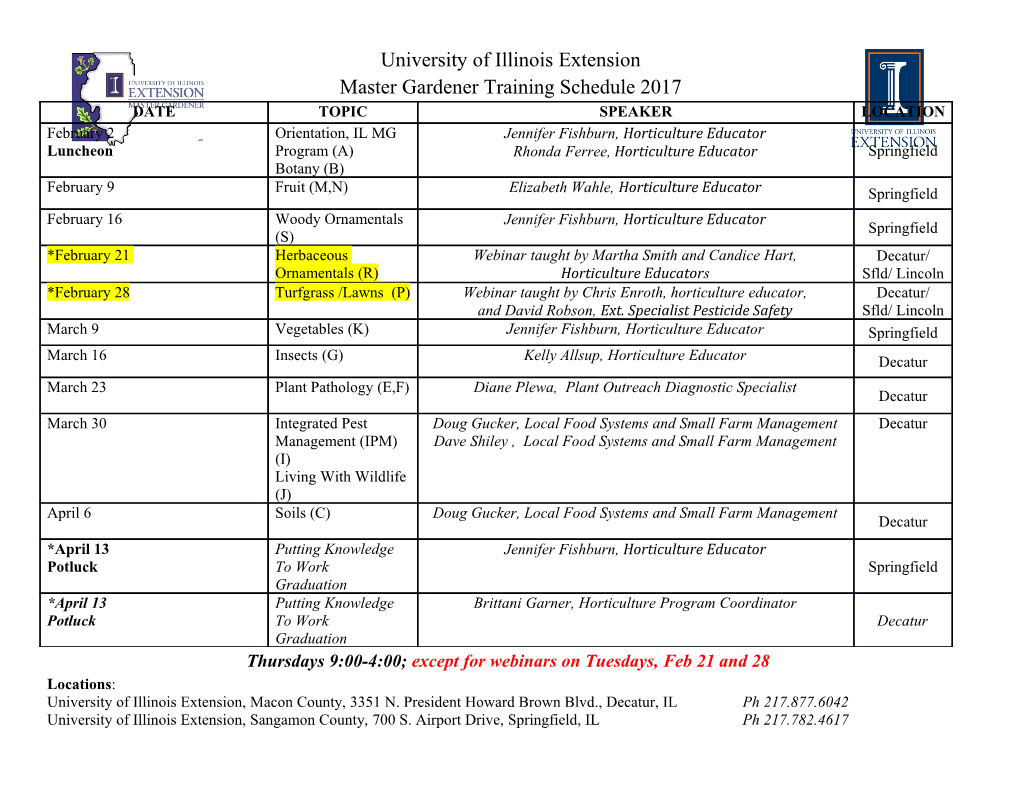
<p>TOP 10 </p><p>SHA </p><p>VIOLATIONS </p><p><sup style="top: -0.5667em;">for </sup>2016 </p><p>E VEN TS </p><p>SPECIAL REPORT </p><p>Top 10 OSHA <br>Violations for 2016 </p><p>i</p><p>Vice President, </p><ul style="display: flex;"><li style="flex:1">Content and Product Development: </li><li style="flex:1">Patricia Trainor, JD </li></ul><p></p><ul style="display: flex;"><li style="flex:1">Robert L. Brady, JD </li><li style="flex:1">Founder: </li></ul><p>Senior Managing Editor, </p><ul style="display: flex;"><li style="flex:1">Environment, Health, and Safety: </li><li style="flex:1">Amanda Czepiel, JD </li></ul><p></p><ul style="display: flex;"><li style="flex:1">Emily Scace </li><li style="flex:1">Senior Editor, Safety: </li></ul><p>Senior Production Manager—CMS: Content Production Specialist: Quality Control Associate: Proofreaders: <br>Matt Sharpe Sherry Newcomb Linda Costa Joan Carlson, Brechin Knapp </p><p>This publication is designed to provide accurate and authoritative information in regard to the subject matter covered. It is sold with the understanding that the publisher is not engaged in rendering legal, accounting, or other professional services. If legal advice or other expert assistance is required, the services of a competent professional should be sought. (From a Declaration of Principles jointly adopted by a Committee of the American Bar Association and a Committee of Publishers.) </p><p>© 2017 BLR<sup style="top: -0.3025em;">®</sup>—BUSINESS & LEGAL RESOURCES All rights reserved. This book may not be reproduced in part or in whole by any process without written permission from the publisher. </p><p>Authorization to photocopy items for internal or personal use or the internal or personal use of specific clients is granted by Business & Legal Resources. For permission to reuse material from <em>OSHA’s Top 10 Violations for 2016</em>, 978-1- <a href="/goto?url=http://www.copyright.com or contact the Copyright" target="_blank">55645-585-8, please go to http://ww</a><a href="/goto?url=http://www.copyright.com or contact the Copyright" target="_blank">w</a><a href="/goto?url=http://www.copyright.com or contact the Copyright" target="_blank">.</a><a href="/goto?url=http://www.copyright.com or contact the Copyright" target="_blank">copyright.com or contact the Copyright </a>Clearance Center, Inc. (CCC), 222 Rosewood Drive, Danvers, MA 01923, 978- 750-8400. CCC is a not-for-profit organization that provides licenses and registration for a variety of uses. </p><p>ISBN: 978-1-55645-585-8 Printed in the United States of America Questions or comments about this publication? Contact: BLR—Business & Legal Resources 100 Winners Circle, Suite 300 Nashville, TN 37027 800-727-5257 </p><p><a href="/goto?url=http://www.blr.com" target="_blank">http://ww</a><a href="/goto?url=http://www.blr.com" target="_blank">w</a><a href="/goto?url=http://www.blr.com" target="_blank">.</a><a href="/goto?url=http://www.blr.com" target="_blank">blr.com </a></p><p>ii </p><p>Top 10 OSHA Violations for 2016 </p><p><strong>Table of contents </strong></p><p><strong>Introduction . . . . . . . . . . . . . . . . . . . . . . . . . . . . . . . . . . . . . . . . . . . . . . . . . . . . . . 1 </strong></p><p>General Duty Clause enforcement. . . . . . . . . . . . . . . . . . . . . . . . . . . . . . . . 2 Recent GDC cases . . . . . . . . . . . . . . . . . . . . . . . . . . . . . . . . . . . . . . . . . . . . . . 3 Severe injury reporting, enforcement, and RRIs . . . . . . . . . . . . . . . . . . . . 4 Types of OSHA citations . . . . . . . . . . . . . . . . . . . . . . . . . . . . . . . . . . . . . . . . 5 Penalty increases. . . . . . . . . . . . . . . . . . . . . . . . . . . . . . . . . . . . . . . . . . . . . . . 6 Coming soon: Electronic injury and illness submission. . . . . . . . . . . . . . . . . . . . . . . . . . . 6 Most frequently violated standards— General industry 2016 . . . . . . . . . . . . . . . . . . . . . . . . . . . . . . . . . . . . . . . . . . 