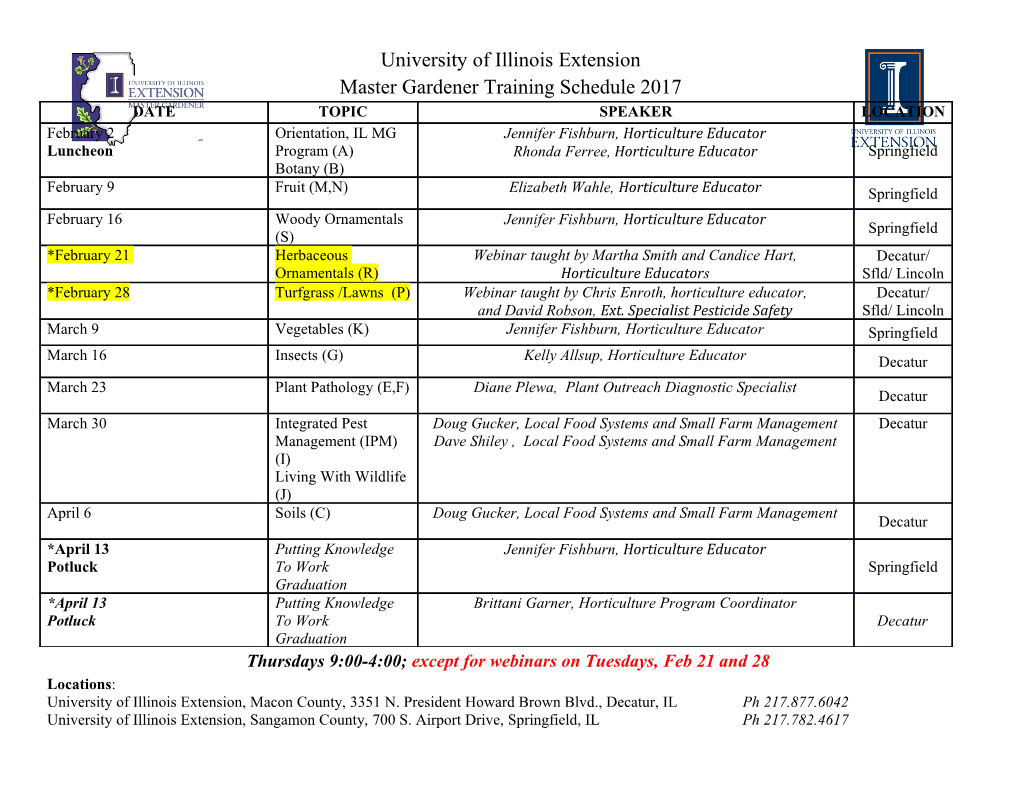
Digital Transformation in Process Distributed Control Systems (DCS) Discover how our customers and some of your process skids builders realized significant benefits through digitalization of their production processes. www.rockwellautomation.com Dear reader, Therefore, we have assembled a mix of different examples in different industries showcasing how customers’ issues turned into an improvements for their business. To achieve our customers’ goals, it’s clear that a digital plant is no longer contained within the walls of the plant itself, but instead stretches to the complete supply chain – from raw materials to the shops where consumers can order or buy their products. When looking at a digital plant, it is clear that a separate DCS system is no longer an option, instead an integrated digital DCS is required to I’m inviting you to discover how we, at not only quickly meet these flexible production Rockwell Automation, are enabling the industry demands, but also to play a much larger role in to realize the benefits from digitalizing their the digital factory of the future. This is backed factories and process skids. up by one customer, who told us “doing the The need to adopt digitalization in the face same we did five years ago would set us back of ever-changing consumer behaviour puts 20 years, so we need to digitalize our plants increased pressure on manufacturers of tomorrow.” products and their suppliers. While we provide a better insight in some A key market trend is that consumers demand key industry trends, we trust you also find it greater variety and more intuitive tailored beneficial to read through the different blogs Product selection combined with instant highlighting our solutions to respond to delivery. market trends. While in the past consumers would select only Thanks you for taking the time to read through what they wanted based on what was available our joint achievements and do not hesitate to on the shelf, now we are seeing them check all contact me for any question. the options online before getting confirmation on availability and then ordering from multiple Friendly yours sources – at the best available prices. Alain Hermans Indeed, our customers are telling us that demand for higher variability by consumers is Process Business Leader, EMEA accelerating the adoption of new technology at Rockwell Automation. for process control. Email: [email protected] 3 Contents Introduction 3 Need to Need to modernize Need to address growing aging systems 5 customer demands 27 modernize Anchor Glass 6 corosys 28 Azov Controls and Zaporizhstall 7 DELIN Elettronica 29 College Station Water Services (CSWS) 8 KCC 30 aging systems Columbia Pipeline Group 9 ProLabNL 31 Du Pont 10 Quimikao 32 Energy Control Technologies (ECT) 11 Blog: Gelatine production 12 Stemming the Next Pandemic 33 Kraft Heinz 13 Optima Control Solutions 14 Tata Steel 15 Tereos France 16 Blog: Time to Move Beyond Aging Assets 17 Need for open, Process skid solutions 35 scalable and secure Bausch+Ströbel 36 solution that meets Dinnissen Process Technology 37 all the requirements 19 Feluwa 38 Frames 39 AB electric 20 FrymaKoruma 40 Liquid Petroleum Distributor 21 IMA Automation 41 Prodesa 22 IMA Automation 42 Petroecuador 23 Zellwag 43 Tradebe 24 Zeton 44 Blog: Zippe 45 Peace of Mind 25 4 5 Anchor Glass Azov Controls and Zaporizhstall Food & Beverage In addition to serving the beverage Metals Zaporizhstal PJSC turned to Ukraine- industry with a variety of shapes, colors based Rockwell Automation. and sizes of glass bottles, Anchor Glass Recognised System Integrator, also produces glass containers for jams, Azov Controls LLC, to not only replace sauces and salsa for food and beverage and build the control systems for its companies around the world. fifth and sixth sinter strands, but also Anchor Glass facility in Minesota, US design and populate a brand new produces up to 600 bottles per minute. central control room. Challenges Solutions Challenge Solutions PlantPAx® Modern DCS A Rockwell Automation Integrated Process An aging furnace was causing • Single, scalable, plantwide process control Ageing control infrastructure at control system was installed, which included: energy inefficiencies and threating system Ukrainian sinter plant unable to • OWS stations productivity at a Minnesota Anchor • Process historian improves access to real- leverage modern data-driven • EWS Stations with integrated design tools Glass facility. time and historical data, and automated process advances. • Industrial Ethernet switches reporting capabilities • Multiple EtherNet/IP-based device level rings The inability to see more than two • System tracks most frequent alarms and (DLR) prioritizes for easier operator response weeks’ worth of production data • Integrated Safety • Internal model control system