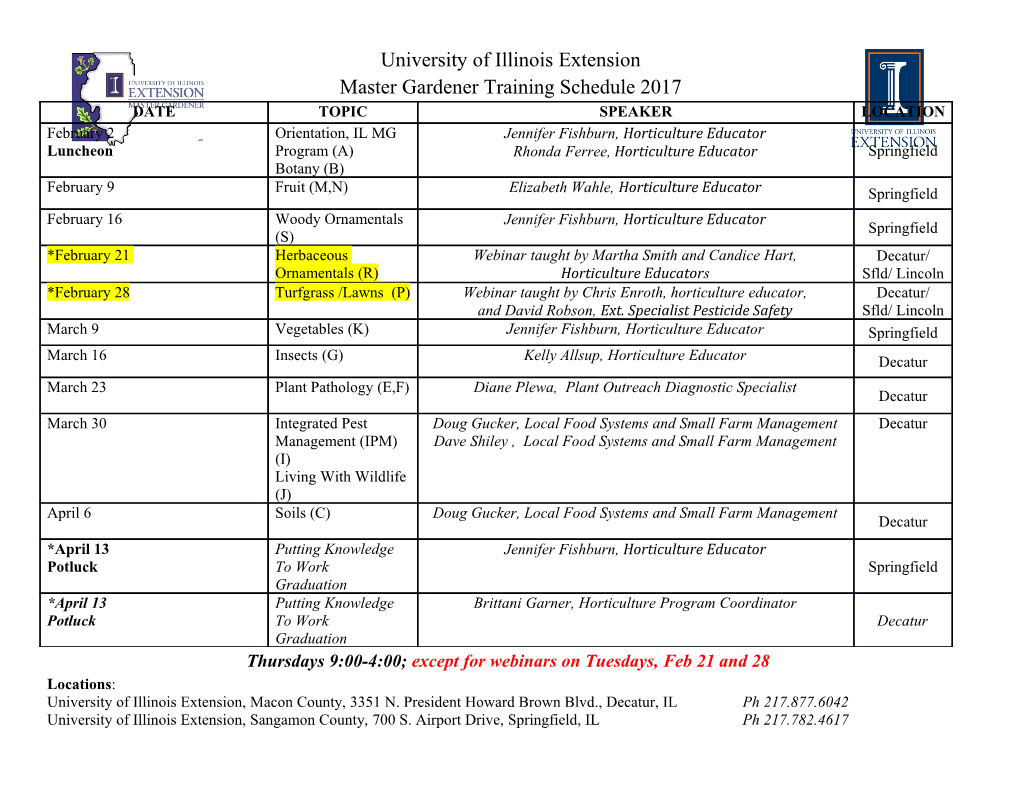
TWO LAYERED BALLAST SYSTEM FOR IMPROVED PERFORMANCE OF RAILWAY TRACK CHAITANYA CALLA A thesis submitted in partial fulfilment of the University’s requirements for the Degree of Doctor of Philosophy December 2003 Coventry University Abstract Considerable evidence suggests that, ballast is the main cause of uniform and non- uniform settlement of ballasted railway track, provided the subgrade is adequately specified. The requirement of a good track is that the sleepers are firmly supported by the ballast bed but over a period of time uneven settlement of the ballast will cause voids to form under the sleepers leading to unacceptable ride quality of track. Voids below sleepers can lead to major track defects and in worst cases can be the cause of vehicle derailment (Ball 2003, Cope and Ellis 2001- p206). Regular maintenance is required to remove voids below sleepers and correct other track geometry faults for smooth, safe and efficient running of the railways. The fundamental principle of track maintenance is to lift the track wherever it is low and pack ballast firmly under the sleepers ( Tazwell 1928, Frazer 1938, Cope and Ellis 2001 - p231). Track maintenance has evolved from manual methods of track maintenance, beater packing and measured shovel packing, of early railways to today’s sophisticated mechanised automated systems of maintenance, tamping and stoneblowing, but the basic principles of maintenance still remain the same. Beater packing or tamping works by compressing existing ballast below and around the sleepers into the void below the sleeper while in measured shovel packing and stoneblowing new stones of smaller size are introduced into the void below the sleeper. Ideally ballast below sleepers once compacted by traffic should be left undisturbed, which is the case for measured shovel packing and stoneblowing techniques of maintenance but beater packing and tamping disturbs ballast below the sleepers (Tratman 1909 - p361, Cope and Ellis 2001 – p260). The durability of track geometry of track maintained by the stoneblower is higher, but tamping still remains the preferred option as opposed to stoneblower for track maintenance (Ball 2003). Both stoneblowing and tamping require expensive on-track plant and are expensive to carry out, overall a large percentage of the railway budget is spent on ballast maintenance (Ball 2003). 2 The proposed two layered ballast system described in this thesis replaces the crib ballast around the sleepers by stones of size smaller than standard railway ballast. The aim is to fill the voids below the sleepers before they become unacceptably large, without use of expensive plant or manual intervention. Model and full scale laboratory tests carried out using the proposed two layered ballast system have demonstrated that with smaller stone as crib ballast (ballast around the sleepers) a void below the sleeper will be filled up to the average particle size of the crib ballast, by smaller crib ballast particles flowing into the void below the sleeper (Claisse et al 2002, Claisse and Calla 2003). The system is self- maintaining and does not require manual intervention or use of mechanical tools or plant once the smaller ballast