7 Most frequently violated standards— Construction 2016. . . . . . . . . . . . . . . . . . . . . . . . . . . . . . . . . . . . . . . . . . . . . . 8 </p><p><strong>1. 29 CFR 1926.501 Fall Protection in Construction . . . . . . . . . . . . . . . . . . . 9 </strong></p><p>Total violations—6,877 Total penalties—$26,044,601 . . . . . . . . . . . . . . . . . . . . . . . . . . . . . . . . . . . . . 9 </p><p><strong>2. 29 CFR 1910.1200 Hazard Communication . . . . . . . . . . . . . . . . . . . . . . . 10 </strong></p><p>Total violations—5,646 Total penalties—$3,864,543 . . . . . . . . . . . . . . . . . . . . . . . . . . . . . . . . . . . . . 10 </p><p><strong>3. 29 CFR 1926.451—Scaffolding in Construction . . . . . . . . . . . . . . . . . . . 12 </strong></p><p>Total violations—3,884 Total penalties—$8,362,429 . . . . . . . . . . . . . . . . . . . . . . . . . . . . . . . . . . . . . 12 </p><p><strong>4. 29 CFR 1910.134—Respiratory Protection . . . . . . . . . . . . . . . . . . . . . . . . 13 </strong></p><p>Total violations—3,562 Total penalties—$2,949,453 . . . . . . . . . . . . . . . . . . . . . . . . . . . . . . . . . . . . . 13 </p><p><strong>5. 29 CFR 1910.147—Control of Hazardous Energy (Lockout/Tagout). . 14 </strong></p><p>Total violations—3,391 Total penalties—$13,288,827 . . . . . . . . . . . . . . . . . . . . . . . . . . . . . . . . . . . . 14 </p><p><strong>6. 29 CFR 1910.178—Powered Industrial Trucks . . . . . . . . . . . . . . . . . . . . 16 </strong></p><p>Total violations—2,843 Total penalties—$5,138,924 . . . . . . . . . . . . . . . . . . . . . . . . . . . . . . . . . . . . . 16 </p><p><strong>7. 29 CFR 1926.1053—Ladders in Construction . . . . . . . . . . . . . . . . . . . . . 17 </strong></p><p>Total violations—2,615 Total penalties—$4,711,849 . . . . . . . . . . . . . . . . . . . . . . . . . . . . . . . . . . . . . 17 </p><p><strong>8. 29 CFR 1910.212—Machine Guarding—General requirements for all machines . . . . . . . . . . . . . . . . . . . . . . . . . . . . . . . . . . . . . . . . . . . . . . . . . . . . 19 </strong></p><p>Total violations—2,437 Total penalties—$9,414,885 . . . . . . . . . . . . . . . . . . . . . . . . . . . . . . . . . . . . . 19 </p><p>©BLR<sup style="top: -0.1925em;">®</sup>—Business & Legal Resources 10102600 </p><p>iii </p><p><strong>9. 29 CFR 1910.305—Electrical—Wiring methods, components, and equipment—General . . . . . . . . . . . . . . . . . . . . . . . . . . . . . . . . . . . . . . . . . 20 </strong></p><p>Total violations—1,934 Total penalties—$2,289,718 . . . . . . . . . . . . . . . . . . . . . . . . . . . . . . . . . . . . . 20 </p><p><strong>10. 29 CFR 1910.303—Electrical— </strong><br><strong>General requirements. . . . . . . . . . . . . . . . . . . . . . . . . . . . . . . . . . . . . . . . . 21 </strong></p><p>Total violations—1,703 Total penalties—$2,907,873 . . . . . . . . . . . . . . . . . . . . . . . . . . . . . . . . . . . . . 21 </p><p>iv </p><p>Top 10 OSHA Violations for 2016 </p><p><strong>Introduction </strong></p><p>Because the U.S. Occupational Safety and Health Administration (OSHA) cannot inspect all 7 million workplaces it covers each year, the Agency seeks to focus its inspection resources on the most hazardous workplaces in the following order of priority: </p><p><strong>1. Imminent danger situations—</strong>hazards that could cause death or seri- </p><p>ous physical harm—receive top priority. Compliance officers will ask employers to correct these hazards immediately or remove endangered employees. </p><p><strong>2. Fatalities, catastrophes, and severe injuries and illnesses—</strong>employers </p><p>are required to report all work-related fatalities within 8 hours and all work-related inpatient hospitalizations, amputations, or eye-loss incidents within 24 hours. Based on the severity of the incident and other specified criteria, OSHA will either conduct an on-site investigation or