal to form a parabolic shape All metals that can be cast by static casting True centrifugal casting (horizontal, vertical, due to the competing gravitational and centrifugal can be cast by the centrifugal casting process, or inclined) forces. including carbon and alloy steels, high-alloy Semicentrifugal (centrifugal mold) casting corrosion- and heat-resistant steels, gray iron, Centrifuge mold (centrifugal die) casting ductile and nodular iron, high-alloy irons, True Centrifugal Casting stainless steels, nickel steels, aluminum alloys, The latter two methods are only done with copper alloys, magnesium alloys, nickel- and vertical spinning. This method, also referred to as just centrifu- cobalt-base alloys, and titanium alloys. Non- Horizontal centrifugal casting is mainly used gal casting, is characterized by an outer cylin- metals can also be cast by centrifugal casting, to cast pieces with a high length-to-diameter drical mold with no cores. The process can be including ceramics, glasses, plastics, and virtu- ratio or with a uniform internal diameter. Prod- vertical, horizontal, or inclined (Fig. 1). The ally any material that can be made into liquid ucts include pipe, tubes, bushings, cylinder permanent mold is rotated about its axis at high or pourable slurries. Centrifugal castings can sleeves (liners), and cylindrical or tubular speeds (300 to 3000 rpm), so that the molten be best described as isotropic, that is, having castings that are simple in shape. On the other metal is forced to the inside mold wall, where equal properties in all directions. This is not hand, vertical centrifugal casting is mainly for it solidifies. The casting is usually very fine true of a forging, rolling, or extrusion. castings with a low length-to-diameter ratio grained on the outer diameter, while the inside The centrifugal technique is used primarily (except vertically cast extralong rolls) or with diameter has more impurities and inclusions for the production of hollow components, but a conical diameter. The product range for that can be machined away. centrifugal casting is used to create solid parts. vertical centrifugal casting machines is wider, Centrifugal casting is used to produce cylin- The centrifugal casting process is generally pre- because noncylindrical (or even nonsymmetri- drical, tubular, or ring-shaped castings. The ferred for producing a superior-quality tubular cal) parts can be made using vertical centrifugal need for a center core is completely eliminated. or cylindrical casting, because the process is casting. All vertical centrifugal castings have Castings produced by this method will always economical with regard to casting yield, clean- more or less taper on their inside diameters, have a true cylindrical bore or inside diameter, ing room cost, and mold cost. The centrifugal depending on the gravitational (g) force applied regardless of shape or configuration. The bore force causes high pressures to develop in the to the mold and the casting size. The inclined of the casting will be straight or tapered, metal, and it contributes to the feeding of the centrifugal casting machine bears advantages depending on the horizontal or vertical spinning metal, with separation from nonmetallic inclu- and disadvantages of both horizontal and verti- axis used. Castings produced in metal molds by sions and evolved gases. In centrifugal casting cal castings and can be very useful in certain this method have true directional heat flow, of hollow sections, nonmetallic inclusions and applications. facilitating a planar solidification front move evolved gases tend toward the inner surface of Although both vertical and horizontal from the outside of the casting toward the axis the hollow casting. By using the outstanding methods employ centrifugal force, there are of rotation. This method results in the produc- advantage created by the centrifugal force of some differences in how the force is applied tion of high-quality, defect-free castings with- rotating molds, castings of high quality and with respect to the axis of the mold rotation out shrinkage, which is the largest single integrity can be produced because of their high and the speed of the molten metal relative to cause of defective sand castings. 668 / Centrifugal Casting Horizontal true Vertical true Dimensional flexibility: Horizontal centrifu- centrifugal casting centrifugal casting gal casting allows the manufacture of pipes with maximum outside diameters close to 1.6 m (63 in.) and wall thicknesses to Molten Gate metal 200 mm (8 in.). Tolerances depend on part Mold size and the type of mold used. Quality: The centrifugal action removes Mold unwanted inclusions, dross, cleaner casting, and material that contains shrinkage, which Wheel can be machined away. Class I castings can Drive be produced without the need for upgrading and costly weld repairs. Vertical semi-centrifugal Properties: Mechanical properties are often Inclined true (centritugal-mold) casting superior to those of static castings due to the centrifugal casting finer grains resulting from the process, which Mold Integral tube are of constant size in circumferential and axial directions. Due to cleanliness and finer Flasks Cope grain size, good weldability is achieved. Drag Semicentrifugal (Centrifugal Mold) Casting In semicentrifugal casting (Fig. 1), a mold is rotated around its axis of symmetry. Cast con- figurations may be complex, determined by the shape of the mold. Molds for semicentrifu- Centrifuge gal casting often contain cores for production casting of internal surfaces. Directional solidification is obtained only by proper gating, as in static Molten casting. Castings that are difficult to produce metal statically can often be economically produced by this method, because centrifugal force feeds Mold Casting the molten metal under pressure many times higher than that in static casting. This improves casting yield significantly (85 to 95%), com- pletely fills mold cavities, and results in a high-quality casting free of voids and poros- ity. Thinner casting sections can be produced with this method than with static casting. Typi- cal castings of this type include gear blanks, pulley sheaves, wheels, impellers, cogwheels, and electric motor rotors. The centrifugal force is used for slag separation and refilling of melt. Fig. 1 Methods of casting with rotating molds. True centrifugal casting (top row) can be horizontal, vertical, or at an incline. Semicentrifugal and centrifuge die casting are vertical methods with molds that can be designed to produce solid parts. Centrifuge (Centrifugal Die) Casting Centrifugal mold or die casting, also referred to as centrifuge casting, has the widest field of Centrifugal casting is also the preferred Advantages of centrifugal casting include: application. This casting method is typically method for Babbitting medium- and thick-wall, used to produce valve bodies and bonnets, half-shell or full-round (nonsplit) journal bear- Flexibility in casting composition: Centrifu- plugs, yokes, brackets, and a wide variety of ings, because it virtually eliminates porosity gal casting is applicable to nearly all compo- various industrial castings.
Details
-
File Typepdf
-
Upload Time-
-
Content LanguagesEnglish
-
Upload UserAnonymous/Not logged-in
-
File Pages7 Page
-
File Size-