has been placed in the crib. 3 ACKNOWLEDGEMENTS Work on this thesis has been carried out under the guidance of Dr Peter Claisse and late Dr Michael Keedwell. The author wants to express his deep and sincere gratitude to his guides Dr Claisse and Dr Keedwell for giving him the opportunity to work on this project and for their invaluable guidance and deep insight into the subject. The research project has been funded by Balfour Beatty Rail Company and RMC Concrete products and the author would like to thank Tony Darroch of RMC and Charles Penny of Balfour Beatty Rail for their invaluable advice on various practical aspects of this project. The author is grateful to the technicians at the School of Science and the Environment for their support and encouragement throughout the project. The author also wants to thank Austin Reeves and Jim McCartney for their cooperation and support while writing the thesis. 4 Contents Page Abstract ii Acknowledgements iv Contents v List of figures xiii List of tables xxiii Executive Summary xxv 1. Introduction 1.1 Two layered ballast system 2 2 Literature review 2.1 Introduction 5 2.2 Rails 6 2.3 Sleepers 7 2.4 Ballast 11 2.4.2 Ballast depth 12 2.4.2 Material for ballast 15 2.4.3 Ballast size 16 2.4.4 Ballast fouling and drainage 17 2.5 Ballast and track geometry deterioration 19 5 2.5.1 Voids below sleeper 21 2.5.1.1 Wet spots and ballast failure 26 2.5.1.2 Twist faults and cyclic tops 28 2.5.1.3 Track geometry measurement and analysis 30 2.6 Track maintenance 33 2.6.1 Beater packing 34 2.6.2 Ordinary and measured shovel packing 35 2.6.3 Mechanised tamping 38 2.6.3.1 Use of hand held tamping tools 38 2.6.3.2 Use of fully mechanised automatic tamping machines 38 2.6.4 Pnuematic ballast injection machines (Stoneblowers) 50 2.6.4.1 Hand held stoneblowing machines 50 2.6.4.2 Mechanised pneumatic ballast injection machines 52 2.6.5 Dynamic track stabiliser and crib and shoulder surface compactor 59 2.7 Ballast specification – a historical perspective and present problems 61 2.7.1 Ballast material 61 2.7.2 Ballast size 63 2.8 Railway track loads 67 2.9 Ballast settlement equations 69 2.10 Model and full scale testing of ballast 73 2.10.1 Box test by Selig et al 73 2.10.2 Box test by Anderson et al 76 6 2.10.3 Model test by Ishikawa et al 77 2.11 Alternatives to conventional ballasted track 78 3 Measurement and virtual instrumentation 3.1 Introduction 83 3.2 Data acquisition instruments 83 3.3 DAQ drivers or driver softwares 84 3.4 Application software 86 3.4.1 Front panel and block diagram 87 3.4.2 Functions 90 4 Laboratory test set up 4.1 Introduction 97 4.2 Simple and uplift cycles 98 4.3 Model test set up 100 4.3.1 Model test components 101 4.3.1.1 Sleepers 102 4.3.1.2 Ballast and subgrade 103 4.3.1.4 Types if runs 108 4.3.1.5 Problems with oil pressure 112 4.3.2 Virtual instrumentation of model test set up 114 4.3.2.1 Calibration of compression machine and displacement 115 transducer 7 4.3.2.2 Labview control panel 117 4.3.3 Data processing 120 4.3.4 Instrumented sleeper 124 4.3.4.1 Computer set up for the instrumented sleeper 126 4.3.4.2 Calibration of strain gauges 127 4.4 Box test set up 136 4.4.1 The ballast box 136 4.4.2 Hardware set up for the test 138 4.4.3 Ballast