initiate a rapid-response investigation (RRI) that requires the employer to conduct its own root cause analysis and submit evidence of corrective actions. </p><p><strong>3. Complaints—</strong>allegations of hazards or violations also receive a high priority. Employees may request anonymity when they file complaints. </p><p><strong>4. Referrals </strong>of hazard information from other federal, state, or local agencies; individuals; organizations; or the media receive consideration for inspection. </p><p><strong>5. Follow-ups—</strong>checks for abatement of violations cited during previous inspections are also conducted by the Agency in certain circumstances. </p><p><strong>6. Planned or programmed investigations—</strong>inspections aimed at specific </p><p>high-hazard industries or individual workplaces that have experienced high rates of injuries and illnesses also receive priority. </p><p>As a result of OSHA’s enforcement efforts, many of the same standards make the “most frequently violated” list again and again. </p><p>In this year’s report, we have provided individual charts for the top 10 violations for both general industry and construction, with last year’s ranking in the last column. The report covers violations for fiscal year (FY) 2016, which runs from October 1, 2015, through September 30, 2016. </p><p>©BLR<sup style="top: -0.1925em;">®</sup>—Business & Legal Resources 10102600 </p><p>1</p><p>General Duty Clause enforcement </p><p>In this report, we discuss OSHA’s top 10 most frequently violated standards. But many employers do not realize that when there is no specific standard, OSHA will use the General Duty Clause (GDC), Section 5(a)(1), of the Occupational Safety and Health Act (OSH Act) of 1970 to cite employers. </p><p>Section 5(a)(1) of the OSH Act requires: “Each employer shall furnish to each of his employees employment and a place of employment which are free from recognized hazards that are causing or are likely to cause death or serious physical harm to his employees.” </p><p>The GDC is the “gap filler” in enforcement actions that addresses recognized hazards where no OSHA standard exists. The Agency often looks to voluntary consensus standards such as those put out by the National Fire Protection Association (NFPA) or the American National Standards Association (ANSI) as a basis for GDC citations, as well as information in manufacturers’ instructions or product warning labels. Over the past several years, OSHA has shown itself to be increasingly willing to cite employers under the GDC for a variety of hazards not covered by its safety and health standards. </p><p>The courts have interpreted OSHA’s GDC to mean that an employer has a legal obligation to provide a workplace free of conditions or activities that either the employer or industry recognizes as hazardous and that cause, or are likely to cause, death or serious physical harm to employees when there is a feasible method to abate the hazard. </p><p>An employer can be found to be in violation of the GDC if it can be shown that: <br>◆◆ A hazard existed. ◆◆ The hazard was likely to cause death or serious physical harm. ◆◆ The employer had knowledge of the hazard or should have had knowledge because the hazard had been recognized by the employer, the industry, or common sense. </p><p>◆◆ The hazard was foreseeable. ◆◆ Workers were exposed to the hazard. </p><p>Common areas in which OSHA uses the GDC include: <br>◆◆ Musculoskeletal disorders (MSDs) resulting from hazardous lifting, repetitive tasks, awkward positions; </p><p>◆◆ Failure to protect employees from heat stress; ◆◆ Failure to keep employee chemical exposure levels below <em>recommended </em>levels; </p><p>◆◆ Cell phone use while driving on the job; ◆◆ Use of a forklift without a seat belt; ◆◆ Risk of workplace violence; ◆◆ Improper storage of highly reactive chemicals; <em>and </em>◆◆ Combustible dust explosion hazards. </p><p>2</p><p>Top 10 OSHA Violations for 2016 </p><p>Necessary elements to prove a violation of the GDC include: <br>◆◆ The employer failed to keep the workplace free of a hazard to which employees of that employer were exposed; </p><p>◆◆ The hazard was recognized; ◆◆ The hazard was causing or was likely to cause death or serious physical </p><p>harm; <em>and </em></p><p>◆◆ There was a feasible and useful method to correct the hazard. <br>A GDC violation must involve both the presence of a serious hazard and exposure of the cited employer’s own employees within the previous 6 months. It is key under the GDC that employers can be cited only for exposure of “his own employees,” as worded in the GDC. </p><p>In 2016, more than 1,200 GDC violations were cited, with nearly $6 million in penalties. In any typical year, somewhat more than 1,000 OSHA inspections result in fines for a GDC violation. So, when designing and evaluating your safety program, remember that it’s not enough to stop at compliance with OSHA standards; you also must consider whether additional hazards at your facility might constitute a violation of the GDC and take steps to create a safe working environment for all your employees. </p><p>Recent GDC cases </p><p><strong>Unloading trailers with forklifts </strong></p><p>In FY 2016, OSHA used the GDC several times in cases where forklift drivers were exposed to fall, crush, and struck-by hazards while loading or unloading tractor trailers that did not remain stationary while the work was taking place. In one such case, an employee operating a forklift was traveling back and forth from a loading dock to a trailer. The employee was inside the trailer when it started to pull away from the dock, causing the employee and his forklift to roll out of the trailer and land on the ground approximately 4 feet below. In another case, a forklift operator was unloading a tractor trailer when the truck driver pulled away from the dock. The forklift was on its way out of the trailer as the trailer separated from the dock, forcing the forklift operator to jump from the forklift to the ground below, resulting in injuries. OSHA found that the employer did not verify that the forklift operator had exited the trailer before notifying the truck driver that the unloading was complete. The employer was fined $17,000 as a result. </p><p><strong>Heat exposure </strong></p><p>In FY 2016, OSHA issued over 50 citations for heat exposure under the GDC. Most of the employers cited for heat exposure were in construction, landscaping, and other outdoor industries, but employers with indoor operations weren’t immune. </p><p>For example, Hospital Central Services, a commercial laundry facility, was issued a serious violation and fined over $10,000 under the GDC for exposing </p><p>©BLR<sup style="top: -0.1925em;">®</sup>—Business & Legal Resources 10102600 </p><p>3</p><p>employees to heat stress while they worked around heat sources such as flat iron machines, dryers, and washing machines for 10-hour shifts. According to OSHA, employees were exposed to time-weighted average temperatures that exceeded 90 degrees Fahrenheit (°F) in this environment, and some suffered from heat-related illnesses as a result. </p><p>In another significant heat stress case, OSHA cited the U.S. Postal Service after multiple employees were exposed to dangerously high temperatures. According to the agency, while working in weather conditions with temperatures exceeding 90°F, a mail carrier who had not become acclimatized to walking and delivering mail in high heat worked from a vehicle without air-conditioning and carried a mail bag weighing up to 15 pounds, causing him to develop a heat-related illness. Another worker was taken to the emergency room for heat exhaustion and dehydration after exposure to extremely high heat levels. Because the U.S. Postal Service had been previously cited for similar hazards, OSHA issued a repeat citation that carried a fine of $69,591. </p><p>Regardless of whether your employees