improved limited monitoring and trending • Connected variable speed AC & DC drives capabilities. management of furnace thermal operations • Stone Technologies implemented virtualized Results PlantPAx® modern DCS • Modern connected automation solution for Results sinter plant • Brand new central control room To read the full Improved Energy Efficiency Read our process application story visit application stories here • Greatly enhanced process data capture • Improved operator flexibility and ability to monitor temperature variables through • More efficient energy control PlantPAx® system • Remote access • Better handle 18 changeovers each month • Automated management of automation • Estimated reduced energy costs of over assets $1 million 6 7 College Station Water Services (CSWS) Columbia Pipeline Group Water & Wastewater Pumping groundwater from wells Oil and Gas Columbia Pipeline Group (CPG) recently around the county, the College Station modernized its operational environment Water Services (CSWS) cools the water by implementing a modern distributed and transports it through water lines control system to improve reliability, gain to a second pump station for further better insight into its production data, treatment. and ease maintenance. From there, water is transported into the distribution system and two elevated storage tanks. Challenge Solutions Challenge Solutions PlantPAx® process automation system Virtualization Aging control system was putting • Virtualized solution provides improved Modernize the operational • Virtualized PlantPAx® process control system a strain on staff and providing little access to process data, updated alarms and environment to improve reliability, shares information across facilities and up to to no access into real-time process events, and easyto- interpret production gain better insight into production executive level dashboards data. data, and ease maintenance. Information-Enabled • Rockwell Software applications enable Results system control, monitoring, reporting and Improved process control data recording over EtherNet/IP • Increased production from 8.1 million gallons Long-Term Maintenance per day to 11.8 million gallons • FactoryTalk AssetCentre software helps Reduced operations costs securely control user access in the field. • Reduced energy costs by $65,000 annually Results • Reduced spare parts inventory from $250,000 to less than $20,000 per year • Reached 99.5 percent reliability at To read the full Reduced downtime To read the full 100 percent capacity application story visit application story visit • Standardized solution eased troubleshooting • Provided information to the Enterprise and maintenance Analytics group to make business decisions based on real-time and historical data • Decreased downtime through remote troubleshooting capabilities and virtualized • Saved approximately $2.3 million in servers maintenance costs in 2014 8 9 Du Pont Energy Control Technologies (ECT) Food & Beverage The Du Pont plant in Brazilian city of Oil and Gas Energy Control Technologies Esteio, Rio Grande do Sul, founded in (ECT), an OEM member in the 1958, was the first to manufacture Rockwell Automation PartnerNetwork™ margarine in the country. program, is one of the companies Currently, it provides protein solutions for helping drive this relatively recent major players in two primary markets: energy boom. meat (which uses it for processed meats, The Iowa-based company designs, for example) and nutrition (shakes, juices, builds and supports turbomachinery- cereal bars, among others). plant control systems for oil and gas production. Challenge Solutions Challenge Solutions Deployment of the PlantPAx® Distributed PlantPAx® DCS Perform the migration of obsolete Control System (DCS) with support from Replace multiple proprietary • Technology based on open-communications DCS and PLC systems, at the end of technical consultants and Engineering from systems used in turbomachinery standards serves as common automation Rockwell Automation. their service life and unsupported control with one open, integrated platform by connecting multiple control systems by the manufacturer, with large platform. Results • Integrated HMI gives workers visibility into all number of I/O points and within Increased operational availability, faster systems from one screen three weeks. maintenance agility, better control of operating AADvance Fault-Tolerant Control System costs, and gains in flexibility in the control • Provides SIL-3 hardware process control for system. auxiliary systems; manages overall system trips, interlocks and permissives Results Reduced Costs Read our process To read the full • Integrated platform speeds deployment, application stories
Details
-
File Typepdf
-
Upload Time-
-
Content LanguagesEnglish
-
Upload UserAnonymous/Not logged-in
-
File Pages25 Page
-
File Size-