for box test 140 4.5 Test set up for full scale laboratory test 140 4.5.1 Sleeper, rail and ballast 141 4.5.2 Boundary conditions 141 4.5.3 Displacement measurement 144 4.5.4 Simple and uplift cycles 144 5 Model test results 147 5.1 Observations from two dimensional glass model 148 5.2 Model tests 149 5.2.1 Tests on monoblock sleepers 150 5.2.1.1 Initial tests on the two layered ballast system- Type A runs 150 5.2.1.1.1 Observations on the initial tests 152 5.2.1.1.2 Discussion 155 5.2.1.2 Effect of sleeper spacing – Type A runs 156 8 5.2.1.2.1 Observations 158 5.2.1.2.2 Discussion 162 5.2.1.3 Effect of crib ballast particle size and uplift height in uplift cycles 162 5.2.1.3.1 Uplift height 163 5.2.1.3.1.1 Observations 165 5.2.1.3.2 Particle analysis 168 5.2.1.3.2.1 Observations 170 5.2.1.3.3 Discussion 172 5.2.1.4 Effect of bottom ballast size and grading on the two layered ballast system 173 5.2.1.4.1 Effect of bottom ballast grading 173 5.2.1.4.2 Effect of bottom ballast size 174 5.2.1.4.2.1 Observation 175 5.2.1.5 Uplift equal to displacement cycles 176 5.2.1.5.1 Observations 178 5.2.1.6 Tests with different configuration of simple and uplift cycles – Type B runs 179 5.2.1.7 Tests on twin block sleepers 183 5.2.3 Tests on steel sleepers 186 5.2.3.1 Initial testing 186 5.2.3.2 Comparison of results for 5mm and 2mm crib ballast 188 5.2.4 Tests on instrumented sleeper 189 9 6 Full scale test results 193 6.1 Box test 6.1.1 Tests with 50mm bottom ballast and 50mm crib ballast 194 6.1.1.1 Observations 195 6.1.2 Tests with 50mm bottom ballast and smaller crib ballast 196 6.1.2.1 Test with 20mm crib ballast 196 6.1.2.1.1 Observations 197 6.1.2.2 Box test with 5mm crib ballast 201 6.1.3 Tests with 20mm bottom and crib ballast 205 6.1.3.1 Observations 205 6.1.4 Test with graded ballast 206 6.1.4.1 Observations 209 6.2 Full scale test on a single sleeper and rail assembly 211 6.2.1 Initial tests with sleeper spacing 550mm 211 6.2.1.1 Observations 213 6.2.2 Tests with sleeper spacing 600mm 215 6.2.2.1 Test with 50mm bottom and 20mm crib ballast 215 6.2.2.2 Tests with 50mm bottom ballast and different sizes of crib ballast 220 6.2.2.2.1 Test with 20mm stone and sand as crib ballast 221 6.2.2.2.2 Test with 10mm and 5mm crib ballast 225 6.2.2.3 Test with 20mm top and bottom ballast 227 10 6.2.2.3.1 Observations 228 6.2.2.4 Test to simulate the stoneblowing machine design uplift 231 6.2.2.4.1 Observations 233 6.2.3 Tests with sleeper spacing at 800mm 235 6.2.3.1 Observations 236 7 Discussion on results 7.1 Introduction 237 7.2 Ballast compression under sustained cyclic loading 238 7.2.1 Observations 239 7.3 Sleeper height gain in uplift cycles for Type A runs 240 7.4 Observations on empirical analysis and discussion on results 252 7.4.1 A maximum (Am) Vs A empirical (Ae) 252 7.4.2 Parameter – Sleeper spacing 253 7.4.3 Parameter – Uplift height and crib ballast particle size 258 7.4.3.1 Model tests carried out without bottom ballast on sandpaper 258 7.4.3.2 Full scale tests (including box tests) 260 7.4.4 Constant c and B 261 7.4.4.1 Effect of sleeper spacing on constant c in model
Details
-
File Typepdf
-
Upload Time-
-
Content LanguagesEnglish
-
Upload UserAnonymous/Not logged-in
-
File Pages332 Page
-
File Size-