work outdoors, in an indoor manufacturing environment, or in vehicles, you must consider whether they could be exposed to conditions likely to cause heat stress and take appropriate protective measures. </p><p><strong>Workplace violence </strong></p><p>In FY 2016, OSHA cited over 1 dozen employers under the GDC for hazards related to workplace violence. Many of these cases were in health care or related social services; others affected convenience stores, property management companies, and security services. In one tragic incident, a security guard was interacting with a visitor in a federal building when the visitor shot the employee with a firearm, killing him. OSHA determined that the employer failed to develop a workplace violence prevention program and take other measures to protect its employees from the known threat, given the nature of working as a security guard, of workplace violence and active shooter situations. The employer was cited with a serious violation and fined $7,000. In another case, OSHA cited a home healthcare company with a willful violation under the GDC for exposing its employees to verbal and serious physical assaults while they provided nursing care services to clients in what the agency referred to as “hostile home environments.” The company was fined $70,000 for the GDC violation, as well as an additional $28,000 for various recordkeeping violations. </p><p>Severe injury reporting,enforcement,and RRIs </p><p>Since January 2015, employers have been required to report to OSHA within 24 hours any work-related inpatient hospitalization, amputation, or loss of an eye, in addition to the existing requirement to report fatalities within 8 hours. The agency says that the new reporting requirement has provided timely information about where and how serious injuries were occurring in workplaces across the country and allowed it to focus its efforts more effectively. </p><p>4</p><p>Top 10 OSHA Violations for 2016 </p><p>To prioritize its enforcement resources, OSHA does not conduct a full investigation in every one of these reported incidents. Instead, it uses a triage system to direct enforcement to the most hazardous locations. In over one-half of reported severe injury and fatality cases, OSHA does not send its inspectors to the site but instead uses a rapid response investigation (RRI) protocol, which requires employers to conduct their own root cause analysis of the incident and submit evidence of corrective actions. If an employer does not cooperate with the RRI process, an in-person inspection can result. If you are subject to an RRI following an incident at your facility, it is in your best interest to be thorough in conducting your root cause analysis and implementing and documenting corrective actions. </p><p>Types of OSHA citations </p><p><strong>Willful. </strong>An employer has demonstrated either intentional disregard for the requirements of the OSH Act or plain indifference to employee safety and health. Penalties range from $9,054 to $126,749 per willful violation. If an employer is convicted of a willful violation that has resulted in an employee fatality, the offense is punishable by a court fine, by imprisonment for up to 6 months, or both. Criminal conviction can result in fines of up to $250,000 for an individual or $500,000 for a corporation. </p><p><strong>Serious. </strong>A serious violation means there is a substantial probability that death or serious physical harm could result from a condition that exists or from practices, operations, or processes. OSHA may propose a penalty of up to $12,675 for each violation. </p><p><strong>Other than serious. </strong>This type of violation results from a condition that is hazardous and has a direct relationship to employees’ safety and health but would probably not cause death or serious physical harm. OSHA may impose a penalty of up to $12,675 for each violation. </p><p><strong>De minimis. </strong>These are conditions in which an employer has implemented a measure different from one specified in a standard that has no direct or immediate relationship to safety or health. These conditions do not result in citations or penalties. </p><p><strong>Failure to abate. </strong>In this case, a previously cited hazardous condition has not been brought into compliance since the prior inspection and is discovered at a later inspection. If the violation is corrected but later recurs, the subsequent occurrence is a repeat violation. OSHA may impose a penalty of up to $12,675 per day for each violation. </p><p><strong>Repeat. </strong>A repeated violation is one that has been cited previously within the past 5 years for the same or a substantially similar condition or hazard, and the citation has become a final order of the Occupational Safety and Health Review Commission (OSHRC). Repeat violations can bring a civil penalty of up to $126,749 for each violation. </p><p>©BLR<sup style="top: -0.1925em;">®</sup>—Business & Legal Resources 10102600 </p><p>5</p><p>Penalty increases </p><p>In August 2016, higher civil penalty levels for OSHA violations—the first increase in over 25 years—took effect. The August 2016 penalty levels, which represented a onetime “catch-up” increase to compensate for a long period without adjustment, were 78 percent higher than the previous levels. Penalties went up by an additional 1 percent in January 2017, the first in what is supposed to be a series of regular increases to keep pace with inflation. </p><p>Type of Violation </p><p>Other than serious Serious </p><p>Old penalty range </p><p>Up to $7,000 </p><p>Current penalty range </p><p>Up to $12,675 </p><ul style="display: flex;"><li style="flex:1">Up to $7,000 </li><li style="flex:1">Up to $12,675 </li></ul><p></p><ul style="display: flex;"><li style="flex:1">Willful </li><li style="flex:1">Minimum of $5,000 </li></ul><p>up to $70,000 <br>Minimum of $9,054 up to $126,749 </p><p></p><ul style="display: flex;"><li style="flex:1">Repeat </li><li style="flex:1">Up to $70,000 </li><li style="flex:1">Up to $126,749 </li></ul><p></p><ul style="display: flex;"><li style="flex:1">Failure to abate </li><li style="flex:1">Up to $7,000 per day </li><li style="flex:1">Up to $12,675 per day </li></ul><p></p><p>Given this upward trend in fines, it is more important than ever to make sure your safety programs are on point so you don’t fall into the trap of one of the most frequent violations. </p><p>Coming soon: Electronic injury and illness submission </p><p>Under the Final Rule to Improve Tracking of Workplace Injuries and Illnesses, finalized in May 2016, certain employers will soon be required to submit data from their injury and illness records to OSHA electronically on an annual basis. Originally, the first electronic submission deadline was July 1, 2017; however, OSHA has extended that deadline to December 1, 2017. </p><p>By December 1, 2017, establishments with 250 or more employees that are required to keep injury and illness records, as well as establishments with 20–249 employees in designated high-hazard industries, must electronically submit data from their 2016 OSHA 300A, Summary of Work-Related Injuries and Illnesses. Additional requirements are scheduled to be phased in through 2019. </p><p>As of August 1, 2017, OSHA has launched its online Injury Tracking Application, <a href="/goto?url=https://www.osha.gov/injuryreporting/ita/" target="_blank">available at </a><a href="/goto?url=https://www.osha.gov/injuryreporting/ita/" target="_blank">https://www.osha.gov/injuryreporting/ita</a>. There are three options for data submission. Employers can manually enter data into a Web-based form, upload a CSV file, or, for those with automated recordkeeping systems, transmit data electronically via an application programming interface (API). </p>
Details
-
File Typepdf
-
Upload Time-
-
Content LanguagesEnglish
-
Upload UserAnonymous/Not logged-in
-
File Pages27 Page
-
File Size-